Sulphur 395 Jul-Aug 2021
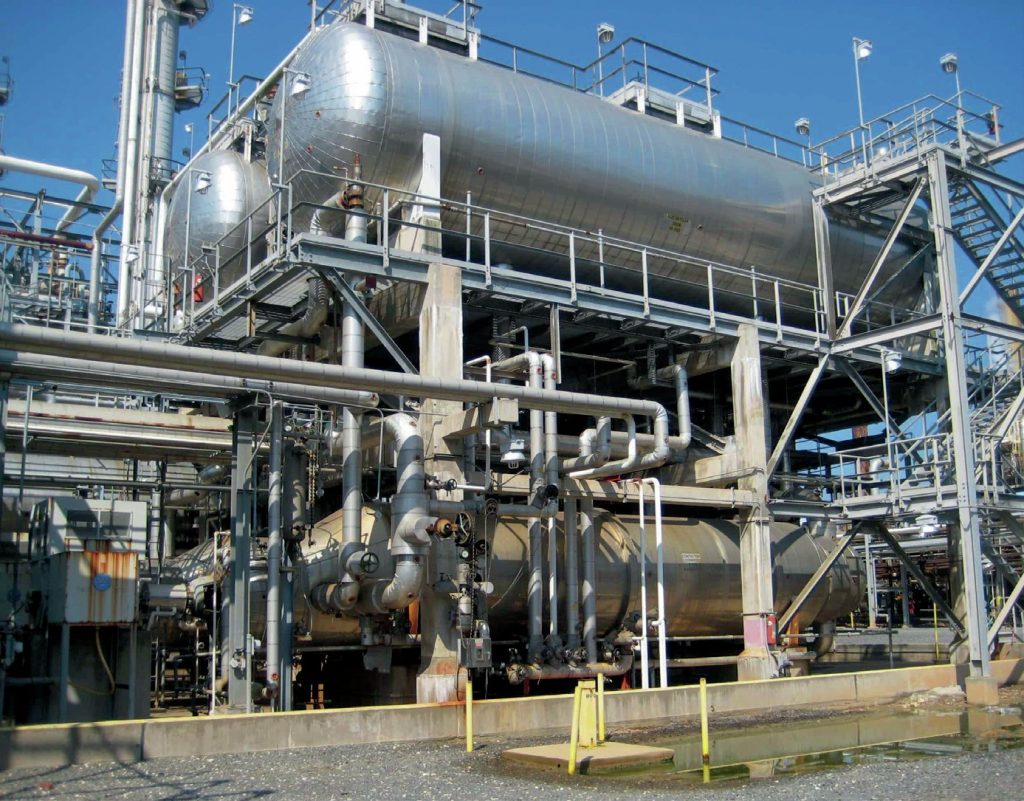
31 July 2021
Sulphuric acid alkylation
ALKYLATION
Sulphuric acid alkylation
The continuing spread of alkylation technology and the preference for the sulphuric acid route are leading to increased demand for acid in refineries.
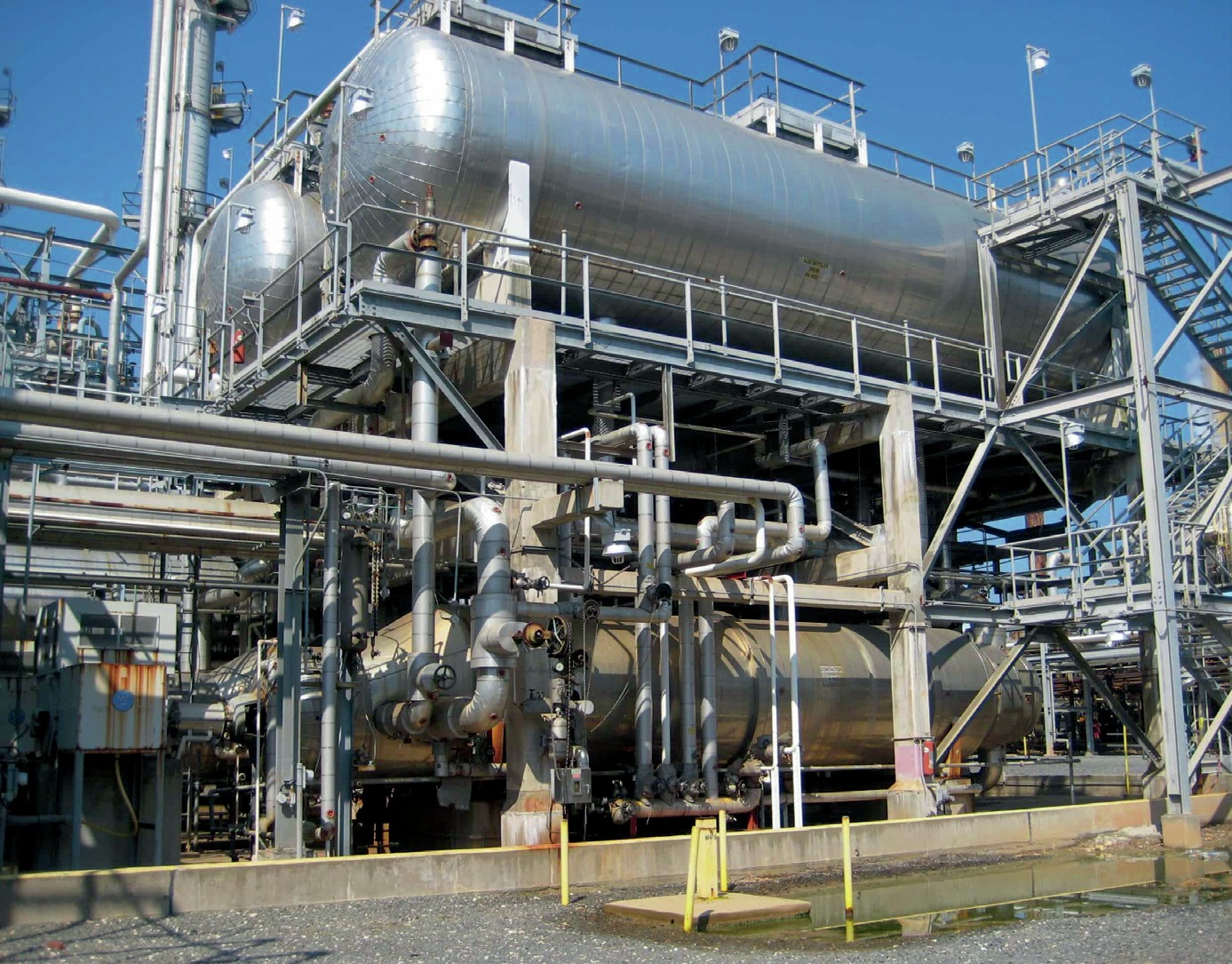
Alkylation is a refinery process which converts light olefins into a highquality gasoline blendstock by reacting them with isobutane. The most common is C4 alkylate, made by alkylating butylene with isobutane. However, alkylate can also be made from propylene and isobutane, or pentene and isobutane. It is particularly desirable because of its combination of properties; zero sulphur content, no aromatic content, low vapour pressure and high octane number, and is used as a blendstock in the manufacture of cleaner burning, premium quality gasoline. In the US, a creeping ban on the use of MTBE – the major alternative octane improver – and the increasing use of ethanol as a gasoline component have also led to increased demand for alkylate as a balancing component. It is reckoned that in California the proportion of alkylate used in gasoline rose from 17% (when MTBE was permitted) to 23% now that up to 10% ethanol is blended.
Although alkylation has traditionally mainly been a North American phenomenon, its use is spreading worldwide – our news this issue notes that DuPont has licensed its STRATCO alkylation process to two more Chinese refineries, making six plants in China now using that process.
Sulphur vs HF
Acid is used to catalyse the alkylation reaction, and the two main ones used are sulphuric and hydrofluoric (HF) acid. There are two main HF processes, licensed by UOP and ConocoPhillips, while sulphuric acid licensors include DuPont (the major licensor), ExxonMobil/Axens, CB&I (now Lummus), and a Kellogg process which is no longer offered commercially – KBR instead now has a solid acid alkylation technology called K-SAAT, with installations in both China and the US. Chevron and Honeywell have developed a non-acidic process using an ionic liquid called ISOALKY, though there is so far only one commercial reference. The China University of Petroleum has also developed an ionic process which is marketed by Wall as Ionikylation, and which has been used in several Chinese refineries.
