Nitrogen+Syngas 372 Jul-Aug 2021
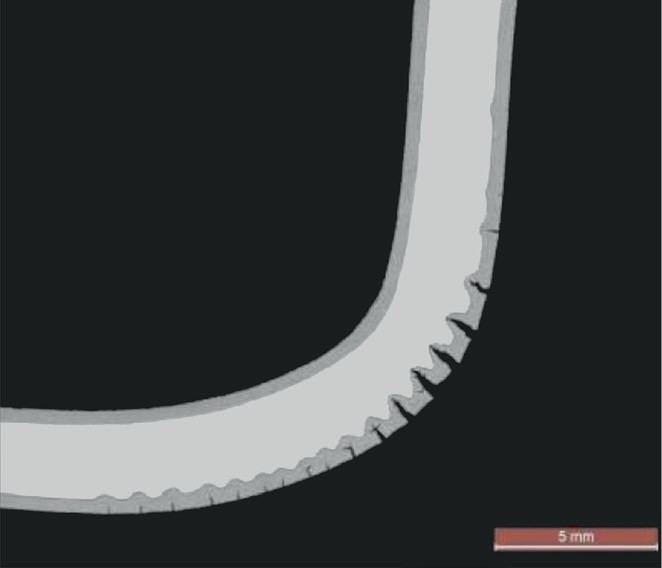
31 July 2021
Nitriding in ammonia converters: behaviour, experience, and solution
CORROSION IN AMMONIA PLANTS
Nitriding in ammonia converters: behaviour, experience, and solution
The internals of ammonia synthesis converters are generally made of austenitic stainless steel to withstand the harsh operating conditions (high temperature, high pressure and synthesis gas containing hydrogen and ammonia). Since nitriding is the most critical material degradation for the converter internals, Casale has set up a large nitriding analysis campaign. In the last decade, samples of materials operated under different pressures and temperatures and for different time spans have been tested and analysed. The data obtained has been used to increase nitriding knowledge and to establish a correlation to predict nitriding rate to allow the most suitable material and relevant thickness to be selected. L. Redaelli and G. Deodato of Casale report on how this correlation was established and provide valuable insight on this phenomenon and how to predict and control it.
One of the key items in an ammonia plant is the synthesis converter. Besides the efficiency of its performance, reliability is essential, as a plant cannot run if the converter is down and the risk involved in its failure is significant because of the high pressure, flammable gas it contains. In addition, the ammonia synthesis converter is the reactor with the longest run between catalyst changes, usually more than ten years, but sometimes up to 25 and more. Ammonia catalyst, once reduced, is highly pyrophoric and should not be allowed to come into contact with oxygen. Therefore, any maintenance activity is only possible when the catalyst is replaced and converters should operate between catalyst changes without repairs or internal inspections.
To achieve this, several aspects need to be considered since converters are subject to different metallurgical deterioration phenomena, and they have a complicated mechanical design with multiple catalyst beds and internal heat exchangers to improve efficiency.
Ammonia converter environment
The ammonia converter operating environment is characterised by an aggressive combination of high pressure and high temperature gas composed of hydrogen, nitrogen and ammonia, which implies the concurrence of hydrogen related damage and nitriding.
To reduce these problems the catalytic bed where the ammonia is generated at high temperature is usually separated from the pressure bearing shell. In most designs and in all multi-bed solutions the catalytic beds are enclosed in a protective shell inside the pressure retaining vessel, which separates the pressure bearing function from the high temperature environment. Cold flushing of the external vessel is provided by the inlet gas, which is low in temperature and ammonia content. This arrangement is called a cold wall design, while in the absence of a cartridge the converter arrangement is defined as a hot wall design.
The latter design avoids the cartridge by inserting the catalytic bed directly in the pressure vessel with the aim of reducing capital cost. It was used in the past and is sometimes still used when an additional single bed converter has to be added downstream of the main converter, but several of these vessels have faced problems during their operating life.
A brief introduction to the metallurgical phenomena that affect the ammonia converter is required to understand the different choices in the design of ammonia converters, the problems related to these choices and the solution proposed.
