Fertilizer International 504 Sept-Oct 2021
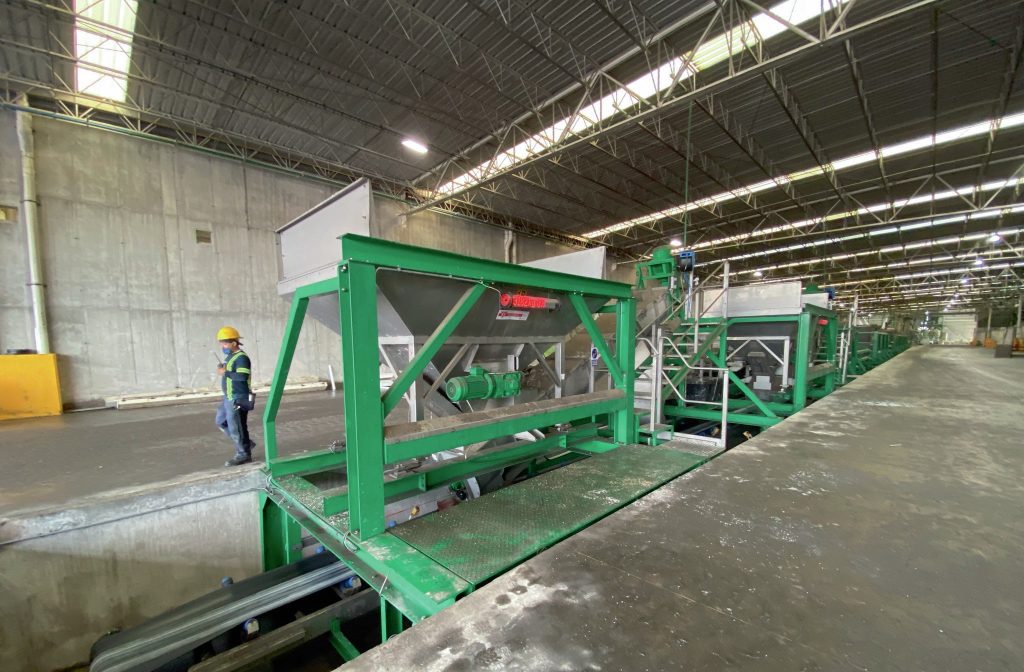
30 September 2021
Who’s who in fertilizer handling, bagging and blending
FERTILIZER HANDLING
Who’s who in fertilizer handling, bagging and blending
An update on the latest in fertilizer ship loading, handling, bagging and blending, including new contracts, company news and advances in technology.
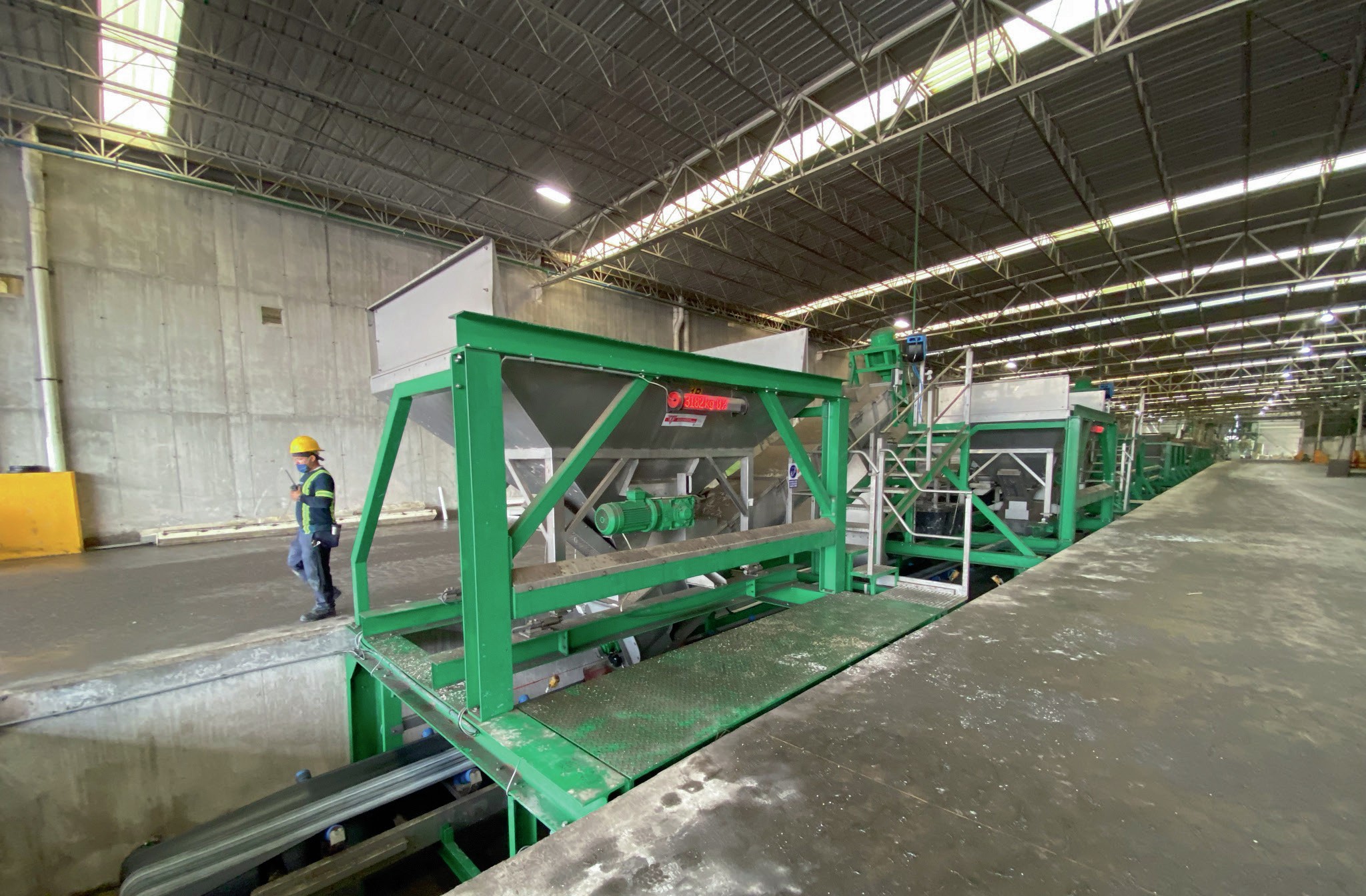
AMECO has over 80 years of experience in the bulk handling business. Notably, the company designed and manufactured the world’s first portal reclaimer for Morocco’s phosphate mines in 1965. The Alsace-based French firm also went on to start-up the first portal reclaimer in the United States in 1969.
AMECO currently supplies stackers, reclaimers, blending systems and shiploaders for fertilizer, pulp, biomass and coal power plants and port terminals. In 2020, the company secured a contract to design and deliver a portal reclaimer for Keyera at Canada’s largest sulphur handling facility. This was due to be delivered in the first half of 2021 in partnership with Tri Innovations, a leading engineering firm based in Calgary.
The 2,000 t/h reclaimer, based at the South Cheecham Sulphur Handling Facility (SCSHF), will handle a 20,000 tonne stockpile of prilled sulphur – and is hardened to withstand both extreme Northern Alberta temperatures and corrosive sulphur dust. It comes installed with automation and remote-control features that help increase safety by minimising on-site human intervention. Both the reclaimer and the SCSHF were scheduled to begin operations in the first half of 2021.
“I am very excited that our first collaboration with Tri Innovations and Keyera has led to such a successful outcome. This deal highlights how well our teams – from sales and marketing to engineering and project management – can get things done as well as the momentum our company has despite challenges due to Covid-19,” said Stephane Killian, AMECO’s CEO.
