Nitrogen+Syngas 370 Mar-Apr 2021
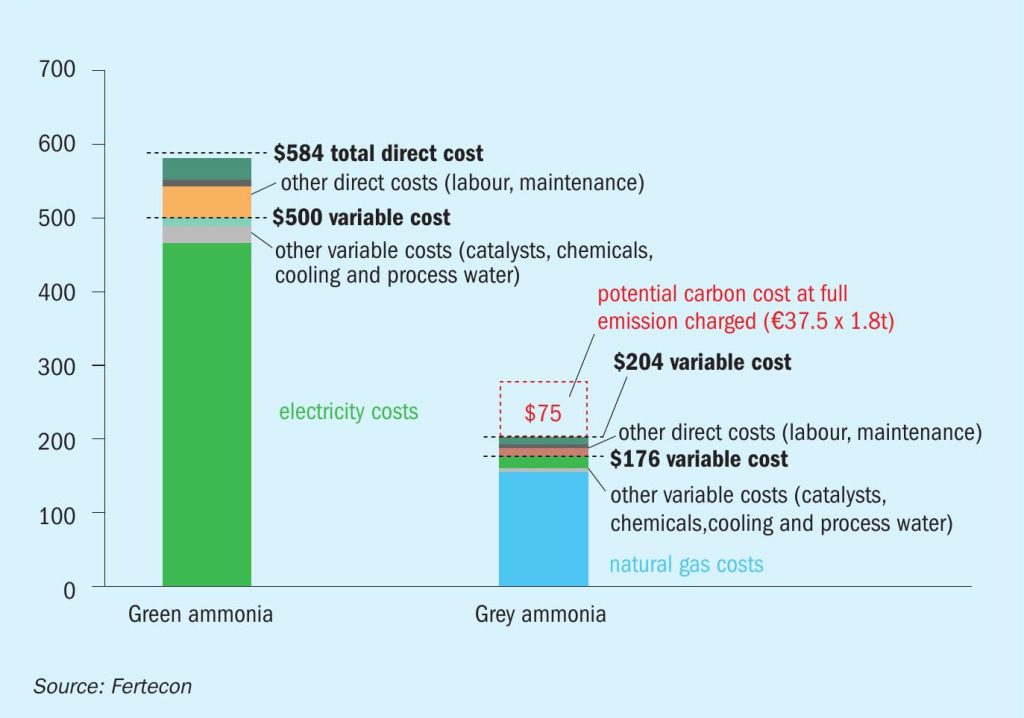
31 March 2021
Towards a sustainable nitrogen fertilizer industry:
ENVIRONMENT
Towards a sustainable nitrogen fertilizer industry:
Part 2: Decarbonising ammonia production
Georgy Eliseev, Principal Analyst at Fertecon for IHS Markit, looks at the medium to long term outlook for both ‘green’ and ‘blue’ ammonia production.
Ammonia production capacity amounts to 220 million tonnes globally, with ammonia production for 2020 being estimated at 190 million tonnes. The vast majority of all ammonia produced, with negligibly small exceptions, is a result of hydrocarbon feedstocks – mostly natural gas or coal – via steam reforming and Haber-Bosch synthesis.
Air provides the nitrogen for the creation of ammonia, which is easily obtained in large quantities from the atmosphere. With minute concentrations in air, obtaining hydrogen is a far more difficult task. At present, the steam reforming of methane is the most convenient way to produce the hydrogen necessary for the synthesis of ammonia in the required quantities and at a reasonable cost. Natural gas, water/ steam and air represent the feedstocks, and ammonia, steam and CO2 are the outputs of this process. In the case of coal being used as a feedstock (mainly in China), a coal gasifier is also required before the reforming stage.
The amount of CO2 output depends on the rate of natural gas, or energy, consumed in the process. One of the main improvements in ammonia technology since the single train ammonia concept was developed in the 1960s has been in the area of energy efficiency, and the reduction of natural gas consumption per tonne of ammonia. The best plants today consume less than 28 MMBtu of natural gas to produce 1 tonne of ammonia. In such cases, the output of CO2 will be below 1.6 tonnes per tonne of ammonia. However, the majority of natural gas-fed plants actually consume anywhere from 28 to 41 MMBtu/tonne and so emit from 1.6 to 2.3 tonnes of CO2 per tonne of ammonia. Coal-based plants emit considerably more than this, approximately 3.5 tonnes of CO2 or even greater amounts.
