Sulphur 403 Nov-Dec 2022
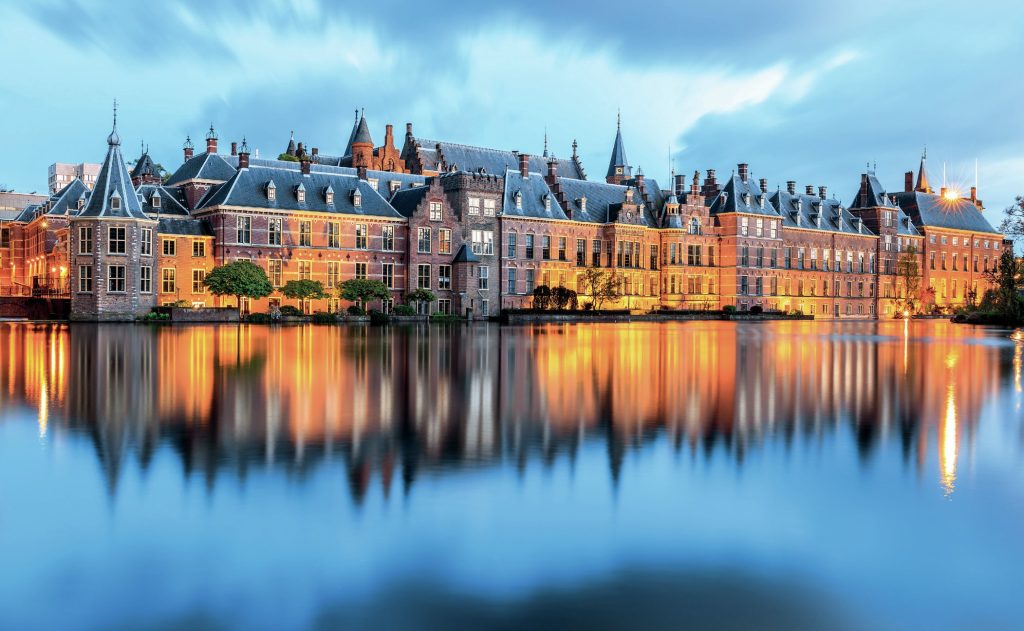
30 November 2022
Sulphur + Sulphuric Acid 2022
CONFERENCE REPORT
Sulphur + Sulphuric Acid 2022
A report on CRU’s annual Sulphur + Sulphuric Acid conference, which returned to being face to face meeting at the end of October 2022.
It was with some sense of relief, I think, that delegates gathered in the Hague in the Netherlands at the end of October for the CRU Sulphur and Sulphuric Acid conference, as it was the first time in three years that the conference had been held as a face to face even, following the covid pandemic. Though numbers were down slightly on pre-pandemic times, the combination of the conference with the REFCOM refining meeting drew 470 visitors.
The format was slightly changed from previous runs, with the first morning devoted to a series of technical showcases. These were short, 15 minute presentations on specific products or services by the likes of Kimre, MECS-Elessent, Blasch, Begg Cousland and Steuler, and appeared to be popular with the delegates.
Market papers
On Monday afternoon the conference proper began. CRU’s Peter Harrison started as is traditional with the sulphur market paper. He reflected how sulphur prices had slumped in Q3 2022 from 14-year highs of $500/t to 14-year lows of $80/t. Demand had rebounded and supply was tight in the first half of 2021. Moving into the second half of the year, exports were weak, with overrunning turnarounds in the Middle East and issues at Astrakhan in Russia. Of course, for the first half of 2022 the war in Ukraine had dominated markets, leading to prices climbing sharply as consumers became concerned where to source sulphur. The recent collapse in prices by up to 90% has been driven by demand destruction and reduced demand in China caused by quotas for phosphate exports. However, after an overcorrection, prices have bounced back towards $150/t. The outlook for the full year is a small contraction in supply and a larger one in demand due to lower fertilizer applications, but new refinery capacity and sour gas plants will keep supply growing, while a rebound in fertilizers and new metals demand will dive growth in demand out to 2027.
