Fertilizer International 503 Jul-Aug 2021
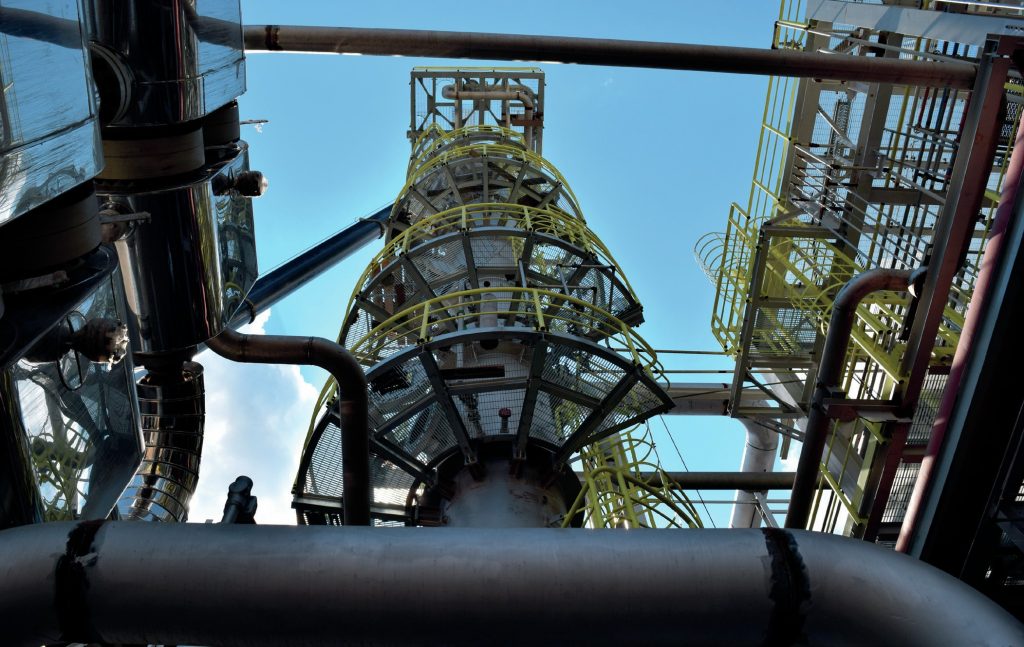
31 July 2021
World-scale nitrogen projects
NITROGEN PROJECT REPORT
World-scale nitrogen projects
We highlight the large-scale nitrogen projects that are currently under development across the globe – with a focus on ammonia and urea technology licensors and engineering contractors.
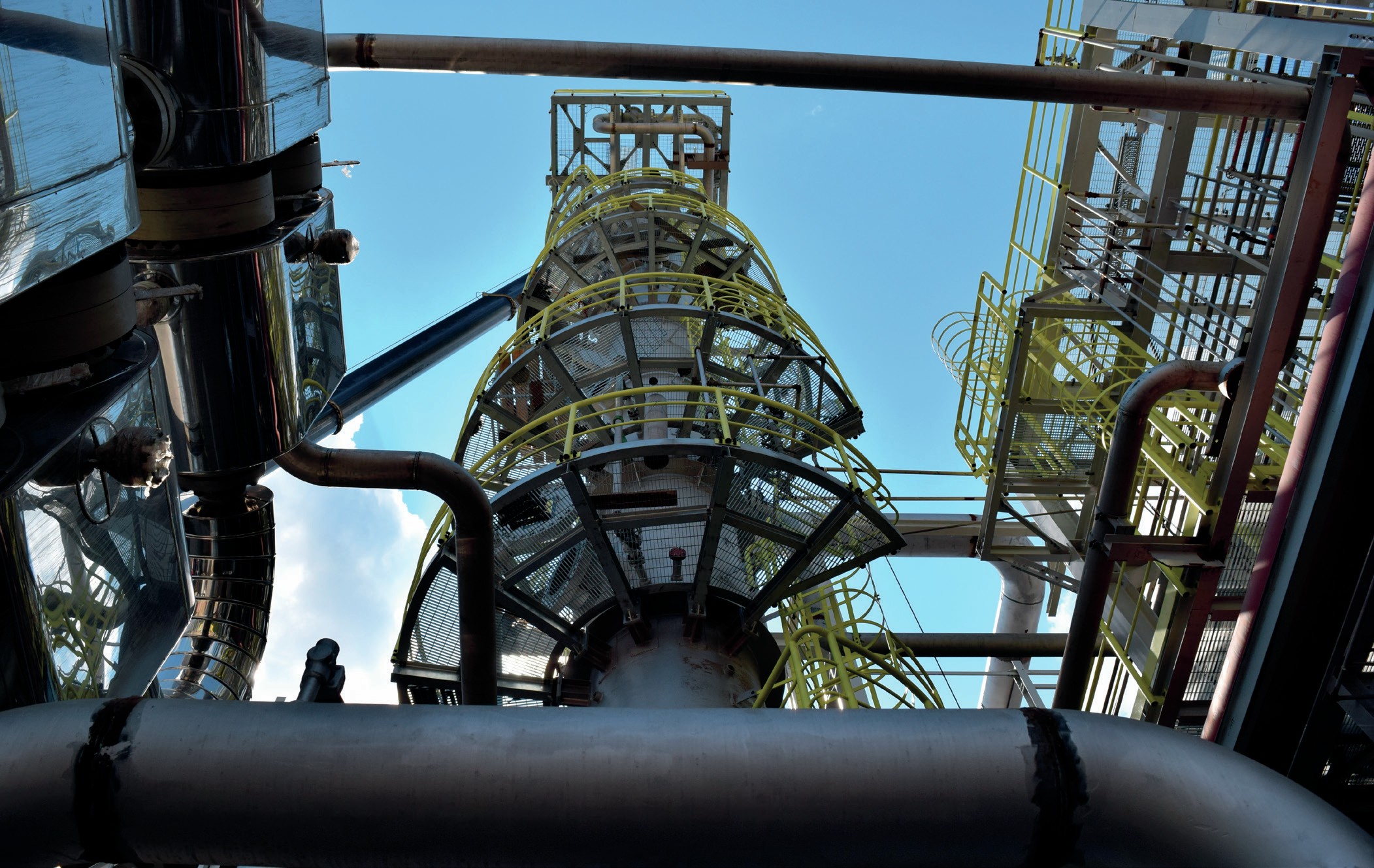
With urea prices currently hovering around the $450/t mark, farmers might be relieved to know that extra global urea supply is on its way.
