Fertilizer International 514 May-Jun 2023
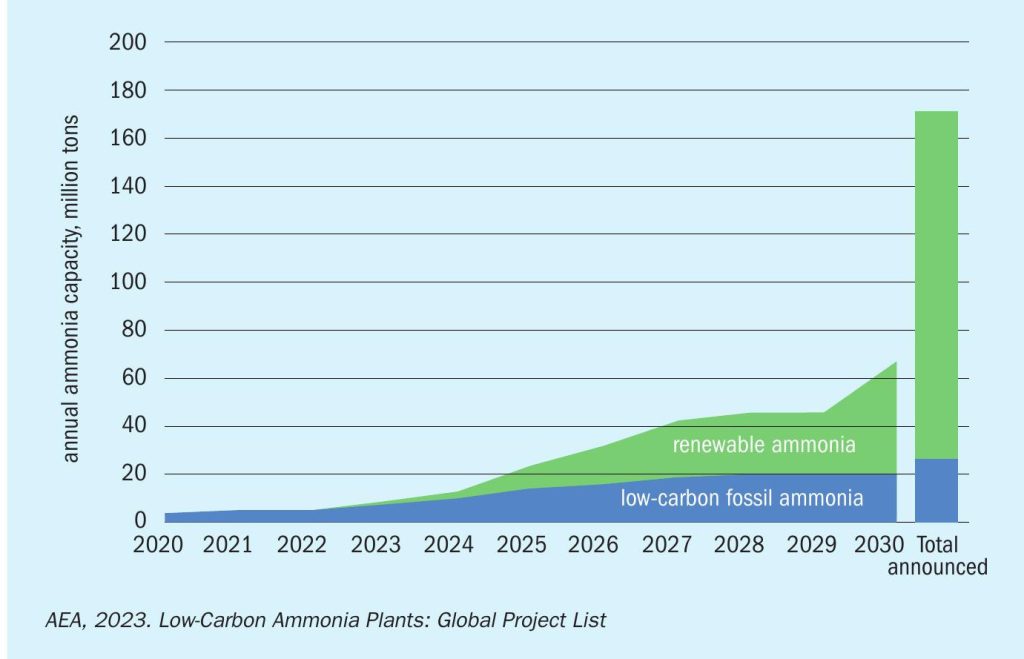
31 May 2023
Clean ammonia projects and technologies
SUSTAINABILITY
Clean ammonia projects and technologies
New methods for low-carbon ammonia production are emerging, while project activity is also rising rapidly.
AMMONIA ENERGY ASSOCIATION
Scaling-up low-carbon ammonia production
A lot of low-carbon ammonia plants have been announced in recent years – so many, in fact, that you’ve probably lost count.
The more than 100 projects announced so far have a combined capacity of 172 million tonnes for low-carbon ammonia. That’s equal to 95 percent of today’s ammonia demand of around 180 million tonnes.
While some of these plants are already operational, most are still in the feasibility and pre-FEED (front-end engineering design) stages. One simple, key factor will determine how many of these projects succeed: demand. To de-risk project financing and support offtake agreements, clear demand signals are therefore required from both regulators and customers alike.
A global project list
The Ammonia Energy Association (AEA) is an industry body that promotes the responsible use of ammonia in a sustainable energy economy. Our mission encompasses the decarbonisation of ammonia production on the supply side, as well as the adoption of ammonia in energy markets on the demand side. The AEA’s membership includes more than 220 corporations from around the globe, representing the full value chain across multiple sectors.
More than 100 low-carbon ammonia plants are either operating today or have been announced and are in the project pipeline to be built in coming years. If every single announced project eventually enters operation, the combined capacity of these plants would be enough to produce more than 172 million tonnes of low-carbon ammonia each year (Figure 1).
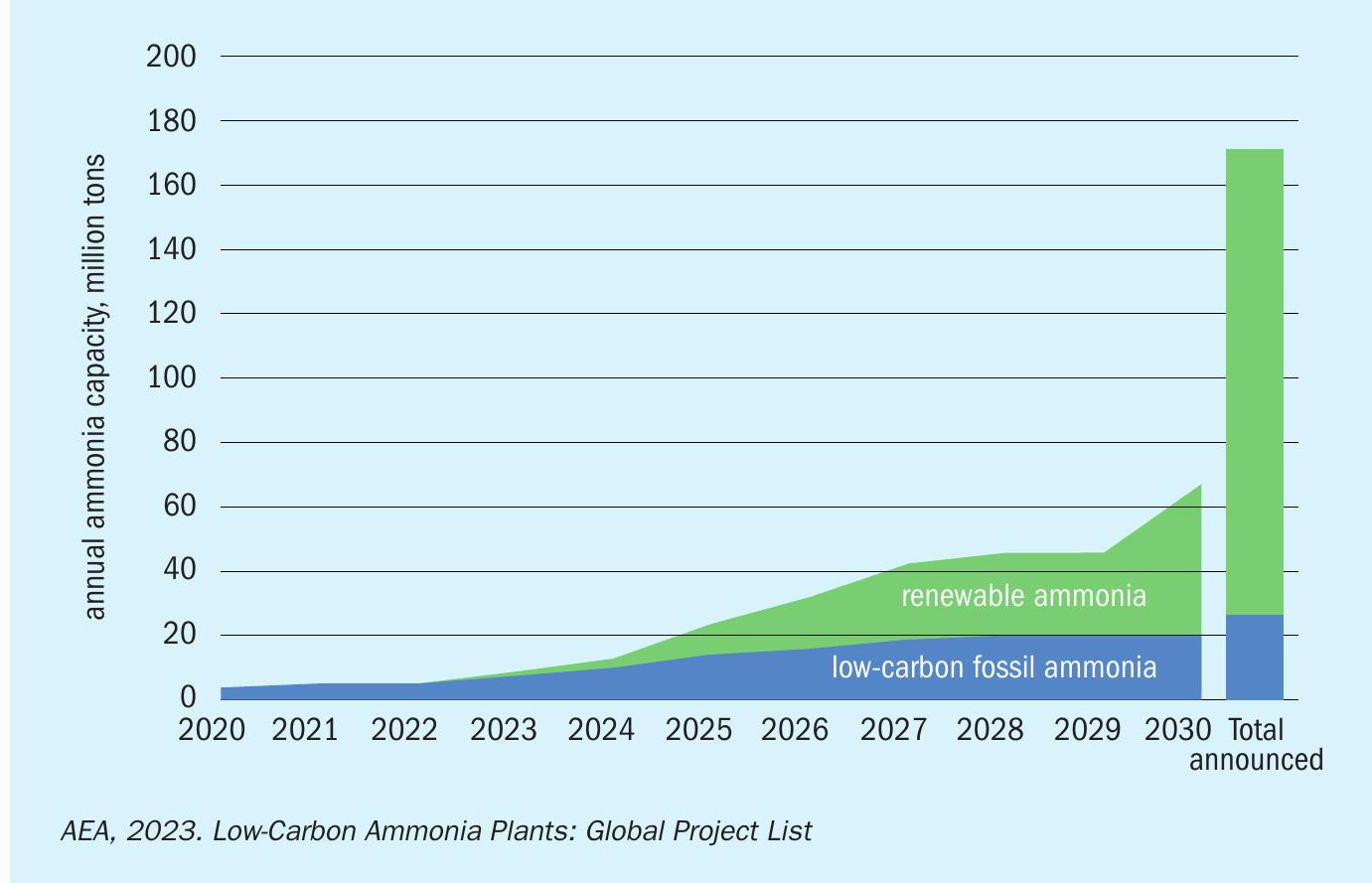
The AEA has been tracking these projects since the first wind-to-ammonia pilot plant began operating in 2013. Now, for the first time, we are publishing a report in May this year containing the complete list of all low-carbon ammonia projects that are operational or have been announced, based on publicly available data.
