Sulphur 390 Sept-Oct 2020
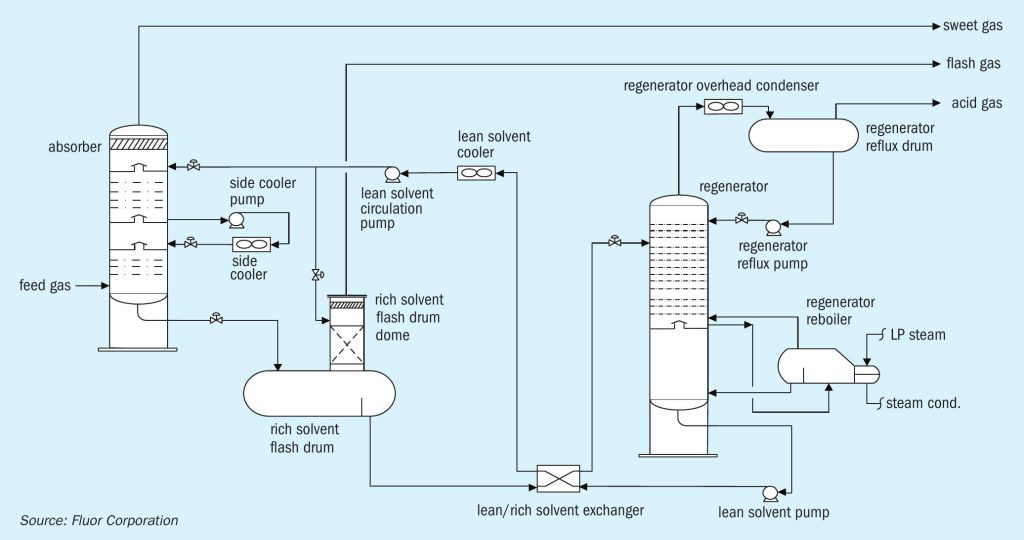
30 September 2020
Two-stage absorption for mercaptan removal
DGA TREATMENT OF ULTRA-SOUR GAS
Two-stage absorption for mercaptan removal
Fluor’s case study of recently constructed ultra-sour gas treating facilities provides new information about the operation of DGA-based AGRUs. B. Lynch and C. Graham of Fluor Corporation discuss how using this knowledge and leveraging the recent improvements to process simulators in the gas sweetening space, Fluor has developed an efficient, flexible, and cost effective solution in the two-stage absorption process to maximise mercaptan removal from ultra-sour gases with minimal equipment.
As the depletion of sweet gas reserves continues, development of ultra-sour gas fields (20%+ H2 S) is integral to meeting the increasing global demand for natural gas. Many sour reserves that had been left untouched due to technological and economic challenges are now being reevaluated in light of recent advancements.
This is especially true in the Middle East, where a large percentage of the region’s gas reserves are sour. Currently, only a very limited number of facilities process ultra-sour feeds, and an even smaller number do so on a large scale. Development of these ultra-sour fields are hindered by challenges such as varying acid gas concentrations from well to well and the presence of organic sulphur species (e.g. COS and mercaptans) that must be removed. The number of producers in this space will surely grow rapidly in the coming years; therefore, it is imperative that acid gas removal solutions are effective, flexible, and cost efficient. Fluor’s recent experiences with its licensed acid gas removal units (AGRU) have led to insights and innovations for ultra-sour gas treating that offer flexibility and cost savings over conventional AGRU designs.
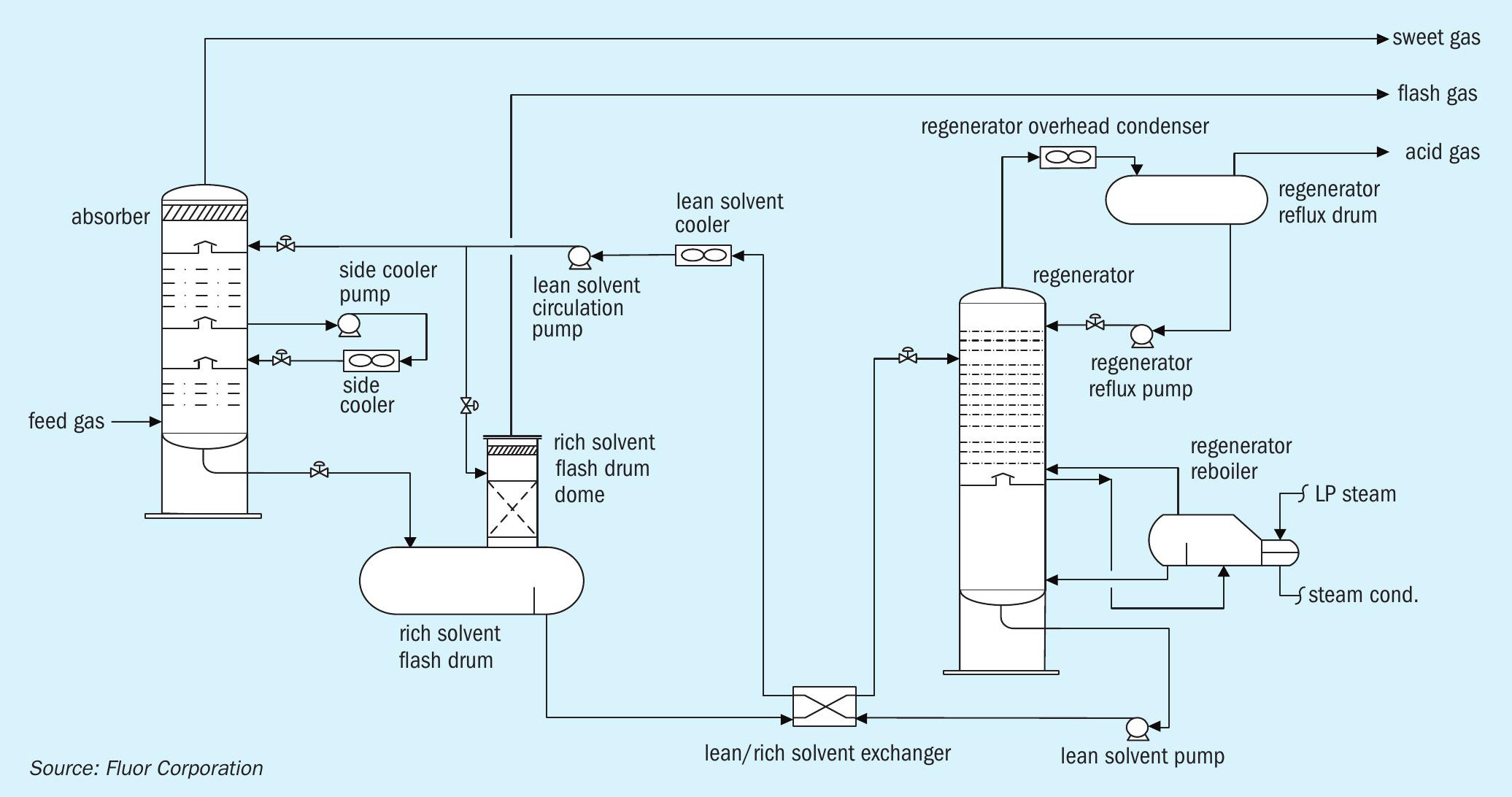
Acid gas removal with DGA
Alkanolamines are commonly used as chemical solvents to remove acid gases (H2 S and CO2 ) from sour hydrocarbon gas streams. Diglycolamine (DGA) is a type of alkanolamine that couples the stability and reactivity of monoethanolamine (MEA) with the low vapour pressure and hygroscopicity of diethylene glycol, which allows for more concentrated solutions and thus lower solvent flow rates. DGA has proven to be very effective at treating large volumes of gas at both high and low absorption pressures. Even at high ambient temperatures, DGA can produce sweet gas