Fertilizer International 495 Mar-Apr 2020
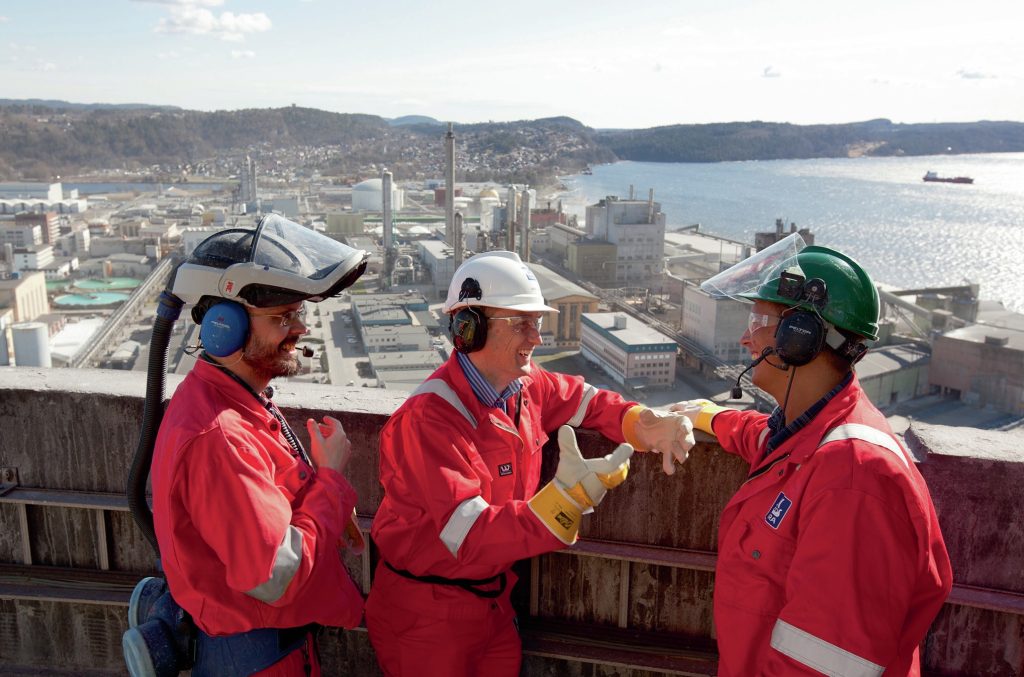
31 March 2020
Making fertilizer plants safe
SAFETY MANAGEMENT
Making fertilizer plants safe
We look at safety, health and environmental (SHE) management and hazards at nitrogen fertilizer plants and the importance of the International Fertilizer Association’s ‘Protect & Sustain’ certification scheme.
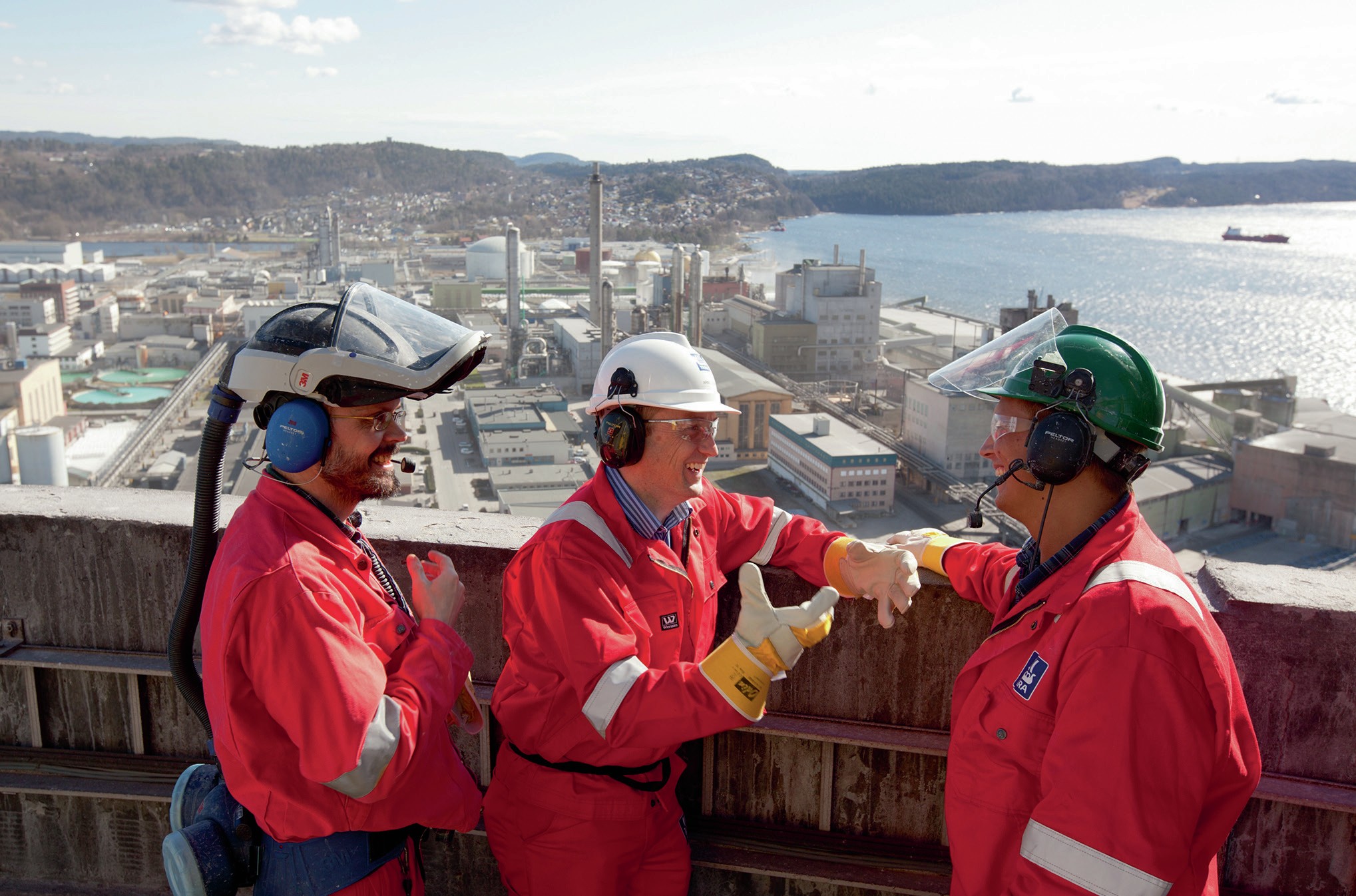
Catastrophic events in the chemical process industries are categorised as “low-probability, high-consequence occurrences”. These naturally receive a huge amount of media attention at the time.
But history teaches us that even these major events fall off the news agenda and are forgotten with the passage of time. That makes effective investigation, reporting and follow-up of catastrophic events critical to achieving a safer operational environment.
Using past mistakes to avoid future errors
Accident investigations provide the opportunity to learn from reported incidents and take corrective action to prevent them from recurring in future. It is essential to translate such learning into design and operational practices1 .
This is certainly the approach taken by leading global urea technology licensor Stamicarbon. All of the international design standards developed by Stamicarbon – which form the basis for its current safe plant design – have been derived largely from experience of past incidents1 .