This list includes relevant information about each low-carbon ammonia plant – the location, start-up year, company, capacity, feedstock, and technology – taken from a more detailed market intelligence database that is only available to members of the AEA.
The report also provides an analysis and assessment of the project list. This highlights observed trends in geography, timing, technology, and the capacity of low-carbon ammonia plants – all of which show significant shifts from existing market dynamics.
As part of this analysis, the list of plants has been divided into two categories: fossil-based and renewable. The renewable category primarily includes ammonia plants based on water electrolysis powered by renewable energy, although some projects also propose to use bio-based feedstocks. These are commonly termed ‘green’ ammonia plants.
The fossil-based category primarily includes fossil fuel ammonia plants incorporating carbon capture and storage (CCS) or utilisation (CCU). These are commonly termed ‘blue’ ammonia plants. The fossil-based category also includes plants based on methane pyrolysis or those that consume by-product hydrogen from other processes. Also included in this category are ammonia projects that propose to compensate for carbon emissions via the purchase of forestry offsets instead of through direct emissions mitigation measures. All these production pathways are summarised in Figure 2.
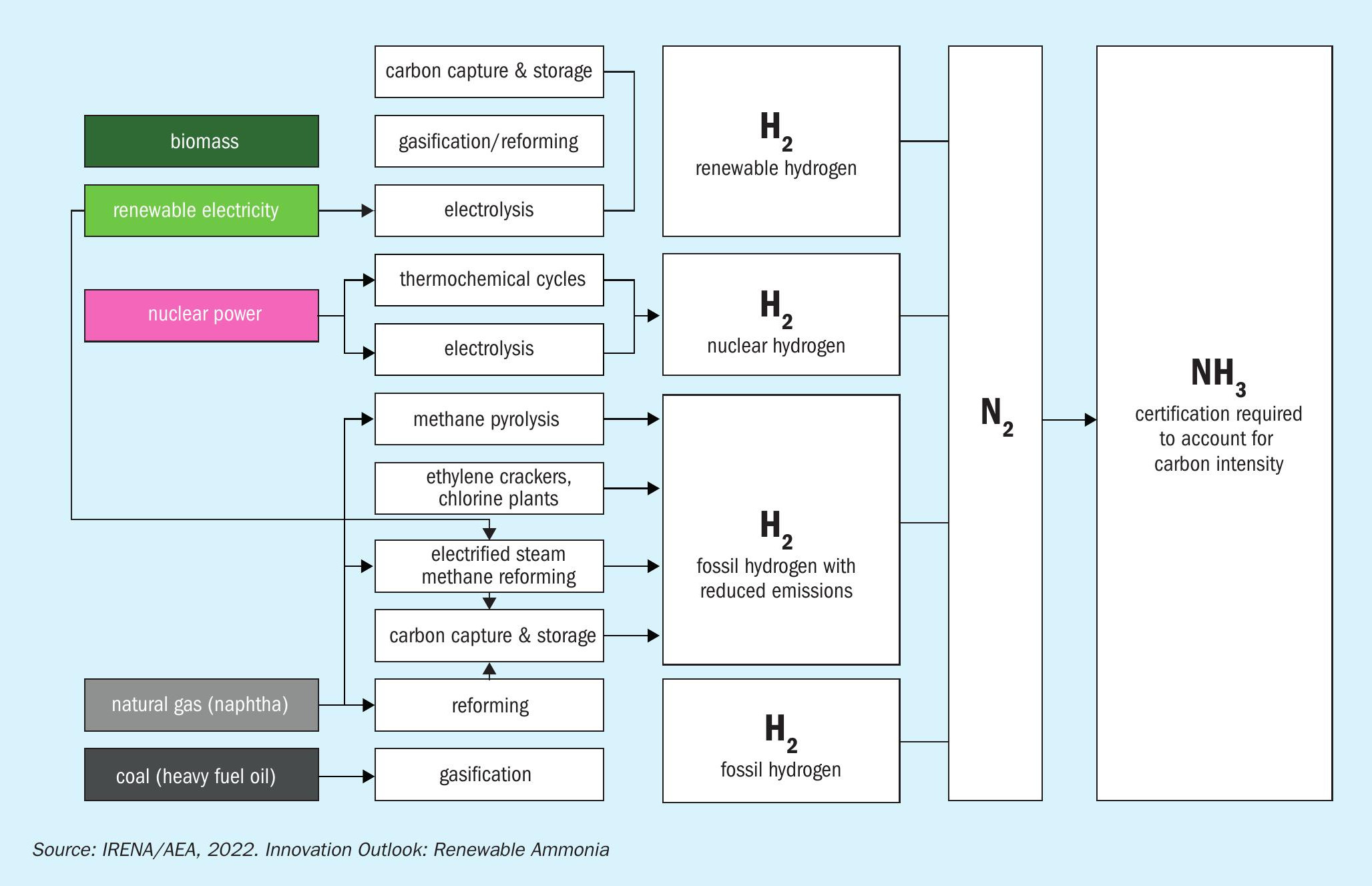
It is important to note that the two categories – fossil-based or renewable – do not necessarily indicate the carbon intensity of ammonia production, as certification (i.e., measurement of the carbon footprint) of the ammonia generated is required for that. Our report chooses to analyse these two categories separately because we have observed that separate trends and drivers apply to each – resulting in distinctly different technologies, cost curves, region-specific regulatory regimes, resource availability, and long-term scalability etc.
