Sulphur 395 Jul-Aug 2021
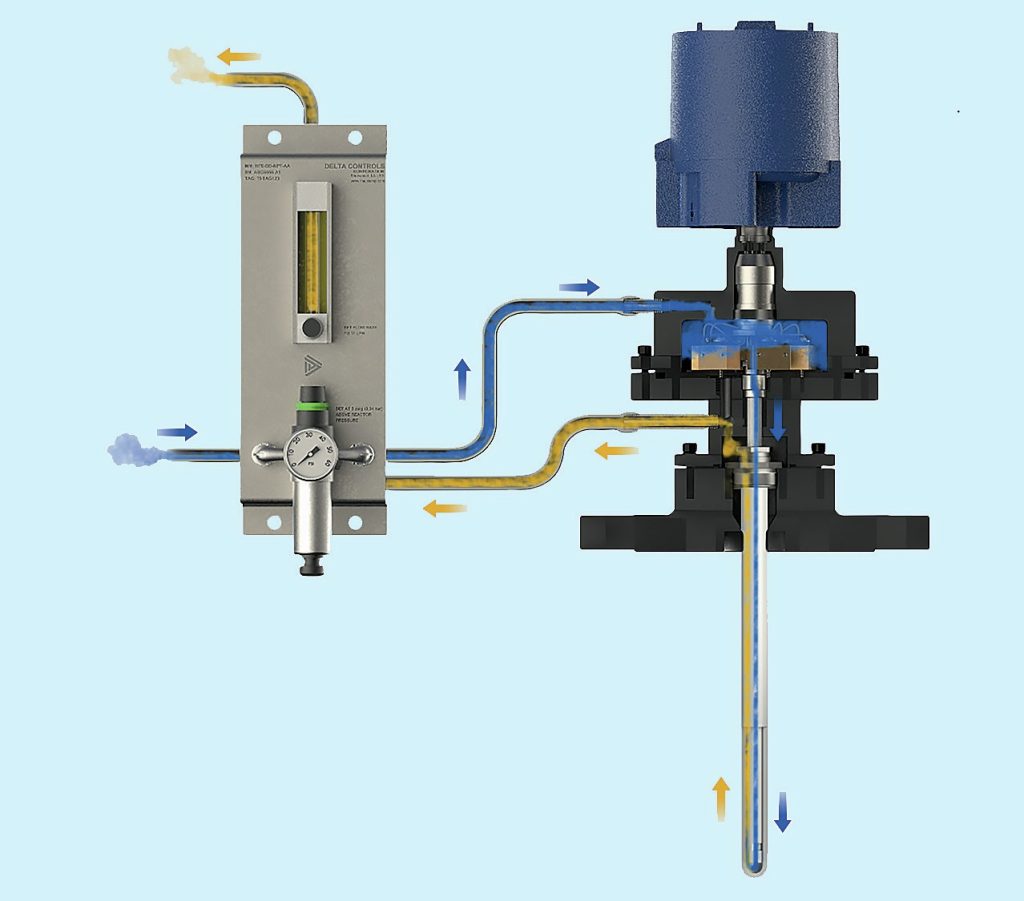
31 July 2021
Temperature measurement in sulphur recovery
CLAUS THERMAL REACTOR
Temperature measurement in sulphur recovery
Temperature monitoring and measurement of the Claus thermal reactor in sulphur recovery units is one of the most challenging applications in the oil and gas industry. Recently, market interest in unpurged thermocouples has increased with the introduction of new unpurged thermocouple designs utilising alternative thermowell materials such as monocrystalline sapphire.
DELTA CONTROLS CORPORATION
Purged vs unpurged thermocouples in Claus thermal reactors
Temperature measurement in the main reactor of the sulphur recovery unit (SRU) is not only a primary process variable, but also critical for the overall safety and reliability of the reactor. Recently, many legacy reactors with limited to no temperature instrumentation may be required to handle more throughput than originally designed. In addition, many reactors are adding supplemental oxygen resulting in increased operating temperatures. With higher reactor operating temperatures, the importance of temperature monitoring is greatly increased. As standard process temperatures rise through the use of oxygen enrichment and reach maximum capabilities of the refractory, it is and will be increasingly important to have accurate and reliable temperature indication.
SRU temperature measurement technologies
There are currently two technologies suitable for reliable temperature monitoring in the main reactor: infrared pyrometers and thermocouples. It is recommended to use both technologies for maximised reliability.
Pyrometers designed for sulphur recovery are specifically engineered for the optical characteristics of the reactor and high temperature environment. Thermocouples suitable for sulphur recovery are designed utilising special materials and protection mechanisms to provide accuracy and reliability at the extreme process temperatures. These thermocouples utilise a series of alumina ceramic thermowells and noble metal type thermocouple elements. Thermocouples in sulphur recovery utilise purged or unpurged technology with purged designs offering the highest reliability track record. Recent research and development efforts by Delta Controls Corporation have resulted in a highly reliable unpurged alternative.