In Stamicarbon’s view, if you can use the mistakes of the past to avoid future errors, you have a good chance of staying in business. When a higher-consequence accident takes place at a process plant, the majority of the plant’s personnel are involved, either directly or indirectly. Their involvement can range from being part of the incident investigation team implementing corrective actions or – in the worst case – being directly affected by the accident itself1 .
The impact of a catastrophic event on an organisation is profound, especially when co-workers are severely injured or killed. Everybody affected therefore understands the necessity of effective safeguards and operational practices. Indeed, to prevent similar incidents from reoccurring, it is essential, in Stamicarbon’s view, to formally embed the lessons from these incidents within design practices and operational regimes1 .
Lessons from urea safety incidents
In 2017, industry websites ammoniaknowhow.com and ureaknowhow.com introduced global open source risk registers for ammonia and urea plants. At the start of 2018, the risk register for urea plants listed 100 safety hazards relating to more than 100 safety incidents, these having led to at least 65 fatalities and 217 injuries2 .
These 100 safety hazards were collated from incident databases, public domain hazard and operability (HAZOP) study results, and incidents reported by of ureaknowhow.com members. This register of safety hazards represents a significant proportion of the most critical safety hazards in urea plants. They relate to serious incidents that could potentially lead to fatalities, injuries, loss of containment, compromise the integrity of equipment, or cause serious damage to critical and expensive items2 .