What is low-carbon ammonia?
Currently, there is no available global definition of ‘low-carbon’ ammonia, although various regions and organisations have defined emission thresholds, renewability criteria or other sustainability metrics.
The AEA’s list is therefore technology neutral, being inclusive of all announced projects that appear to have potential for reducing the carbon intensity of ammonia production. Moreover, this list includes decarbonisation pathways that might deliver useful emission reductions (e.g., 10-25 percent cuts) even though these would fail to meet any commonly held threshold for low-carbon products (often defined as >60 percent reduction).
Hybrid ammonia plants, where decarbonisation technologies are partially installed at an existing ammonia plant, create additional complexity. That’s because it’s not always clear exactly what proportion of the plant’s capacity will be low-carbon. We have therefore made a best estimate where such information is not publicly available.
Each of the projects listed could well produce ammonia with a different carbon intensity. Indeed, a single ammonia plant might produce batches of ammonia with different carbon intensities over its lifetime, depending on the month, day, or hour – even, perhaps, according to the market it intends to supply.
What is clear, however, is that clear and credible certification of the carbon intensity (and other relevant sustainability attributes) of ammonia will be necessary in future to enable markets and regions to specify what products are (or are not) acceptable. Recognising this, the AEA is developing a global ammonia certification scheme, which we intend to pilot in 2024.