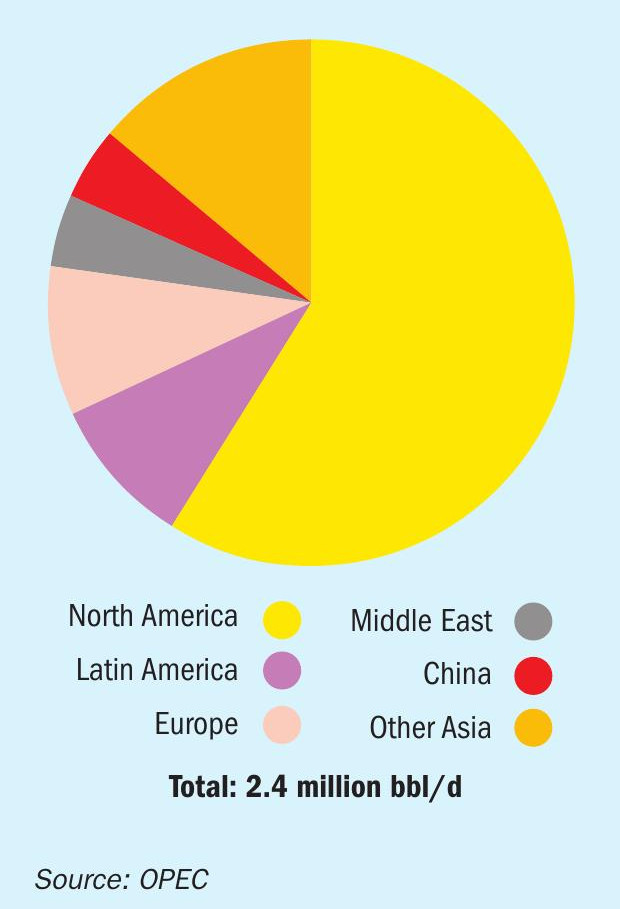
Installation and operating costs are similar for sulphuric and hydrofluoric acid alkylation. Sulphuric acid is cheaper than HF but is more complex to regenerate and has higher usage rates. In the early days of the processes sulphuric acid was preferred, but during the 1980s and 90s, HF gained predominance, and by the turn of the century there was roughly a 50-50 split between their installations. However, the number of new HF installations has fallen dramatically over the past 20 years, due to increasing safety concerns, and only about one third of US refineries now use HF. While both sulphuric and hydrofluoric acids are highly corrosive and can cause terrible burns on skin contact, the danger with HF is that it is more volatile, and can form an expanding toxic vapour cloud that travels along the ground and which can affect a much wider area, and which also has the potential for explosion, whereas sulphuric acid merely pools as a liquid. With the acids being used in close proximity to hydrocarbons such as LPG, there is a potential for explosions which can rupture acid tanks and release large volumes of acid. A series of HF accidents and near misses at US refineries, and culminating in an explosion and fire at the Philadelphia Energy Solutions (PES) refinery in Philadelphia in 2019, have led the US Chemical Safety Board (CSB) to call upon the Environmental Protection Agency (EPA) to review its regulation of HF in alkylation and other applications and look for substitutes. So far, however, an EPA response to the CSB request has not been forthcoming. Meanwhile, the CSB’s final report on PES is still pending approval. Operators argue that the use of modifiers in HF can reduce the formation of vapour clouds and water spray systems can be used to contain any release. Nevertheless, there have been several conversions from HF to sulphuric acid or other systems. DuPont markets its ConvEx technology for converting HF alkylation plants to sulphuric acid which can also be used to expand unit capacity at the same time.
In China, which has had a number of the alkylation installations outside of the US, there are only two HF alkylation plants operating, and considerable scrutiny of the process by the Environmental Protection Ministry.
Another factor favouring sulphur is that as refineries have been pushed towards increased sulphur removal from crude feeds, so the volumes of elemental sulphur available at refineries have increased, making for a ready potential feedstock for on-site sulphuric acid production, and helping to control the cost and any logistical difficulties of importing acid.
Spent acid regeneration
With the cost of merchant acid increasing, and costs of safe disposal of spent acid likewise, the option to regenerate spent acid is becoming an increasingly attractive one, with a number of companies now providing acid regeneration services, either on a merchant basis or via a captive acid regeneration unit. Where refiners have taken the option of on-site acid generation, it can be relatively straightforward to build acid regeneration capacity into the existing sulphuric acid plant.
Capacity
Total US alkylate capacity is just over 1.3 million bbl/d, according to the Energy Information Association, just over half of it in the PADD 3 region (US Gulf Coast). This has been a slow, steady rise from around 1.0 million bbl/d in 1990. Over the same period, alkylation capacity outside the US has risen to around 1.1 million bbl/d, according to OPEC figures (see Figure 1), with installations at, e.g. Reliance’s refinery in Jamnagar where an 83,000 bbl/d unit – one of the largest in the world – now operates. Chinese capacity now represents about 100,000 bbl/d of this, with a number of alkylation sections added to refineries over the past decade to help meet China-VI (<10ppm sulphur content) gasoline standards.
Additional alkylation capacity out to 2025 is projected to add another 200,000 bbl/d of capacity, with OPEC projecting a further 600,000 bbl/d of capacity being added in the decade from 20252035, by which time global alkylation capacity will reach 3.2 million bbl/d. This represents a modest but still noteworthy average annual growth rate of about 1.8-2.0% over the period.
Sulphuric acid demand
While HF functions almost as a ‘pure’ catalyst, for the sulphuric acid alkylation route there is a fractional conversion of acid, and hence ‘consumption’ is relatively high; around 10-12 kg of acid per barrel of alkylate produced at best, and potentially as high as 15-25 kg/bbl alkylate if the cracker is being run at high severity. Not all of this is pure consumption; acid concentrations must be kept high (>90%) in order to prevent acid ‘runaway’, where catalytic activity rapidly declines and polymerisation is enhanced, and so the acid must be continually topped up with fresh acid and spent acid removed from the system. But this effective consumption of acid means that the total market for sulphuric acid as an alkylate catalyst is thus around 10 million metric tonnes per year; only a small fraction of the global market for sulphuric acid (less than 4%), but still an important end-use.