Regionally, Europe is likely to swing to being a net importer by 2026 as domestic supply falters with the closure of the Grossenknetten gas plant and some refinery closures, and by 20227 the continent could be importing 200,000 t/a of sulphur. In North America, there has been a short term supply jump to 7.9 million t/a in the US due to extra sulphur from refineries, but output will fall from next year. Canada will see a return to oil sands supply growth, but Alberta sour gas production continues to see an overall steady decline. Consumption will see an uptick over the forecast period due to new metallurgical use, and overall net US imports may rise to more than 2 million t/a by 2027. CIS supply continues to find its way to the international market, with Turkmenistan expected to see supply growth. In the Middle East, there is more sulphur from Kuwait’s refineries, the Shah 2 project in Abu Dhabi, and incremental supply from Iran and Qatar. Indian imports may grow over the next five years in spite of some new refinery sulphur due to new sulphur burning acid plants at phosphate producers. In China refining is also boosting domestic supply, with import requirements dropping by 2.3 million t/a out to 2027. Finally, in southeast Asia, Indonesian nickel production is driving demand growth, as new HPAL plants appear to have started up more efficiently than previous plants elsewhere in the world.
Trade continues to shift, though, with the war showing up how exposed some markets are to disruption – the share of Senegal’s imports coming from the CIS is more than 70%, and for Brazil the figure is close to 50%, with Europe at 34%. Over the next five years, Morocco will see more import demand growth to feed phosphate production, with most supply growth coming from the Middle East. As far as the price outlook goes, the market is in notional oversupply, and will be into 2023, but thereafter demand growth will overtake supply growth, leading to a small overall deficit by 2025. Continuing lower prices are forecast to Q4 2023, rising after that.
Erisa Pasco of CRU followed with the sulphuric acid market presentation. Acid prices have followed sulphur prices this year, but have been less volatile. The first half of 2021 was a period of tighter supply from smelter acid, and prices reached $250/t, but this year Asian prices have weakened and in 3Q 2022 prices have fallen as Chinese acid volumes entered the market and demand weakened, dragging f.o.b. prices to $50/t as a fall in DAP, sulphur and nitrogen prices have all weakened price support for sulphuric acid. Local demand has been lower in China, pushing more acid onto international markets. Chinese exports were 2.9 million tonnes for January to August 2022, compared to 2.8 million tonnes for the whole of 2021; an 88% rise for the first eight months of the year. However, Chinese demand is expected to recover from 2023, and exports will gradually fall, dropping to an estimated 1.5 million t/a by 2026. Chile will see import demand fall as copper projects fail to replace demand losses from closures. Chilean demand will drop from 8.1 million t/a in 2021 to below 7.0 million t/a in 2027. Meanwhile Indian sulphuric acid capacity growth will continue. Coromandel, Iffco and PPL are all building or considering new sulphur burning plants, and the new Hindustan Zinc smelter will start up next year. The Adani smelter project could also add another 3 million t/a of capacity from 2025. Even so, demand growth is expected to outpace new supply and import requirements will rise slightly. Morocco is also adding sulphur burning capacity, and its imports of acid are expected to fall. Europe has seen a supply drop this year from scheduled smelter maintenance but should see a return to normal next year. The outlook for the rest of 2022 is stable prices in the $50120/t range for f.o.b. and delivered acid respectively, with the Jiangsu burner breakeven cost expected to drive floor prices of $70-80/t in 2023.
The trio of market papers was completed by CRU’s Glen Kurokawa, who presented the phosphate outlook. DAP prices have risen recently faster than crop prices leading to less affordability for farmers. Phosphate demand is consequently expected to decline in 2022, with MAP/DAP demand down 9% year on year, comparable to the fall seen in 2008. Consumption will return as prices ease from their current high levels, however. Chinese phosphate exports, which represent around one third of the traded market for MAP and DAP, have been subdued due to restrictions and quotas to keep prices lower domestically. These will rise in 2023 but increases may be impeded by lingering export restrictions, rising production costs and competition from other countries. Morocco, which represents 15% of global phosphoric acid production, is seeing production and exports increase as OCP continues to expand phosphate production. However, in 2021-22 it raised prices, leading to lower exports despite its low costs. This may not be a sustainable strategy in the long term. US production has declined, and in spite of a recovery in 2023 will probably continue to see some declines in production, while Russian phosphate exports are expected to grow in spite of sanctions, as its main export destinations, India and Brazil, are not affected. European production is stable but dipped in 2022 due to high prices and disruption at Lifosa in Lithuania. India remains the biggest importer, though high prices have led to more domestic production and lower imports in 2021. Import subsidies have been raised this year and imports are expected to increase, but out to 2026 there will be increased domestic phosphoric acid production due to government policies to favour domestic production. India remains at the high end of the cost curve. Further declines in phosphate prices are expected next year as crop prices fall and there may be lingering demand destruction, with increased exports from China and Morocco.
“Indian sulphuric acid capacity growth will continue.”