Indeed, across the globe, a wave of new urea projects are either in the final stages of construction or being commissioned.
Globally, the International Fertilizer Association (IFA) expects urea capacity to grow by around seven percent (14 million tonnes) during 2020 and 2021 to reach 223 million tonnes1 . This short-term surge in capacity growth is being mainly driven by around a dozen new urea projects in just five countries – India, Nigeria, Russia, Brunei and Iran (Figure 1). These five countries collectively are expected to add around 12.6 million tonnes to global urea capacity.
However, analysts ICIS expect that, realistically, only 2.5-3.0 million tonnes of new urea supply will actually hit the market in 2021 – due to project delays arising from the Covid-19 pandemic and other factors (Fertilizer International 501, p20). According to ICIS, notable urea projects likely to be commissioned this year include:
- The new world-class Dangote Lekki-I plant and the second Indorama (IEPL) Eleme urea line in Nigeria. These are expected to become operational in mid2021, although doubts about the exact timing of their arrival remain.
- New Russian production capacity, including units at Acron (Novgorod), Metafrax (Gubakha) and TOAZ (Togliatti), is also likely to come on-stream by the year’s end.
- But only one of the four government-owned urea ‘revival projects’ in India, RFCL Ramagundam, is now expected to come on-stream in 2021 due to project delays.
Similarly, CRU is expecting the commissioning of up to six major urea projects in 2021:
- Brunei Fertilizer Industries (BFI), Sungai Liang, Brunei, 1.287 million tonnes capacity
- Dangote, Lekki-I, Nigeria, 1.271 million tonnes capacity
- RFCL, Ramagundam, India, 1.270 million tonnes capacity
- NavoiAzot, Navoi, Uzbekistan, 580,000 tonnes capacity
- Metafraz, Gubakha, Russia, 575,000 tonnes capacity
- Acron, Novgorod, Russia, 520,000 tonnes capacity.
These six projects combined would add around 5.5 million tonnes to global urea production capacity.
Below, we highlight some key ammonia-urea project developments over the last 12 months, with a particular focus on Australia, China, Egypt, India, Nigeria and Russia (Table 1).
AUSTRALIA
New urea plant for Western Australia
Australian gas producer Strike Energy is pressing ahead with a project to build an ammonia-urea production complex in Geraldton, Western Australia.
Project Haber, which includes a 800,000 t/a ammonia plant and a 1.4 million t/a urea plant, will consume natural gas sourced from Strike’s Greater Erregulla development in the Perth basin. This will be transported to the site via a 120-kilometre pipeline. The proposed production complex will also include 300,000 tonnes of on-site urea storage, power, utilities, steam generation and rail sidings.

Strike is currently preparing to move Project Haber to the front end engineering and design (FEED) stage. Engineering partner Technip Energies is currently reassessing the project’s capital cost estimate of $1.74 billion as part of this pre-FEED work. Strike has also retained JBS&G Strategen to start the planning process and seek the necessary environmental approvals for the project.
Strike intends to secure offtake agreements for up to 80 percent of the proposed plant’s urea output before advancing the project to the FEED stage. Discussions have already begun with 12 potential domestic and international buyers on urea offtake contracts.
At present, Technip and technology partner Haldor Topsoe are also exploring ways to maximise green hydrogen input to the project’s production process. Strike already intends to provide two percent of the plant’s hydrogen requirements via its own 10 MW electrolysis unit.
Strike estimates that Project Haber, by reducing its emissions intensity, could ultimately reduce the carbon footprint of Australian urea consumption by 50-65 percent, due to the abatement of 650,000-795,000 CO2 equivalent tonnes annually.
Pre-FEED studies and revised cost estimates are expected to be completed by the end of August. As a next step, Strike is planning to begin the process to finance the Project Haber later this year, although a final investment decision is not expected before the end of 2022.
Strike Energy has emphasised that Project Haber is at a preliminary stage, with successful development contingent on a number of factors. These include the proving of sufficient gas reserves, the outcome of FEED, access to finance and the securing of offtake agreements. If and when the green light is given, construction of Project Haber is expected to take 36 months.
Perdaman awards construction contract for Burrup urea plant
Perdaman Chemicals and Fertilizers Pty Ltd awarded the engineering, procurement and construction (EPC) contract for its Burrup urea project at the end of last year. The project is located at the Burrup Peninsula Industrial Area, some 20 kilometres northwest of Karratha, on Western Australia’s coast.
