Sulphur 399 Mar-Apr 2022
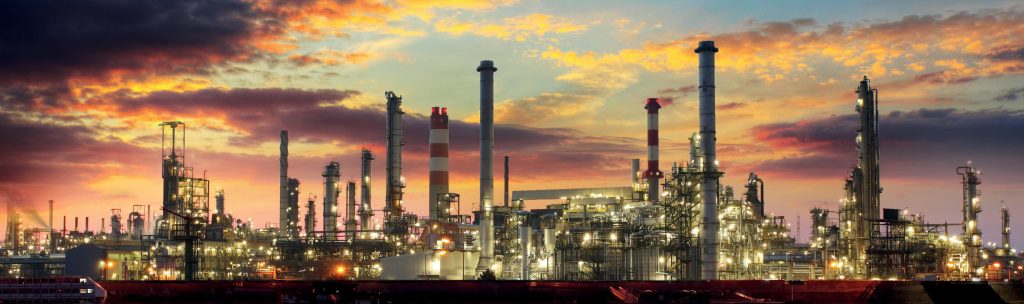
31 March 2022
SulGas Virtual 2022 Conference
CONFERENCE REPORT
SulGas Virtual 2022 Conference
The fourth SulGas Conference organised by Three Ten Initiative Technologies took place 1-4 February as a virtual event. Selected highlights from some of the presentations from SulGas 2022 are given below.
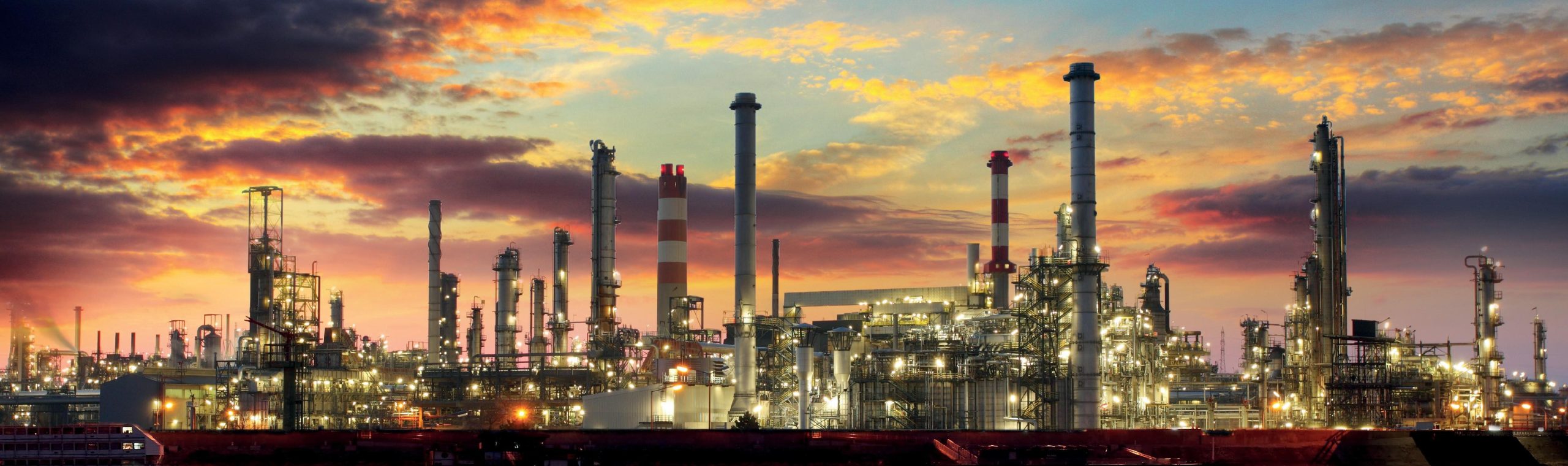
This year’s SulGas Conference, now in its fourth year, was held for the second time as a virtual event due to the ongoing Covid-19 pandemic challenges and restrictions. Organised by Three Ten Initiative Technologies, the Sulgas Virtual 2022 Conference was bigger than ever attracting 436 participants from 80+ countries including 40+ operating companies. The event was held over four days from 1-4 February and combined a mixture of technical presentations and Q&A sessions as well as an exhibition and networking opportunities. All being well, the plan is to return to an in-person event in 2023.