with below 4 ppmv H2 S1 . Unlike selective amines that result in CO2 slip into the treated gas, DGA can also remove CO2 down to ppm levels. CO2 removal improves the heating value of sales gas and is imperative to prevent freezing in downstream low temperature units such as NGL recovery and LNG liquefaction. Another benefit of DGA is removal of COS and CS2 from the feed gas. Removal efficiency for these components can exceed 90%. As such, DGA is the solvent of choice for the Fluor Improved EconamineSM process. Fig. 1 provides a process flow diagram of a typical Improved EconamineSM flow scheme.
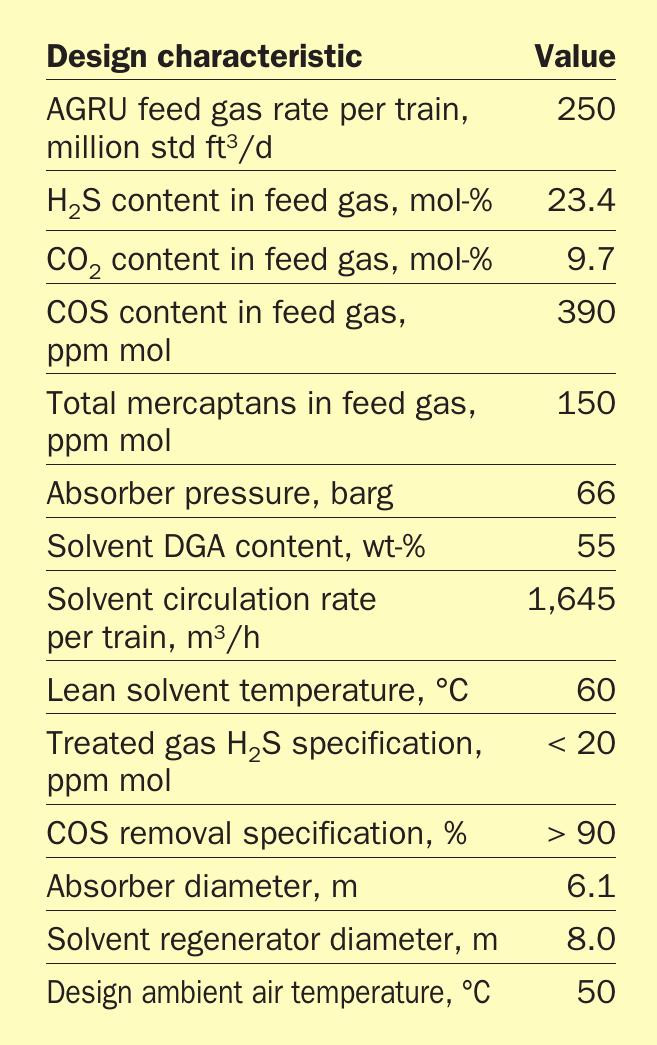
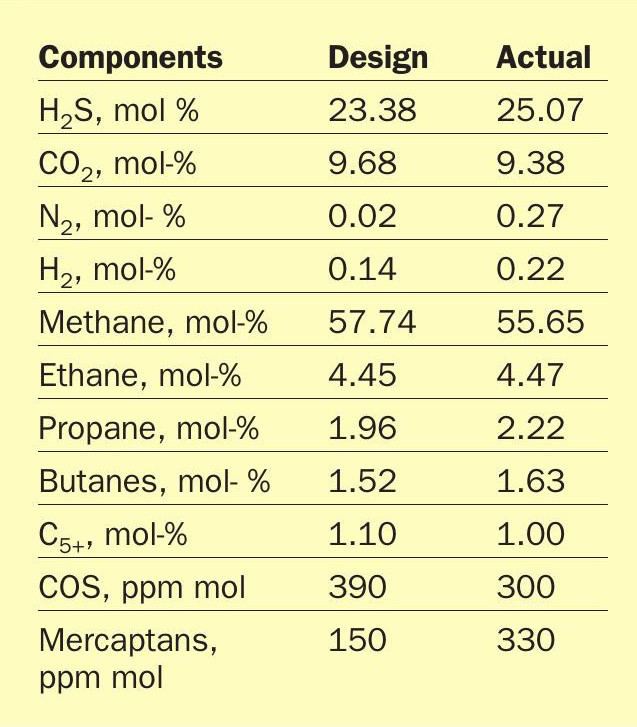
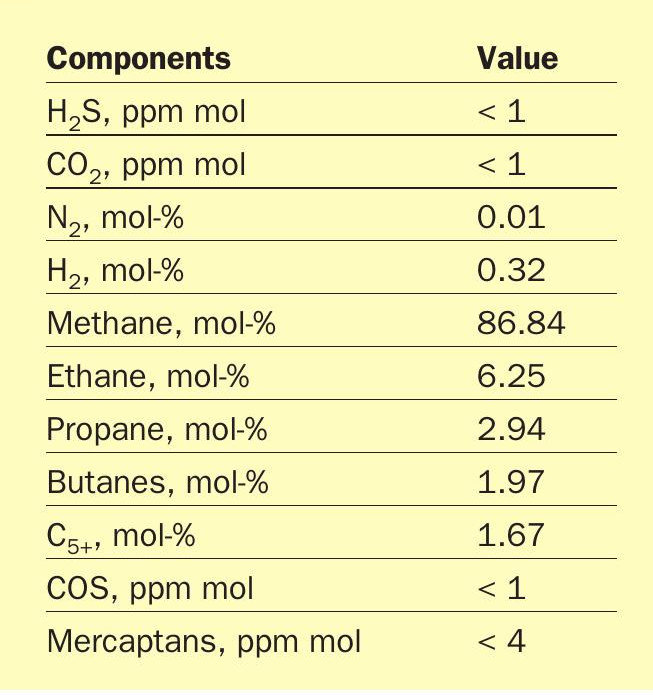
Experience treating ultra-sour streams with DGA
Due to the small number of facilities that treat ultra-sour feeds on a large scale, there is limited experience regarding the design and operation of such facilities. Recently, a high capacity AGRU based on Fluor Improved Econamine DGA technology, was constructed and commissioned. Table 1 provides basic design information and operating conditions for the facility.
As Table 1 shows, this facility provides a unique challenge of treating a large volume of very sour gas (almost 35 mol-%) down to a standard sales gas specification in a very hot climate. More information is available on the design of these units in Reference 2.
Performance of this unit, after a successful start-up and stable operation, provided valuable data for a detailed analysis of the AGRU. This study has yielded new insights into ultra-sour gas treatment utilising DGA. Table 2 provides a comparison between the design sour gas composition and the average actual sour gas composition during operation. The actual sour gas composition was determined by laboratory analysis of samples taken at site.
Although the H2 S content in the actual feed gas is greater than design, the unit effectively removes all acid gases as shown by the extremely low treated gas H2 S and CO2 content in Table 3. The 25.1 mol-% of H2 S and 9.4 mol-% of CO2 in the feed gas are treated to less than 1 ppm(mol) in the sweet gas, demonstrating that DGA is an extremely effective solvent for ultra-sour feed gases.