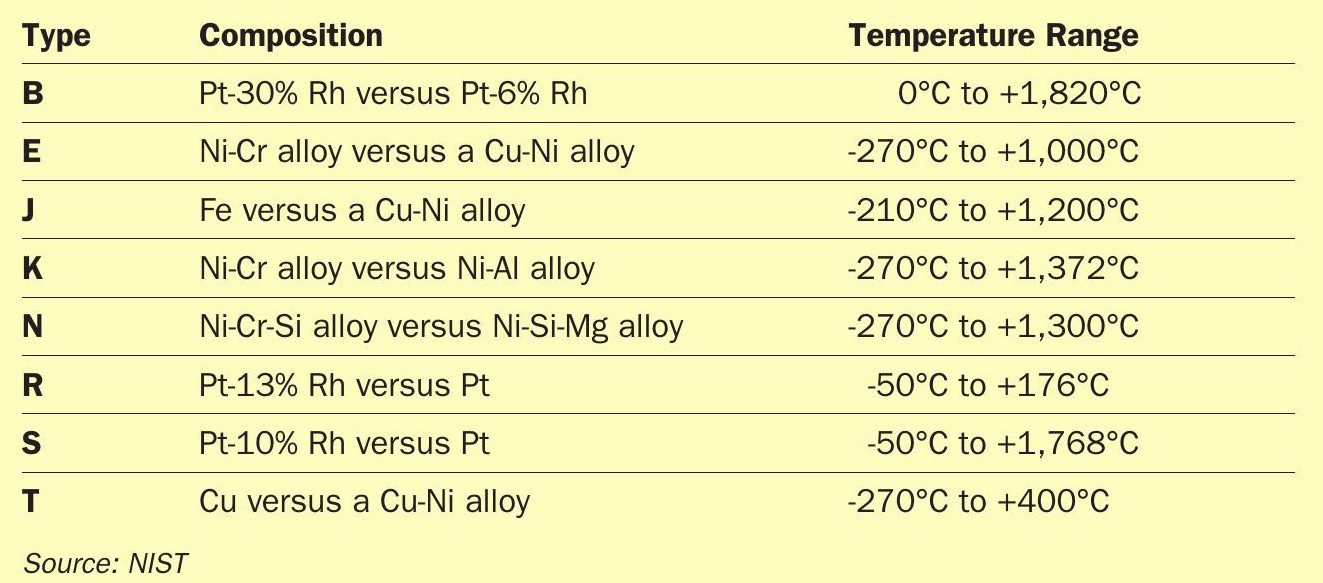
SRU thermocouple challenges
Thermocouples, both purged and unpurged, are presented with numerous individual challenges in the sulphur recovery environment, and when presented together compound to create significant reliability challenges. Proven thermocouple designs utilise a series of alumina ceramic thermowells and noble metal thermocouple elements.
The high temperatures permit only a few thermocouple types to fall in the readable range (see Table. 1). Also many metals commonly used on thermocouple sheaths, or thermowells, are not suitable due to melting temperatures below +3,000°F (+1,649°C). In addition to high temperatures, the process is highly corrosive with process gases hydrogen sulphide, sulphur dioxide, and other sulphur species present. Noble metal thermocouple types such as B, R, and S may be subjected to a multitude of detrimental effects, including hydrogen embrittlement, platinum oxide sublimation (see Fig. 1), and other degradation reactions. These reactions lead to signal degradation or, ultimately, failure.
An alumina thermowell does not provide complete protection from the process gases. The porosity of the aluminium oxide at operating temperatures allows small amounts of process gases to diffuse through the thermowell, particularly at operating temperatures. If these gases are allowed to accumulate inside the thermowell, they will corrode, contaminate, or otherwise degrade the thermocouple within a few weeks.
Purged thermocouple technology
The proven method of protecting thermocouple elements is to purge the thermowell with an inert gas, usually nitrogen, in order to sweep away any process gases that diffuse through the primary thermowell (see Fig. 2). The gas is piped to the upper chamber of the thermocouple where it then travels down the holes of the element support where the thermocouple wires are positioned. The gas envelops the sensing junction at the end of the support. Any diffused process gas is mixed with the nitrogen, then directed to the outlet. Due to the slow rate of process gas diffusion through the thermowell, a purge flow of approximately 11 L/h is sufficient to provide protection without significantly cooling the thermocouple.
Disadvantages of purged thermocouple technology
Purged thermocouple designs, when properly installed and maintained, are the proven solution for reliable temperature indication from turnaround to turnaround. However, purged thermocouples are not without compromise. Installing and maintaining the purge system will require additional costs and complexity that may be considered a disadvantage. The purge gas system also introduces additional potential failure modes for the thermocouple as the purge gas must remain free of contaminants such as moisture or hydrocarbons that may damage the thermocouple elements. The system requires periodic maintenance to verify correct pressure and flow settings as well as functionality.
