Sulphur 405 Mar-Apr 2023
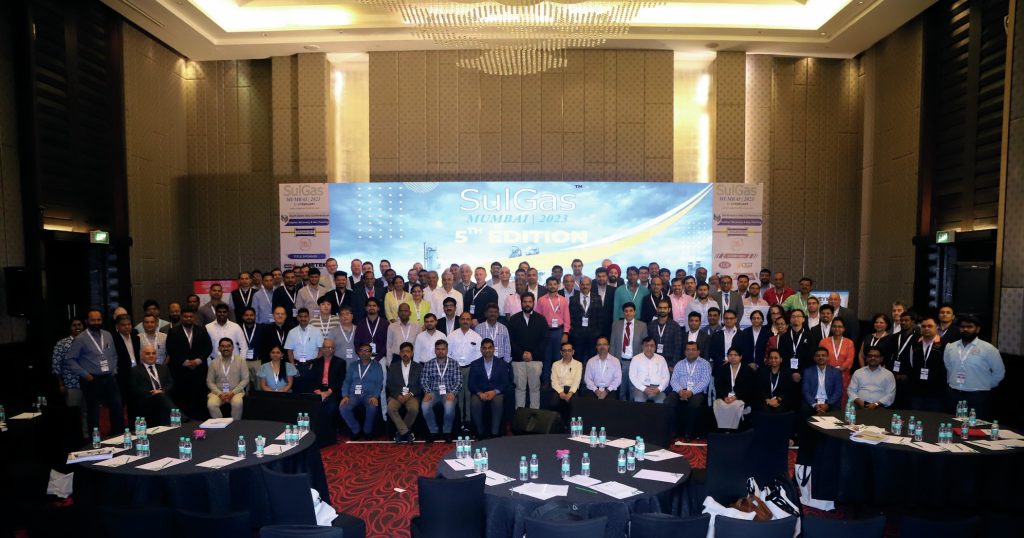
31 March 2023
SulGas Mumbai 2023
CONFERENCE REPORT
SulGas Mumbai 2023
SulGas, South Asia’s sulphur recovery and gas treating conference, returned to a live event in 2023, providing participants with a platform to interact with experts in the field, share best practices and troubleshooting tips with fellow refiners and discuss advanced technologies and operating procedures with technology providers, vendors and licensors.
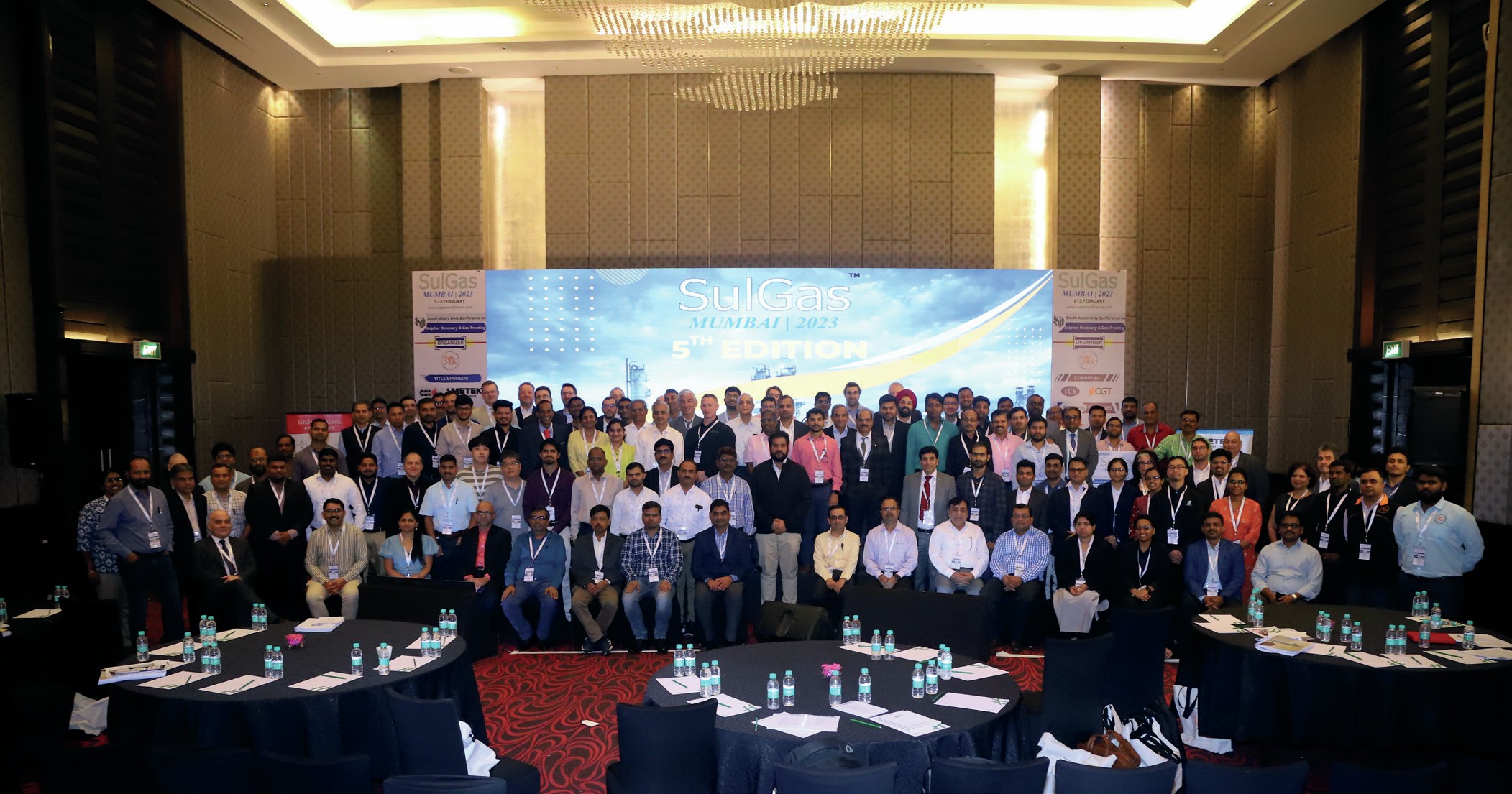
Three Ten Initiative Technologies LLP organised the 5th edition of SulGas from 1-3 February 2023 at the Hotel Holiday Inn Mumbai International Airport, Mumbai, bringing together public sector oil companies, private refiners, petrochemical, chemical and fertilizer plants, licensors, engineering companies, solvent and column equipment manufacturers, and control and instrumentation companies.
SulGas Mumbai 2023 provided a three-day interactive technical programme and exhibition, attracting over 155 attendees from over 68 companies representing all major areas of sulphur handling and gas processing.
The conference agenda was split over three days comprising expert forums, ten technical sessions and daily roundtables, as well as dedicated time to explore the exhibition.
The opening session on Wednesday 1 February started off with an expert forum on instrumentation basics for sulphur recovery units and tail gas units in which Jochen Geiger of Ametek Process Instruments reviewed and discussed the use of modern process analysers in SRUs and tail gas treating units, with detailed focus on how a feed gas analyser benefits the overall plant performance of an SRU and understanding process upset using installed analysers.
SRU instrumentation and control
The first technical session continued the theme of SRU instrumentation and control. David Inward of Sick discussed enhanced monitoring requirements from SRUs, providing detailed insights for a recent extended field trial at an oil refinery which applied a multi-component hot extractive infra-red analyser to meet reporting requirements both for conventional emission limit values as well as mass emissions.
Nirmalya Nandi of Bharat Petroleum Corporation shared experiences of how a problem of sticking tail gas treating unit (TGTU) feed valves was solved through in-house modifications, resulting in improved reliability and availability of TGTU feed and incinerator control elements.