A challenge with ultra-sour gas treatment is the removal of organic sulphur species such as carbonyl sulphide (COS), carbon disulphide (CS2 ), and mercaptans. These organic sulphur species are present in many sour gases and must be removed to meet total sulphur specifications for the sales gas and NGL products. Operating experience has proven that DGA is effective for COS removal above 90% in the majority of applications, thus prompting the COS removal guarantee listed in Table 1. DGA has also proven ability to remove mercaptans, but no data existed for the extent of removal at conditions similar to the referenced facility. As such, a mercaptan removal guarantee was not made and downstream provisions for mercaptan removal were included in the design.
Table 3 also shows low concentrations of COS and mercaptans in the sweet gas, indicating that for this system, DGA removed not only the majority of COS in the feed, as expected, but the majority of the mercaptans as well. To prove the long-term sustainability of organic sulphur removal, daily sample data for the organic sulphur content of the feed gas and treated sweet gas was collected over a 14 month period. This data has been consolidated into Fig. 2 and Fig. 3.
Fig. 2 shows that the feed gas organic sulphur content ranges between 500 ppm (mol) and 800 ppm(mol) for the majority of operation. Once treated, the organic sulphur content in the gas is consistently below 10 ppm (mol) as shown in Fig. 3. Table 3 shows that the average COS content in the sweet gas is less than 1 ppm (mol), so the remaining organic sulphur in the sweet gas are mercaptans. This corresponds to a total mercaptan removal efficiency of well over 90%.
Mercaptan removal by DGA occurs through both chemical and physical absorption. The dominating mechanism varies from system to system and is dependent on the operating conditions and the specific types of mercaptans in the feed gas. From a chemical perspective, mercaptans have acidic properties, like H2 S, but because of the hydrocarbon functional group, they are much weaker acids than H2 S. Mercaptans behave less like acids and more like hydrocarbons as the hydrocarbon chain length increases. Due to their acidic properties, mercaptans chemically react with amines, but these chemical bonds are weak and are readily dissociated by more acidic compounds (e.g. H2 S and CO2 ). The solubility of mercaptans in amine solutions increases with increased solvent alkalinity (less absorbed H2 S and/or CO2 ), and decreases with increased temperature1 . Similarly to other physical absorption systems, the rate of physical absorption of mercaptans by DGA increases with an increase in absorber pressure. This is due to the increased partial pressure of mercaptans in the gas.