Is this enough ammonia?
The existing and announced low-carbon ammonia plants would produce a lot of ammonia. 172 million tonnes per annum of ammonia is equivalent to 75 percent of today’s global installed ammonia capacity (228 million t/a) (Figure 3), or 95 percent in terms of today’s total global demand for ammonia (180 million t/a). However, many of the projects included in the collective 172 million t/a capacity total have not yet specified their start-up date.
Nevertheless, the 68 million t/a of low-carbon ammonia announced to start-up by 2030 is more than sufficient for supplying near-term markets. These include low-carbon fertilizers, explosives, or industrial feedstocks, as well as nascent markets like maritime fuel and power generation, and the use of ammonia as a carrier for transporting hydrogen.
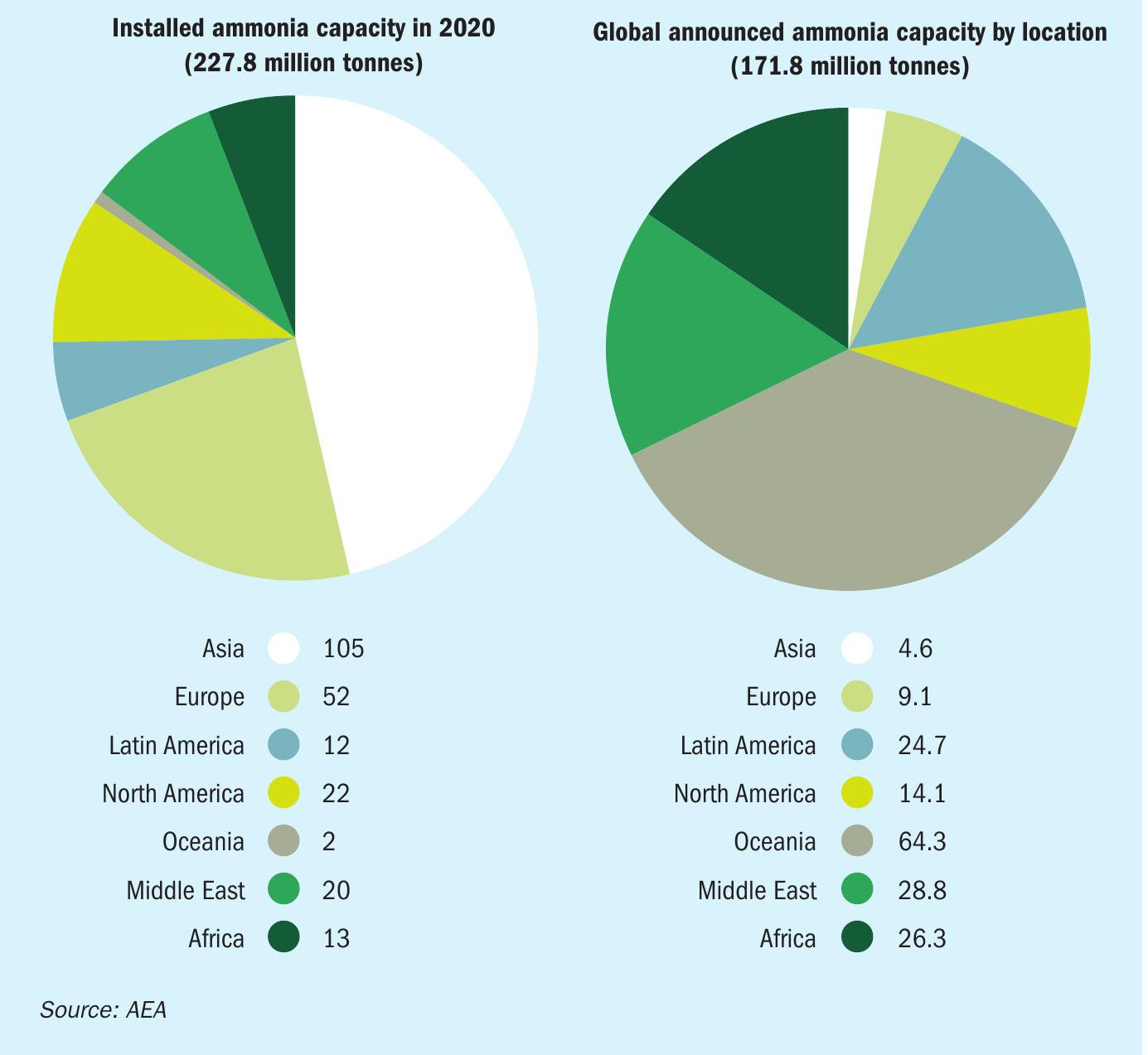
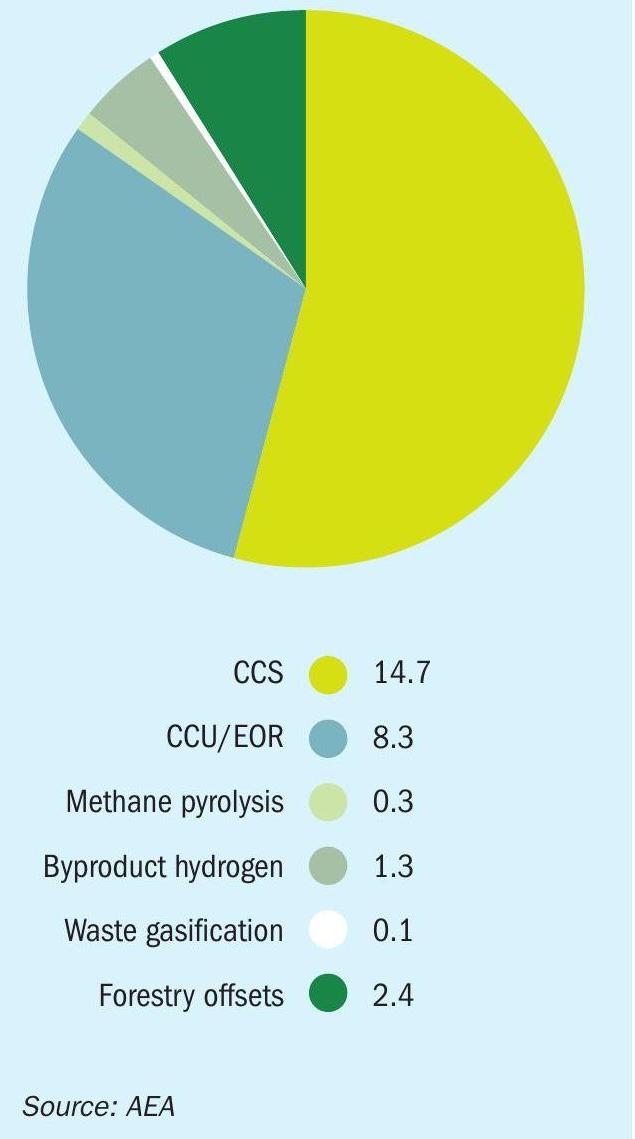
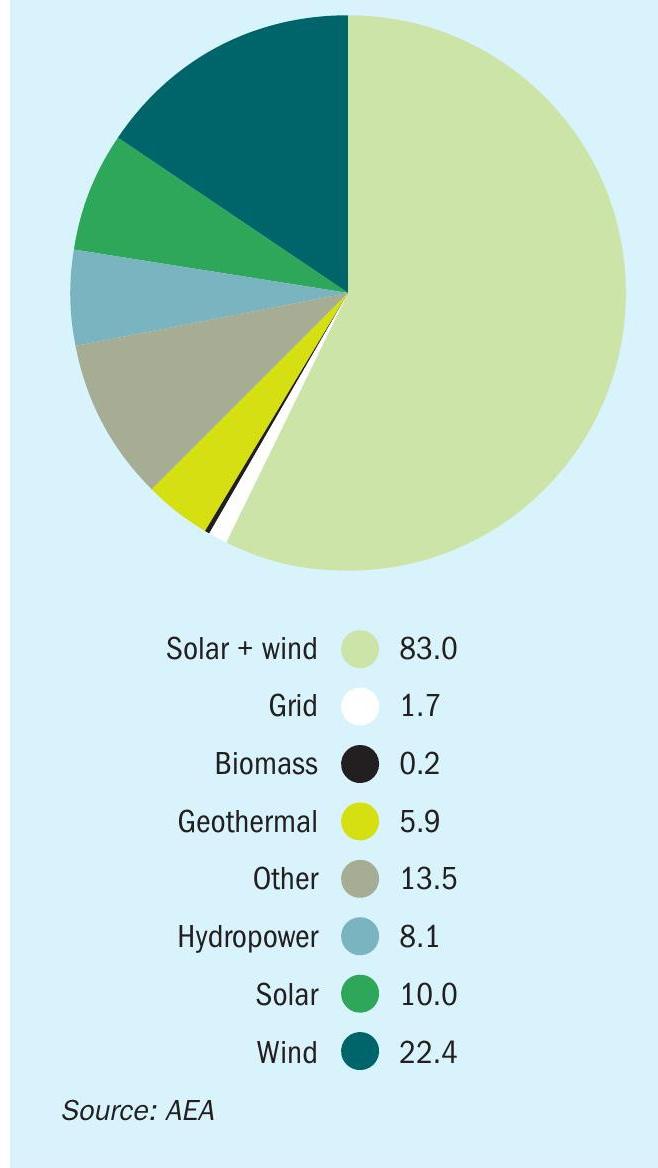
In the long-term, however, we’ll need many more low-carbon ammonia plants than have been announced so far: by 2050, in a 1.5 degrees aligned world, the global market for low-carbon ammonia could range from 540-1,140 million tonnes, according to the Ammonia Sector Transition Strategy published by the Mission Possible Partnership in late 2022. These volumes are divided between the following end-markets:
- Up to 110 million tonnes as a hydrogen carrier
- 35-105 million tonnes for power generation
- 210-250 million tonnes for fertilizer and existing industrial applications
- 295-670 million tonnes for shipping fuel.
