Sulphur 386 Jan-Feb 2020
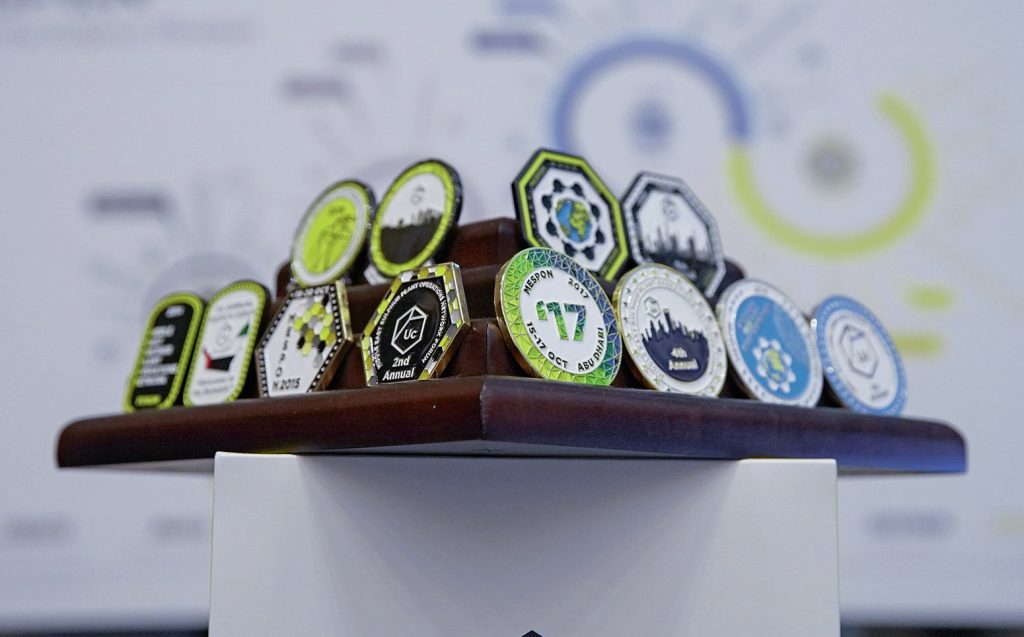
31 January 2020
MESPON 2019
CONFERENCE REPORT
MESPON 2019
The Sixth Annual MESPON Forum took place 7-10 October at the Rosewood Hotel Abu Dhabi, where the global sour gas and sulphur community gathered for four days of networking, learning, and collaboration. This year’s theme highlighted new trends, innovations and best practices in the field of sour gas processing that enhance operations.
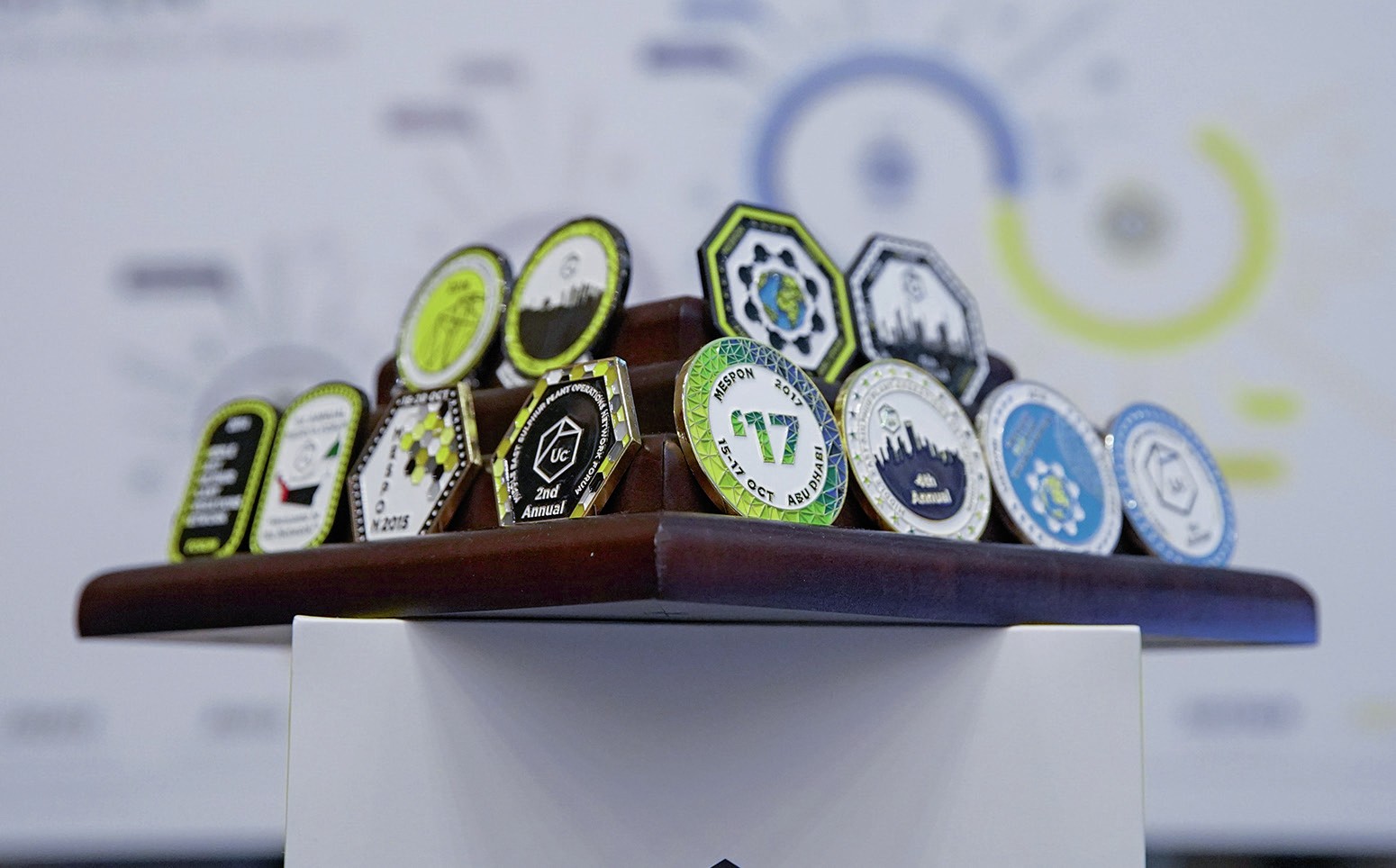
The Middle East Sour Plant Operations Network (MESPON), organised by UniverSUL Consulting and supported by ADNOC is one of the industry’s premier events for knowledge exchange and networking in the field of sour gas production, processing and sulphur recovery. Each year at this event, the sour gas community comes together from across the globe to share knowledge and resources in support of continual improvements in HSE, reliability, efficiency and general best practices.
Given that the Middle East became the largest sulphur producing region in 2015, ADNOC has created an environment of effective industry stewardship, ensuring collaboration and information sharing in established subject matters, while also promoting development of new innovations that will drive the industry forward for decades to come.
Some of the major themes for MESPON 2019 were:
- Operational excellence in sour gas treating, sulphur recovery and sulphur handling
- Ultra sour gas processing innovations, including digitalisation and artificial intelligence
- CO 2 capture for enhanced oil recovery (EOR)
MESPON 2019 started off with a Sour Gas Innovation & Technology Day which featured presentations and interactive exhibits that showcased recent advancements and R&D breakthroughs in the sour gas industry. The main themes of the day were optimised asset utilisation and potentially disruptive technologies.