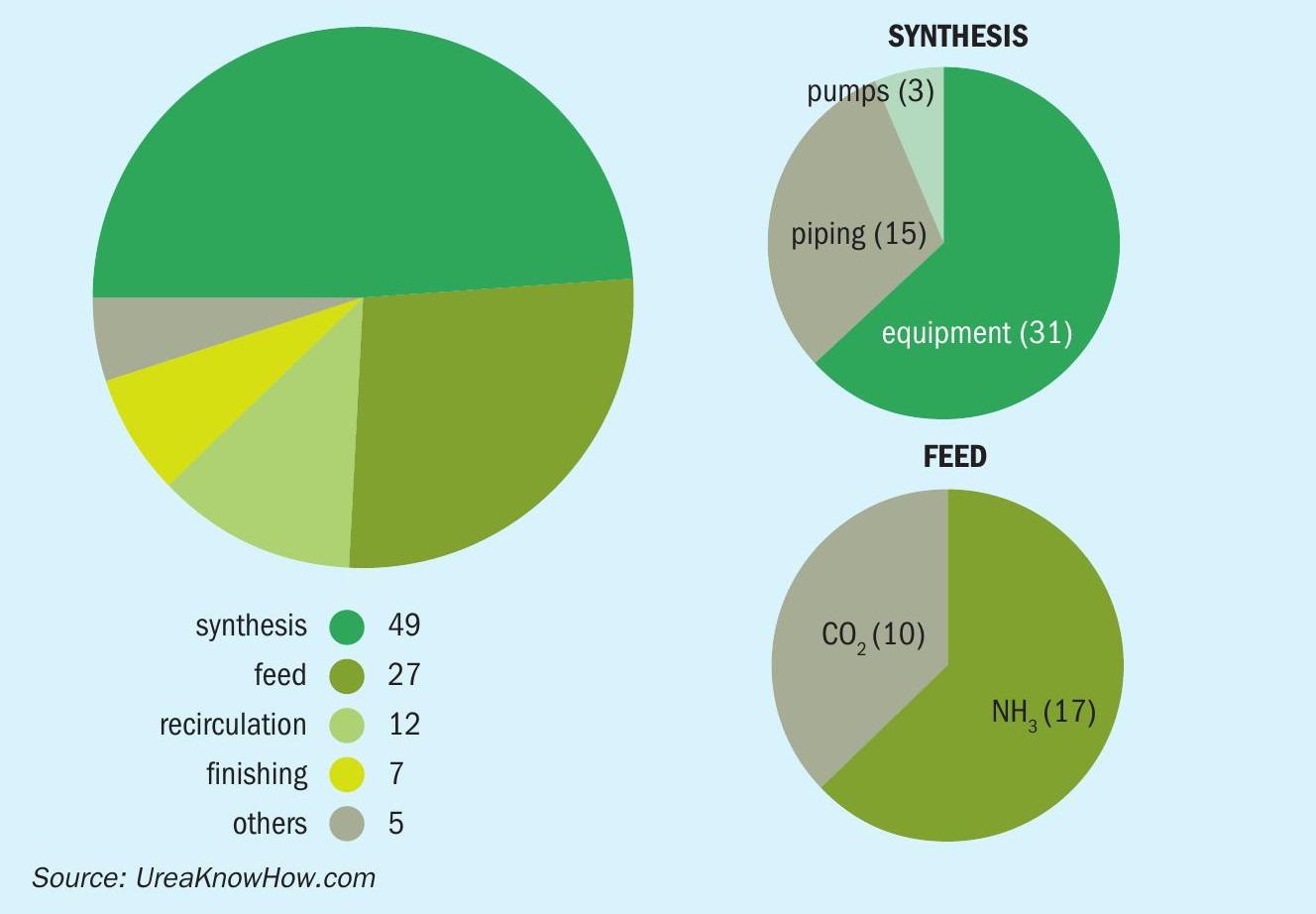
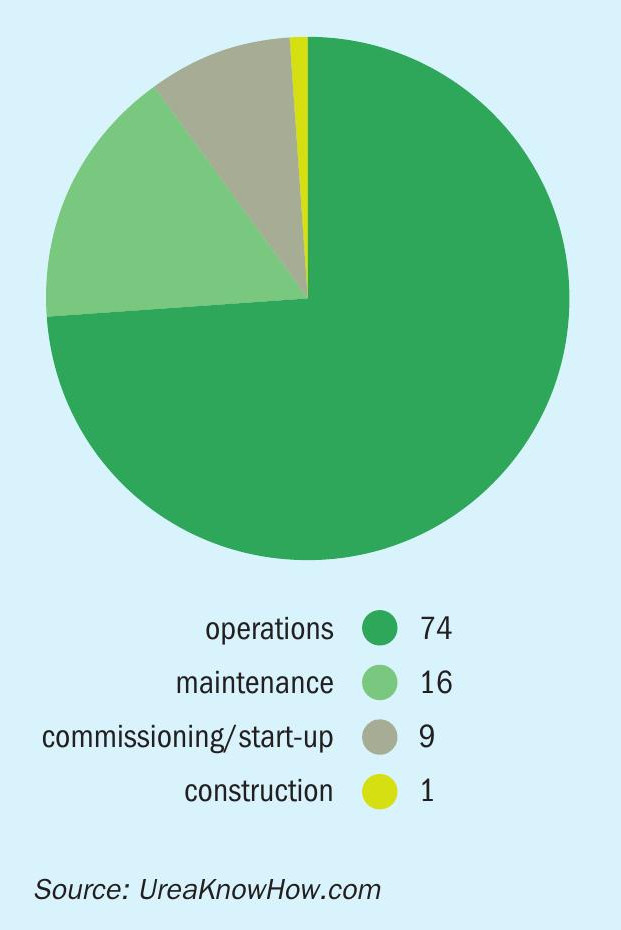
The risk register provides a good overview of urea plant safety hazards. Not only are the hazards identified and listed, each hazard is allocated a risk factor, prevention and mitigation measures are suggested, and reference is made to companies who are able to provide support for implementing these measures. Risk registers are a valuable information source for any HAZOP and safety study of a urea plant.
Where do most safety hazards occur?
A breakdown of the 100 safety hazards by urea plant section (Figure 1) shows these mostly occur in the high pressure synthesis section (49), the feed section (27), the recirculation section (12) and the finishing section (7).
The safety hazards in the high-pressure synthesis section mostly related to high-pressure equipment (63%), high-pressure piping (31%) and high-pressure pumps (6%). Any leak in this section leads to a critical situation due to the release of toxic ammonia, the high pressures and temperature involved, and the presence of corrosive ammonium carbamate. High-pressure equipment is more vulnerable because of the corrosion risk to pressure-bearing carbon steel walls. Ammonium carbamate can corrode carbon steel at a rate of 1,000 millimetres per year.
A significant number of safety hazards occurred in the feed section (27), with 60 percent of these relating to ammonia and 40 percent to the carbon dioxide feed system. A significant part of the feed section is made from carbon steel. Any backflow from high-pressure synthesis