The $2.4 billion EPC contract was secured by a 50:50 joint venture between Italy’s Saipem SpA and local engineering and construction firm Clough Group. It covers engineering, the supply of equipment and materials, and the construction and commissioning of the 2.1 million t/a urea production plant. The building of a water treatment plant, a 100 MW power plant are also included in the contract, as are urea storage, loading and unloading facilities.
Saipem will provide Snamprogetti technology for the urea plant, while Haldor Topsoe will license its SynCOR™ technology to build the world’s largest single-train ammonia plant.
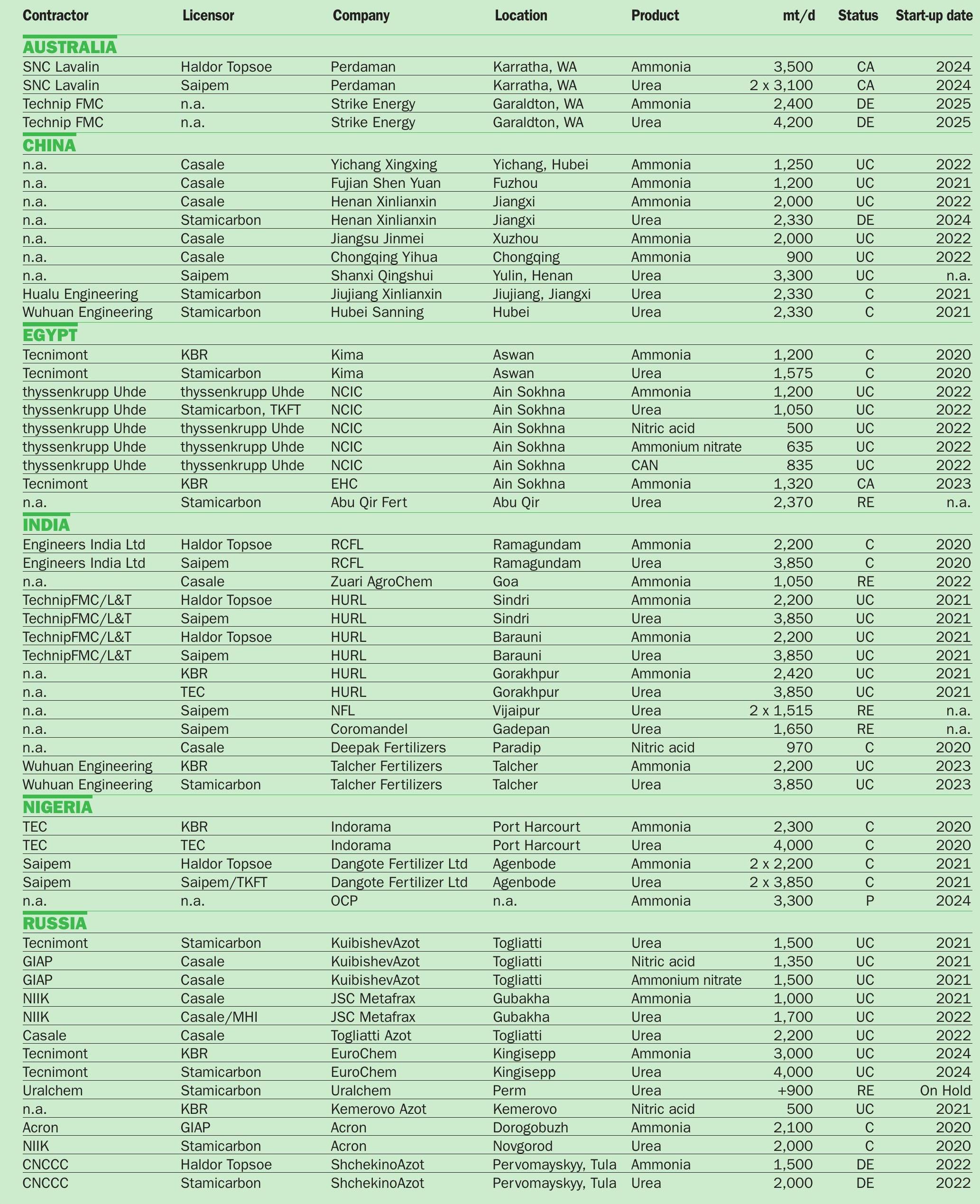
*Note This is an extract from the full global 2021 nitrogen project listing published in our sister magazine Nitrogen+Syngas in June this year (Nitrogen+Syngas 371, p26).
KEY
BE: Basic engineering
C: Completed/commissioning
CA: Contract awarded
DE: Design engineering
FS: Feasibility study n.a.: Information not available
P: Planned/proposed
RE: Revamp
UC: Under construction
Conversion:
1 t/d of hydrogen = 464 Nm/h
1 t/d of natural gas = 1,400 Nm/d 3 3
SAIPEM: New ammonia industry milestones
Saipem, with its reputation as a tier-1 engineering, procurement and construction (EPC) contractor, is fully committed to the energy transition and the sustainable and innovative approaches needed to deliver this. This is illustrated by the following three projects:
The Perdaman project, Western Australia
Perdaman’s ammonia-urea project is located at the Burrup Strategic Industrial Area (BSIA), approximately 10 kilometres from Dampier on Western Australia’s north coastline. Known as the Destiny Project, it will take natural gas from an LNG plant as a feedstock and convert this into large quantities of granular urea for export. This world-scale urea plant has an overall design capacity of 6,200 t/d, while the 3,507 t/d ammonia plant will be the world’s largest with a single converter.