Unpurged thermocouple technology
Plants may attempt to reduce operational and capital expenditure costs by installing unpurged thermocouples that are unsuitable for the challenges of the reactor environment. Most of these attempts result in a failed thermocouple after a relatively short time resulting in the main reactor losing critical temperature indication and introducing associated safety concerns.
Recently, market interest in unpurged thermocouples has increased with the introduction of additional unpurged thermocouple designs utilising alternative thermowell materials such as monocrystalline sapphire. Sapphire is grown from a single crystal, rather than slip cast or recrystallised like alumina resulting in a molecular monocrystalline crystal lattice structure that is uniform throughout the thermowell. Traditional high purity alumina ceramic has a higher molecular porosity that can allow process gases to diffuse through the ceramic at the high operating temperatures in the main reactor. Sapphire is compositionally identical to high purity alumina as both are composed of aluminium oxide, Al2 O3 . However, the monocrystalline structure of sapphire is not porous at high temperature and therefore the diffusion of process gases through its crystalline matrix is much slower than through alumina ceramic. While monocrystalline structures are absent of grain boundaries, it is unlikely that process gas diffusion is completely prevented.
The utilisation of a sapphire thermowell in an unpurged thermocouple design exclusively is not sufficient for long term reliability of the instrument. The seals that surround the thermowell are critical to the prevention of process gas diffusion into the assembly. Even the most effective seals will not have a zero leakage rate. While contaminants may be impeded by the sapphire thermowell, the seals surrounding the thermowell are subject to trace amounts of leakage. The trace contaminants can accumulate inside the thermocouple assembly eventually causing degradation of the thermocouple elements.
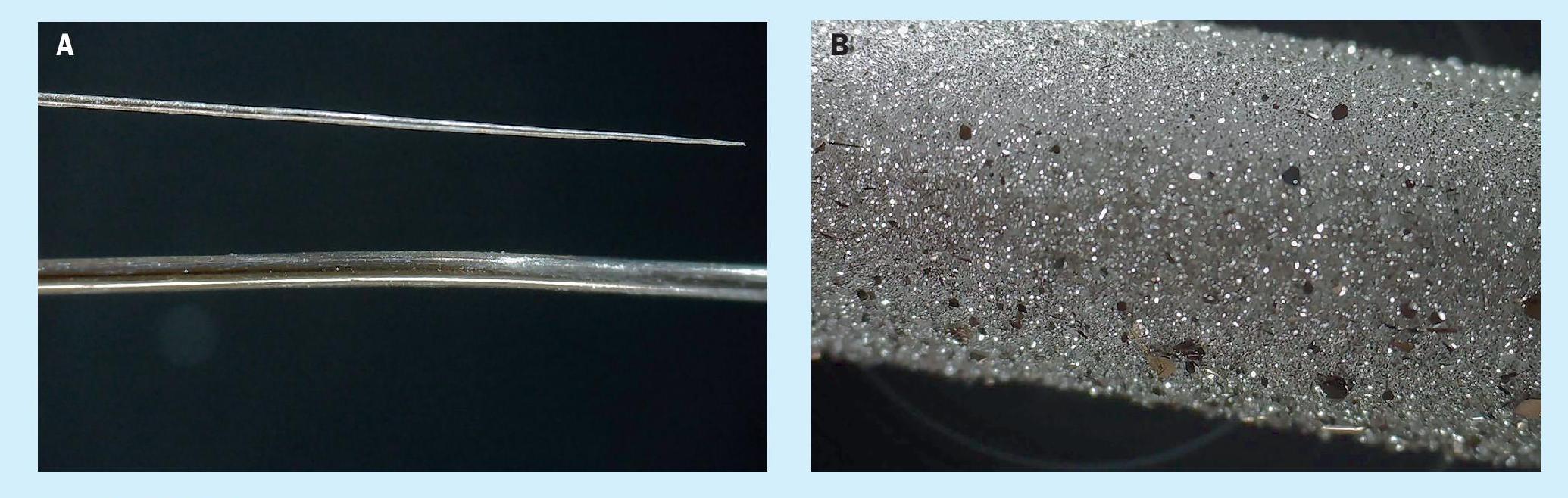
The Delta Controls Model HTV thermocouple (Fig. 3) reliably addresses the seal leakage problem by implementing a newly developed, patent-pending seal mechanism designated as QSeal™ . The design utilises a series of protection mechanisms to prevent process gas diffusion, gas accumulation, and seal leakage from compromising the temperature indication. The issues are first addressed with careful selection of advanced seal materials that minimise diffusion through the seal structure. Secondly, a high compression wedge seal design mechanically reduces contaminant bypass around the seal. Finally, and most importantly, the seal system design prevents any contaminants that bypass the primary seals from accumulating within the thermocouple assembly to concentrations higher than the ambient atmosphere. Secondary seals, which are exposed to a nearly ambient atmosphere, isolate the open end of the sapphire thermowell; therefore, contaminant leakage through secondary seals is negligible. Multiple redundant seals, in addition to the primary and secondary seals, ensure process containment is maintained in the event of thermowell breakage.