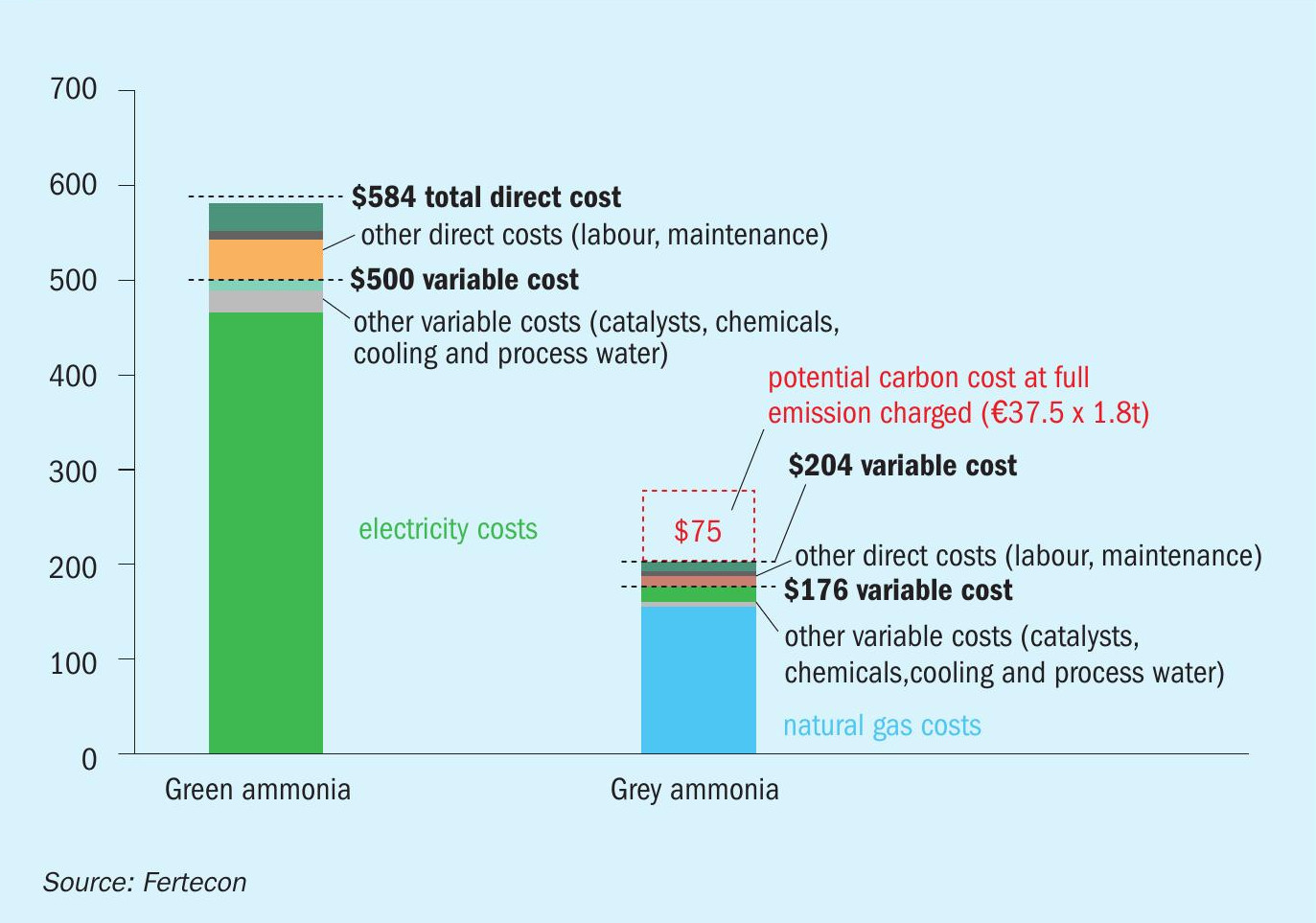
With a global ammonia production of 190 million tonnes in 2020, including about 45 million tonnes of coal-based gasification technology, the annual CO2 emissions from ammonia industry can be estimated at 380-400 million tonnes of CO2 .