The AEA’s project data confirm that supply is not a bottleneck preventing these markets from developing. Low-carbon ammonia production is, after all, a very mature technology – given that the first industrial-scale renewable ammonia plant started up in 1921!
Low-carbon ammonia supply can also expand at the speed required to meet demand. But, to enable these projects to reach financial close and begin construction, clear demand signals will be required, from regulators and customers, to support offtake agreements and de-risk project financing.
Will low-carbon ammonia be available where and when we need it?
If all this supply were to come online, it would represent a swift expansion, quadrupling between 2020 and 2030 the volume of ammonia shipped internationally each year. Many additional investments have been announced, not included in this project list, that would expand the necessary infrastructure for storage, shipping, conversion, and delivery of ammonia around the world.
It is reasonable to expect that most of the announced low-carbon ammonia projects are looking to ship their products internationally, because we can observe a significant shift in the location of announced low-carbon ammonia plants versus the current location of existing ammonia plants (Figure 3).
Currently installed ammonia capacity (227.8 million t/a) is heavily centred in Asia. Capacity in this region (105.0 million t/a) represents almost half of global ammonia capacity, with China and India as established major producers (Figure 3, left). Europe, including Russia, represents almost another quarter of global capacity (52.6 million t/a). Most of the ammonia capacity in this region is dedicated to fertilizer production.
By contrast, less than 10 percent of announced low-carbon ammonia capacity (171.8 million t/a) is located in either Asia (4.6 million t/a) or Europe (9.1 million t/a). Instead, most of the announced low-carbon ammonia capacity is situated in Oceania, primarily Australia. Many other projects are located in South America, particularly Chile, as well as in the Middle East and Africa (Figure 3, right).
Some of the low-carbon ammonia plants scheduled to be built out over the next decade are very, very large (e.g., 10 million t/a capacity), initially supplying but ultimately outgrowing any domestic markets for fertilizer.
Will low-carbon ammonia be renewable or fossil-based?
It is observable from the data that low-carbon fossil-based ammonia is already available at greater volumes than renewable ammonia. In 2020, the capacity of low-carbon fossil-based ammonia capacity exceeded four million t/a, although none of this was specifically marketed as low-carbon.
Fossil-based capacity also represents the majority of the low-carbon ammonia capacity announced to come online in the first part of this decade – a fivefold expansion of supply to more than 20 million tonnes. This trend makes sense since fossil-based capacity scales up more quickly than renewable capacity, as these projects are often:
- Existing assets
- Using mature technologies
- In areas with existing industrial infrastructure.
Fossil-based projects are therefore smaller and quicker to develop investments that are easier to de-risk than renewable projects – which, in contrast, are generally:
- New-builds
- With new technologies
- In new places.
Given that renewable ammonia was barely produced in 2020, the announced project pipeline represents an exponential scale-up of renewable ammonia supply that looks set to outpace fossil-based supply before 2030. Some 47 million tonnes of renewable ammonia capacity have been announced to come online by 2030, more than double the volume of low-carbon fossil-based ammonia over this period.
This trend also appears to continue over the long-term, as there is significantly (five times) more renewable ammonia under development than fossil-based ammonia. In total, 27.0 million tonnes of low-carbon fossil-based ammonia is under development today (Figure 4), versus 144.7 million tonnes of renewable ammonia capacity (Figure 5).
These differences may be explained by resource limits. Expansion of fossil-based low-carbon ammonia capacity, for example, is physically constrained by the availability of natural gas and suitable sites for CO2 sequestration. The physical constraints on the development of renewable ammonia projects, meanwhile, are primarily the availability of land and water providing high-quality renewable resources, and the manufacturing capacity for electrolysers. In the long-term, these differing constraints could allow renewable ammonia capacity to continue expanding faster than fossil-based ammonia capacity.
Many of the announced low-carbon ammonia projects will need a host of factors to be in place before they can reach financial close and begin construction. These include:
- Clear market signals and the long-term regulatory confidence needed to support offtake agreements
- Technology and manufacturing scale-up and deployment to push down costs
- The successful demonstration of new technologies and new markets
- Certification to verify the carbon intensity of ammonia products.
CASALE
Decarbonising ammonia production
The development of green and blue ammonia production processes is largely being driven by carbon dioxide reduction commitments and the introduction of carbon taxes.
Blue ammonia is recognised as the lower cost and more immediate option for large-scale clean ammonia production. The recent natural gas price surge, meanwhile, together with the greater availability of low-cost renewable energy sources, is placing green ammonia on the development fast track.
As well as the installation of new production capacity, the retrofitting of green and blue ammonia technologies, by allowing the cleaner operation of existing production plants, can also help ammonia producers meet corporate and legislative targets.
Casale’s strategy
Casale strategy for decarbonising ammonia production is based on three pillars:
- Moving towards zero carbon dioxide emissions by updating existing plants
- Designing new blue ammonia plants which capture and sequester carbon dioxide generated by conventional grey ammonia generation with natural gas
- Designing new green ammonia plants which avoid carbon dioxide emissions by using renewable energy and feedstocks.
Updating existing plants
Starting with the updating of existing production units, Casale can offer a customised approach based on process optimisation, improved equipment design and the integration of operating units.
The clean ammonia solutions developed by Casale are applicable to any ammonia production process, not just those based on its own proprietary technologies. Casale’s track record in the ammonia industry also means its approach to clean ammonia projects can draw on the combined knowledge and expertise gained from its worldwide plant reference list.