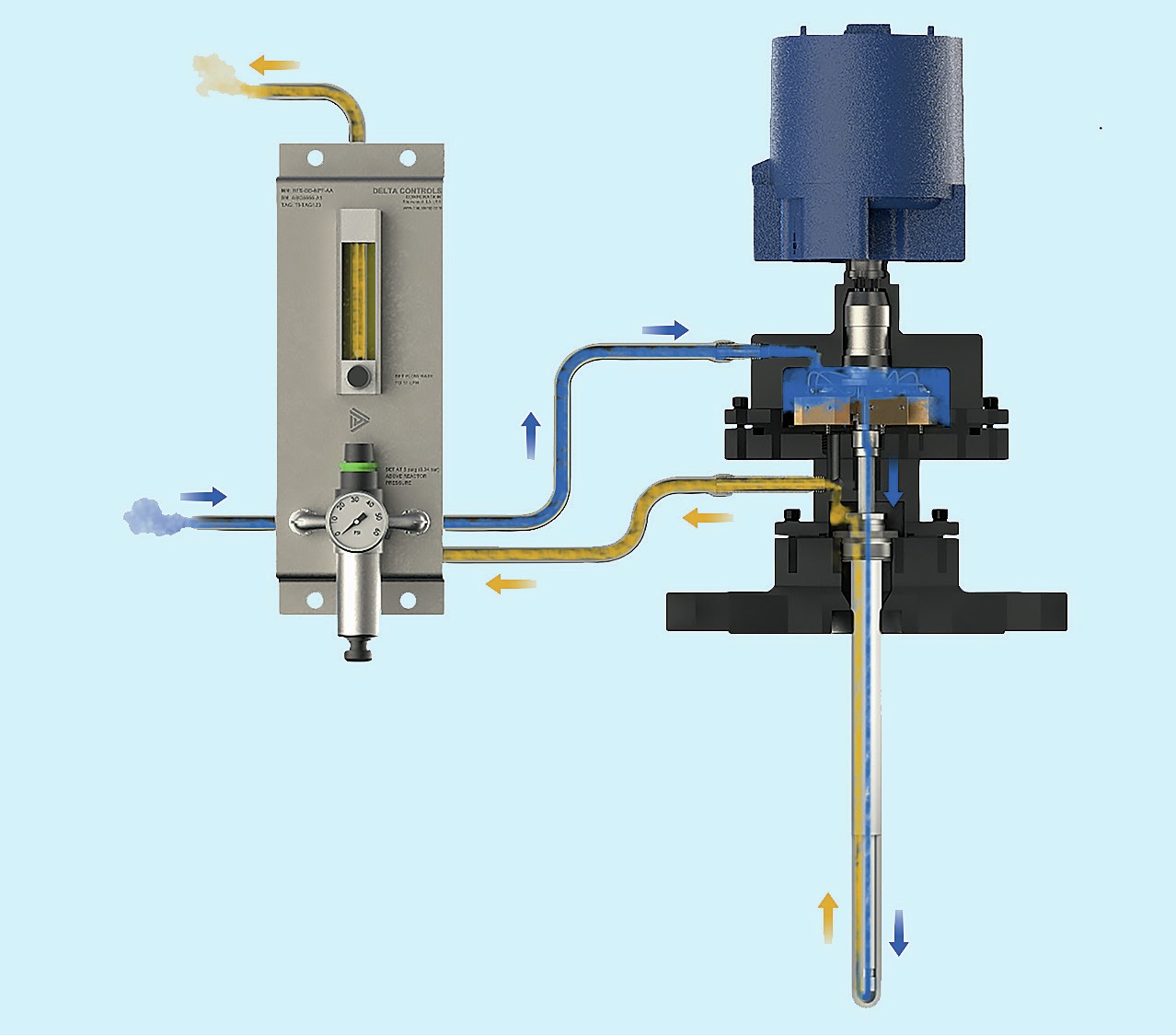
Disadvantages of unpurged thermocouple technology
While thermocouples utilising a sapphire thermowell have been in high temperature applications for many years, the designs have only recently been evaluated for use in sulphur recovery thermal reactors. Due to the recent implementation of this technology, it is unproven in terms of reliability and longevity in sulphur recovery service.
