Sulphur 400 May-Jun 2022
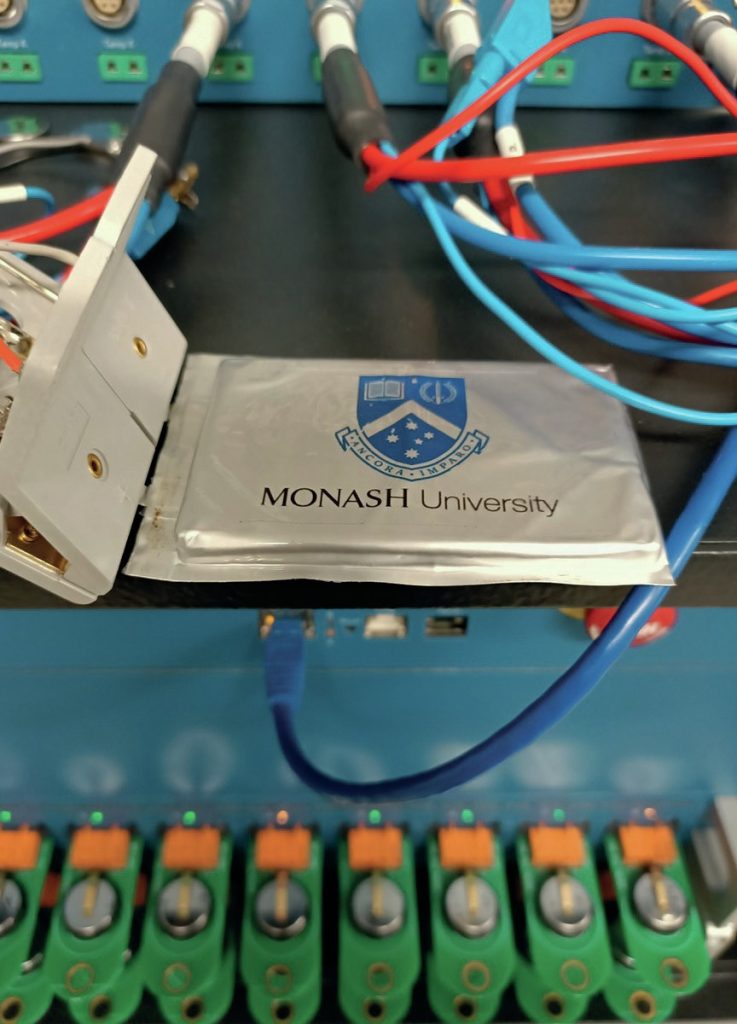
31 May 2022
Sulphur Industry News Roundup
Sulphur Industry News
AUSTRALIA
Breakthrough in lithium-sulphur battery technology
Researchers from Australia’s Monash University say that they have created a new generation of lithium-sulphur batteries which could provide a cheaper, cleaner and faster-charging energy storage solution that outlasts lithium-ion alternatives and is rechargeable hundreds of times without failing. The team has creating a new interlayer which allows for exceptionally fast lithium transfer, as well as an improvement in the performance and lifetime of the batteries.
“The interlayer stops polysulphides, a chemical that forms inside this type of battery, from moving across the battery; polysulphides interfere with the anode and shorten the battery life,” said professor Matthew Hill, deputy head of the university’s Department of Chemical and Biological Engineering. “The new interlayer overcomes the slower charge and discharge rates of previous generation lithium-sulphur batteries. It means the battery can be charged and discharged hundreds of times without failing.”
Lithium-sulphur batteries already offer higher energy density and reduced costs compared to lithium ion batteries and can store 2-5 times more energy per kg, but previously the electrodes in lithium-sulphur batteries have deteriorated rapidly during the recharge process. Hill said the development could be a ‘gamechanger’ for lithium-sulphur batteries, which do not rely on metals like cobalt, nickel and manganese, which are critical minerals for lithium-ion batteries.
Separately, scientists in the United States have announced that they have developed a lithium-sulphur battery using a commercially available carbonate electrolyte which retained more than 80% of its initial capacity after 4,000 cycles. The group used a vapor deposition process, which unexpectedly produced a form of sulphur that did not react with the electrolyte, overcoming one of the key challenges for this battery chemistry.