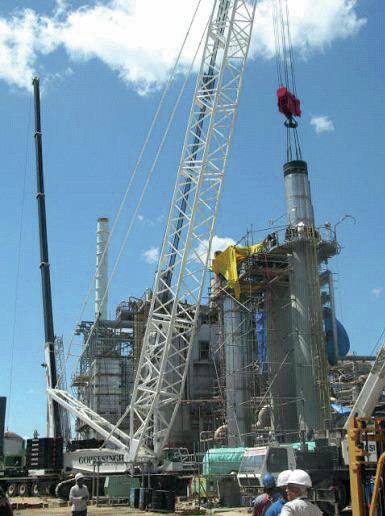
The motivation for producers to update and modify their ammonia plants to reduce carbon dioxide emissions is usually provided by company environmental targets and/or the need for compliance with carbon legislation (e.g., the EU emissions trading scheme) or to benefit from policy incentives such as the 2022 US Inflation Reduction Act.
Clean ammonia projects at existing production plants offer the following advantages:
- Increased plant capacity and energy savings
- An accurate forecast of the necessary investment costs – these being much lower that the plant’s original construction cost
- A typically short payback time for any plant modifications – usually less than three years
- Fast implementation – with plant modifications generally completed within two years.
Achievable CO2 emission reductions for these kind of projects range from 10-100 percent. An existing ammonia plant can be therefore turned from ‘grey’ to ‘blue’ and finally to ‘green’, as the following two project case studies show.
First case study: This describes an upgrade project at a long-established ammonia plant licenced by CF Braun. In this project, the reduction in carbon dioxide emissions was combined with a plant capacity increase.
The modifications to the plant were designed to increase the CO2 capture rate from 62-69 percent and raise plant capacity by seven percent.
To meet these targets, modifications to the most energy intensive sections of the plant were necessary, namely:
- The reforming section
- The synthesis loop with the Casale converter
- The CO2 removal section
- The steam system.
The integration of Casale’s proprietary and third party technologies was central to this revamp project. The payback period for the project was less than three years.
Quite remarkably, this upgrade was successfully accomplished on an ammonia plant that was more than 50 years old. Despite its age, the plant remained profitable because the existing process technology was still modern and already quite efficient.
Second case study: The next case study describes a project where the carbon dioxide emitted by an operational methanol plant was captured and utilised to produce urea and then more melamine (Figure 1). This project provides an excellent example of how an existing production plant can be modified for carbon capture and utilisation (CCU) via the integration of new production units.