The absence of grain boundaries in monocrystalline sapphire can slow the diffusion of process gases through the thermowell, but it is unknown whether the diffusion rate is sufficiently minimised to prevent thermocouple deterioration for the targeted five to seven years between turnarounds. Another potential concern is the effect of the atmosphere contained within the thermocouple assembly will have on the longevity of the device. A number of deleterious reactions are known to occur with platinum at high temperatures. These reactions are not a problem in a purged thermocouple, where the purge gas is constantly replacing the atmosphere within the thermocouple assembly with inert nitrogen. How problematic contained atmosphere is remains to be seen.
Trials are underway, but an insufficient number of sapphire protected thermocouples have been installed long enough to clearly demonstrate turnaround to turnaround reliability. Until the technology has matured and demonstrated reliability, it is recommended that sapphire protected thermocouples only be installed in addition to other proven temperature measurement technologies such as purged thermocouples or pyrometers.
In conclusion, unpurged sapphire thermocouples show promise as an alternative to purged thermocouples; however, overcoming the associated application challenges in sulphur recovery service require more than changing the thermowell material. Careful attention must be paid to the seal materials, seal design, and overall architecture of the thermocouple assembly to assure safety, longevity, and reliability.
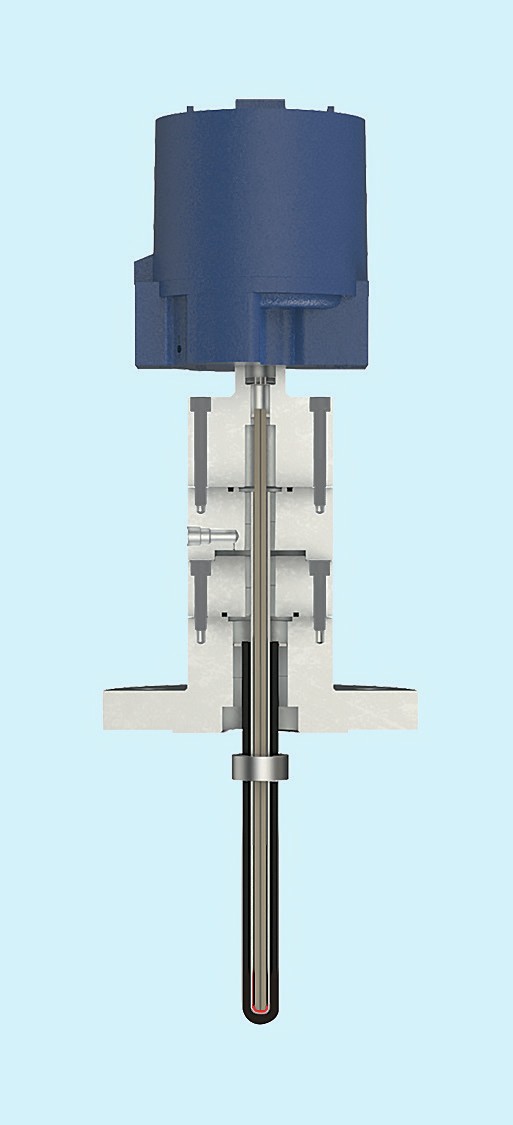
Unpurged sapphire thermocouples have only been used in SRUs for a relatively short time. It will be 5 to 10 years before enough field data has been collected to evaluate whether unpurged sapphire thermocouples are as reliable as purged thermocouples in SRUs.
The Claus thermal reactor is a challenging environment for the long term reliability of all temperature indicating devices. It is imperative that an accurate temperature measurement be continuously reliable for efficient and safe operation. Low reliability thermocouple design consequences include not only financial costs, but also potential loss of safety critical SIS indication while in operation and increased down time of the SRU. As proven in hundreds of worldwide installations for nearly 50 years, a properly designed and installed purged thermocouple reliably serves this purpose.
DAILY THERMETRICS
A complete temperature measurement system
Removal of sulphur from natural gas or crude oil is one of the most critical operations within a plant. Traditionally, this occurs within a thermal reactor that is a part of the sulphur recovery unit. The reaction occurring is called as Claus reaction, which removes the sulphur from process stream occurs at elevated temperatures and is exothermal, therefore excess heat is created throughout the process run.
Even though there are several reactors involved within the Claus process, one of the most important is the thermal reactor (also called the Claus reaction furnace or main combustion chamber) since the operating temperatures could be as high as 1,500-1,600°C (2,700-2,800°F). In this reactor, thermal energy is utilised to react hydrogen sulphide with oxygen to yield elemental Sulphur as well as water.
Since the reaction within the thermal reactor is most efficient at higher temperatures, temperature measurement control of this reactor is extremely critical to ensure safe operation, considering the highly toxic gas that is contained. An important point to consider here is the condition of refractory walls which could degrade over time at the elevated temperatures, which increases the criticality of temperature measurement for the maximized lifetime of the refractory and therefore the reaction furnace. If not properly monitored, refractory lining could potentially melt which was the case in modern history catastrophes. The normal limit for refractory lining is 1,650°C, however some refractories are rated much high temperatures of up to 1,800°C. Monitoring the refractory temperature is critical to prevent the vessel shell from overheating and containment of toxic gas.