The EPC project awarded to the Saipem-Clough joint venture includes:
- 3,507 t/d ammonia unit licensed by Haldor Topsoe A/S (HTAS)
- 6,200 t/d urea units licensed by Saipem and 6,200 t/d urea granulation units licensed by thyssenkrupp Fertilizer Technology (tkFT)
- Air separation unit able to produce 2,200 t/d of oxygen
- A combined cycle gas turbine (CCGT) power plant to produce electricity and steam from natural gas
- All associated utilities and offsite export facilities – including storage, ship loaders and conveyors at Dampier Port.
- The innovative construction approach will also involve extensive use of modularisation.
The state-of the-art technologies selected for the project will ensure high quality products are produced in a highly efficient and environmentally-friendly manner. Haldor Topsoe’s SynCOR™ technology, in particular, meets the international best practice benchmark for energy efficiency in ammonia-urea production. Consequently, the project will achieve a much lower average greenhouse gas (GHG) intensity compared to other more conventional fertilizer projects. To reduce the project’s carbon footprint even further, a dedicated solar power plant will generate about five percent of total net electrical power requirements.
This milestone project – due to its scale and by setting a new benchmark for low energy consumption – established new standards for the fertilizer industry and will become an exemplary reference plant for the burgeoning blue ammonia industry.
Haifa project, Israel
Saipem is providing Israel’s Haifa Chemicals with an efficient and low emissions solution for small-scale ammonia production. The new ammonia unit has a nominal rated capacity of 300 t/d and incorporates Haldor Topsoe’s Low Energy Ammonia Technology design.
Around 70-75 percent of the ammonia produced will be consumed by Haifa’s on-site nitric acid plants. The remaining 20-25 percent will be transported off-site in tankers by road. Any surplus ammonia will be refrigerated and stored on site at atmospheric pressure.
The project includes the installation of a carbon dioxide purification unit. This 75 t/d capacity unit will generate high quality food-grade CO2 from carbon dioxide recovered from the ammonia plant’s vent stream. The unit will purify, then liquefy and store this before eventual sale into the merchant liquid CO2 market.
The scale of this project makes it an important flagship reference for the emerging green ammonia industry.
Barents blue ammonia project, Norway
Saipem is pleased to announce the award of the concept study for Horisont Energi’s ambitious Barents blue ammonia proejct in northern Norway. This 3,000 t/a capacity plant will incorporate Haldor Topsoe SynCOR™ technology capable of achieving a 99 percent carbon capture rate.
Stefano Cao, Saipem’s CEO, said: “We congratulate Perdaman Industries for the achievement, and we are grateful for the confidence demonstrated towards our Saipem-Clough JV. This project – one of the largest and environmentally efficient urea plants in the world – will strengthen our leadership role in the gas monetisation market and will contribute to further diversify our geographical footprint.”
EGYPT
KIMA 2 enters commercial production
KIMA’s new $770 million ammonia-urea plant at its Aswan complex in Upper Egypt commenced production in May last year. This followed the completion of construction by contractor Tecnimont and commissioning trials in the first-quarter of 2020.
The KIMA 2 plant has a capacity to produce 1,200 t/d of ammonia and 1,575 t/d of urea. The ammonia production unit incorporates KBR Purifier technology, while the urea melt unit is based on Stamicarbon’s Pool Reactor technology.
EHC ammonia plant construction contract
Maire Tecnimont has secured a $350 million engineering, procurement and construction (EPC) contract with Egypt Hydrocarbon Corp (EHC) for a new ammonia plant at Ain Sokhna near Suez.
The contract, finalised in May last year, covers the construction of a new 1,320 t/d capacity ammonia plant at the site, as well as providing extensive utilities and off-site facilities. Output from the new plant will feed EHC’s existing ammonium nitrate plant at Ain Sokhna.
The project is scheduled for completion 36 months after financial closure. Project finance is being arranged by the Italian export credit agency SACE and US EXIM Bank.
Basil El-Baz, EHC chairman, said: “This contract is another outstanding opportunity to work with Maire Tecnimont, a company we trust with best in class expertise and experience. The EHC expansion project is a vote of confidence in the Egyptian economy and the reforms that have been undertaken to date. The project will serve as a catalyst for the mining sector, attracting foreign investment and increasing employment opportunities and providing the raw materials needed for the sectors activities.”
STAMICARBON: Focus on sustainability
Stamicarbon, the innovation and license company of Maire Tecnimont Group, has been at the forefront of fertilizer industry innovation since its establishment almost 75 years ago. The company is committed to increasing its investment in innovation and sustainable fertilizer production. Examples include:
- Ultra-Low Energy technology to reduce plant steam (energy) consumption.
- MicroMist™ venturi scrubbing systems to significantly lower emissions.
- Stami Green Ammonia technology to enable sustainable and green fertilizer production by using renewable resources and eliminating carbon.
- The development of a renewable power-to-fertilizer plant in Kenya, based on Stamicarbon’s green ammonia and nitric acid technologies (see page 8).
- The partnership with Shchekinoazot to develop and bring green technologies to Russia (see page 8).