As already mentioned, the combination of a high content of hydrogen and ammonia implies the concurrence of hydrogen-related damage and nitriding, exacerbated by high temperature and high pressure.
Hydrogen related damage refers mainly to high temperature hydrogen attack (HTHA) and hydrogen debonding.
High temperature hydrogen attack occurs in hydrogen-rich environments where, under certain conditions of temperature and pressure, carbon and low alloy steels can suffer irreversible damage. Its mechanism is described in International recognised standards such as API 941 and it is dealt with in ammonia converter pressure vessels by using the cold wall design and by proper material selection. In this design the converter cartridge and all of its internals are made of austenitic materials that are not affected by HTHA.
Hydrogen debonding affects welding between dissimilar metals, including weld overlays of stainless steels and nickel alloys on ferritic steels. Cracking commonly occurs at the interface between the austenitic weld material and the heterogeneous base metal, due to hydrogen, which has penetrated the metal during fabrication or operation, remaining entrapped up to saturation levels at cooling down cycles. The faster the rate of cooling, the higher the likelihood of entrapped hydrogen causing debonding. In general, stressed heterogenous welds should be avoided, especially when involving thick sections.
Nitriding
Nitriding is the introduction of atomic nitrogen in the surface of a metallic component. Atomic nitrogen forms solid solution and several nitrides with iron, but also nitrides with other elements with an affinity for nitrogen such as chromium. Since atomic nitrogen is required, molecular nitrogen is not a nitriding agent unless it is ionised, but gaseous ammonia mixtures with hydrogen are. Above a certain temperature ammonia decomposes over steel according to the reaction where [N] represents the nitrogen dissolved in the steel.
NH3 → [N] + 3 /2 H2
This reaction occurs on the surface of the steel. Depending on the type of steel, temperature, pressure and gas composition, different types of solid solution and nitrides can form on the surface, creating an external nitride layer. This layer can increase in thickness over time and typically comprises a compound layer and an underlying diffusion zone. The compound layer is richer in nitrogen and harder, while the diffusion zone is softer with fewer nitrides, but overall the nitride layer is much harder than the base metal. This characteristic has been widely used to increase resistance against wear and fatigue of components such as engine cylinders.
While controlled nitriding is a technological process used to improve specific features of steel components, uncontrolled nitriding can be a problem due to its intrinsic characteristics. The nitride layer is hard but also brittle and involves structural modifications that causes volumetric changes.
The penetration rate of this layer will slow down after an initial fast growth since the layer itself acts as a barrier to further diffusion.
This layer does not cause any problem until it remains compact and does not crack.
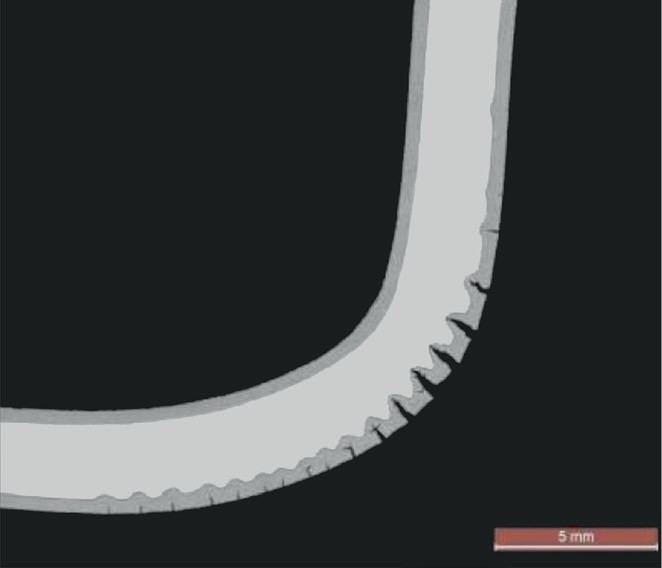
The main characteristic of a hard and brittle material compared to a ductile one is that there is little or no plastic deformation before rupture.