will bring this into potential for contact with corrosive carbamate. In HAZOP, it is generally accepted that such a backflow scenario is sufficiently protected against by applying two non-return valves, each of different design. However, analysis of urea plant safety incidents suggests that this assumption/solution now appears to be questionable.
Carbon steel ammonia lines can also suffer from other failure mechanisms – such as vibration, weld failure, process-side corrosion and erosion, atmospheric corrosion and corrosion under insulation.
The carbon dioxide feed system has its own specific and highly critical safety hazard: a small unnoticed carbon dioxide leak can lead to asphyxiation if it occurs in a built-up, unventilated section of plant. Also, in the recirculation section, various important safety hazards exists, such as backflow of carbamate from the high-pressure synthesis to the centrifugal high-pressure carbamate pumps, buffer tank damage and hydrogen explosion risks. In the finishing section, safety hazards include the risk of crystallisation in the urea melt, as well as risks due to cleaning and maintenance in the prill tower, granulator and warehouse.
The top ten equipment items with the most safety hazards are:
1. High-pressure heat exchangers
2. High-pressure vessels
3. High-pressure piping
4. Ammonia piping/valves
5. Ammonia pumps
6. Atmospheric tanks
7. Carbon dioxide piping/valves
8. Carbon dioxide compressor
9. Low-pressure piping (melt, flare headers)
10. High-pressure carbamate pumps.
When do these safety hazards occur?