Jochen Geiger returned to the podium to discuss oxygen enrichment and its impact on the control of sulphur recovery units.
Changing SRU feeds
The next session focused on the design modifications required to SRUs when processing different feeds. Debopam Chaudhuri of Fluor discussed the design modifications required for Claus plants which co-process significant SO2 (e.g. SO2 -rich refinery flue gases) along with the normal feed gas cocktail of H2 S and NH3 . While small amounts of SO2 in the Claus feed gas have a favourable impact on the overall hydraulic design of the unit, at higher concentrations of SO2 the positive impact of reduction of air demand tends to be overshadowed by the quenching effect on the Claus reaction, reducing the furnace temperatures below allowable operating limits for proper NH3 destruction.
The production of renewable fuels by retrofitting existing refineries and their infrastructure is witnessing exponential growth and is changing the composition and flow rate of the feeds to the sulphur removal and recovery units, which will invariably require suitable modifications to meet overall sulphur recovery or emission specifications. Based on several case studies, Marco van Son of Worley Comprimo discussed the various options available to holistically review the sulphur block to determine the impact and mitigation of processing bio-feed.
Design and equipment advances in sour systems
Matt Thundiyil of Transcend Solutions presented a case study in which a refiner on the US Gulf Coast was forced to clean a heat exchanger in a sour water system every 3-6 months due to fouling. The problem was successfully solved by installing the TORSEP™ oil and solids removal system which removed the solid and hydrocarbon contamination from the sour water stripper units that were causing the problem.
Harnoor Kaur of Optimized Gas Treating demonstrated the importance of addressing the complex sour water chemistry using a true rate-based model such as ProTreat® to evaluate different SWS unit design configurations.
A novel approach for processing ammonia-rich sour gases and converting them to valuable products such as anhydrous NH3 or aqueous NH3 was the topic of Saptarshi Paul of EIL’s presentation. Demand for ammonia in India has been rising year on year. EIL’s patented technology (patent no. 350771) will not only help towards domestic ammonia demand but also reduce operational problems in the SRU as well as reducing NOx emissions.