Global CO2 emissions have been estimated at 34-35 billion tonnes of CO2 for 2020, slightly decreasing as a consequence of the Covid-19 crisis. The share of global emissions represented by the ammonia industry is thus estimated at 1.1-1.2%.
More than half of all ammonia produced globally is used for urea production, and the CO2 captured from the ammonia process is redirected into urea production, as CO2 is a necessary component for urea. However, once applied to soil urea fertilizer releases CO2 into the air, and therefore urea fertilizer production is not a good means of reducing carbon emissions. In addition, the use of urea solution for removing NOx in diesel engines and in power plants (AdBlue/DEF) also releases CO2 .
Policy and incentives
Following the Covid outbreak, people are more concerned with the environment and climate change issues in general. Ammonia producers have accordingly come under additional pressure. Shareholders, investors, politicians, regulators, the public; all are intent on seeing immediate plans of action being rolled out to eliminate carbon emissions. Governments are beginning to do away with any support given to CO2 -emitting projects. Hence, accustomed to the relatively low cost of carbon emissions (paying only for emissions that exceed the allowance benchmark), fertilizer companies in many regions can expect costs to rise.
Looking at Europe specifically, the European Emission Trading System (ETS) is one of the most advanced worldwide, and boasts high liquidity among the several regional carbon trade platforms currently in place. A benchmark allowance for emissions based on industry best practices has been set. For ammonia producers, this allowance is set at 1,619 kg of CO2 for 1,000 kg of ammonia. This corresponds to the average emission of to the 10% most efficient European plants. Producers are not required to pay if they remain under this benchmark, and will pay for any emissions exceeding this allowance. From 2021, the benchmark will be reduced year by year, which will lead to an increase in costs for ammonia producers.
Recently, there has been considerable growth in CO2 prices in the ETS, figures rising from ~e25 in 2020 to e38 in Feb 2021. However, this level is still not yet sufficient to provide the necessary competitiveness for green ammonia. It is logical to expect that with the growth in demand (as producers will need to buy more carbon allowances at the ETS) carbon prices will also naturally see a rise. At the same time, government and public funding for the support of green ammonia projects will be essential over the next 10-15 years unless green ammonia costs can somehow decrease and become competitive.
Efforts to decarbonise ammonia in Europe (and in other regions) will also inevitably lead to the introduction of border barriers, brought in in order to block ‘carbon leakage’. The new Carbon Border Adjustment Mechanism in Europe, taking the form of an import carbon duty or an extension of ETS rules to apply to foreign suppliers, is expected to be in place by 2024.
‘Blue’ ammonia
‘Blue’ ammonia differs in only one way from conventional or ‘grey’ ammonia: the CO2 flow from combustion is either captured and stored or sequestered; it is not redirected into the urea process. Instead, it is stored or used in such a way which prevents it from escaping into the atmosphere. However, blue ammonia is not exactly carbon-free, as this process has not been perfected and some small quantity of carbon can still make its way into the atmosphere, hence it would be better to call this type of ammonia ‘low carbon’. It is considered to be a temporary solution while green ammonia technologies are maturing.
“By 2035 the costs of green ammonia may become competitive with those of grey ammonia.
Carbon dioxide from the ammonia process can be injected underground and sequestered in some geological formations. Such projects exist, the Wabash Valley Resources in the USA and Horizon Energi in Norway, for example, as well as a number of projects under consideration in Australia and Canada. Each of these projects will have a long future helping to get rid of carbon by injecting it underground, usually in a liquefied form, however this method cannot be used for all the carbon emitted by the ammonia industry as a permanent answer to the problem.
Another similar way is to take the CO2 produced and inject it into oil fields in a process known as enhanced oil recovery (EOR), in which gases such as CO2 are injected into oil layers so as improve the efficiency and yield of oil production by pushing additional oil into a extraction wellbore. This practice has been actively used since the 1970s. The disadvantage of this method is that CO2 is sequestered, but at the same time more carbon is extracted with the oil taken out.