Bedeschi shiploading system for Borealis
Bedeschi is a well-established supplier of crushing and handling machines for cement, steel, coal, mining and other industrial processes. The Italian industrial manufacturer moved into the marine sector 15 years ago and now offers a range of large-scale onshore shiploading equipment.
An innovative feature of Bedeschi’s ship-loading technology is the sealed conveyor and telescopic chute system developed by the firm. The system is highly effective at dust prevention during the port-side unloading, handling and bagging of fertilizers.
In 2020, Bedeschi installed a new ship-loading system for Borealis in the port of Rouen, northern France. The company’s contract also covered the installation of the conveyors needed to transport products from the Borealis-owned manufacturing plant to the port. The project presented Bedeschi with some notable challenges:
- The product being handled – calcium ammonium nitrate (CAN) – is extremely aggressive in terms of corrosion
- A special rubber tyre mounted shiploader machine was necessary, because of the limited space available on the dock
- Project management, particularly health and safety, was also a major concern, as the shiploader would need to be installed while the production plant remained in operation
- Finally, the time available for delivery, installation and commissioning of the equipment was extremely short.
In September 2020, Bedeschi also secured a contract to supply Egypt’s first fertilizer export facility at the Port of Sokhna in the Red Sea. This was awarded by Petrojet, the main contractor for fertilizer producer NCIC. The contract covers automatic storage with the stacking and reclaiming of up to 100,000 tonnes of fertilizers from NCIC’s nearby phosphate production site. A complex system of belt conveyors then transports the fertilizer to the quay where a 900 t/h capacity mobile shiploader on rubber tires loads awaiting ships. Bedeschi was selected as the only company being able to provide both the stacking and reclaiming system and the shiploading machines.
In November 2019, also in Egypt, Bedeschi installed a complete handling system on behalf of KIMA at its ammonia-urea complex at Aswan. The project, developed with long-standing partner Tecnimont, was designed to transport urea coming from the granulation plant to either bagging silos or to urea bulk storage, as well as reclaim urea from bulk storage to bagging silos. Specified equipment included:
- A reclaimer with a 240 t/h capacity
- A belt conveyor line with a total length of one kilometre
- Three tripper cars
- Diverters
- A dedusting system for each transfer point
- Vibrating screens
- Belt weighers
- A complete control system.
Bedeschi has also strengthened its presence elsewhere North Africa. In October 2019, Morocco’s OCP Group once again chose Bedeschi as its engineering, procurement and construction (EPC) contractor for an expansion project at its Jorf Lasfar complex and port – with the aim of increasing sea freight capacity for shipping out fertilizers. The project consists of a five kilometre long, 2,000 t/h capacity conveyor line for fertilizers and phosphates. Bedeschi is providing the engineering, design, assembly and commissioning of the new conveyor line and will also integrate it with the OCP’s existing handling systems at Jorf Lasfar.
Bruks Siwertell’s healthy order book
Bruks Siwertell has successfully secured several fertilizer and sulphur industry contracts since the start of 2019. These have included repeat business from US company Martin Operating Partnership in Beaumont, Texas. This contract covered the installation of a new shiploader capable of safely and reliably handling sulphur prills at high capacities.
The new rail-travelling loader will be used for loading prilled sulphur into ships at a capacity of up to 1,200 t/h. It is ideal for terminals where space is at a premium, being capable of filling every ship’s hold without the vessel needing to move along its berth.
“Martin Operating Partnership returns to Bruks Siwertell as a trusted and reliable partner, and we are delighted to renew our strong 15-year business relationship with them,” said Ken Upchurch, vice president, sales and marketing, Bruks Siwertell Americas. “Our proven technological capabilities and our commitment to deliver the loader within the space of nine months were all factors that secured the contract.”
Martin Operating Partnership handles various sulphur cargoes. Prilled sulphur, usually destined for agricultural applications, can be stored and loaded in open air – although minimising sulphur dust emissions remained a key concern for the company. Fortunately, the shiploader’s fully-enclosed conveyors, as well as its dust suppression systems, provide a high level of environmental protection.