Temperature measurement challenges
Traditionally, the monitoring of this crucial temperature in the furnace is done either with infrared pyrometers or special high temperature thermowells using a noble temperature sensor. High temperature thermowells are usually seen as unreliable as most of the technologies available in the industry were not successful in finding answers to common problems within the Claus thermal reactor. For this reason, most operators prefer using pyrometers, despite their high maintenance costs. In general, pyrometers are practical, however one should be careful with the readings as it could potentially be showing temperatures with a high error (up to 20%) due to sulphur build up or potential drift.
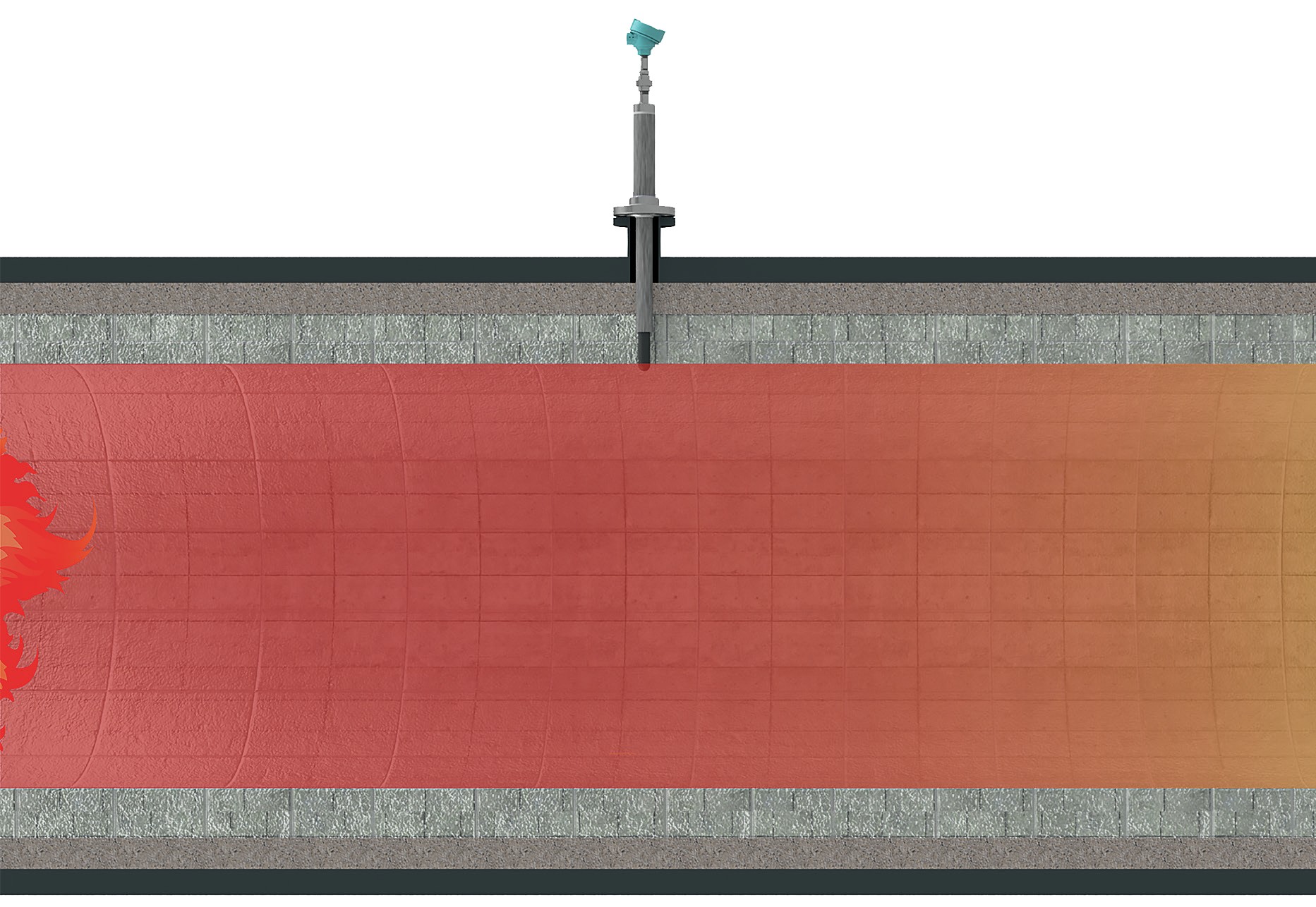
The current high temperature assemblies available in the market, or in other words the ceramic thermowells, are widely susceptible to hydrogen sulphide migration which corrupts the noble metal thermocouples within. The main reason for this is the porous outer ceramic material that is utilised, which allows toxic gas to pass through and potentially reach the noble thermocouple wires.