CO2 can be converted into solid carbon substances, such as carbon black, graphite, or fly ash. These materials have their applications, although these are somewhat limited. Saudi Aramco uses this concept to produce polypropylene carbonate polyols with CO2 instead of methane as a feedstock. Other ideas also exist with regard to eliminating or soaking up the CO2 created during the production of ammonia, such as producing chemicals, plastics, nanofibers and so on. CO2 can also be used to improve the quality of concrete. Finally, there is the biological sequestration of CO2 by plants into soil. Scientists are working on ways to accelerate this process. This may represent a long-term solution for CO2 stream sequestration; making artificial soil and using it to soak up carbon.
‘Green’ ammonia
For full decarbonisation a carbon-free way for the production of ammonia is necessary, and this is the idea of green ammonia – which is based on the electrolysis of water. Some 10.5 MWh of green electricity are needed to split a molecule of water and separate hydrogen from oxygen. Oxygen is a by-product from this process. Unlike in the steam-reforming process where air is injected to add nitrogen, in the green ammonia process nitrogen should be separately produced in an air separation unit. Then, both hydrogen and nitrogen are directed into the same Haber-Bosch synthesis to be converted into ammonia. In this process, carbon is not present in any sense, so this really is a carbon-free process.
The technology of green ammonia is under development at the present time, and it is already known that the energy consumed by electrolysis may be reduced to less than 8 MWh. This is vital for the use of ammonia as an energy carrier, as its energy content is 5.2 MWh – so the loss of energy during this transformation to ammonia is currently about half. Moreover, new catalysts may be developed to reduce temperature and pressure in the ammonia converter, which should reduce costs accordingly. There is an idea that one-stage green ammonia production could be viable, so that not hydrogen, but ammonia rather would be produced during electrolysis.
Costs gap
There is still a notable gap in both the Opex and Capex for green and grey ammonia. The direct costs, including energy, chemicals, catalysts, process and cooling water, labour and maintenance, calculated for Europe, are almost 3 times higher for green ammonia (Figure 1) than for traditional ammonia. Even if the full costs of carbon emission credits were added to the grey ammonia costs, green ammonia will still remain uncompetitive. Electricity represents about 80% of the direct costs of green ammonia, whereas natural gas represents 76% of grey ammonia costs.
Reducing the costs of green electricity along with the development of green energy (via economies of scale) and advances in technology, on the one hand, and the introduction of carbon taxes and rising natural gas prices on the other, will reduce the Opex gap, so that by 2035 the costs of green ammonia may become competitive compared with those of grey ammonia.
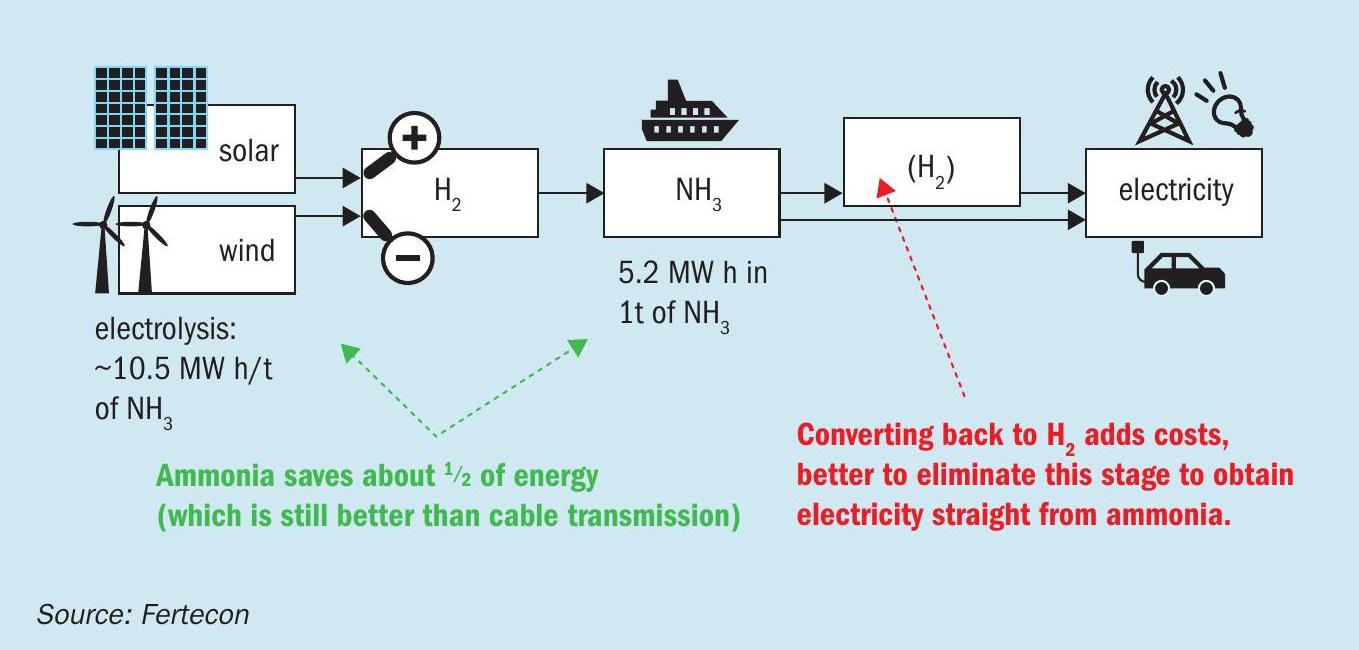
Regarding the Capex, our estimates show that the capital expenditure per tonne of nominal ammonia capacity amounts to $2,700 for a hypothetical green ammonia plant (400 t/d), or $1,500 in the case of a small green hydrogen plant being added to an existing ammonia unit. The Capex of recent standalone grey ammonia projects was from $826/t (Yara/BASF Freeport 2018 – a short cycle plant which receives H2 and N2 from a supplier) to $1,203/t (PAU Indonesia 2018, full cycle), and up to $1,342/t (Salalah Oman 2021, a smaller sized plant).