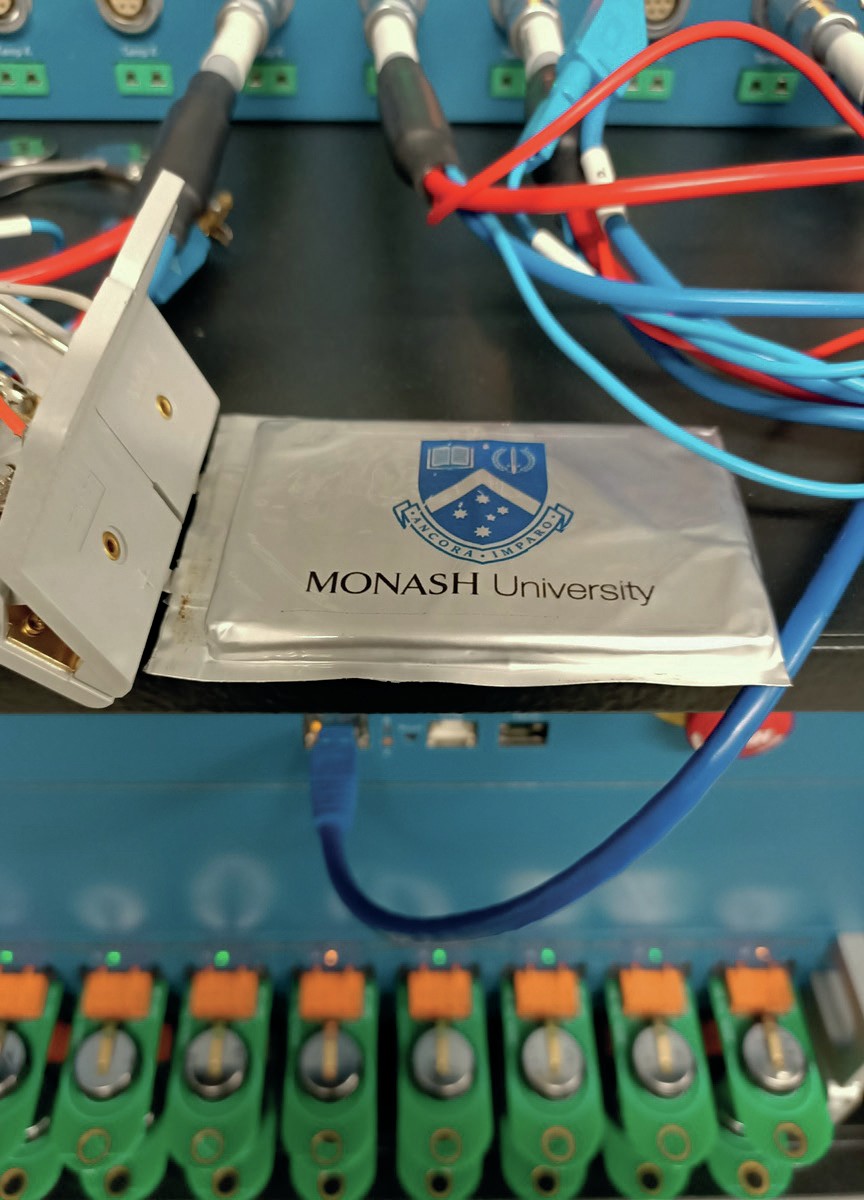
UNITED STATES
LyondellBasell to shut Houston refinery by 2024
LyondellBasell says that it will stop operations at its 268,000 bbl/d Houston refinery in Texas by 2024 unless it can find a buyer for the facility. The company has been trying to sell the complex since last year, but is also said to be evaluating other uses for the site as part of its goal to reach net zero emissions by 2050. LyondellBasell, which is based in the Netherlands and run from Houston, aims to produce 2 million t/a of recycled or renewable-based polymers by 2030.
“While this was a difficult decision, our exit of the refining business advances the company’s decarbonisation goals,” LyondellBasell interim chief executive officer Ken Lane said. “The site’s prime location gives us more options for advancing our future strategic objectives, including circularity.”
The refinery is designed to process heavy, high-sulphur crude grades, chiefly from Mexico – in 3Q 2021 it imported 5.6 million barrels of oil from Mexico. However, Mexico has declared its intention to halt crude oil exports in 2023, and US sanctions against Russian oil have also clouded the outlook for sour heavy crude supply in the US Gulf coast.
Sulphur fire on cargo barge
A sulphur fire broke out on the Alafia sulphur barge and its attendant tug the Kelly at the port of Tampa on April 22nd. The vessel, owned by Savage Marine Services, was evacuated and the fire brought under control. There were no reported injuries among the crew and minor injuries to one firefighter. The boat was docked at the International Ship Repair and Marine Services for repairs and the fire was reportedly started by welding sparks igniting sulphur dust in the cargo hold.
IRAN
New sulphur forming plants
Two new facilities have been inaugurated at the Shahid Soleimani Sulphur Complex at Sarakhs in the northeastern Khorasan Razavi province of Iran, close to the Turkmenistan border, to convert raw crushed lump sulphur into more valuable forms, according to Iranian Oil Ministry’s news agency Shana. The facilities, built at a cost of $15 million, join two existing sulphur forming facilities at the site. One of the new plants will produce 72,000 t/a of sulphur bentonite for fertilizer use, and the other 150,000 t/a of granulated sulphur.