The extent of mercaptan absorption in this system can most likely be attributed to the following:
- high absorber pressure (66 barg) promoting physical absorption;
- high solvent circulation rate to ensure H2 S and CO2 removal;
- limited chemical absorption competition by H2 S and CO2 in the upper trays.
Simulation validation
Using insights gleaned from the operating data, a simulation model of the AGRU process was built. Developing an accurate model (if possible) is imperative to any optimisation efforts or future design improvements for ultra-sour facilities. It should be noted that at the time that this facility was designed, process simulators were limited in their application to the extreme conditions in which these units operate. Recently, however, simulators such as Bryan Research and Engineering ProMax v4.0 (released in 2016) have seen major improvements in mass and heat transfer based absorption models, resulting in improved accuracy and consistency with operating data. Table 4 compares operating data for August and September of 2016 to ProMax v4.0 simulation results of the AGRU.
Based on the comparison in Table 4, the new mass + heat transfer column models in ProMax v4.0 can provide accurate results for large, ultra-sour facilities using DGA solvent. Predicted acid gas removal is in line with operational results with virtually no error.
The predicted column temperature profile, which is an accuracy indicator of trayby-tray acid gas absorption, also agrees well with operational data. The model slightly under predicts the absorption in the bottom tray and shifts some absorption up to the second tray, as seen by the smaller temperature differential between the trays compared to actual results. However, by the third and fourth trays, the predicted profile is in line with observed results.