For this reason, in case of stress concentration, there is no plasticisation and consequently stress cannot redistribute over a larger area and can easily reach high local peaks. Therefore, a brittle material will more easily reach its rupture limit in areas of stress concentration. When the rupture stress is exceeded, a brittle material will crack.
In a nitriding environment, when cracks appear, further surface is exposed leading to further penetration of the nitride layer (Fig. 1). The apex of the cracks is subject to high stress concentration, even ten times higher than nominal stress. When nitriding progresses, these high stresses cannot be accommodated by plasticisation of the material and the rupture limit is again exceeded leading to further propagation of the crack. This propagation, cycle after cycle, can lead to the component failure.
Experience shows that components designed to avoid any stress concentration, preventing any abrupt geometrical change, sharp corners, temperature induced peak stress and sharp transitions can withstand moderate nitriding because the brittle layer remains compact.
It should be noted that, since nitriding generally involves a volume increase in steel it also generates internal stresses that could lead to cracks even in the absence of external loads.
In ammonia converters nitriding will occur to a degree depending on the combination of pressure, temperature, ammonia content and steel composition.
Nitriding develops on carbon steel, low alloy steels and on stainless steels, however, on the latter at a much reduced rate and at higher temperatures.
According to the literature and Casale experience, nitriding of carbon steel and low alloys starts at temperatures above 370-380°C and becomes significant above 400°C. As a consequence, carbon steel and low alloys are not recommended in ammonia atmospheres above 370-380°C, instead austenitic stainless steel or even nickel alloy should be used.
This limitation is the main reason, together with hydrogen attack, for the selection of the cold wall design of the ammonia converter, where the pressure retaining vessel is cold flushed by the inlet gas, poor in ammonia, and an internal stainless steel cartridge encloses the hot part of the process.
At higher temperature and reduced rates, nitriding also affects austenitic stainless steels, converting the comparatively ductile, moderate strength austenitic matrix to a very hard and brittle magnetic microstructure. It is the most critical material degradation phenomenon for the internals of ammonia converters, affecting the design and limiting the useful life of many components. However, due to the limited industrial application of nitriding on stainless steel and the differences between the controlled nitriding of the industrial process and the long term effects of uncontrolled nitriding in the ammonia synthesis environment, data about the effects of nitriding inside ammonia converters are scarce and difficult to correlate with actual operating conditions. No detailed data are available in the literature and it is not easy to simulate the effects of high temperature and pressure over an exposure time of 10 to 20 years in a laboratory.
Casale approach
Casale, as a leader in ammonia plant design and specifically ammonia converter design for one hundred years, has gained a wide experience in the effects of nitriding on the design of converter internals. In the continuous effort to develop ever more efficient and reliable technologies, Casale implemented a specific program to review the knowledge of nitriding in the ammonia synthesis environment for the purpose of optimising the design of critical components. Samples of materials which operated under different pressures and temperatures and for different time spans from ammonia converter components replaced in revamps, were analysed in laboratories, and mechanically tested over the last decade.