The aim of the SulGas conference is to bring together all stakeholders from across the refining, gas processing, chemicals, technology, and engineering companies in the area of sulphur and gas treating. SulGas focuses on issues unique to India in the areas of equipment and process design, process optimisation, operations, near misses, analytical methods, and troubleshooting.
The keynote speaker for SulGas 2022 was S. Bharathan, Executive Director – R&D of Hindustan Petroleum Corporation Limited, who provided an overview of the oil and gas industry in India focusing on three main themes: desulphurisation, decarbonisation, and digitisation.
Starting with desulphurisation, current research and development in hydroprocessing was highlighted, including improved reactor internals and new hydrotreating catalysts designed for low pressure (<25 bar), lower hydrogen consumption, enhanced lifetime, and low metal loading. There have also been advances in solvents, sorbents, and membranes. Future research will be carried out into selective catalytic reduction. A large number of biogas plants will be built in India in the next 2-3 years, all of them requiring gas cleaning as the first step.
The focus of the presentation then moved on to decarbonisation and how refineries will look in the future as they transition from traditional refinery processes to a future with low-carbon refineries. India’s contribution to CO2 emissions in 2019 was 2.6 trillion tonnes. Use of natural gas instead of naphtha and intermediate fuel oil (IFO) in hydrogen generation units (HGUs) and process heaters/furnaces could reduce CO2 emissions by >30%.
The presentation finished with a discussion on the benefits that digital transformation has already brought to the oil and gas industry and what can be expected in the future.
Deep desulphurisation requirements
In recent years Indian refiners have faced the dual challenge to switch over simultaneously to BS VI fuels and also change over to low sulphur fuel oil (LSFO) due to IMO regulations in 2020. In a bid to curb vehicular pollution, the Indian Government decided in January 2018 to implement stricter emission norms of Bharat Stage (BS) VI from April 1, 2020, by skipping BS-V altogether. The main challenge in moving from BS IV to BS VI was an 80% reduction in sulphur from 50 to 10 ppm for both MS and HSD coupled with a revision of a few other major parameters specific to MS and HSD. Nagendra Hindupur of Hindustan Petroleum Corporation Ltd discussed the challenges faced by refiners, the strategies that were used to roll out BS VI fuels successfully by April 2020 and alternatives to manage refinery residue in the changed fuel oil quality post IMO 2020 implementation.
Debottlenecking for capacity increase
Subramanya Prabhu of Mangalore Refinery and Petrochemicals Ltd described MRPL’s low-cost modification scheme to enhance the AAG processing capacity of its existing conventional Claus process. MRPL operates six sulphur recovery trains. The capacity of SRU 2/3 has been increased by approximately 14% compared to the previous maximum throughput by using an in-house oxygen enrichment scheme. The SRU units were debottlenecked with minor investment by making use of an available oxygen-rich waste stream from the polypropylene nitrogen plant.
Process instrumentation and control
One of the key topics of the conference was the importance and challenges of sulphur plant process instrumentation and control. Jochen Geiger and Anantha Kukkuvada of Ametek Process Instruments reviewed today’s process analysers and best practices to maximise the full benefits of analysers. The air demand/tail gas analyser can contribute up to 10% of the total efficiency of the sulphur plant. A closed control loop, including a H2 S in feed gas analyser can add another 3%. Analysers have an average lifetime of approx. 15 years and maintenance continues to be the largest cost component of the lifecycle cost for analysers. The importance of involving specialist analyser vendors during the front-end engineering and detailed engineering stages of a new project and having a complete analyser maintenance team and philosophy in place at start-up was emphasized. Bringing together the process, analyser, control, and piping engineering disciplines of the team so all benefits are realised is key as is the regular training of operators and maintenance staff to keep up with the latest technical advancements.