The final paper in the commercial session was provided by John Bryant of The Sulphur Institute (TSI). He argued that sulphur as a business driven by supply chains, is at a crossroads. Pricing has been more volatile over the past 15 years since the financial crisis than at any time in the history of the industry, and it is facing factors such as covid, shutdowns, an economic slowdown, labour shortfalls, the green energy transition, the Ukraine conflict and its knock-on effects, inflation, higher fuel and freight costs etc. The potential impacts of these are longer supply chains, higher costs and longer delivery times; unplanned delays, cost inflation, offtake and delivery problems, and more besides. However, what is not changing is that sulphur production continues to be involuntary, but remains of high value to many sectors, with a distinction between solid and liquid transport, the molten assets tending to be dedicated and highly utilised. Exacerbated volatility adds market costs to ownership, while supply chain interruptions will increase and threaten operating rates. Industry responses to this could take the form of new attitudes about owning the full supply chain, additions to storage capacity, new transforming assets for forming and melting, new transport assets, and sharpening and improving commercial terms for greater price transparency.
Sulphur technology
With demand for hydrogen projected to reach 290 million t/a by 2050, the sulphur technology strand of the conference began with two papers on recovery of hydrogen and carbon dioxide from Claus plants. Marcus Weber of Fluor showed that Fluor’s oxygen enriched COPE process could produce a gas stream richer in H2 and CO2 at a lower capital cost and footprint than standard post-combustion carbon capture, if oxygen levels were greater than 95%. Moderate levels of steam injection can boost hydrogen output. Gerritt Bloemendal of Worley Comprimo offered a similar scheme with >95% oxygen enrichment and again with hydrogen and CO2 recovery post tail gas treatment and pre-incinerator. A cold flash for CO2 recovery was recommended, but a chemical solvent option could be optimised.
Matt Coady of Delta Controls presented a new camera system, ProSpection, for SRU monitoring – there is a fuller article elsewhere in this issue. Moving further downstream, Diego Scilla of Siirtec Nigi showcased his company’s DegaSN degassing system, capable of reducing dissolved H2 S in sulphur down to less than 10 ppm. Liquid sulphur is fed to a sprayer before being mixed with low pressure steam and a slipstream of stripping air, the latter is bubbled through mass transfer elements to achieve intimate contact between the liquid and gas phases.
Refineries must deal with a variety of feeds these days, and Marco van Son of Comprimo looked at the impact of biological feeds on sulphur recovery. In a co-processing situation, existing amine and SRUs can process the revised sour products, but the sour water stripper may need debottlenecking and there is the potential for increased emissions. However, in a new grassroots biorefinery sulphur throughput may be only 1% of conventional diesel production and other sulphur recovery options may be appropriate.
David Savage of Matrix described options for above ground liquid sulphur storage as an alternative to sulphur pits, including pitfalls to be avoided in terms of tank heating and insulation and fire safety and suppression systems.
Mason Lee of Aecometric introduced at the theory and practice of reaction furnace design, and ASRL’s Chris Lavery looed at reaction kinetics for COS and CS2 conversion on Claus catalysts; enefficieny conversion of which can lead to loss of sulphur recovery efficiency. Alumina and titania catalysts tended to show lower end of run conversion in experimental tests.
Wednesday morning saw a Middle East Sulphur Conference (MESCon) round table discussion hosted by Angie Slavens on the subject of corrosion considerations for sulphur plant operators. At the end of the second day, Worley Comprimo also ran a workshop covering sulphur recovery techniques with a recovery above 96.5% highlighting differences in capex, opex and CO2 footprint, as well as showcasing Insight, a digital tool for plant data analysis.
Emissions monitoring and control
On the final day, David Inward of SICK AG began with a look at emission reporting from SRUs; the limits for SO2 and – increasingly – other releases such as NOx and CO/ CO2 , and the techniques used to measure them. A field trial at a European refinery in 2020 proved the suitability of a hot, wet extractive infra-red analysis system to measure tail gas emissions.
Jeff Weinfield of Optimized Gas Treating also looked at SO2 emissions, this time a slip from a TGTU caused by hydrogenation reactor poisoning. The plant in question was reporting cloudy quench water and thiosulphates in the amine section, but could not detect SO2 in the feed gas – possibly indicating an intermittent problem. Jeff used a modified SulphurPro model which indicated that a small slip of excess Claus air led to a 100ppm+ SO2 slip exceeding the quench ammonia buffer capacity and passing on into the amine system.