“At Bruks Siwertell, we handle sulphur under many conditions and in different climates,” said Upchurch. “The foundation of our robust, reliable designs is their ability to withstand demanding operating conditions and also to handle cargoes without damage and spillage.”
EMT’s 200-metre-long blending plant in Mexico
Netherlands-headquartered EMT is one of the world’s largest fertilizer blending and bagging equipment producers.
In the first half of 2021, the company installed a state-of-the-art fertilizer blending factory, for ISAOSA (Insumos y Servicios Agrícolas de Occidente S.A.) at the port city of Topolobampo in the Gulf of California, Mexico.
ISAOSA helps Mexico’s farmers create value by offering completely balanced nutrition programmes for strategic crops. These incorporate blended mixtures of fertilizer products precisely tailored to match soil conditions and crop yields. This is now possible thanks to the best available blending and bagging technology provided by EMT. Zico Zeeman, EMT’s business development manager, picks up the story.
Installation of the factory commenced in the last quarter of 2020 and was finished in July 2021. All of the factory’s equipment was manufactured in the Netherlands and shipped to the end user in no fewer than twenty five 40-foot-long shipping containers.
The completed machine is designed to operate at a capacity of 300 t/h and is more than 200 metres in length. This high capacity is achieved by running two lines in parallel. This ensures the blend quality is perfect and also allows the machine to be filled by multiple front loaders simultaneously.
In line with the latest advances in fertilizer treatment, a liquid inhibitor is applied as a direct coating to urea prior to blending. Initially, a conditioner is added to break up any lumpy urea material via a liquid injection point installed above a direct blending screw. By weighing both the urea conditioner and the inhibitor, the flow of both liquids is constantly monitored and adjusted to ensure the treatment of the end-product is exactly as required.
The inhibited urea is received on the central conveyors allowing other weighing hoppers to dose any extra constituents required directly on top of this material. In this way, the inhibited urea can be incorporated within a blend of other products. A total of 12 dosing hoppers and six liquid dosing units are available per line. Another blending screw ensures that all the constituents are properly mixed before they are directed over a coarse screen. A fine screen with a bypass option can also be used to sieve dust out of the blend.
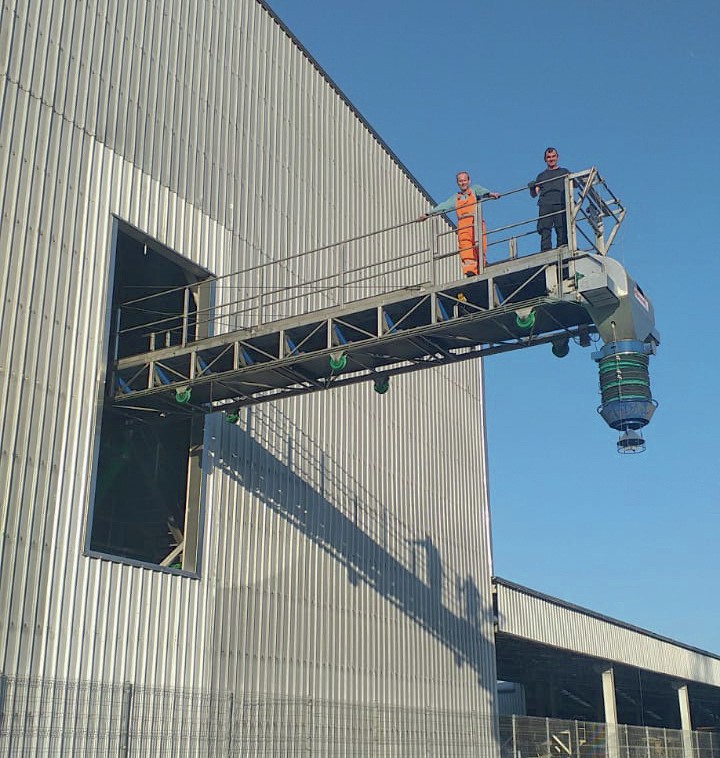
The final blended product is transported to one of the five stainless steel bulk hoppers, each with a capacity of 30 tonnes, or placed directly onto the train filling shuttle conveyor. This conveyor can move over the outer fence of the compound to fill trains which are positioned on the railroad directly next to the production facility. Once the train is full, the conveyor can be retracted inside the compound’s borders.