When the 100 safety hazards are divided according to project phase. (Figure 2), a total of 74 of these are found to occur during the operational phase. However, a relatively large number of safety hazards also take place during the maintenance (16) and commissioning/start-up (9) phases. Relatively large numbers of people are also affected by these hazards due to the volume of contractors on site during these project phases.
Safety hazards during construction, commissioning and start-up
Performing work at elevated heights is a major safety hazard during both construction and maintenance. Although ureaknowhow.com only identified one accident attributable to a construction hazard – which occurred during the construction of a prill tower – this single incident resulted in at least 12 fatalities. The safety risks from working at an elevated height also exist inside a vertical urea reactor.
IFA’s Protect & Sustain programme
Protect & Sustain is a long-standing safety, health and environmental (SHE) management certification scheme offered to fertilizer companies globally by the International Fertilizer Association (IFA).
It forms one of the three pillars of IFA’s global efforts on product stewardship, namely:
- Protect & Sustain certification
- Production benchmarking against four indicators
- The incident reporting portal.
IFA’s ethos on product stewardship is industry-wide, encompassing all of the supply chan. It goes beyond the factory gate by putting in place responsible business management practices across the whole of the product lifecycle – in cooperation with the industry’s producer, distributor, transport and retail companies.
In general, IFA member companies are expected to adhere to the following 12 SHE principles:
1. Management fully committed to showing SHE leadership in fertilizer production, distribution and sales.
2. Strive for zero harm when it comes to environmental impact and worker health.
3. Make SHE a priority by fully integrating this with corporate policy.
4. Provide the necessary financial and human resources to improve SHE performance.
5. Legal compliance with all local SHE and safety regulations.
6. Monitor performance through annual objectives, targets or key performance indicators.
7. Establish adequate procedures to ensure SHE is not jeopardised
8. All staff and contractors are trained and informed to ensure SHE competence.
9. Enhancement of SHE performance by adhering to hazard and risk assessment principles.
10. Subscribe to SHE and safety management systems and be open to internal and external auditing.
11. Voluntarily share information on SHE lessons and experiences with IFA member companies externally and with staff and contractors internally.
12. By taking responsibility for continual SHE and safety improvements, contribute to the overall social responsibility and accountability of the global fertilizer industry.
IFA has made safety and security a key priority due to their potentially grave reputational risks. This is understandable, given that a global stakeholder reputation survey commissioned by IFA revealed that safety – including security – is the number one driver of the fertilizer industry’s reputation.
The prevention measures in IFA’s Protect & Sustain programme cover two distinct types of fertilizer incident:
- Operational accidents – product safety
- The misuse of fertilizers as explosives – product security.
Protect & Sustain is now recognised as the de facto gold standard for the global fertilizer industry, for both product safety and security. The programme was developed by IFA members for IFA members – in collaboration with authorised external auditors SGS and DNV GL.
Currently, an impressive 59 fertilizer companies in 57 different countries are Protect & Sustain certified. These include almost all of the leading global fertilizer producing companies. More recently, industry coverage has been expanded by making certification available to the sector’s non-producers – including fertilizer distributors, traders, port operators and freight and shipment companies.
While Protect & Sustain is unique – being specifically tailored for fertilizers – it is compatible and overlaps with other widely-recognised international quality management systems. It covers, for example, the quality and SHE aspects of ISO 9001, 14001, 45001 and OHSAS 18001 certification. It also has many points in common with Responsible Care 14001, the management system covering the whole chemical industry.
The following nine safety hazards were identified during the commissioning and start-up phase:
- Four safety hazards from improperly tightened flange connections on high-pressure equipment and piping. These led to leakages and even two ruptures. One of these four safety hazards, a leaking flange connection of a carbon dioxide pipeline, caused one person to pass out.
- Two safety hazards were attributable to the damage of a sight glass. This led to one fatality and injuries to 18 people. Sight glasses are a major safety risk factor in urea plants.
- One incident of a severe vibration in a high-pressure ammonia pipeline was recorded during start-up flow conditions.
- Another incident was linked to the potential damage to atmospheric storage tanks, and the loose liners of equipment, that can occur when flushed with steam, as this is liable to condense, creating vacuum pressure.