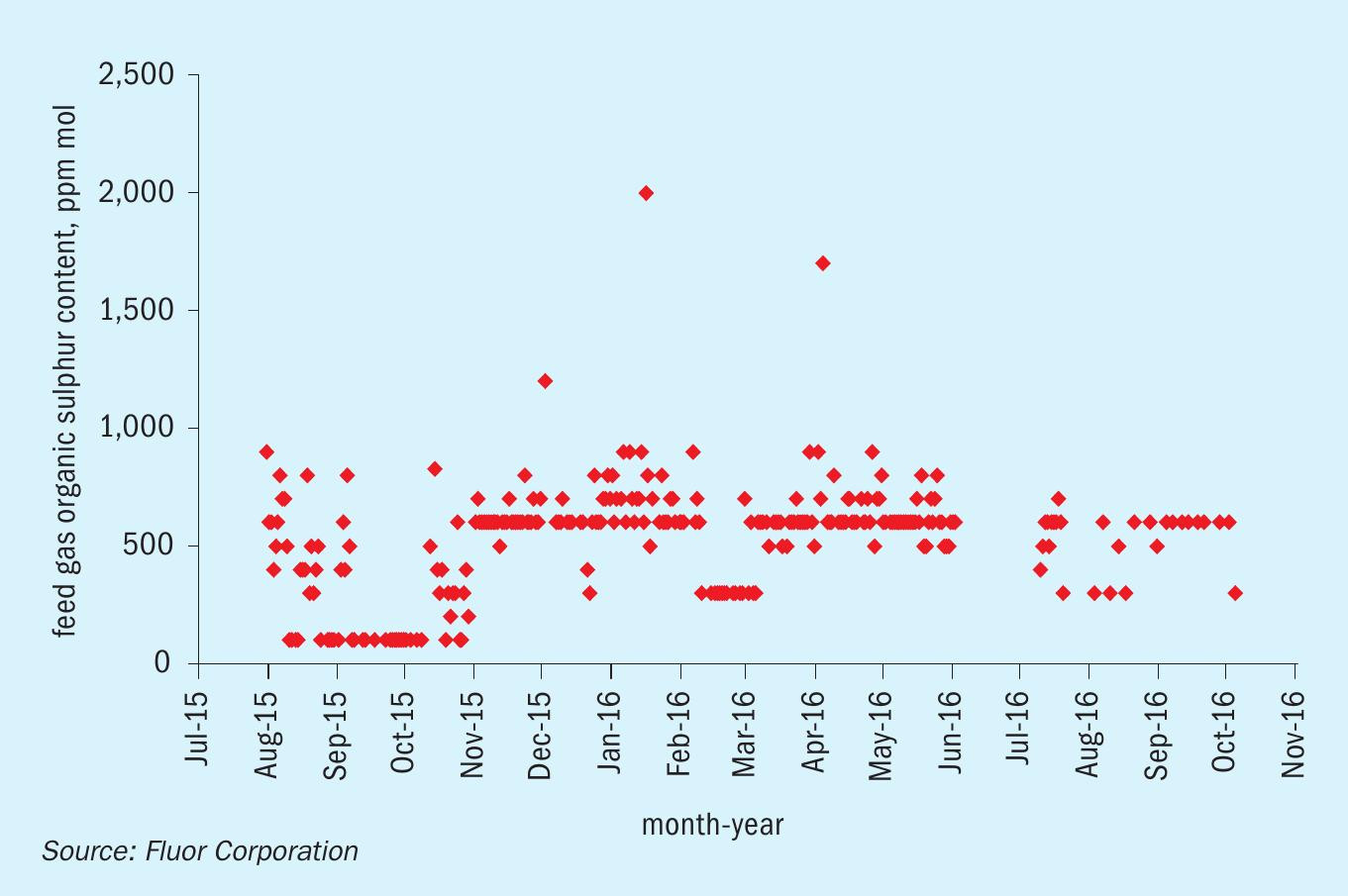
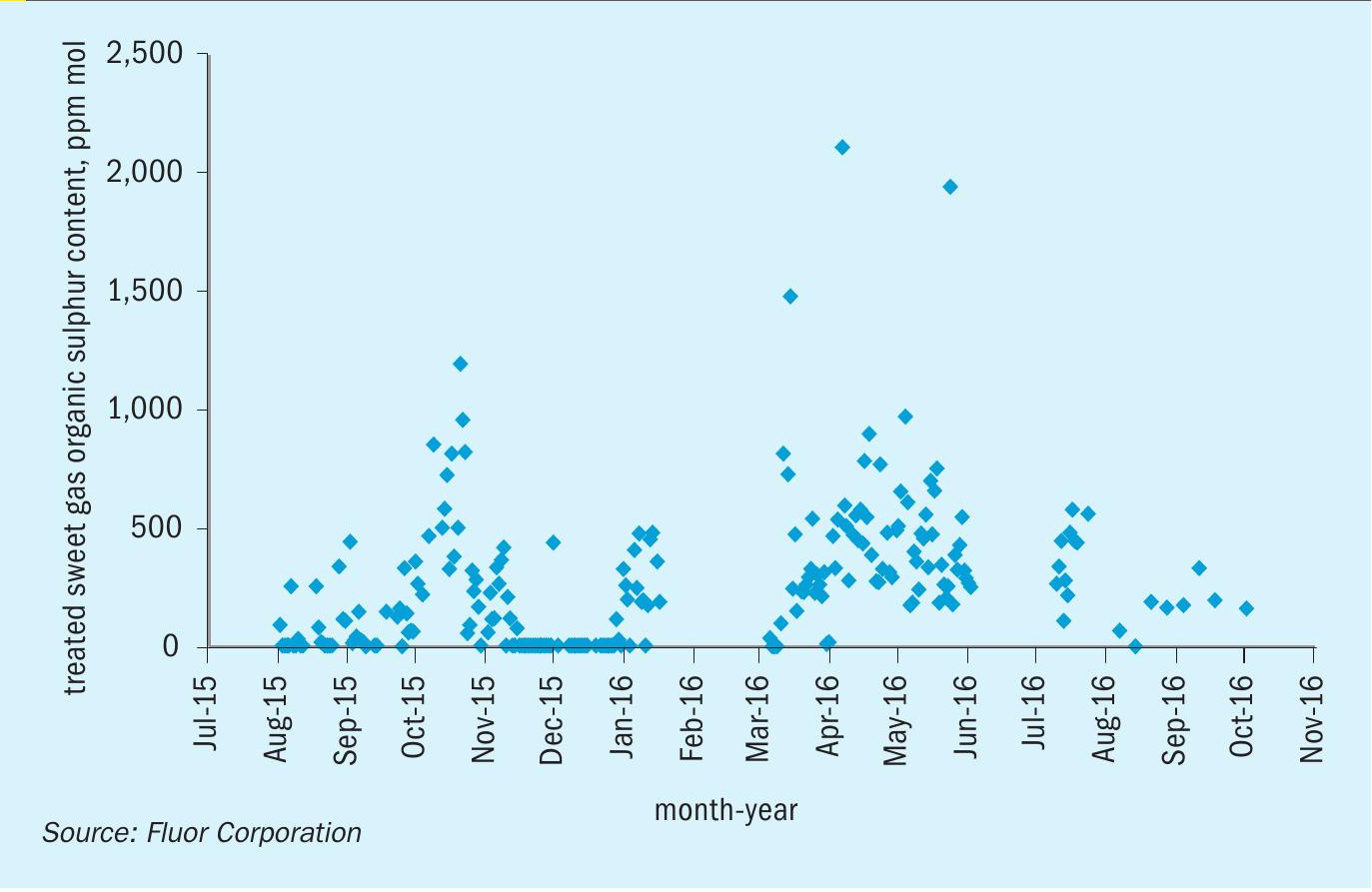
For mercaptan removal prediction, the model is not as accurate. Predicted methyl mercaptan (C1 -mercaptan) absorption is very accurate (99.8% vs > 99% in actual operation). However, predicted ethyl mercaptan (C2 -mercaptan) and propyl mercaptan (C3 -mercaptan) removal is much less than observed removal (64% vs > 99% and 26% vs 99%, respectively). The accuracy decreases as the hydrocarbon chain length on the mercaptan increases. This is most likely due to under-prediction of the chemical absorption influence of heavier mercaptans. The accurate prediction of methyl mercaptan removal should prove to be important in future designs as methyl mercaptan often makes up a large fraction of the total mercaptan content in sour gas. This is evidenced by the much better agreement of predicted total mercaptan removal to operating data when compared to predicted ethyl and propyl mercaptan pickup.
The comparison in Table 4 shows that the improvements to ProMax v4.0 prove that the simulator will be an important design tool for future ultra-sour developments. While the mercaptan removal predictions could be improved, they currently provide a solid starting point. At the very least, they will contribute to slightly conservative designs, which is much preferred to the alternative. The accurate results also allowed for further optimisation and improvement of Fluor’s Improved Econamine process, as discussed in the following sections.