- Participation in the European INITIATE project to create a symbiosis between the steel and fertilizer industry – by re-using captured carbon dioxide and carbon-rich off-gasses from steel mills.
- Contributing to the European PRO-METEO green development project to reduce CO2 emissions.
Energy saving
Stamicarbon’s innovative Ultra-Low Energy design for urea plants – which recycles heat three times instead of two – offers unrivalled energy savings. The design also substantially reduces urea plant operating costs by significantly reducing both steam and cooling water consumption. As well as being suitable for new plants, the Ultra-Low Energy design can also be incorporated in plant revamps – being applicable to both CO2 stripping plants and conventional urea plants.
The first two Ultra-Low Energy design plants with a capacity of 2,334 t/d went into operation this spring in China, while two others are under construction, one in Turkey and one for the same client in China.
Green ammonia
With the launch of Stami Green Ammonia technology, Stamicarbon has become a licensor for small-scale ammonia plants.
With four plants in operation, this capex-competitive technology already has a solid reference base, offering high reliability (thanks to a multi-service reciprocating processor) with a proven design. It can also be installed in currently operating plants, as a hybrid technology solution, to make existing fertilizer production more sustainable.
Other applications include the production of renewable energy carriers such as shipping fuels, for example, or the generation of renewable feedstocks for other processes.
Overall, Stami Green Ammonia technology offers a complete solution for carbon-free and sustainable ammonia production.
Pierroberto Folgiero, the CEO of Tecnimont’s parent company Maire Tecnimont, added: “With this achievement we are proving once again the great resilience of our core business in a particularly challenging period for the whole market. We are also really proud to play a strategic role in the development of the fertilizer industry in Egypt with an entrepreneurial client such as EHC.”
Stripper fabricated for NCIC urea melt plant
Major equipment items have been completed for NCIC’s new urea melt plant in Ain Sokhna, Egypt. Stamicarbon was preparing to ship the plant’s high-pressure stripper in June last year, after this was successfully fabricated by Schoeller-Bleckmann Nitec in Austria.
The 1050 t/d capacity urea melt plant is an integral part of NCIC’s under-construction Ain Sokhna fertilizer complex in Egypt’s Suez governorate. This is currently being built by a consortium of Germany’s thyssenkrupp Industrial Solutions (tkIS) in partnership with the Egyptian company Petrojet. The complex, which is scheduled for completion next year, will have the capacity to produce 440,000 tonnes of ammonia, 380,000 tonnes of urea and 300,000 tonnes of calcium ammonium nitrate (CAN) annually.
In a news update in June last year, Peter Lang, Stamicarbon’s project manager, said the Ain Sokhna project was running smoothly with all equipment on schedule.
Stamicarbon to revamp Abu Qir urea plant
Stamicarbon has signed a contract with Egypt’s Abu Qir Fertilizers to revamp the Abu Qir 3 urea melt plant in Alexandria.
The revamp of Abu Qir 3 will increase urea production capacity to 2,370 t/d. That compares to its current nameplate capacity of 1,750 t/d and design capacity of 1,925 t/d.
The existing urea plant dates from 1996 and uses Stamicarbon’s CO2 stripping process. Stamicarbon is providing both the license and the process design package for the revamped plant. This is expected to become operational in 2025.
The revamp is based on Stamicarbon’s EVOLVE CAPACITY™ design with medium-pressure (MP) add-on technology. This allows capacity to be expanded, but without investing in high pressure equipment or a high-pressure CO2 compressor, while simultaneously reducing energy consumption. The revamp will also reduce emissions to meet local norms.
INDIA
The Indian government has long supported self-sufficiency in urea production under its 2012 New Investment Policy (NIP). Implementation of this policy involves expanding domestic urea production capacity by funding the revival of a number of mothballed urea plants. The policy is finally starting to deliver results – with Chambal Fertilizers & Chemicals Limited (CFCL) commencing production at its 1.3 million t/a Gadepan III urea project in Rajasthan in 2019.
Four more 1.3 million t/a capacity ‘revival’ projects are scheduled to be commissioned over the next 4-5 years, as follows:
- RFCL’s Ramagundam plant, Telangana, in 2021
- HURL’s Gorakhpur plant, Uttar Pradesh, in 2022
- HURL’s Barauni plant, Bihar, and Sindri plant, Jharkhand, in 2023.
As of mid-2020, construction progress at the RFCL, Gorakhpur, Sindri and Barauni plants had reached 99 percent, 77 percent, 70 percent and 69 percent, respectively, according to local media reports.
Although the remaining ‘revival’ project, the Talcher urea plant in Odisha, is scheduled for completion in 2023, the plant remains at the design stage currently.
Ramagundam plant enters production
The renovated Ramagundam urea plant in Telangana edged closer to commercial production in March.
Urea production at the newly renovated plant, owned by Ramagundam Fertilizers and Chemicals Ltd (RFCL), had originally been due to start at the end of March last year, but this was delayed by India’s Covid-19 lockdown. Commercial production has been rescheduled several times since then.
RFCL did, however, successfully complete a prilling tower trial run at the plant at the end of February. Nirlep Singh Rai, RFCL’s CEO, said: “An important technical-grade urea production trial run was held. In addition, [a] bagging unit trial run was also successfully completed.”
He was also confident that commercial production would start in March: “Every day about 3,850 tonnes of urea and 2,200 tonnes of ammonia will be produced at the RFCL plant. In the coming days, there won’t be any shortage of urea in Telangana.”