Is there enough green energy?
However, is there enough green energy to decarbonize the ammonia industry as it is at present? If the electricity requirement of electrolysis units if all existing ‘grey’ ammonia facilities were replaced with green is compared with the current output of solar, wind and biomass electricity available in 2019, it can be seen that total decarbonising of ammonia production would require 67% of currently existing green energy, and – in many regions – more than 100% of existing green energy capacity. If one decides to invest in a green ammonia plant, the first question is: where can this green energy be obtained from? And in most cases the answer would be to invest first in a solar or wind power plant.
The future of urea
One additional point which could slow down the process of decarbonizing the fertilizer industry is urea. Urea is the most popular nitrogen fertilizer across the world, and global consumption in 2020 was over 176 million t/a (China alone consumes 50 million t/a, and India 34.4 million t/a). Urea production absorbs more than 50% of ammonia produced globally. In the absence of a source of CO2 (in the case of green/ blue ammonia), urea will not be produced. However, farmers in India, China and a number of other countries are used to urea, and it will be rather difficult to find a substitute.
Green urea may be produced using biomass, according whether biomass is available in large quantities, while the utilisation of CO2 captured from the air is still extremely expensive, as a consequence of the very low concentration of CO2 in air – only 0.04%.
Strategies for fertilizer companies
At present, there are several green ammonia projects at various stages of implementation in the fertilizer industry. These projects may be divided into 3 groups.
- The first group consists of only one plant, which is scheduled to be completely electrified in the future. The Yara Porsgrunn plant produces 0.5 million t/a of ammonia and is located in Norway. The company has stated that provided power is available at the site and the required public co-funding is in place, the project could be realized within 5-7 years. In fact, electrolysis for this plant is likely to consume 38% of Norway’s wind power. Norway does also possesses a large amount of hydro-electric power generation, so this may also be used for decarbonising Porsgrunn.
- The second group is represented by a number of projects, including Yara Sluiskil in the Netherlands, Yara Pilbara in Australia, Fertiberia in Spain, and CF Industries in the US, which plan to start working with low levels of electrolysis, which will provide their existing ammonia converters with some percentage of carbon-free ammonia, usually about 10% of overall ammonia production. There will be no increase in ammonia capacity, but a there will be a reduction in natural gas use which will be, in turn, replaced by green hydrogen. The average emission per tonne of ammonia will thus be reduced by 10%. The first project from this group may be already on stream this year in Puertollano, Spain, where Iberdrola will supply hydrogen to the Fertiberia ammonia plant.