- The remaining safety hazard was attributed to a high-pressure flush pump. Combined, these incidents led to at least one fatality and injuries to 20 people.
Safety hazards during maintenance
The 16 safety hazards identified during the maintenance phase led to at least 20 fatalities and injuries to a further 19 people. Similar to the construction phase, the relatively high number of deaths and people injured reflects the large numbers of people typically present in the plant during this phase.
Nearly half of the safety hazards during maintenance were connected to a part of the plant that was still in operation or contained process fluid. Such hazards can be mitigated by applying double block and bleed designs. It is also important to be aware of the risks from high-pressure pockets, hydrogen and ammonia explosions during hot work, and the toxicity of ammonia.
Safety hazards can also occur when entering a prill tower or granulator for cleaning activities. Injuries from falling lumps of urea are a risk, for example, and the entrance door to the granulator can close unexpectedly when the fan is put in operation.
Some urea plant maintenance hazards are generic and typical of any chemical process plant, such as working at high elevation, asphyxiation in confined areas and accidents with cranes.
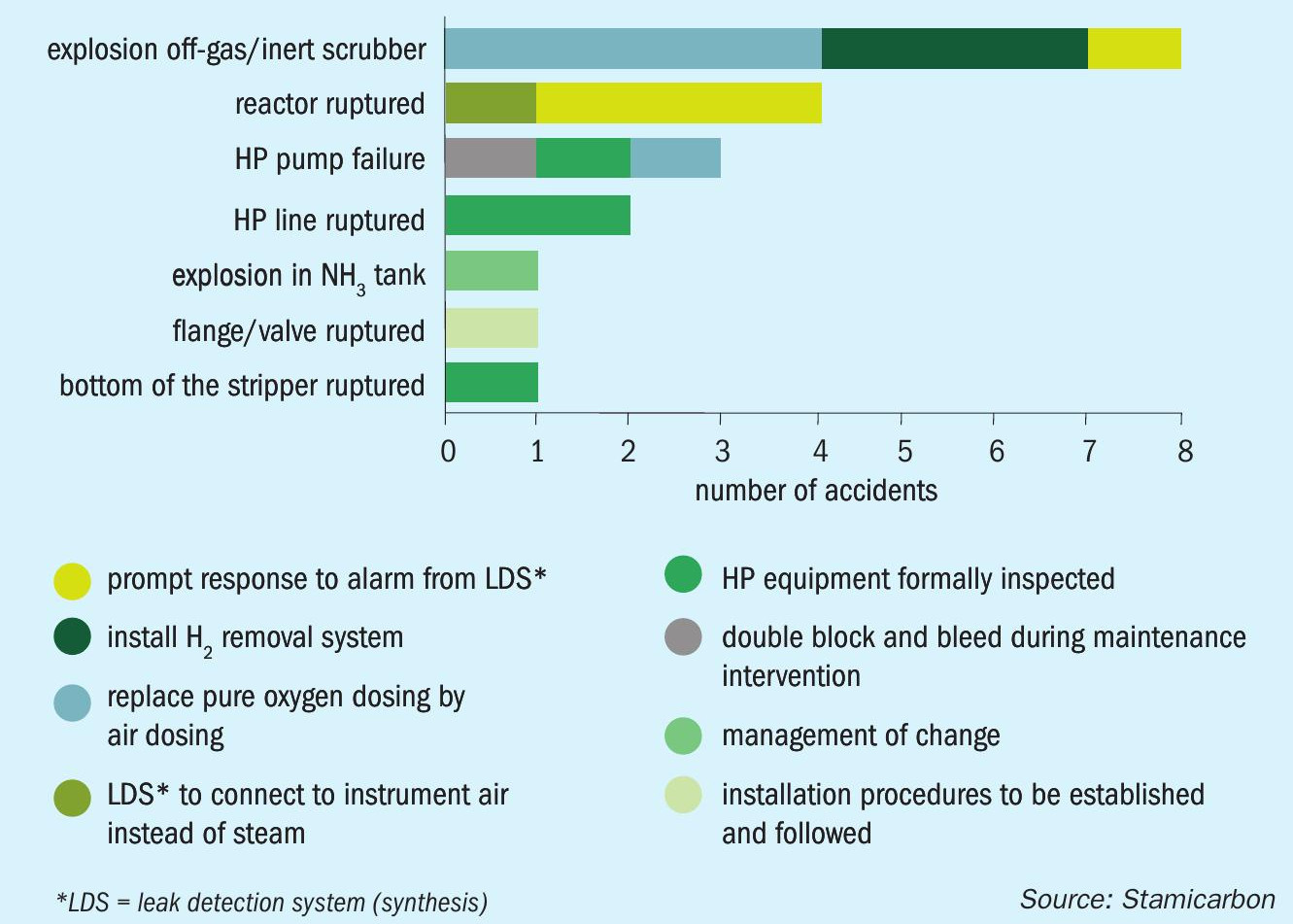
Safety hazards during operation
Some 74 safety hazards were associated with fully operative plants. These led to at least 28 fatalities and injuries to an additional 173 people injured. Many of these safety hazards were linked to process fluid leaks.