In this project, the release of carbon dioxide to the atmosphere was minimised in two ways: by either storing the captured and sequestrated CO2 or fixing this inside a product (melamine).
Casale installed one of the world’s biggest carbon dioxide removal (CDR) units at this plant to capture about 400,000 tonnes of CO2 annually. Some 82,000 tonnes of this amount was then sequestrated within the melamine product.
In general, the approach developed by Casale for converting existing grey plants to blue ammonia production (Figure 1) can achieve a carbon capture rate of 95 percent or more. For operators, the advantages of this blue ammonia conversion scheme include the ability to:
- Carry on using their existing natural gas feedstock
- Combine carbon dioxide emissions reduction with a capacity increase and lower energy consumption
- Benefit from a rapid payback time.
Plants that are already operative can also benefit from so-called hybridisation projects. These integrate electrolyser units to generate a green hydrogen feed for the existing ammonia plant.
Hybridisation enables existing grey production plants to be partially or completely replaced by green ammonia, hydrogen or methanol production (Figure 2). Valuably, hybridisation projects can also increase capacity without increasing either natural gas consumption or carbon dioxide emissions. In this concept, investment costs and modifications to the existing asset are minimised, compared with the construction costs for a new plant of the same capacity.
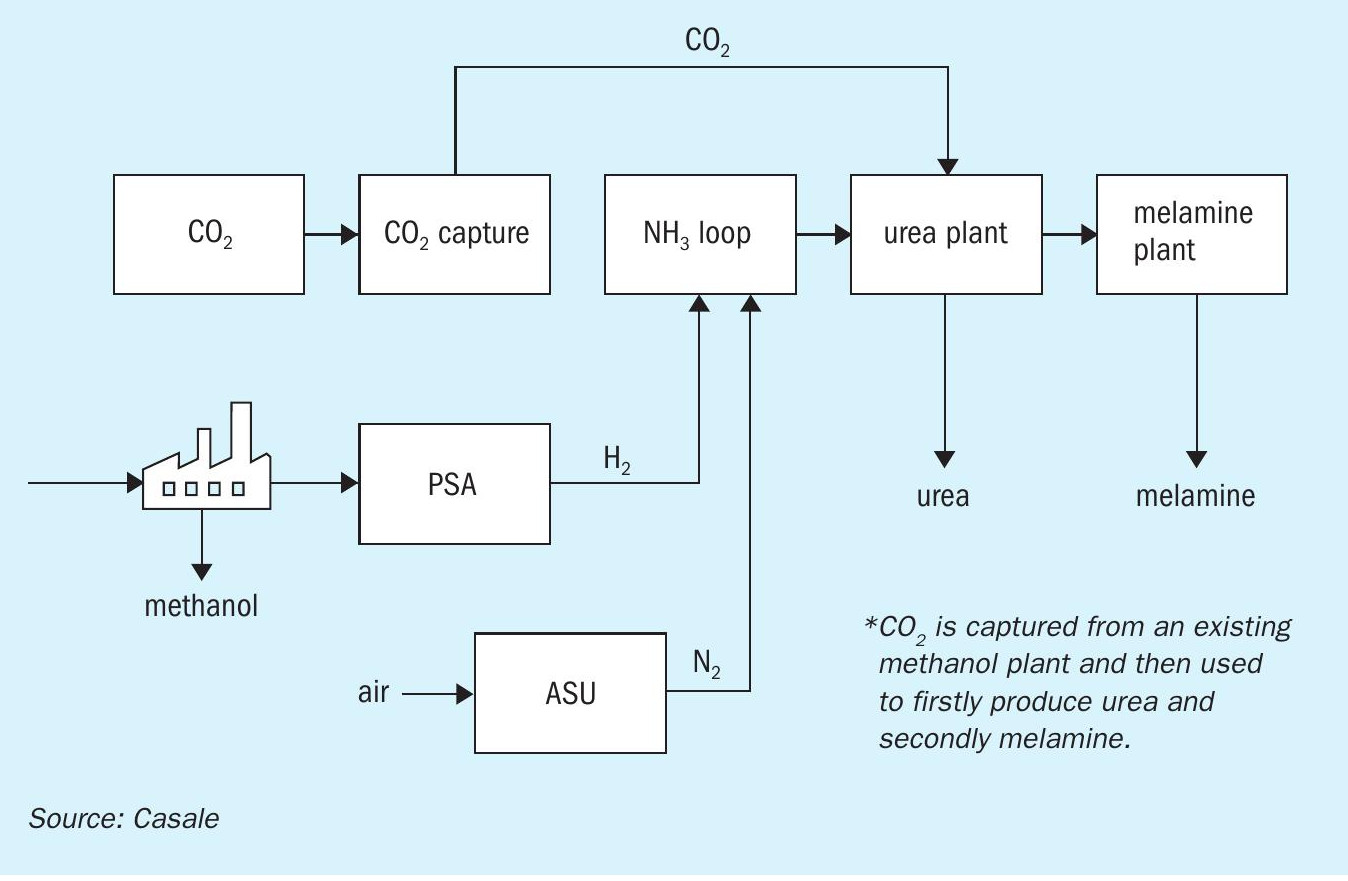
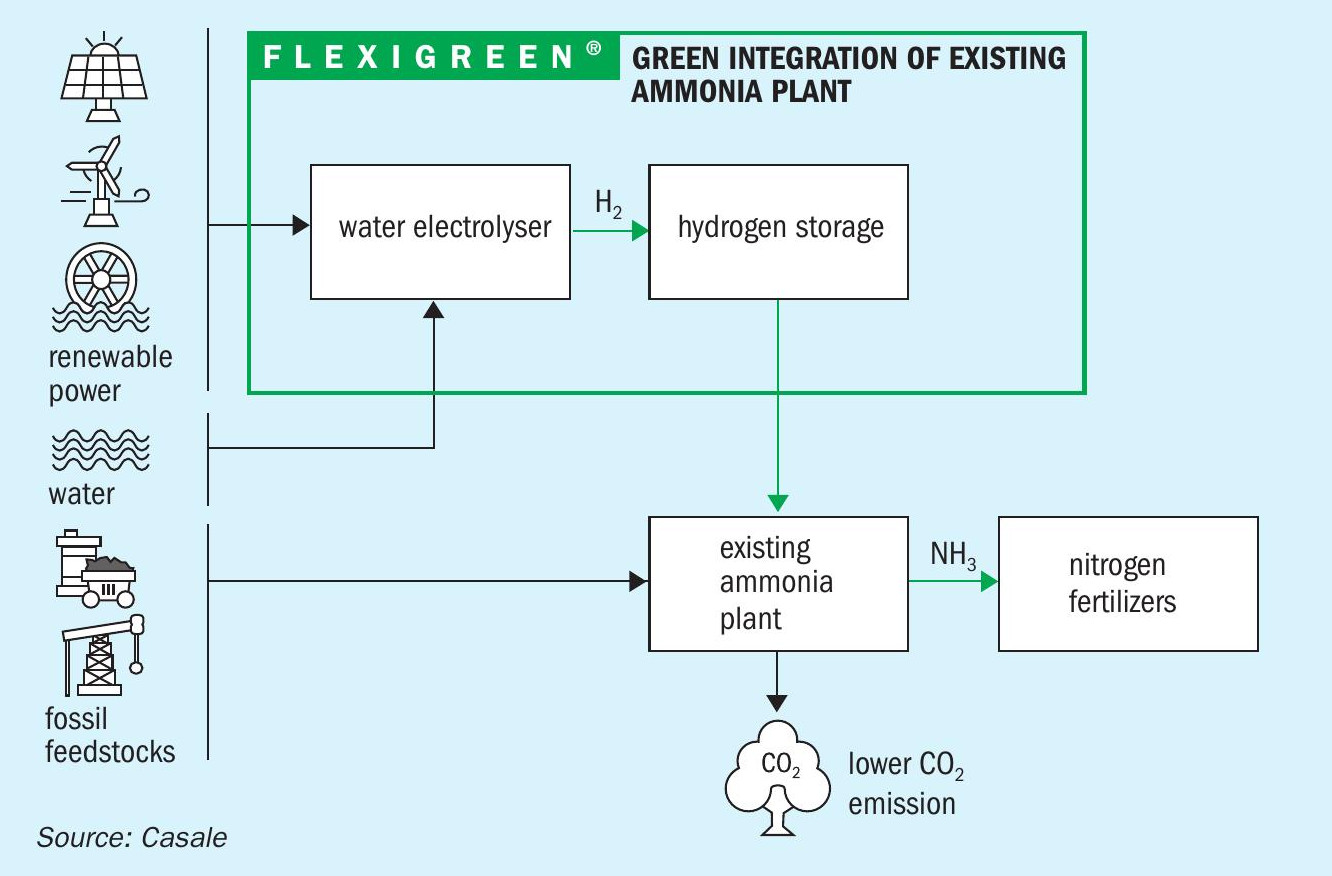
However, in hybrid plants, care and attention must be given to variations in the renewable power used to generate hydrogen. This is because fluctuations in the plant’s power supply – and therefore in the volumes of green hydrogen generated – could have a negative impact on the safe and reliable operation of equipment, as these are normally designed for steady-state operations. Fortunately, Casale has already developed patent-pending technologies designed to overcome this specific issue.