Prof. Alessandro Lanteri of Hult International Business School gave the keynote address on the Innovation and Technology Day in which he stressed that innovation is not about a product or a technology, rather it is about something new. Doing new things means making mistakes and having to learn everything all over again. Innovation is all about learning. We get better at learning by first unlearning what we think we know and then by continuing to learn, testing what we wish to be true. It is important to react quickly and be open to serendipitous events. The advantage lies in rate of learning. A learning culture must be cultivated where mistakes are not accepted, they are celebrated. Everything looks like a failure in the middle but it is important to keep going.
The Sour Gas Innovation & Technology Day was followed by three days of the traditional MESPON Forum which covers the full sour gas value chain:
- Extracting maximum value from sour gas
- Gas sweetening and sour water
- Sulphur recovery and tail gas treating
- Sulphur handling
A key feature of the MESPON agenda is its panel discussions and operations roundtable. The topics of this year’s panel discussions were:
- CO 2 from SRUs/TGTUs for enhanced oil recovery (EOR)
- The sulphur product value chain.
Selected forum highlights
Dual column cryogenic distillation
Tecnimont has developed an innovative cryogenic technology to meet new market demands for the exploitation of highly sour gas fields:
- to produce sales gas or LNG;
- remove N 2 to meet the required gas specification;
- recover as much C2+ as possible;
- reduce CO 2 emissions through EOR and/or direct injection;
- valorise CO 2 through its re-use for the synthesis of chemicals.
Tecnimont’s DCCD ™ technology is a one-step cryogenic gas purification process using a proprietary dual column distillation scheme, providing full removal of mercaptans, sulphur components and other impurities to produce sales gas and/or LNG based on client’s requests.
Compared to conventional solvent based processes, DCCD ™ has lower capex due to fewer items of main equipment and rotating equipment and reduced opex due to lower energy requirements.