The complete blend line is computer controlled and can easily be operated with one operator from the central office. With this new machine line, ISAOSA can triple its annual production to 300,000 t/a capacity.
As well as the granular fertilizer blending plant, EMT is also installing a second blending unit at the ISAOSA warehouse. This is solely dedicated to blending various water-soluble fertilizers (WSFs) according to precise recipes. This WSF blending unit is currently being commissioned and is expected to enter full production in September this year.
The new WSF machine line consists of 11 weighing hoppers which can be filled with big bags, small bags or in bulk. Again, this machine enables the product to be screened for large lumps and allows liquid to be added in the blending screw. A shuttle conveyor can discharge the material into five different bagging units for either small bags or big bags.
In August 2019, Bruks Siwertell also secured a contract with Ashdod Port Company Ltd for the delivery of a Siwertell ST 490-M screw-type ship unloader for Israel’s largest sea port.
The was ordered as part of the port’s major expansion plans. The machine will be rail-mounted and used to discharge sulphur and pet coke at continuous capacities of 600t/h and 500t/h, respectively, from vessels up to 60,000 dwt. The totally-enclosed unloader was the only system that could meet the company’s environmental protection standard together with safe, high-capacity throughput.
“Ashdod Port Company chose Siwertell technology to secure its substantial and growing dry bulk cargo volumes for a number of reasons,” said Bertil Andersson, Siwertell sales manager. “Most significantly, our Siwertell unloaders are the only proven solution for safe, enclosed and continuous sulphur unloading. They also meet the port’s strict environmental requirements, handling materials without dust or spillage.”
Sulphur is highly toxic, volatile and corrosive. Its containment also creates the potential for fires and even explosions.
“We know how to deal with these dangers,” said Andersson. “Our sulphur-handling ship unloaders have been supplied to the market for over 30 years. All these units are fitted with the Siwertell Sulphur Safety System (4S), which detects and extinguishes fires early, shutting down the system to stop their spread, and safely containing them before they can become a full-blown blaze. To contain explosions, steel casings are reinforced and explosion-venting valves are fitted along the conveyors to relieve pressure.”
The delivery of the new ship unloader to Ashdod’s bulk terminal was scheduled for April 2021.
Bruks Siwertell previously installed a new 600 t/h Siwertell ship unloader at Yara International’s Glomfjord fertilizer terminal in Norway, just inside the Arctic Circle. The installation and performance tests were completed on schedule in July 2019. The rail-mounted Siwertell ST-490M ship unloader is being used to offload various types of phosphate rock from vessels of up to 20,000 dwt. It will also handle potash fertilizers.
“Yara is well aware that it can expect a lifespan of many decades from its new unloader, thanks to a previous Siwertell installation for the company that has been in service since 1980,” said Peter Goransson, former sales manager and senior advisor, Siwertell. “It also knows that it can trust the operational and environmental performance of Siwertell technology.”
Glomfjord is exposed to high winds and very cold temperatures. Being within the Arctic Circle, it is also subject to stringent environmental legislation to protect the surrounding coastline from harmful shipping pollution.
“The Siwertell screw-type ship unloader was not only chosen for its ability to safely handle sensitive dry bulk material like phosphates, and for its environmental credentials, which include high levels of efficiency, and a totally-enclosed conveyor system, eliminating dust emissions and spillage, but also for its impressive through-ship capacity,” said Goransson.