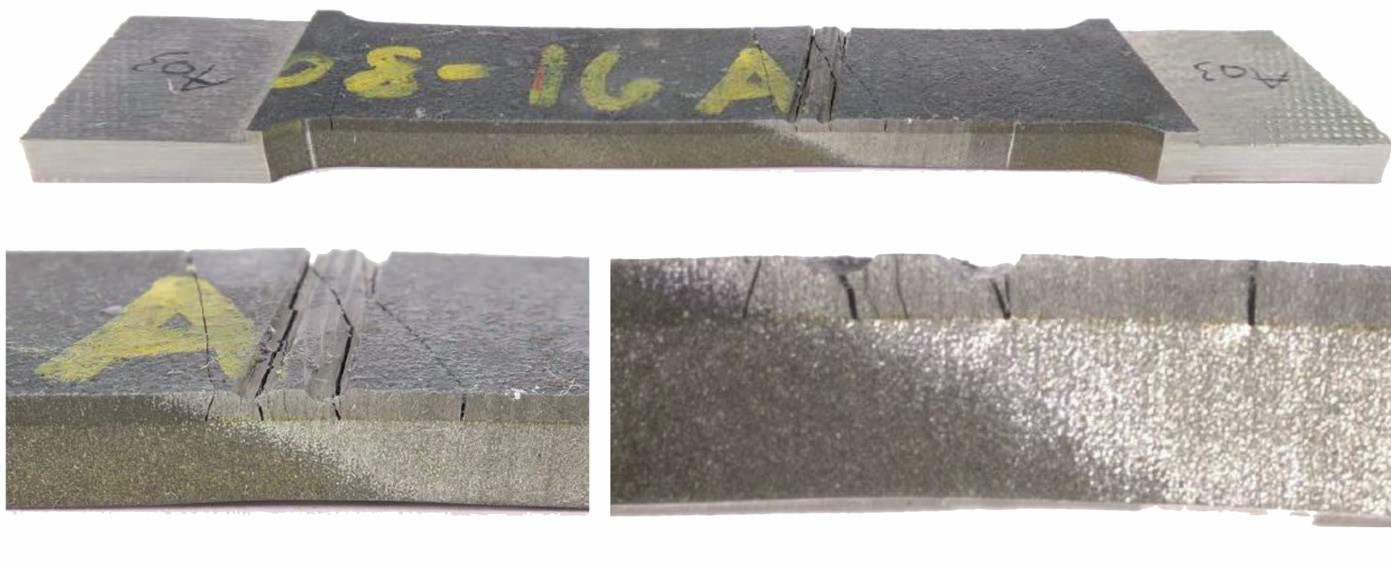
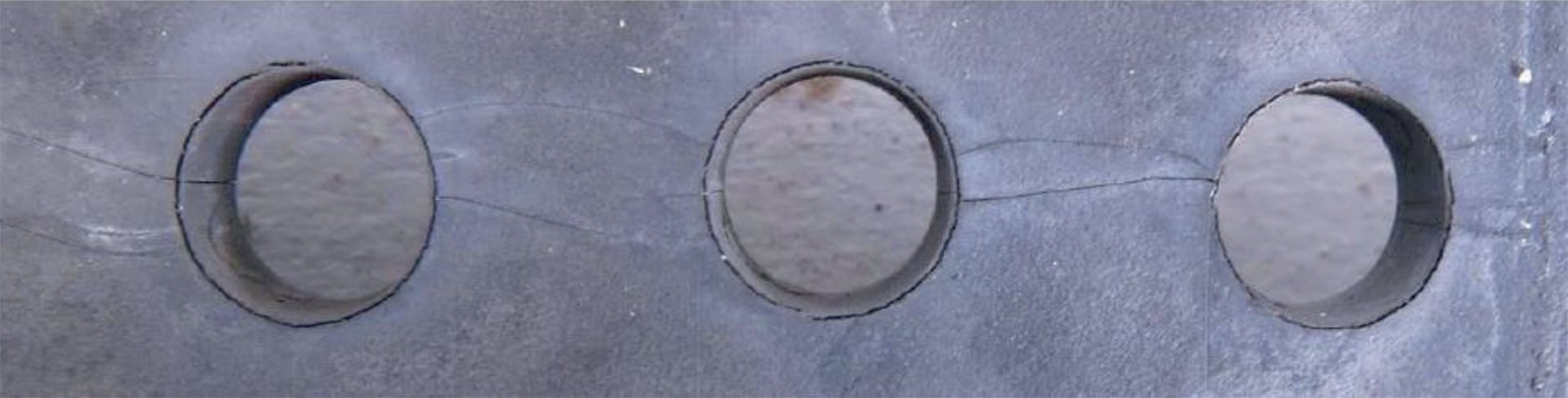
This knowledge supplemented by laboratory testing has provided valuable insight into this phenomenon and how to predict and control it in newly designed components as well as how to assess existing components in order to advise plant owners about the safety of their plant.
As a leader in converter revamping, Casale has modified all types of existing ammonia converters and therefore during this survey samples from different operating conditions and design were collected.