In a urea plant, leaks can be caused by corrosive ammonium carbamate finding its way into stainless steel crevices. Such crevices can occur due to improper alignment/tightening of flanges, or result from improper design of valves or accessories.
The ongoing corrosion of stainless and carbon steel parts and piping by highly corrosive ammonium carbamate leaking must be avoided. This makes the proper design, operation and maintenance of leak detection systems critical for high-pressure equipment, flanges, and valves.
High pressure leakage of ammonium carbamate results in the formation of very hard crystals which erode the sealing areas. Once a leaks occur, it is nearly impossible to stop these by tightening bolts. Adequate tightening of flanges and other connections can be challenging in a urea plant because of the limited choice of suitable construction materials. Employing experienced fitters is important. Attempting to stop leaks during operation – by hot bolting/torqueing and installing clamps – has led to five fatalities and four people being injured and should therefore be avoided at any time.
Other safety hazards that also require full and proper attention include backflow, contamination, vibration, atmospheric corrosion, or corrosion beneath insulation.
Seven safety hazards were linked to the presence of hydrogen in the feed streams to the urea plant. Dissolved hydrogen in liquid streams can lead to its presence in unexpected sections of the urea plant. Hydrogen can also enter the urea plant, via process water and/or drain systems, during integration with an ammonia plant.
Analysis of catastrophic incidents
Individual nitrogen sector companies are also collating and analysing safety incident data to help prevent accidents in future – and check that suitable safeguards are in place. Fatima Fertilizer, for example, Pakistan’s largest fertilizer producer, has collected data for major urea plant accidents worldwide stretching back 50 years3 .
The company has identified the root cause of each accident. Of the major accidents, there were:
- Eight incidents of explosions in the scrubber vapour line
- Four incidents of reactor ruptures
- Three incidents of high-pressure pump failures
- Two incidents of high-pressure piping failure
- Two incidents of stripper bottoms rupturing
- One incident of an explosion in an ammonia water tank.
Learning from incidents
In 2017, Stamicarbon invited urea manufacturers to help build a urea incident database. The idea was to create an open, shared SHE (safety, health and environmental) portal that the whole industry can access and benefit from. Stamicarbon hopes that by launching the portal, and enabling the sharing of experiences, the industry can collectively learn from past incidents and near misses – and thereby improve urea plant safety by gaining a better understanding of operational risks1 .
Stamicarbon first recognised nearly 50 years ago that recording major urea plant safety accidents would enable the company to subsequently improve its process design. As well as simply capturing data, Stamicarbon has also conducted its own root cause analysis of the majority of these events (Figure 3).
The company’s original database covered 20 accidents over the period 1967 to 1981. Eight of these were linked to hydrogen explosions. The takeaway lesson from this was to provide the CO2 supply with a hydrogen removal unit and replace pure oxygen dosing with air dosing instead. No hydrogen explosions have ever occurred in plants where both of these control measures have been implemented. This, says Stamicarbon, clearly shows that earning from past incidents clearly does pay off!1
Because its database originally contained only details for 20 major accidents, the question for Stamicarbon was whether these inputs were sufficient to fulfil company objectives set out in its mission statement, i.e. Can the company identify common causes, and failures of preventative measures, and correct these before a high-consequence incident actually takes place? This provided the main impetus behind the 2017 launch of the company’s open-access SHE portal – and the invitation for other companies to share their data on urea safety incidents for the common good1 .
References