Solex expands into bulk materials handling
Solex Thermal Science is a world leader in high-efficiency, indirect heat exchange technology for the heating, cooling and drying/ conditioning of free-flowing granular materials such as solid granules, pellets, beans, seeds and particles. For more than 30 years, the Canadian-headquartered company has installed more than 800 heat exchangers in more than 50 countries worldwide with applications such as fertilizer, oilseeds, sugar and industrial materials.
Building on this track record and experience, Solex has announced its expansion into the bulk materials handling market. The company recently launched a new line-up of in-house fabricated standalone feeders for industries such as fertilizer, food products and industrial materials.
“This move is a natural evolution for Solex Thermal Science given our 30 years’ of experience in moving solids such as prills, granules and pellets through heat exchangers with incredible precision,” says Solex Thermal Science CEO Lowy Gunnewiek. “This experience will be foundational for us as we expand our growing line-up of high-quality, high-performance and robust equipment solutions to new markets and new customers.”
The highlight of the company’s initial product offering is an oscillating gate design that’s already in active use within the fertilizer industry. Indeed, more than 80 of Solex’s oscillating gate feeders are currently operating as part of vertical heat exchangers in nearly a dozen countries around the world. More than two-thirds of these are in fertilizer applications such as urea, NPK, MAP and potash.
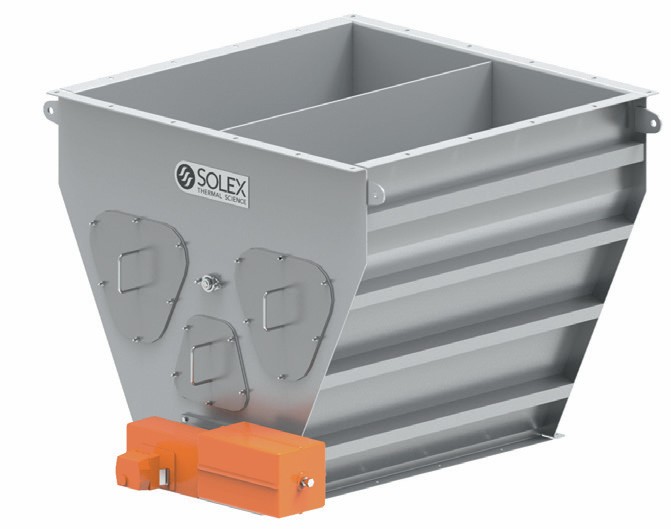
Solex’s oscillating gate splits the product into the two symmetrical mass flow funnels. These are created by the device’s fixed outer walls and its moving inner walls at the centre. These form a pair of slotted shaped openings through which the material flows.
“The gates look like a trouser leg. The product flows downward by gravity and divides into two streams. Those gaps are controlled by a common shaft that, when rotated, moves the walls inward or outward depending on the desired flow rate,” says Jason Gass, technical design & project specialist at Solex Thermal Science.
“And like all of our discharge feeders, we’ve taken a practical, scientific design approach to the oscillating gate that also accounts for the transition between the bottom of a storage bin or feed hopper to the discharge feeder, as well as the spatial constraints and equipment used to convey the bulk solids after being discharged.”
According to Gass, the benefits of the oscillating gate design include its short height, gentle product handling – as well as its reliability within the dusty conditions typical in most fertilizer applications.
In addition to fertilizers, Solex’s oscillating gate is well suited to handling minerals and other high-density granular solids.
Solex’s other two standalone feeders include the vibrating louver and sliding frame designs.
The vibrating louver is designed for lighter material applications such as sand, sugar or plastics. It uses a series of partially overlapping louvers carefully positioned within a self-supported frame. These vibrate linearly to offer a full live-bottom discharge system.
This feeder ensures mass flow by allowing product to flow along the multiple overlapping shallow louvers into a series of slot openings.
The sliding frame, meanwhile, is designed for medium-duty applications such as seeds, beans or delicate granules. It incorporates a fixed component made up of a series of small mass flow hoppers. These feed the material toward the sliding frame and, as the sliding frame moves horizontally back and forth, the hoppers subsequently discharge their solids.