Some numbers from the survey are helpful in understanding the extent of this effort.
Of all samples collected about one hundred were examined in specialised laboratories, for visual analysis, nitriding thickness measurement and chemical composition. The oldest sample was about 45 years old, while the youngest was about four years old. The thickness of samples varied from 2 mm to more than 20 mm. The maximum nitride thickness measured was about 1.6 mm, as expected in the oldest sample. Since the tendency to crack increases with nitride layer thickness, measurements were taken in unaffected areas.
Several of these samples were also mechanically tested to verify the behaviour of the material under traction loads (Fig. 2).
In addition, samples of different chemical composition were submitted to a controlled nitriding atmosphere for comparison with real life results.
Fig. 3 shows the effect of nitriding in a 20-year-old perforated plate.
Some of the results of this survey are summarised here. It is understood that these considerations are valid only for operating conditions within the range of the tested samples, since based on an empirical analysis, but for practical purposes, the operating range represented covers the conditions found in practically all ammonia converters still in operation.
For reference, the samples analysed cover a timespan from four years to 45 years, and a temperature range from 400°C to 540°C. The ammonia content varied from about 2-3% to 21%, and the absolute pressure was also considered.
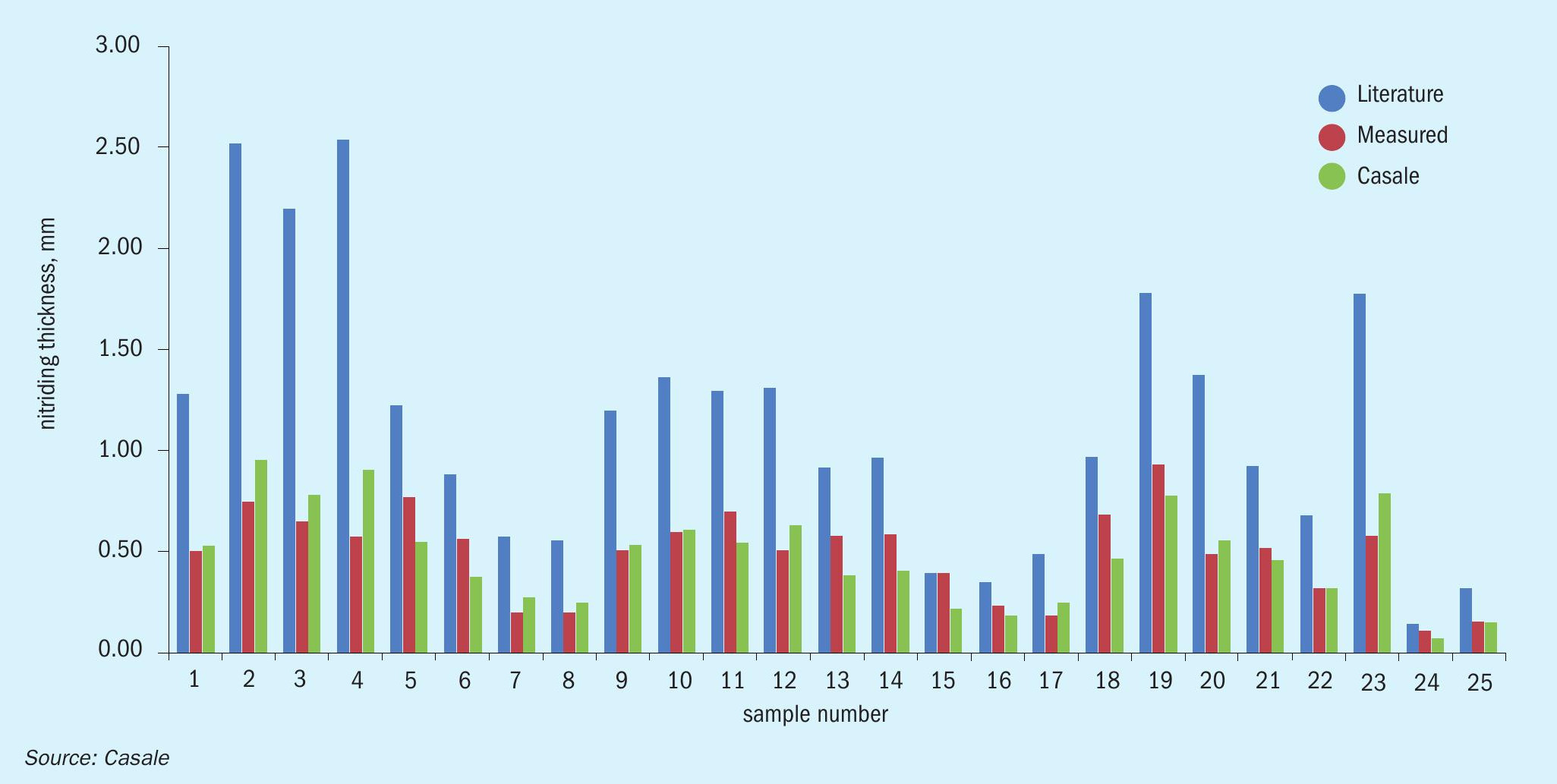
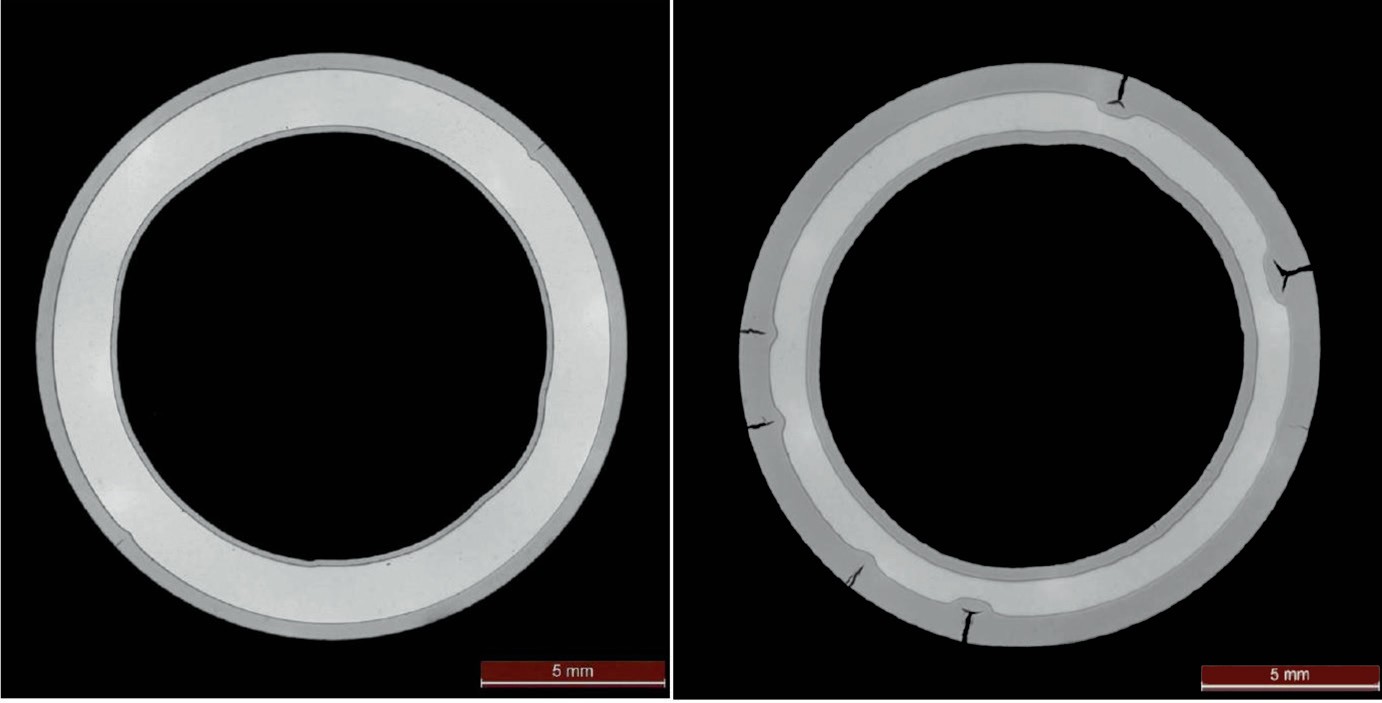
Results
In general, it was found that, for any set of operating conditions, the nitriding rate (increase of nitride layer thickness versus time) is initially high, then progressively decreases but does not stop in the timeframe considered. As an indication, the nitriding thickness reached after eight years will take three times as long to double.