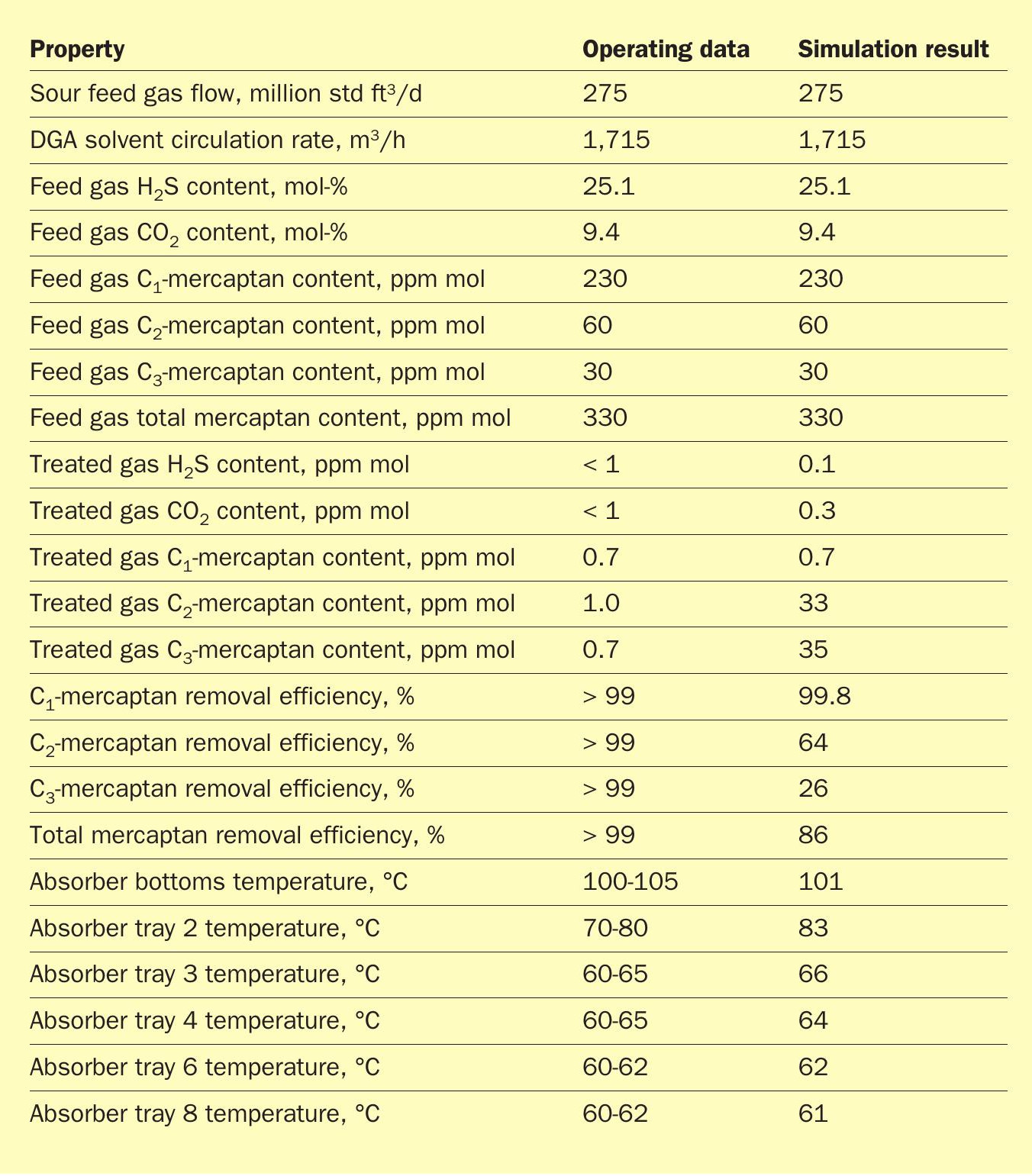
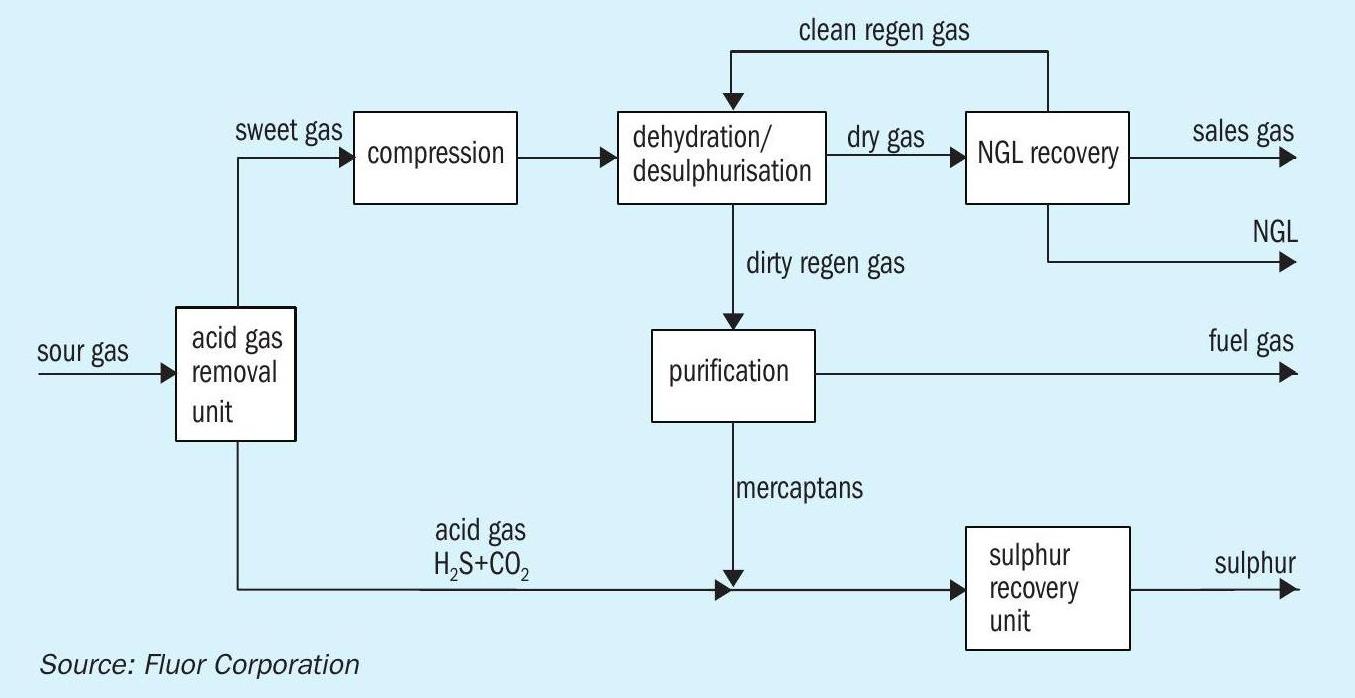
Design for low pressure ultra-sour streams
This case study has demonstrated that high pressure absorption using DGA solvent is effective in removing mercaptans from ultra-sour gases. However, high pressure processing of ultra-sour gases carries major health, safety, and environmental (HSE) risks and impacts such as the following:
- large exclusion zones and unit setbacks leading to larger facility plot areas and increased site preparation requirements;
- requirement to use self-contained breathing apparatus (SCBA) or hard line air requirements when entering sour gas processing units;
- stringent design requirements;
- strict operating and maintenance procedures.