“Whether it’s urea granules or soybeans, reliable, uninterrupted mass flow of bulk solids plays an important role in material handling systems efficiency while maintaining product quality. Our world-tested equipment can be tailored to different material flow properties, while providing operators with maximum control and a guaranteed first-infirst-out flow sequence,” says Gunnewiek.
Virtual commissioning
The virtual commissioning of blending and bagging systems has helped surmount the challenges presented by the Covid-19 pandemic, as Brett Binnekade, development engineer at Bagtech International, explains.
It’s March 2020, and the South African President has just announced a 21-day lockdown. Our mechanical and electrical teams are on-site in Lagos installing a new fertilizer blending plant. Our systems engineer is about to fly out to carry out the final commissioning when all physical travel is halted. Much to our surprise, this would be the first plant that we commission virtually.
Luckily for Bagtech International, virtual commissioning was something we’d been pursuing for some time. Remote assistance and service has always been a high priority for the company – we select the automation components in our plants based on this. Each component is connected to a multi-layer OT (operational technology) network, allowing our technical support team to access them remotely. It is this modern architecture that gave us the means and ability to start commissioning our plants virtually. Yet the Covid-19 pandemic pushed us to do it much sooner than expected. We know many companies who share the same sentiment!
Since the start of the pandemic, our systems engineers have not physically been on-site to commission a machine. Even with the opening of borders and travel, virtual commissioning is now our standard practice. This offers some immediate benefits to our clients and us – like reduced cost of travel and accommodation, significantly faster commissioning times, and reduced risk of Covid19 infections. However, virtual commissioning is more than just remotely accessing machines from thousands of kilometres away. We have been able to do this for years – remote access being just the final stage in a three-stage virtual commissioning process.
The first two stages generally happen behind the scenes and involve simulation and modelling of hardware and software – checking for errors and bugs and cycling back through the stages if any are found. These first two stages are entirely virtual – allowing engineers to run as many tests as they wish to uncover and fix issues. This is all done before installation, thus reducing the time required on-site. Since there is no physical machine running at this point, there is no safety risk, and the delays in conforming to on-site safety standards are negated.
At this point, If you are familiar with the term ‘digital twin’, the concept of virtual commissioning may seem the same, but it’s not. Virtual commissioning, as the name implies, is just for the commissioning phase of a plant. In contrast, a digital twin exists throughout the entire plant’s life cycle – being fed with live data from the physical plant to create a live digital copy. Digital twins do exist in the development and design stage of a physical machine or plant. But they continue to add value after their physical counterpart has been commissioned by providing a deeper level of insight into the system.
Fertilizer blending and bagging, particularly at high production rates, is prone to many variables. External variables, like temperature and humidity, raw material variables, like density and particle size, even variables linked to power or maintenance can cause undesired effects. Nowadays, all these variables are already measured most of the time, even when no dedicated sensors are in place. That’s because some devices have a plethora of sensors inside for their own use. For example, the servo controllers we use are fit for their purpose – which is to drive servo motors. However, they also contain sensors to measure variables like power supply voltage, frequency, temperature, humidity and many more. Now, because they are connected to an OT network, the data from these sensors is available to link to digital twins, internet of things (Iot) applications, machine learning algorithms and, importantly, for virtual commissioning.
As soon as a value from a sensor is digitised, it can be sent via the internet, and the systems engineer can view and analyse it in real-time. With this much data available, there is no need for the system engineers to be on-site anymore. Power problems are prevalent in African countries and a recent plant installation posed some challenges, as the voltage from the local power utility was too high. This meant the entire commissioning and pre-production runs were done using a diesel generator. The generator was new, it was a reliable brand, and our plants are designed to run on generators. Yet, we still faced faults related to power problems. All available test equipment on-site showed flawless power. However, our system engineer could tap into various sensors around the plant and present time-series data showing large voltage spikes, frequency variations and a poor waveform. It was these data that assisted our client in finding the root cause.