Angshuman Paul of Adage Automation focused on the design of process analyser sample probes and sample transport lines to ensure representative and rapid sampling and to avoid the possibility of contamination or dead volume. Adage provides complete, integrated analyser systems and all related services from initial engineering through manufacturing, testing and field start-up. Having an integrated analyser system comprising the sample recovery systems, stream selection facilities, temperature-controlled analyser houses etc., has the benefit of providing a single channel for communicating and interfacing, and helping to achieve consistent design, assembly, and component selection.
Prakhar Rohila of Bharat Oman Refineries Ltd (BORL) presented a new interlock scheme developed in-house for BORL’s SRU reheaters. The original interlock scheme was unreliable and was experiencing faulty signals leading to tripping of the units during electrical faults such as power dips, bus changeover and voltage dips. Tripping of the units had a number of negative consequences such as flaring of acid gas to the environment, financial losses due to loss of sulphur production (7 t/h), reduced reliability, and less margin for restart-up as the burners are turned off when the heater trips, leading to delays in the start-up time. Since implementing the new interlock scheme there has been no tripping of the system.
Pandemic challenges
Prolonged idling of SRUs
Umang Shrivastava of Mangalore Refinery and Petrochemicals Ltd (MRPL) shared MRPL’s experiences and the challenges faced in preservation of its sulphur recovery units after prolonged idling during the pandemic. MRPL operates a 15 million t/a integrated refining and petrochemical complex, which has six trains of SRUs. During the pandemic, as demand for auto fuels reduced worldwide, the process units were either operated at lower load or idled and the SRUs were forced to shut down to avoid operating below turndown limits. The main challenges of the prolonged idling were how to keep the units free of corrosive substances and moisture and how to sustain them under an inert atmosphere. Several challenges were faced in bringing the plants back on online. Critical equipment such as incinerators and condensers caused bottlenecks due to leakages, and back pressure etc. Lessons learned and best practices to ensure reliable operation post prolonged idling were discussed.
Start-up and shutdown with constrained manpower
Harpreet Singh of Indian Oil Corporation Ltd (IOCL) described IOCL’s journey towards commissioning of the BS-VI ARU/SWS/SRU/TGTU plant at IOCL Panipat Refinery. A number of challenges were faced during the Covid crisis in 2020. Covid-19 affected the commissioning activities, limiting the manpower and mobilisation of personnel. After the first Covid wave, plant commissioning activities resumed with limited manpower.
Remote start-up of sulphur recovery units
Jan Willem Hennipman of Comprimo recounted how Comprimo was able to provide remote support for the start-up of sulphur recovery units during the Covid-19 pandemic when international travel came to a virtual standstill. As the usual practice of providing on-site support for operator training, plant inspection, commissioning and start-up could no longer be done “in person”, other means had to be explored to be able to support the operating companies during the initial start-up of their facility.
Jan discussed several start-ups that were completed during the pandemic with remote and partial remote support from the Comprimo subject matter experts. Some of the pitfalls of providing support remotely for start-ups as well as lessons learned from their experiences was shared. In addition, by using newly developed tools, Comprimo was able to provide better support to the operating companies without requiring on-site presence. The new tools enable operating companies to better train their operators for normal and upset conditions of their sulphur recovery units and provide an on-line continuous support system in which plant operation can be optimised in real time for better on-line reliability and lower emissions.
Amine systems
Chemical cleaning in gas treating systems
Ritesh Gulabani of Dow provided guidance on chemical cleaning in gas treating systems. The most widely used processes to sweeten natural gas, refinery gases, syngas, LPG and biogas use amines such as MEA, DEA and MDEA to absorb H2 S and CO2 from sour gas streams. The removal of undesired deposits from the system during turnarounds is of paramount importance to ensure reliable and efficient operation until the next scheduled shutdown. Consequently, chemical cleaning at the start-up should be considered as an integral part of the best practices for any gas treating system.