The simple process configuration, concurrent removal of any sulphur species, lower opex sensitivity to CO 2 feed content and the unique synergies existing with LNG production are just some of the characteristic feature of DCCD ™ technology, which sets it apart from the majority of sour gas treatment process.
DCCD ™ technology has been validated by means of two experimental campaigns and a technology package for an industrial plant has been completed.
Mega-sized SRUs
Comprimo provided an overview of today’s mega-sized SRU trains and gave their outlook for the future. Project economics can be improved by building mega-sized SRU trains. Capex can be reduced due to lower equipment count and economy of scale. There are however limitations to the largest practical sizes of SRU trains, due to both fabrication and transportation limits. Achievable train capacities can be increased by technology selection, e.g. oxygen enrichment, and equipment design modifications, e.g. WHB design. There is no one-mega-size-fits-all solution so close cooperation between operating companies and experienced licensors and contractors is crucial in delivering optimised designs.
Looking to the future, more mega-sized SRU trains are in the pipeline. The largest sizes (currently up to 2,500 t/d) are expected to increase. There will be increased application of oxygen enrichment. Various new build and revamp gas plant projects using oxygen enrichment are already underway. There is also increasing focus on potential for CO 2 reinjection for EOR, which may further favour acid gas enrichment and oxygen enrichment.
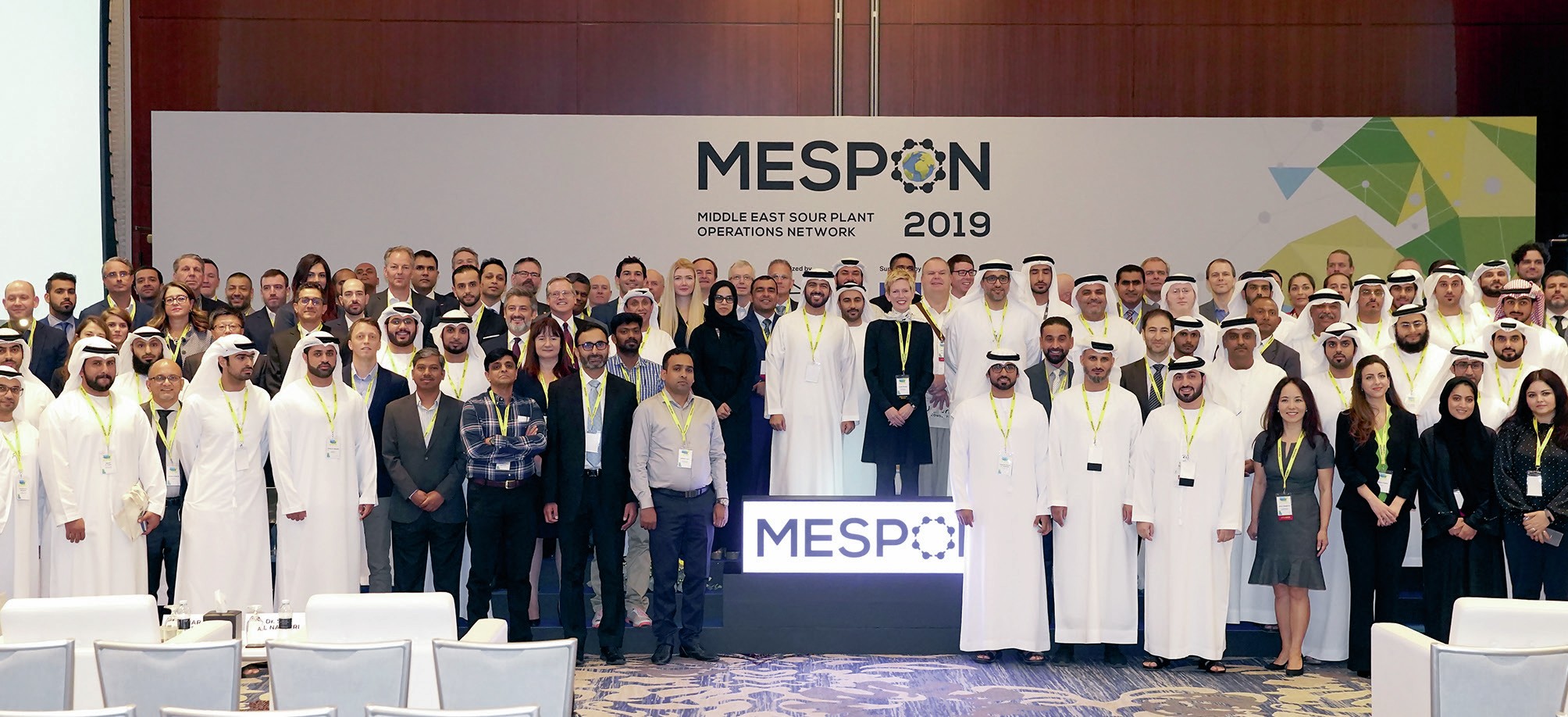
ASG CO 2 recovery project
ADNOC Sour Gas (ASG) owns and operates the Shah Gas Processing plant (SGP) which receives and processes sour fluids (up to 25% H 2 S and 10% CO 2 ) from the nearby Shah Arab Sour Gas Field. ASG has been investigating options to capture and produce CO 2 in a flexible and cost effective approach in case of future growth. The captured CO 2 would be utilised for EOR and would reduce greenhouse gas emissions. After a detailed evaluation of the various options available, ASG has selected pre-combustion CO 2 recovery (i.e. after the SRU tail gas treating unit and before the incinerator unit) and amine absorption for CO 2 capture. The target date for start-up is 2023.