Regarding the operating conditions, the survey shows that the rate of nitriding depends markedly on operating temperature, increasing exponentially with temperature in the field considered.
It depends less markedly on ammonia, increasing with content. The increase is less than linear, and nitriding become significant above about 5% with a thickness which will not double even at concentrations as high as 20%. Of course, the higher the absolute pressure the higher the relevant thickness, since the effective parameter is the ammonia partial pressure, which is the product of ammonia concentration and absolute pressure.
The data obtained has been used to establish a correlation which allows the extent of nitriding over time to be predicted, thereby allowing the most suitable design and relevant material thickness to be selected. This correlation improves previous rationalisations that can be found in the literature, thanks to the huge quantity of specific data that covers the complete operating range of the ammonia converter (see Fig. 4).
It is known that the nitriding rate decreases with increasing nickel content, but it was not possible to address this effect in the correlation by retrieved data only, because all of the samples collected were mainly made of stainless steel grade 304, 316 and 321, which have limited variation of nickel content, or Inconel, which is virtually immune to nitriding.
For this reason, laboratory tests of accelerated nitriding were set up to compare different grades of stainless steel. While accelerated industrial nitriding environments cannot be easily compared to that in an actual ammonia converter, and therefore laboratory tests cannot be used to predict actual nitriding in operating conditions, the behaviour of different grades of stainless steel in tests can be evaluated versus those of grades that have a known behaviour in operating conditions.
From these tests it has been observed that doubling the percentage of nickel has a relevant impact on the nitriding rate and therefore selecting suitable stainless steel grades for critical components in the ammonia converter permits significant improvement in the design, increasing reliability and extending operating life.
Another important issue that has been substantiated by this survey, is the effect of the volumetric change due to nitriding. In stainless steel, the absorption of nitrogen involves an increase in volume in the compound layer that generates stresses due to the geometrical constraints of the unmodified core material. In smooth geometries, when the nitriding layer is small compared to the base material, this effect usually goes unnoticed, but when the thickness of the nitriding layer is high compared to the overall thickness, especially where there are abruptly changes of geometry, cracks will occur in the brittle nitrided layer (see Fig. 5). These cracks will expose the unaffected material, which will be subject to initial fast nitriding of the new material. This phenomenon will lead to a higher nitriding rate due the mechanism of crack progression described previously. For this reason, frequent temperature changes such as in start-up and shutdown, which increase the thermal stress and accelerate the progression of cracks, are much more critical than continuous service at high temperature where the nitriding rate is generally low for some years.
Beyond volume changes, mechanical stresses can also lead to cracking of the nitrided layer. To assess the effects of stresses on the nitrided samples, a series of tension tests were performed on operated samples. As expected, the nitrided layer, which is harder but brittle and therefore cannot accommodate excessive strain by plasticisation, will always fail first. This should be taken into account in ammonia converter design.
A final point to be noted is that the nitrided layer becomes magnetic and subject to oxidation. While the operating atmosphere of ammonia converter is reducing and therefore this phenomenon is not a problem, it should be considered when ammonia converter internals are subject to a long shutdown in an unprotected atmosphere.
Conclusion
The huge amount of data from collected samples and tests have allowed Casale to refine its understanding of the effects of nitriding in the ammonia converter, to establish a correlation which allows the extent of nitriding to be predicted over the years, and to incorporate all of this knowledge in the material selection and design of its converters, improving their reliability and operating life.
References