- The third group consists of fertilizer and industrial nitrate producers who import ammonia, and green ammonia plants will allow companies to reduce or eliminate imports. OCP in Morocco and Enaex in Chile, with partners, are considering such plants. Both countries are blessed with sufficient sunshine to provide green ammonia projects with solar power.
Oddly enough, though, as yet there are still no blue ammonia projects in the industry, which could be seen as a more affordable alternative.
Carbon-free ammonia for green power
Ammonia contains hydrogen and is easier in terms of handling than hydrogen itself. Therefore, it is logical to use ammonia as an auxiliary element in hydrogen energy economics, for example, for the transportation and storage of ammonia.
There are places on the Earth with continuous, long-lasting, and predictable sunshine. This, combined with wind power to cover periods of darkness, mean that hydrogen and ammonia can be produced with very good economics. Investments in green energy will be directed into such areas, and green energy should then be transported to the areas where it will be used. This will lead to the emergence of green energy trade flows between the continents).
Green ammonia may also be the best form in which green hydrogen (or green energy) can be shipped from e.g., Australia to Japan or Europe, or from North Africa to North America and so on. Although converting electricity to ammonia leads to the loss of half of the energy which could be yielded, it is still better than the losses involved in cable transmission over long distances, and one of the few ways to facilitate energy seaborne transportation (Figure 2). There are still additional methods of reducing costs and improving the efficiency of ammonia for the transportation of energy.
Ammonia can also be used as a means of energy storage, given that green energy is highly intermittent and often not easily transmittable, while the electricity produced is cyclical with short term oscillations between peaks and off peaks. From the perspective of both supply and demand there is a need for the storage of energy, and ammonia may be used for this purpose.
Ammonia can be also used as a fuel for certain applications, thus being able to compete with hydrogen. It has certain advantages to hydrogen as a fuel for maritime transportation. The International Maritime Organisation has set rigid targets to reduce the carbon footprint of shipping, which accounts for 2% of global emissions, by at least 50% by 2050 compared to 2008. These targets can be only achieved if, along with low-carbon fuels (such as LNG or methanol) some zero carbon fuel is used. At the present time, hydrogen and ammonia, although containing less energy per tonne, and requiring much more space in bunker tanks than conventional maritime fuel, potentially can be used for this purpose. If 20-25% of maritime fuel was replaced by ammonia right now (not even considering any future growth in traffic), it would require more green ammonia than the existing capacity of grey ammonia.
There are several interesting initiatives for green and blue ammonia production for energy purposes. NEOM is an economic zone located in northwest Saudi Arabia. A $5 billion project with a capacity of 1.2 million t/a of green ammonia is scheduled for 2025. Air Products, a partner in the project, will take the green ammonia from the NEOM site and intend to transport it around the world to be converted back into hydrogen at local hydrogen refuelling stations.
Copenhagen Infrastructure Partners (CIP) have announced a project in Esbjerg, Denmark, to convert power from offshore wind turbines into green ammonia. Capacity is estimated at over 800,000 t/a of green ammonia. BP Australia is planning to start with a pilot project in Geraldton, West Australia, with a capacity of 20,000 t/a and a possible expansion of up to 1 million t/a. A number of other green ammonia projects are planned in Europe and Australia.
Wabash Valley resources will be the largest blue ammonia project globally and will have a capacity of 550,000 t/a and is planned to open in 2022 in the USA. Additionally, there are also a number of potential blue ammonia projects planned for Europe (Horizon Energi), Australia and Canada.
Forecast
Although we do not have sufficient data at present, and there is a large degree of uncertainty, we forecast that carbon-free ammonia production may rise from virtually zero in 2020 to 5 million t/a by 2030, and to 20-30 million t/a by 2035 (Figure 2). If the costs of green ammonia become competitive by the middle of the 2030s, then it is probable that a more rapid expansion of green ammonia will take place, with green replacing grey ammonia after 2035.
The use of ammonia as a fuel or as a hydrogen carrier for power may create a very large industry in the future, with production volumes much exceeding the existing ammonia industry.