Importance of lean amine quality
Muhammad R. Tariq of Saudi Aramco presented their experiences of H2 S breakthrough into the sweet gas from the acid gas removal unit of a gas plant, resulting in a gas that could not meet the treated gas H2 S spec of 4 ppmv. Amine quality is a major factor to achieve treated gas spec. The gas plant team found that the issue started when the plant started to process different feed gas. The problem was correctly identified in a short, systematic and effective investigation that combined field measurements and simulations with good analysis. It was discovered that the H2 S concentration in feed gas was higher compared than the unit design, the lean amine circulation and concentration were lower than the required and the amine solution was contaminated with degradation products like DEA, MEA and TEG which impacted CO2 slippage and increased reboiler and overhead condenser duties. The issue was subsequently successfully fixed by increasing the amine circulation rate to control the H2 S content in the treated gas, controlling the rich amine loading, controlling the amine concentration per design 50 wt-% to improve the acid pickup rate, adjusting he steam rate to the stripper column to achieve the required lean loading, and using the bleed and feed method to minimise the amine degradation contaminants to <2 wt-%.
Best practices
Use of refinery fuel gas in SRUs
Sulfur Recovery Engineering (SRE) has extensive experience and knowledge in the analysis of process streams including refinery fuel gas (RFG). Dharmeshkumar Patel and Ahmad Nyeazi of Sulfur Recovery Engineering Inc. examined the pros and cons of using refinery fuel gas in the SRU process. RFG is an important utility for refinery facilities. Its composition depends on various factors (crude type, unit operations etc.) but is typically made up of C1-C4 hydrocarbons, hydrogen sulphide, hydrogen, and other light components. Most facilities attempt to recover the hydrogen from this stream using various technologies. The majority of the hydrogen sulphide is also removed. When used in sulphur recovery units, RFG has its benefits and some drawbacks. RFG composition tends to fluctuate which can have costly consequences, e.g. soot in SRU converters. Knowing the composition is crucial to ensure problems are not amplified in the SRUs.
Recommended responses to TGU upsets
Breakthrough of SO2 or elemental sulphur from a sulphur plant tail gas unit (TGU) reactor into the downstream quench tower and amine system can be catastrophic. It can result in plugging, corrosion, emissions violations, and unplanned shutdowns, with high costs associated with equipment repair and production downtime. Although the chemistry behind how SO2 or sulphur breakthrough occurs is relatively well known, the operational indicators associated with a breakthrough event and the proper responses are less well known and are often ignored or misunderstood. Jan Kiebert and Gerald Bohme of Sulphur Experts detailed the causes of SO2 and sulphur breakthrough events, all of the operational indicators associated with a breakthrough event, and the recommended responses in order to quickly correct the operation and to minimize the impact on the tail gas unit equipment and operation.
Incinerator design
Acid gas incinerator replacement
Noor Azalea of Petronas shared the lessons learned when new requirements for CO emissions were introduced which led to a thorough analysis of the existing acid gas incinerator (AGI) and its fitness for service. The diagnosis led to the discovery of major defects which may have arisen from incomplete combustion, flame impingement, high convection section temperature and carbon, monoxide and unburned hydrocarbon from the stack.
Despite multiple test runs and modifications, the AGI failed to meet even its intended original design and the decision was made to replace it. The root causes of the AGI underperformance from many aspects of design, operations, control and maintenance have been incorporated into the new design of the AGI.
Ceramic solutions for the SRU reaction furnace and incinerator
Uday N. Parekh of Blasch Precision Ceramics showcased innovative ceramic solutions for improving the operational performance and the structural reliability of the SRU reaction furnace and the incinerator. Conventional checkerwall or choke rings in the reaction furnace often do not provide the desired structural integrity, resulting in compromised performance and shorter run lengths. Also, achieving the desired CO destruction in the incinerator often poses a challenge. Operational data was shared to demonstrate how superior materials and design can be used to address these problems.