The 1.27 million t/a capacity RFCL plant is a joint venture between five organisations. National Fertilizers Limited and Engineers India Limited are major partners, both owning a 26 percent stake. The Fertilizer Corporation of India (11%), the Telangana government (11%), the Gas Authority of India (14.3%) and the HTAS consortium (11.7%) own the remaining 48 percent.
Talcher urea plant selects Stamicarbon process
Stamicarbon was named in January as the technology licensor for the Talcher urea plant in Odisha. The company will deliver the process design package (PDP) for Talcher Fertilizers Limited’s 3,850 t/d urea melt and prilling plant. The melt plant will incorporate Stamicarbon’s Pool Condenser design, while the synthesis section will use Safurex® stainless steel.
The project is a strategic milestone for Stamicarbon, marking its return to the Indian market after more than 40 years. Other urea plants currently under development in India have generally opted for Saipem production technology.
NIGERIA
Dangote aiming for 2021 project start-up
Analysts expect Dangote’s Lekki project to begin commercial production this year, although an official announcement from the company is still pending.
The project’s first 1.3 million t/a capacity urea line underwent trials in June 2020, ICIS reported last year, with exports likely to begin in the first half of 2021.
“Realistically, we expect completion of the first Dangote line by the end of 2020, it is unlikely it will happen before. Commercial output should be available in second-quarter 2021 or possibly first-quarter,” an international trader told ICIS.
Project contractor Saipem was also expecting commissioning to be completed by the end of 2020 with production starting in 2021. “We are picking up now that things are looking more stable and are currently very well advanced,” Maurizio Coratella, Saipem’s chief operating officer, said in mid-July last year. “We are in the commissioning stage of the first train; for the second, we will have that commissioning in six to seven months’ time.”
Saipem is making special arrangements to enable it to meet the completion deadline, Coratella said, including setting up dedicated flights for vendors and suppliers.
Saipem is the project’s EPC contractor and is also supplying the urea technology for the plant. The petrochemicals complex, located in the Lekki district of Nigeria’s capital Lagos, includes two urea trains with a combined capacity of 2.6 million t/a.
Although the plant was said to have been completed mechanically in the first-quarter of last year, initial test runs scheduled for March 2020 were held up when the Covid-19 outbreak prevented Saipem’s engineers flying from Italy to Nigeria to help with commissioning.
While analysts expect the Dangote plant, and Nigeria’s second under-construction urea project, Indorama’s second 1.4 million t/a urea line at Port Harcourt, to both become operational soon – doubts about exact timings remain with no official word from either producer (Fertilizer International 501, p21).
RUSSIA
EuroChem gives go ahead for Northwest 2 project
EuroChem Group is proceeding with a project to develop the Northwest 2 ammonia-urea plant in Kingisepp.
Northwest 2 will have an annual production capacity of 1.4 million tonnes for urea and one million tonnes for ammonia. The new plant will be built alongside the existing one million t/a capacity Northwest 1 ammonia plant. This was commissioned in 2019 to provide ammonia to EuroChem operations in Belgium, Lithuania, and its adjacent phosphate fertilizer plant at Kingisepp. Yara also sources ammonia from the Northwest 1 plant, via the Estonian port of Sillamae, under an offtake agreement.
EuroChem recently secured the necessary finance for construction of the $1.6 billion Northwest 2 plant. Loans for the project were agreed at the St Petersburg International Economic Forum in early June. The lenders are Russian state development corporation VEB.RF and Russian banks Sberbank, VTB, Gazprombank, and Otkritie.
“This is the first time that EuroChem is implementing such a project with Russian banks, and for the first time a debt-toequity ratio of 80:20 has been achieved,” commented Vladimir Rashevskiy, Euro-Chem’s CEO.
Although most of the ammonia produced by Northwest 2 will be consumed on-site, EuroChem plans to place around 300,000 tonnes on the market.
Carbon-abatement at Northwest 2 should reduce the environmental impact of production at the Kingisepp site. The new project will achieve this by consuming the CO2 by-product from the adjacent Northwest 1 ammonia plant during its urea production process.
The new Kingisepp plant is an important project for EuroChem, says Vladimir Rashevskiy: “Northwest 2 is part of our drive to move beyond self-sufficiency in ammonia, a vital component of our fertilizer production needs. It will also boost our urea output capacity and market share in this critical commodity product. We are constructing a state-of-the-art plant in close proximity to our existing rail and shipping facilities, enabling easy transportation to production units and global markets.”
CASALE: Boosting GIAP ammonia plant capacity
In the last 2-3 years, Casale has successfully completed the revamping of two GIAP plants for EuroChem Group in Russia. The projects successfully delivered the maximum possible increase in capacity while simultaneously minimising the investment cost.
The two EuroChem plants, located in Nevinnomyssk and Novomoskovsk, were originally designed with a nameplate capacity of 1,420 t/d. However, in practice, they were operated at production capacities ranging between 1,650-1,700 t/d prior to revamping, depending on the season.
The design of GIAP plants is similar to vintage MW Kellogg plants. The main differences are in the refrigeration section where – instead of a refrigeration compressor – aqua ammonia refrigeration packages (AARP) are used. These are based on ammonia absorption in water. The column internals in the CO2 removal section of GIAP plants are also quite specific.