New technology for reducing amine losses
INEOS has developed Amine Quench ™ , a patent pending process which uses a small piece of proprietary equipment that is installed in the stripper overhead to reduce amine vapour losses in gas processing plants. It provides a cost effective solution for plants experiencing high amine losses and requires minimal modifications to the amine system.
Alkanolamines used for gas and liquid treating are regenerable solvents. The amine solvent is not consumed by the acid gas removal process but some amine loss is inevitable in any system. To determine if amine usage is typical/acceptable industry benchmarks and process simulation can be used. In industry surveys 1-3 lb amine/million standard ft 3 is typical for natural gas processing. High pressure systems can achieve <1 lb amine/million standard ft 3 of gas treated.
Excessive amine losses increase operating costs and can be a symptom of other operational or design issues. It is important to understand the potential pathways for amine leaving the system and to identify and correct the cause of excessive amine loss. Amine loss categories include:
- solubility (liquid treaters);
- entrainment;
- gas-in-liquid (foaming);
- liquid-in-gas;
- liquid-in-liquid;
- degradation;
- mechanical;
- vaporisation.
To troubleshoot, conduct a plant-walkthrough of all process equipment and piping in the amine system to identify leaks, collect process data to enable process simulations to be run to look for problems and use a systematic approach to using a process of elimination to identify and correct the cause of high amine losses.
Once the root cause of amine losses is identified, operational issues or conditions responsible for excessive losses can be addressed.
Innovative approach to Claus tail gas treating
The conventional method for achieving a sulphur recovery efficiency of 99.9+% is to install a TGTU that hydrogenates all the remaining sulphur species to H 2 S, and then uses an amine system to capture and recycle the H 2 S. Such technologies (BSR, SCOT etc.) are widely used when high sulphur recoveries must be met but are relatively expensive with associated high energy consumption.
With amine-based TGTUs the operator only has sulphur to deal with but if sulphuric acid is acceptable, the economics could be considerably improved by combining the Claus plant with a wet gas sulphuric acid plant. Higher energy recovery is achieved when using the wet gas sulphuric acid process for Claus tail gas (in total 808 kJ heat per mole of H 2 S is generated). Approximately 90% heat is recovered as steam or hot air and less than 10% is discharged to cooling water.
However, the industry has not been receptive to handling the relatively large quantities of sulphuric acid produced despite the obvious economic benefits.
A new innovative configuration has therefore been developed by Haldor Topsoe in cooperation with Worley, integrating the WSA process with the Claus process, whereby sulphur compounds in the tail gas from the Claus process are recovered as commercial grade sulphuric acid which can be recycled directly to the Claus reaction furnace for 100% elemental sulphur recovery. The oxygen contained in the recycled sulphuric acid will act in the same way as oxygen enrichment, with the result of lower process gas flow and possibilities for boosting the capacity of an existing plant or reducing the capex of a new Claus plant. The only product is high quality elemental sulphur.
Besides lower opex, capex and CO 2 emissions, using a WSA plant as a TGTU also offers extra flexibility for operators operating a sour water stripper as the sour water stripper off gas can be bypassed around the Claus reaction furnace, increasing reliability of the SRU by avoiding the inherent issues caused by handling ammonia in the Claus plant.
Liquid sulphur degassing
Liquid sulphur degassing technology continues to take a more important role in the sulphur recovery industry as Claus SRU sulphur emissions and handling safety receive greater attention. Based on commercial operating experiences and ever changing environmental emission regulations, Fluor/GAA continues to improve the performance of the D’GAASS out-of-pit liquid sulphur degassing technology. The 3rd generation D’GAASS process offers: shorter degassing duration requirements, smaller equipment, lower capex and opex, as well as enhanced operating flexibility and reliability through reduced corrosion potential. The improvements can also be retrofitted to existing D’GAASS units.