To prevent this from happening, a nitrogen purge system is added to remove this highly toxic gas, but this introduces a temperature difference, generates high operational costs and an extremely hazardous working condition due to the constant monitoring and control required to operate the unit safely.
Moreover, the outer ceramic that is utilised is not well suited for the Claus thermal reactor, which is prone to failure in the unlikely event of refractory shift or thermal shocks, not to mention the complex installation procedures that consume valuable time during turnarounds, as well as difficulties if the thermowell nozzle has a smaller flange or is located on the horizontal axis.
Proven temperature measurement technology
In the light of these drawbacks, the Daily Thermetrics team has worked tirelessly to come up with the latest iteration of their design which provides high reliability and is easy to operate, providing operators with peace of mind (Fig. 1).
The new design with its optimised sensor provides protection from the damaging effect of toxic gas without the added complication and costly requirement for nitrogen purging. The design is therefore maintenance-free.
While designing the assembly, the first area to look at was the outer protection tube, which is designed to be from sintered silicon carbide supported by a high temperature metal support tube to ensure the highest resistance to thermal shock and shifting refractory. This outer protection tube already has an excellent track record within high temperature applications. It is resistant to 1,950°C and proven to provide the ideal solution due to its excellent thermal conductivity.
Another area to consider was whether nitrogen purging is necessary, since there was the belief in the industry that purging is a must or the thermocouple wires could not survive in the toxic gas environment. However, taking a deeper look at the options available, it was obvious that an impermeable layer which would seal around the noble thermocouple wires could eliminate this need.
After a careful search, a monocrystalline sapphire tube was selected to provide the optimum solution which again is proven in extreme temperature applications. Due to its homogenous structure, in contrast to porous structure of ceramic protection tubes, its completely impermeable to any toxic gas penetration, therefore eliminating the need for the costly and high maintenance item of purging equipment.
The assembly offers a process rated containment system to ensure full plant safety at all times. The design itself has primary, secondary and tertiary process sealing that are rated greater than 1.5 times the pressure rating of the process connection. This triple seal system is tailored to mitigate any risk factors:
- first seal fitting for outer protection tube for stability throughout operation;
- second seal fitting for the sapphire tube to ensure process containment in case of potential failure;
- third seal fitting for the thermocouple;
- fourth seal fitting for the individual noble thermocouple wires.
The assembly itself is an integrated well which requires no specialty tools or instructions for installation and could be described as a plug and play system. An additional advantage of this assembly is the flexibility for all existing nozzles due to variable flange sizing down to 2 inches (5 cm) as well as an optional leak detection thermocouple that could be added within the containment chamber for the unlikely events (Fig. 2).
Daily Thermetrics has been providing high temperature assemblies for the some of the most arduous applications within the energy industry such as Claus furnaces, partial oxidation reactors, waste heat boilers, incinerators and many more for more than 40 years.
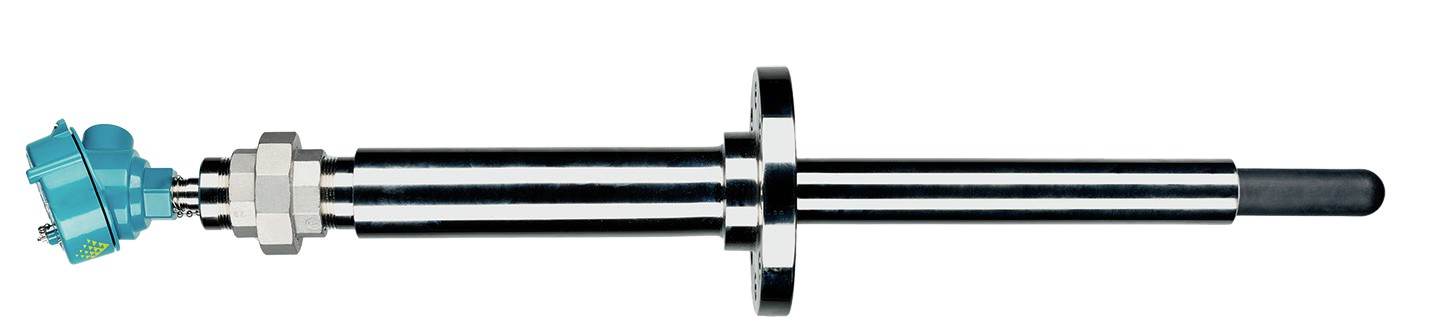
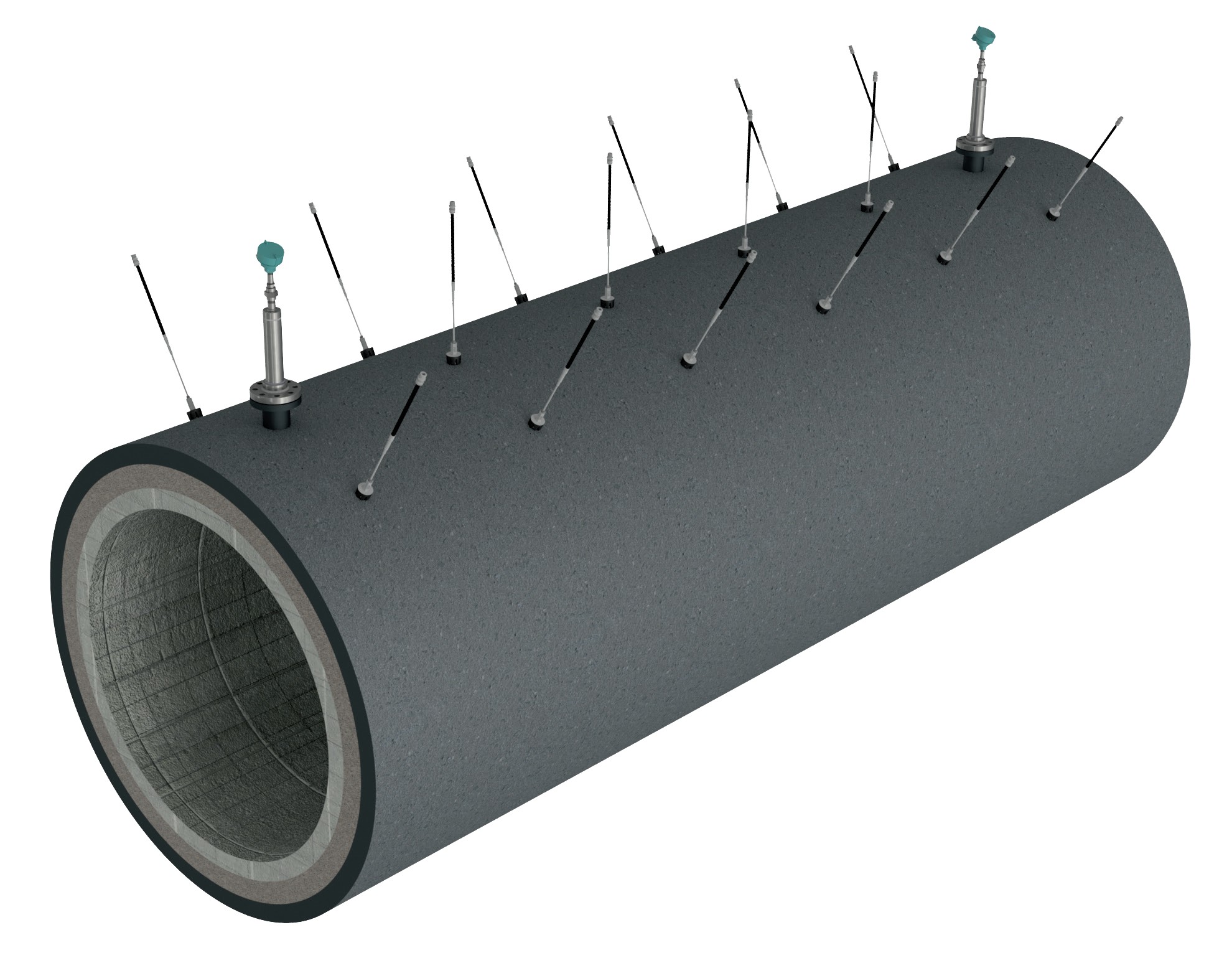
However, in the last couple of years, working intimately with process licensors, engineering contactors and end clients, Daily Thermetrics has developed a complete temperature measurement system for the Claus thermal reactor, which includes the patented Mag VSS™ magnetic skin sensor that is attached on the thermal reactor surface via the magnetic pull force with the Daily ImpermaWell™ (Fig. 3).
This skin sensor assembly has 150 pounds of pull force (68 kg) and is rated up to 540°C surface temperature. It is a general recommendation to install two of these skin sensors at every metre on the reaction furnace length for the monitoring of refractory shift or falling that could potentially happen during the operation. The main advantage is the easy attachment of the assembly as it does not require any welding and its position can be adjusted as desired.
Overall, the Daily ImpermaWell™ is an innovative solution utilising proven technologies and with references in a variety of applications. Combining top shelf materials and expertise from various applications, Daily ImpermaWell™ has already been proven in commercial applications and obtained approvals by clients. This maintenance-free design reduces the total cost of ownership, provided that no purging equipment is needed, and increases plant safe operation as process sealing is at the process connection and no toxic process gas is allowed to enter secondary equipment. Ultimately, it provides reliability and peace of mind.