The following plant bottlenecks needed addressing:
- Air compressor limitations
- Unbalanced burning in the primary reformer affecting convection section performance
- CO2 removal – especially incipient flooding in the absorber
- Syngas compressor and turbine load
- Ammonia synthesis converter
- AARP refrigeration section.
Prior to revamping, the top-fired superheating burners in the primary reformer were operated at maximum load due to the low superheating temperature of the high pressure (HP) steam. This was fixed by repurposing the boiler feedwater (BFW) coil as a low temperature process air coil. This allowed the burner load to be reduced by heating the flue gas before it entered the high temperature super heating coil. This was a straightforward modification requiring only a few items.
The CO2 removal section was debottlenecked by switching to new Casale multipipe trays in the CO2 absorber. With a much higher active area, these trays are twice as efficient as standard sieve trays. The revamped absorber is now capable of exceeding a production capacity of 2,000 t/d.
Casale’s ‘clean/dirty’ separation concept was implemented to improve the performances of the nearby urea plant. This concept involves installing an external elevated vessel to operate as a solution flash drum at slightly higher pressure than the CO2 stripper. The hydrogen content of the CO2 feed to the urea plant was reduced to about 100 ppm thanks to this modification.
Welded plate exchangers were also installed in the CO2 removal section to improve efficiency.
An ammonia washing unt was installed to dry the make-up gas (MUG) feed to the synthesis loop. The ammonia synthesis converter, meanwhile, was revamped by installing an axial-radial three bed configuration with one quench and one interchanger. The resulting improvement in efficiency significantly reduced circulation inside the synthesis loop, with correspondingly lower power consumption in the synthesis gas compressor.
Casale adopted two different strategies for the AARP-based refrigeration sections at the Novomoskovsk and Nevinnomyssk plants. A completely new AARP was installed at the Novomoskovsk plant with a cooling capacity of about 12 MW. At Nevinnomyssk, in contrast, as well as the original AARP units, the client had an additional second-hand AARP. Casale therefore revamped this existing configuration.
The start-up and commissioning of the two GIAP plants was carried out smoothly after a shutdown of about 30 days. The success of Casale’s revamp project for EuroChem was confirmed by performances tests (below) – the revamps having transformed both sites into the most productive GIAP plants in Russia.
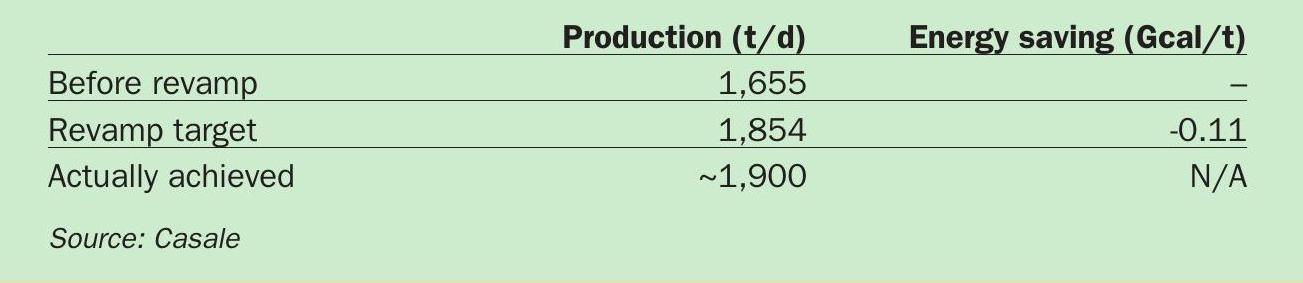
Previously, EuroChem had selected Maire Tecnimont to carry out early works for Northwest 2 under a memorandum of intent signed in October 2019. This work, carried out by subsidiaries Tecnimont S.p.A and Tecnimont Russia LLC, involved preliminary engineering and site surveying work at a brownfield site adjacent to EuroChem’s existing Kingisepp ammonia plant.
Acron completes ammonia revamp
Acron completed the revamp of its Number 4 ammonia plant at Novgorod in April. The Ammonia-4 plant was successfully uprated to its new production capacity of 2,500 t/d, having passed guarantee test runs.
The plant was originally commissioned in 2016 at a cost $500 million. It was the first ammonia plant built domestically in modern times by Russian engineers without the support of foreign contractors.
The Ammonia-4 revamp was carried out by Acron in conjunction with Haldor Topsoe. The revised design incorporates Topsoe’s heat exchange reformer (HTER), changes to the CO2 removal section, plus other modifications.
A team of Acron engineers and Topsoe specialists, working hundreds of miles apart, completed the successful overhaul of Ammonia4 late last year, enabling the plant to reach its new design capacity.
“Haldor Topsoe and Acron have been in successful partnership for quite a while and the revamp project, delivered in November 2020, marks another milestone in our cooperation. We believe our partnership will develop further, to the benefit of both companies,” said Peter Vang Christensen, managing director of Haldor Topsoe’s Moscow office.
Aleksandr Popov, Acron’s chairman, said: “Boosting the Ammonia-4 plant is an important project for Acron Group’s investment program… [allowing] us to increase production of nitrogenous and compound fertilizers at our Novgorod site.”
Dorogobuzh completes ammonia plant upgrade
PJSC Dorogobuzh, part of Acron Group, completed a five billion rouble upgrade of an ammonia plant at its nitrogen fertilizer complex in Russia’s Smolensk region in August last year.