Reference 4 provides a detailed description of the various requirements for safe processing of very sour streams. These restrictions may be manageable for small facilities in more remote locations, but can have significant design and operability impact for larger facilities. For ultra-sour feed gases with a relatively low gathering system pressure (either due to HSE or reservoir limitations), the costs and risks are greater since the feed gas must be compressed to a higher pressure before treating. In an instance such as this, the sour gas compressors would be constructed of expensive metallurgy and carry additional risk due to the higher number of potential leak points. To mitigate these risks, treating of ultra-sour gases is typically performed at low pressure. However, operating experience has shown that low pressure systems suffer from poor mercaptan removal efficiency. As a result, a separate system for mercaptan removal is usually required, adding complexity and cost to the design. One example is the use of a downstream molecular sieve unit to remove both mercaptans and water moisture. Including mercaptan removal in the molecular sieve requires more sieve volumes as well as the need for an auxiliary purification system (e.g. Selexol) to remove the mercaptans from the regeneration gas. Fig. 4 shows the typical line-up of units required for an ultra-sour feed gas with mercaptan removal using molecular sieves.
A more attractive solution is the patented Fluor two-stage absorption5 process. The two-stage absorption process was developed to take advantage of improved mercaptan removal at higher pressures in a way that maintains the health and safety advantages of the low pressure absorption configuration. The improved mercaptan removal will reduce or, in some scenarios, completely eliminate the need for downstream mercaptan removal. The auxiliary purification system can also be reduced or eliminated, resulting in significant cost savings for the overall facility. Fig. 5 shows the optimised line-up of units made possible through the two-stage absorption process.
The newly developed process is comprised of two stages. The first stage removes the bulk of H2 S at the lower feed gas pressure. The semi-treated gas, with relatively low H2 S partial pressure, is then compressed to the higher pressure second stage at which the remaining H2 S, CO2 , and organic sulphur species are removed to achieve treated gas specifications. Fig. 6 shows a process flow diagram for the Fluor two-stage absorption process.
The feed gas is fed to the LP absorber where it is contacted counter-currently with a semi-rich solvent stream from the HP absorber to remove the majority of the acid gases. The level of acid gas removal in the LP absorber depends on the operating pressure of the HP absorber and HSE requirements. The semi-treated gas leaves the top of the LP absorber and is sent to the semi-treated gas compression train. Once the semi-treated gas is compressed, it is fed to the HP absorber where it is contacted counter-currently with lean solvent from the solvent regeneration system. The lean solvent removes the remaining H2 S and CO2 in the semi-treated gas along with a significant amount of the mercaptans. The treated gas leaves the top of the HP absorber for further processing. The semi-rich solvent from the bottom of the HP absorber is flashed across a control valve and then routed to the LP absorber. The rich solvent leaving the bottom of the LP absorber is regenerated in a typical AGRU solvent regeneration system.
Although the Fluor two-stage absorption process requires two absorber columns, the total number of trays required can be identical to a single-stage process. In some instances, the HP absorber can be a smaller diameter than the LP absorber due to the higher pressure and the bulk removal of H2 S and CO2 occurring in the LP absorber.
Table 5 compares the simulation results between a low pressure, single-stage absorption process and the Fluor two-stage absorption process. The data is based on a feed gas that contains approximately 22 mol-% H2 S, 10 mol-% CO2 , 100 ppm mol methyl mercaptan, 40 ppm mol ethyl mercaptan, and 160 ppm mol total mercaptans. The feed gas enters the system at 20 barg and 35°C. For the single-stage process, the absorber operates at roughly 20 barg. For the two-stage process, the LP absorber operates at roughly 20 barg and the HP absorber operates at roughly 70 barg. The absorber in the single-stage process has 23 trays. In the two-stage process, the LP absorber has five trays, and the HP absorber has 18 trays, for a total of 23 trays. The lean solvent concentration is 55 wt-% DGA and the solvent circulation rate is the same for both scenarios. The lean solvent temperature is 58°C for both scenarios, which is typical for air-cooled solvents in the Middle East.