Finally, Neils Seijsner of Fluor ran through a variety of processes for removing SO2 and SO3 from flue gas, highlighting their respective strengths and weaknesses.
SRU case studies
A number of case studies detailed operator experiences with sulphur plants. ADNOC Sour Gas presented two papers, the first dealing with optimisation of catalyst loading in a sulphur recovery unit and a tail gas treatment unit respectively. The SRU loading was able to minimise titania loading to 30% without compromising performance, while the TGTU eliminator reactor internals and used a low density catalyst to reduce pressure drop and minimise catalyst volume. ADNOC also presented a report on refractory and shell damage to the incinerator downstream of the TGTU due to condensation in the absorber overhead line.
Adel Najar of Saudi Aramco’s Ras Tanura refinery detailed issues with sulphur fume emissions from a sulphur pit. Investigation found a steam ejector valve was giving a wrong open/closed indication leading to sulphur pit steam coils leaking inside the pit.
Sulphuric acid technology
The acid technology strand began with two presentations on digitalisation. Topsoe reviewed their ClearView digital services suite, highlighting its ‘real world’ use and effects at a Topsoe wet sulphuric acid (WSA) plant at Anglo-American Platinum in South Africa, while Susanna Voges of Voovio Technologies extolled the virtues of operator training using ‘digital twin’ technology.
Two catalyst papers followed, beginning with BASF, who highlighted their new X3D catalyst shape, produced using 3D printing to generate more complex geometries, for a 66% lower pressure drop at the same activity level and slightly higher conversion level. A case study installed in a third catalyst bed at a sulphonation plant showed a 75% decrease in pressure drop across the catalyst bed and conversion increase form 97.3% to 99%. Topsoe presented their VK-38 acid catalyst, with modified support and optimised melt formulation to give increased steam generation and acid production.
Clark Solutions introduced their SafeHR and SafeHX acid cooling systems, which avoid any potential for acid-water contact by using an inert fluid circuit as an intermediary. SafeHX is a recent improvement on the original system, with no intermediate pump and fewer valves for easier maintenance.
Simon Puels of SensoTech looked at the monitoring of acid and oleum concentrations in real time using LiquiSonic ultrasonic sensors, to an accuracy of 0.030.05%, maintenance free, and CG Thermal and Wilk Graphite presented Extracid, an acid concentration/dewatering system based on a heat exchanger which can recover up to 70% of input energy.
Greener production
Sulphuric acid production is already a zero carbon source of power, but opportunities exist at all phases of a plant’s development to improve its environmental performance, said Rene Dijkstra of Chemetics, including plant location, choice of technology, plant design and plant operation and maintenance. Colin Shore of Elessent added to this with a look at heat recovery and energy optimisation in an acid plant, and potentially upgrading heat to low pressure steam and LP steam to HP steam.
Operating experience
Several papers covered acid plant operating experience. Frans Kodeda of Metso Outotec presented a case study of the engineering and delivery of an Edmeston SX absorption circuit for BASF, wjhile Randal Sarrazin of NORAM described the replacement of a converter at Simplot’s Rock Springs acid plant in Wyoming – a significant undertaking! And in a joint paper, UBE and Sulphurnet explained a case study involving the extension ofoperational lifetime of a converter which had been experiencing problems with dust.
On the subject of practical modifications to plants, Hector Gonzales of Industrias Basicas de Caldas in Colombia described how new waste water legislation had forced a rethink of how their acid plant dealt with sulphonation. They had built a return for exhaust gas from sulphonation to the acid plant, converting more than 80% of the SO2 to SO3 and managed to generate additional acid and reduce water consumption. Meanwhile, Georgi Deganov of KCM in Bulgaria explained how a new batch process lead smelter at the site, generating variable quantities of SO2 , had been integrated into the existing acid plant flowsheet.
Hydrogen safety
The issue of hydrogen formation in acid plants is a topic that is assuming ever-greater prominence in the industry. Rick Davis, Hannes Storch of Metso Outotec, Jurgens Hanekom of Elessent and Rene Dijkstra of Chemetics presented findings from the International Hydrogen Safety Working Group. It is important to quickly acknowledge when acid concentrations are out of range, keep blowers running and examine the potential for venting at high points in the plant where hydrogen can collect. Stagnant space should be minimised, especially at side gas outlets. Alloy towers seem to show greater potential for corrosion and hydrogen formation. Early detection is vital with conductivity and pH analysers on water returns. The good news is that there have been fewer incidents since 2019 and more open and transparent reporting. German plant operators have published a set of guidelines, although at present they are only available in German – an English version is planned.