CANADA
Refuel Energy to use Topsoe technology at renewable fuel facility
Refuel Energy Inc has announced plans for the construction of a 3,000 bbl/d renewable fuel plant in southern Ontario. The proposed project, called Refuel YYZ, would supply the aviation and terrestrial fuel needs of the greater Toronto area, home to 6 million Canadians, while lowering the CO2 emissions for the end users by up to 80%. The plant would utilize Haldor Topsoe’s proprietary HydroFlex™ and H2bridge™ technologies for the production of renewable diesel and sustainable aviation fuel (SAF). Planned feedstocks include a mix of waste fats, oils and greases, such as regionally-sourced used cooking oil, animal fats and non-edible crop oils.
“We are very pleased that Refuel has selected our technologies for this state of the art, standalone renewable diesel and SAF facility. Our market-leading technologies are complementary and together they will produce some of the lowest carbon intensity renewable fuels in the world,” said Henrik Rasmussen, managing director, The Americas at Topsoe.
Refuel expects to make a final investment decision in 2023. If approved, production at the new facility would start in 2025.
UNITED ARAB EMIRATES
Bids submitted for Fujairah LNG project
Front end engineering and design (FEED) bits have reportedly been submitted for the Abu Dhabi National Oil Company’s (ADNOC’s) 10 million t/a Fujairah liquefied natural gas export terminal. Middle East Economic Digest reports that the bidders include KBR, Fluor and McDermott International of the US and French engineering company Technip Energies. Japan’s JGC and Chiyoda are said to no be longer involved. The FEED study will be carried out later this year. The LNG project includes two 5 million t/a liquefaction trains, processing facilities and utilities, as well as an export jetty, and possibly a 2 bcf/d pipeline from Habshan to Fujairah. The project will be owned and operated by ADNOC LNG, in which ADNOC holds the controlling 70% stake, with other holdings from Mitsui, BP and Total.
The company is separately progressing with a revised FEED study on the Hail & Ghasha sour gas project to supply gas for the LNG and other projects. The UAE is aiming to reduce its dependence on gas imports from Qatar via the Dolphin pipeline and expand its existing 6 million t/a of LNG exports. Technip is said to be revising designs for Hail and Ghasha to reduce estimated $15-20 billion construction costs, aiming to competed FEED work by the end of 2022. The development will now be phased to spread costs: first gas will come online in 2025 as originally planned but will then be ramped up in stages to the 1.5bn ft³/d target plateau by end-decade.
MALAYSIA
Samsung tipped to win sour gas EPC contract
South Korea’s Samsung Engineering looks set to be awarded the engineering, procurement and construction contract for Malaysia’s new Rosmari-Marjoram onshore gas plant on Sarawak. The plant, to be built and operated by Petronas, will process highly sour gas from offshore sour gas fields operated by Royal Dutch Shell (75%), Brunei Energy Exploration and Petroliam Nasional. The project is expected to start commercial production in 2025 and is forecast to peak in 2028 at approximately 16,500 bbl/d of crude oil and condensate and 495 million scf/d of natural gas.
It is one of several sour gas developments in Sarawak, where gas fields include high levels of carbon dioxide (between 20-70%). However some fields, including PTTEP’s Lang Lebah off Sarawak, also have high H2 S concentrations. Petronas is targeting reinjection as a way of dealing with the acidic component of the gas feed, but is pitching this as ‘carbon capture and storage’; gas produced at Lang Lebah will flow to a platform on the Golok field and from there to a new 900 million scf/d onshore gas processing plant at Kasa-wari, where the H2 S and other contaminants will be removed before the CO2 rich stream is sent back offshore via pipeline for injection into the designated storage site. Honeywell UOP is providing modular natural gas processing technology to the project, including MemGuard and Separex technologies and adsorbents, to remove contaminants such as carbon dioxide, hydrogen sulphide, and mercury.
RUSSIA
Halliburton says contracts will end in May
Halliburton says that sanctions imposed in the wake of Russia’s invasion of Ukraine will require it to wind down several of its ongoing contracts in Russia by May 15th. On March 18th the company said that it was ending all future work in Russia, and that it would “prioritise safety and reliability” as it wound down existing operations in the country. Halliburton says that the total net book value of its assets in Russia is about $340 million and warned that sanctions could cause the company to take a charge related to those assets. Trade restrictions are blocking Halliburton’s ability to export, re-export and move some equipment within Russia, according to company filings.
The US government has tightened export controls on oil and gas equipment, including drilling rigs, hydraulic fracturing software, high-pressure pumps and drill pipes, and refinery technology including gas separation, hydrogen generation and sulphur recovery. Other major contractors including Schlumberger and Baker Hughes have agreed to halt future work in Russia.