Fibre and membrane-based contactors
In the next session the focus turned first to CO2 membrane advancements to reduce emissions and enable CCS which was presented by Tanzim Choudhury of SLB, followed by a presentation by Saurabh Agarwala of EIL & Evergreen Technologies on innovative hardware solutions for sulphur reduction in light hydrocarbons like naphtha or LPG which are often contaminated with acidic components such as H2 S, COS, CS2 , mercaptans, SO2 etc.
Energy transition
Rajiv Srinivasan of Shell India opened day two of the proceedings with an expert’s forum on gas processing technologies in the energy transition. Many organisations have set a target to become a net-zero emissions energy business by 2050. Some of the technologies at the forefront of the energy transition were discussed along with their impact.
CO2 capture
Chandrakant Joshi of Sulzer introduced the new Sulzer Mellapak™ CC packings for outstanding performance in absorption systems encountered in CO2 capture in large power plants, natural gas processing plants and the fertilizer industry.
Vijaya Durga Kakara of HPLC described the latest developments to HP-HiGAS’ compact carbon technology based on a rotating packed bed. A first of its kind commercial scale plant is operational at its Vsakh refinery for fuel gas treatment and a demonstration plant with a capacity of 24,000 t/a is being put up in HPCL Vizag refinery for capture of CO2 from a PSA feed slip stream.
SRU hardware improvements
Sean Matthew of Ametek/Controls Southeast shared experiences of the first commercial installation of the ICON™ sulphur degassing system, as well as considerations for future installations, and the benefits of ICON™ .
Roelof ten Hooven of Duiker Combustion Engineers discussed several refinery applications of its SCO technology for utilising stoichiometry-controlled oxidation to handle ammonia waste streams. Dedicated ammonia incineration offers an attractive alternative to conventional processing of SWSAG in the SRU/TGTU and allows for complete combustion of ammonia without the need for flue gas after treatment, due to low NOx formation.
Brian Visioli or Porocel explained how operators of tail gas treating units can now use a catalyst which has improved sustainability without sacrificing performance or quality.
Protecting the integrity of your SRU
The afternoon of day 2 was dedicated to the analysis, monitoring and protection of the front end of SRUs. Bob Poteet presented a revolutionary method of temperature monitoring for Claus units which provides an easy way to monitor the condition of the brick lining of the thermal reactor by using a special continuous thermocouple system that reads only the highest reading anywhere along the sheath.
Mason Lee of Aecometric Corporation reported on thermoacoustic modal analysis for a large sulphur reaction furnace. In a study, the acoustic natural mode of the reaction furnace under operating conditions was analysed through numerical simulation and then used to diagnose whether the vibration frequency of the furnace body in field operation is close to acoustic natural modes, which can then be used to analyse the causes of furnace vibration.
Domenica Misale shone a spotlight on tubesheet protection systems and the key design and operating considerations for the SRU waste heat boiler (WHB), raising the awareness of its importance for reliability and to prevent WHB failures.
Nasser Abukhdeir of Continuum Engineering presented the results of a study on simulation-based analysis of vapour distribution and liquid recirculation in kettle-type waste heat boilers. The findings could enable the enhancement of existing WHBs through retrofits and the design of new units with significantly improved performance and reliability.
Troubleshooting
Amine solution foaming problems have been studied and reported extensively, however, direct correlations about the root causes of foaming have not been established. Ben Spooner of Amine Experts described six different foaming related cases and provided systematic approaches for foaming troubleshooting as well as a series of measures for foam minimisation to ensure foam does not take place in the future.
Anand Govindarajan of Three Ten Initiative Technologies discussed the use of the simulation tool ProTreat® and how it is meant to be used in the context of troubleshooting amine systems, and the technically right way to interpret the results.
The focus then moved on to troubleshooting heavy TEG losses from a gas dehydration unit which was presented by Sivaraj N of SLB.
Optimising hardware and retrofits of treating units
Mohd Firdaus Sabturani of Petronas shared the results of an investigation into the root case of repeated failures of column trays and Schoepentoeter inlet devices in amine regenerator columns in the AGRU and highlighted the critical link between the design of column internals and their vibration characteristics. Design improvements to consider in order to increase the natural frequency of the column internals include shortening the length of panels, increasing the panel thickness and utilising fixed valve trays.
Wai choon Liong of BASF reported on a successful amine swap case study in which OASE yellow technology was successfully used to optimise an existing amine scrubber unit based on MEA.
Lessons learned – SRU operations
The final session on day three of the conference focused on lessons learned in SRU operations.
Dharmeshkumar Patel of Sulphur Recovery Engineering used case studies to highlight common problems seen in the SRU and TGTU and stressed the importance of regular performance checks e.g. using a combination of GC analysis, simulation with specialised programs, combined with evaluation of DCS date to mitigate problems and optimise the performance of SRU and TGTU units.
Harpreet Singh & Radhe Syam of IOCL concluded the session by sharing lessons learned during the commissioning of a new 225 t/d sulphur recovery unit at IOCL, Panipat during the height of the Covid -19 pandemic.
The sixth edition of the SulGas conference will take place in early February 2024.