The upgrade has increased the plant’s ammonia production capacity by one-fifth to 2,100 t/d. The revamp is being hailed as a landmark achievement. This is the first time in the whole of the post-Soviet era, according to Acron, that a Russian ammonia plant based on KBR technology has achieved this output level.
The Dorogobuzh ammonia plant, which dates from 1979, had an original design capacity of 450,000 t/a. Its annual ammonia output is now expected to increase by an extra 130,000 tonnes.
Dorogobuzh is the first ammonia plant in Russian to use KBR’s KRES heat exchange reformer technology. The resulting energy efficiency improvements have reduced the plant’s natural gas consumption by seven percent (per tonne of ammonia).
LLC Novgorodsky GIAP designed the ammonia plant upgrade. The project itself was carried out by 60 Russian contractors who brought in over 1,100 specialists and 50 pieces of equipment. Dorogobuzh and Acron employees also participated.
“The upgrades to the Dorogobuzh ammonia unit are an essential part of our technology development programme,” commented Vladimir Kunitsky, Acron’s CEO. “The increase in the unit’s capacity will give us additional ammonia to use for new projects.”
Gubakha project makes steady progress
Construction of the large Metafrax ammoniaurea-melamine (AUM) complex at Gubakha is making steady progress, Casale reported in an update last year. This was despite the serious hurdles caused by the Covid-19 pandemic and the need to guarantee the health and safety of all of those involved in the project, including Casale’s own on-site team.
“At the onset of the pandemic, appropriate measures and strategies were quickly put in place. We have strictly complied with all norms and procedures enacted by Russian authorities. All this has given us the confidence not to actually increase the strength of our on-site team. Meanwhile, for all vendors, specific procedures have enabled remote working, with minimal disruption of the workflow and reduced impact on the schedule,” Casale said.
The company added that it was confident that the project’s ammonia unit would come on stream soon: “All equipment of all units was already delivered to site before the pandemic struck. Owing to this, the piping prefabrication and installation is underway.”
Analysts expect Metafrax’s 575,000 t/a Gubakha urea plant to enter production this year.
TOYO: Three large-scale urea projects near completion
Japan’s Toyo Engineering Corporation is a leading urea process technology licensor and EPC contractor. The company owns the ACES21® proprietary urea synthesis technology and Spout Fluid Bed Granulation, a unique urea granulation technology.
Toyo continues to invest in innovation. It recently introduced innovative digital plant optimisation technology and novel urea plant maintenance techniques that enable the inspection of internal equipment.
In the past year, Toyo has been especially active globally in the construction, pre-commissioning and/or commissioning of the three large-scale and ‘epoch-making’ urea plants, as described below.
Indorama Train-2 project, Nigeria
In 2018, Indorama Eleme Fertilizer & Chemicals Limited (IEFCL) awarded a contract to Toyo to build one of the world’s largest ammonia-urea complex. This Train-2 project, located at Port Harcourt in Nigeria, has a design capacity of 2,300 t/d for ammonia (KBR Purifier™ process) and 4,000 t/d for granulated urea. This under-construction project follows the successful completion of the Train-1 project for IEFCL in 2016.
HURL project, Gorakhpur, India
In 2018, Toyo was awarded the urea technology license and the EPC contract by Hindustan Urvarak and Rasayan Ltd (HURL) to build a new ammonia-urea complex in Gorakhpur, India. The plant has a design capacity of 2,200 t/d for ammonia (KBR Purifier™ process) and 3,850 t/d for prilled urea. Construction activities are continuing, despite the serious Covid-19 pandemic situation in India, with commissioning expected in due course. Operational staff at the plant will have the opportunity to train on Toyo’s own operation training simulator (OTS) prior to the commissioning phase.
MSPIC project, Khuzestan, Iran
Toyo is the urea technology licensor for the under-construction Masjed Soleyman Petrochemical Industries Company (MSPIC) ammonia-urea plant. This project is currently being built by PDIEC in Iran’s Khuzestan Province. Toyo was originally awarded the license for the 3,250 t/d capacity urea plant in 2016. The company subsequently completed the design package for MSPIC and also remotely supported the project’s detailed design, fulfilling both requirements in a timely manner. With both construction and pre-commissioning now close to completion, the MSPIC plant is due to enter commissioning later this year.
CHINA
Stamicarbon licenses second ultra-low energy urea plant
Stamicarbon has signed a licensing and equipment supply deal for a second ultra-low energy urea plant in Jiangxi province.
The agreement is with Henan Xinlianxin Chemicals Group who are currently commissioning the first plant in China designed using Stamicarbon’s Launch Melt™ ultra-low energy design.
The second urea plant for Henan Xinlianxin will have a production capacity of 2,334 t/d and features a pool reactor. It is expected to enter production in 2023. Stamicarbon has agreed to deliver the process design package, together with proprietary high pressure equipment in Safurex® , plus associated services for the urea melt plant and prilling plant.
The Launch Melt™ design – which recycles heat three times – offers unrivalled energy savings, according to Stamicarbon. It also reduces plant operating costs by cutting both steam and cooling water consumption.
This is the third licensing deal between the two companies in five years. The latest agreement follows an initial revamping project signed in 2016, and the award of the design license for the first ultra-low energy urea plant in 2017.
Author’s note
A complete and comprehensive breakdown of all current global nitrogen projects is provided in the 2021 Nitrogen project listing published by our sister publication Nitrogen+Syngas in June (Nitrogen+Syngas 371, p26).
References