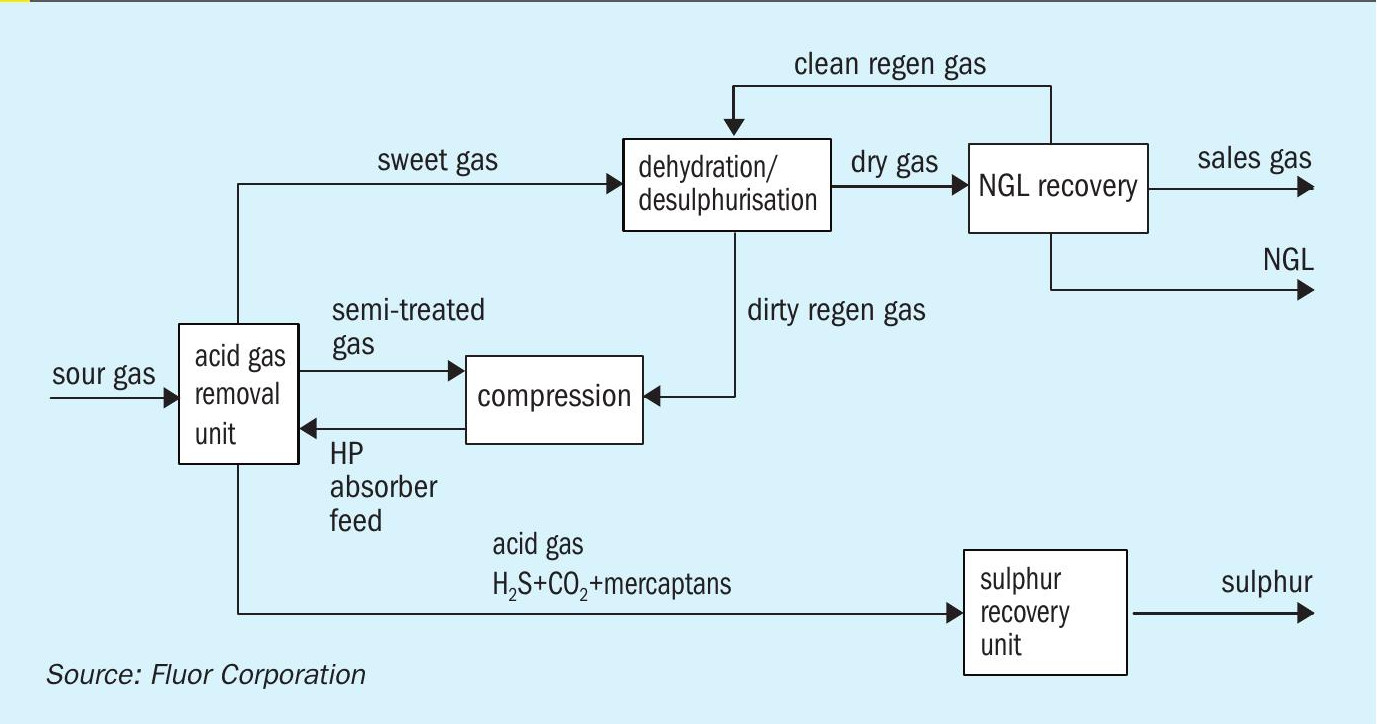
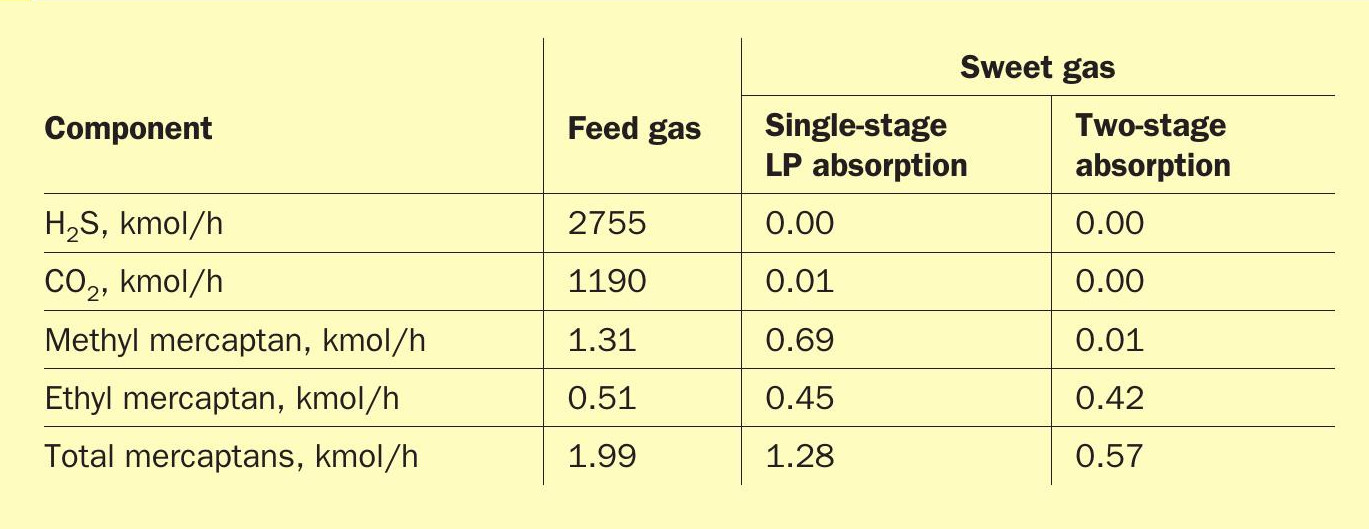
Table 5 shows that the single-stage process results in 47% methyl mercaptan removal, 12% ethyl mercaptan removal, and 36% total mercaptan removal. The two-stage process results in over 99% methyl mercaptan removal, 18% ethyl mercaptan removal, and 71% total mercaptan removal. These results indicate that the two-stage system provides a significant advantage in methyl mercaptan removal, which leads to roughly twice the total mercaptan removal from the feed gas. However, operating experience for single-stage, high pressure absorption systems (as described in a previous section) shows that ethyl and heavier mercaptans exhibit higher removal efficiencies than indicated in the simulation results. This further supports the notion that a two-stage system has appreciable mercaptan removal capabilities compared to a single-stage, low pressure system.
The Fluor two-stage absorption process can offer several benefits compared to the typical single-stage absorption process such as the following:
- improved mercaptan removal;
- similar equipment count in AGRU;
- minimal HSE risks and impacts;
- reduction in size or elimination of downstream mercaptan treatment units which saves capex and opex:
– molecular sieves
– regeneration gas treatment
– Merox units in a NGL recovery unit;
- reduced plot space compared to single-stage, high pressure treatment
Conclusion
As the number of sweet gas reserves continues to decline, the development of ultra-sour gas reserves is essential to meet the global natural gas demand. Development of these ultra-sour reserves encounters many technical challenges, including organic sulphur removal, that were previously met with conservatism due to limited operational experience. Fluor has developed a two-stage absorption process utilising DGA to maximise mercaptan removal from ultra-sour gases with minimal equipment.
Moving forward, innovative solutions such as these will be crucial to meet the growing need for ultra-sour gas development.
References