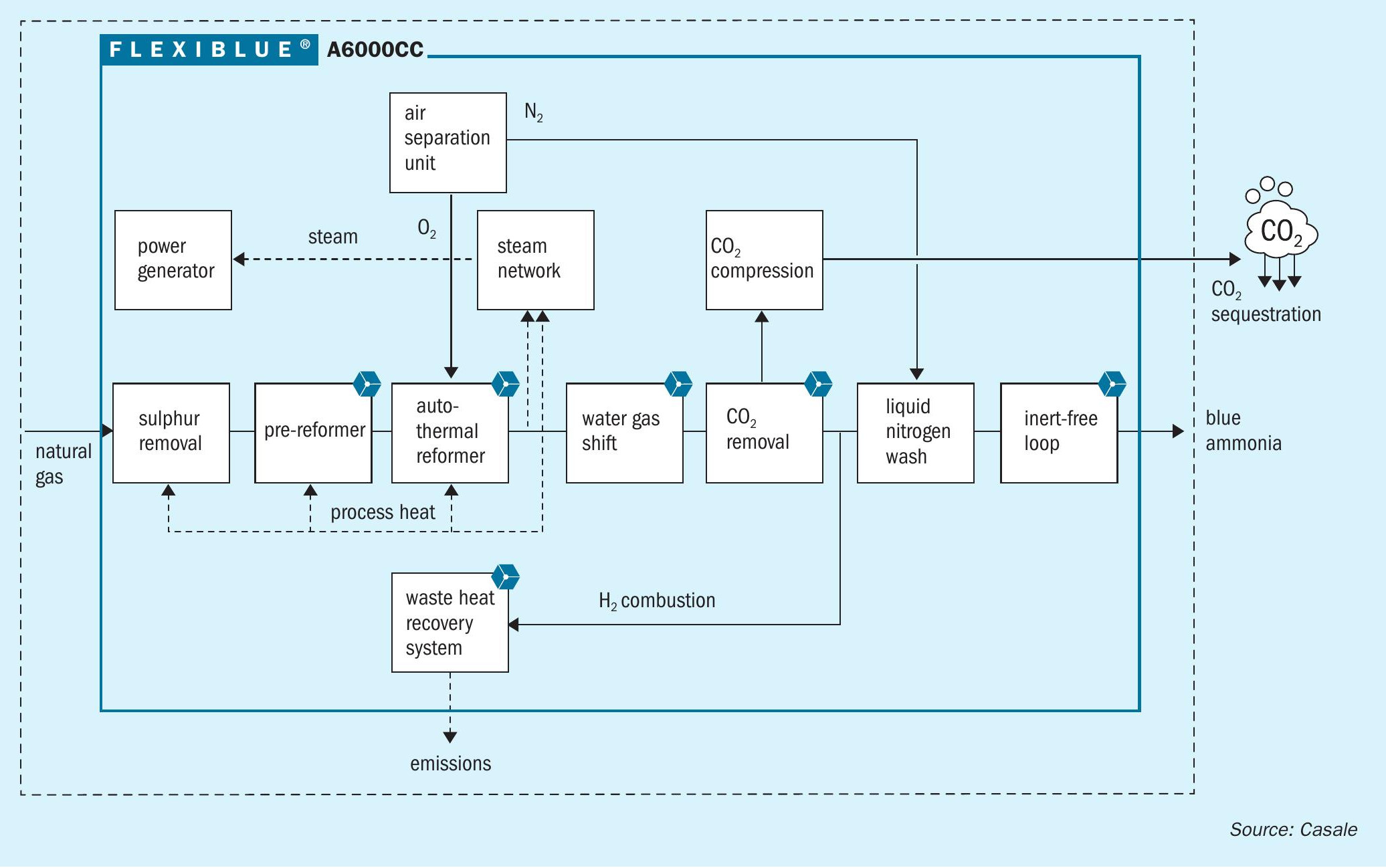
In one of Casale’s most challenging hybridisation projects, an existing grey ammonia production plant, licensed by Pritchard, was updated and converted to 100 percent green production. This complete hybridisation project, one of the most important globally, fully replaced the hydrogen generated at the plant’s front end with hydrogen generated by electrolysis.
The ability to minimise capital expenditure is one of the most attractive reasons for converting an existing grey production plant to green production. Project expenditure can be kept low because many of the existing units and sections can be reused. That includes the synthesis loop, the demi water preparation unit, and the CW system.
The main achievement of the Pritchard plant hybridisation project were:
- 100 percent reduction in carbon dioxide emissions
- This ended 700,000 tonnes of carbon dioxide emissions to the atmosphere annually
- An associated 30 percent ammonia production capacity increase, from 900 tonnes per day to 1,150 t/d.
New clean ammonia plants
New blue and green ammonia plant designs are also being developed, based on carbon capture and sequestration (CCS) and carbon-free production technologies, respectively. This is happening in parallel to the clean ammonia upgrades and conversions at operational plants described above.
The decarbonisation of industry, including ammonia production, will be necessary to meet the climate goals endorsed by 196 countries in the 2015 COP21 Paris Agreement. By 2030, the switch to net zero should become competitive for many sectors representing more than 70 percent of global emissions, according to the agreement. Currently, many new green and blue ammonia projects are being announced across globe, backed by public and private investor interest in these new opportunities.
Casale’s approach to – and main technologies for – blue and green production of hydrogen and ammonia are outlined below.
Blue ammonia plants
The main motivations for investing in new blue ammonia plants are:
- Their ability to drastically reduce carbon emissions while still keeping natural gas as a feedstock
- Avoiding the limitations associated with green ammonia production such as renewable energy availability and the need to incorporate costly electrolyser units.
The installation of a new Casale-designed blue ammonia unit provides additional advantages. In particular, it offers production at a very high capacity using technologies that are closely related to those already used at standard ammonia plants – and therefore have similar investment costs.
The carbon capture process developed by Casale to produce blue ammonia, known as A6000CC™ , has a single line capacity of up to 7,000 tonnes per day. The scheme converts a conventional ammonia plant into a blue plant by the addition of pre-combustion stage to sequester carbon at a capture rate of 95-99 percent (Figure 3).
Blue ammonia production using the A6000CC™ process (Figure 4) has the following features:
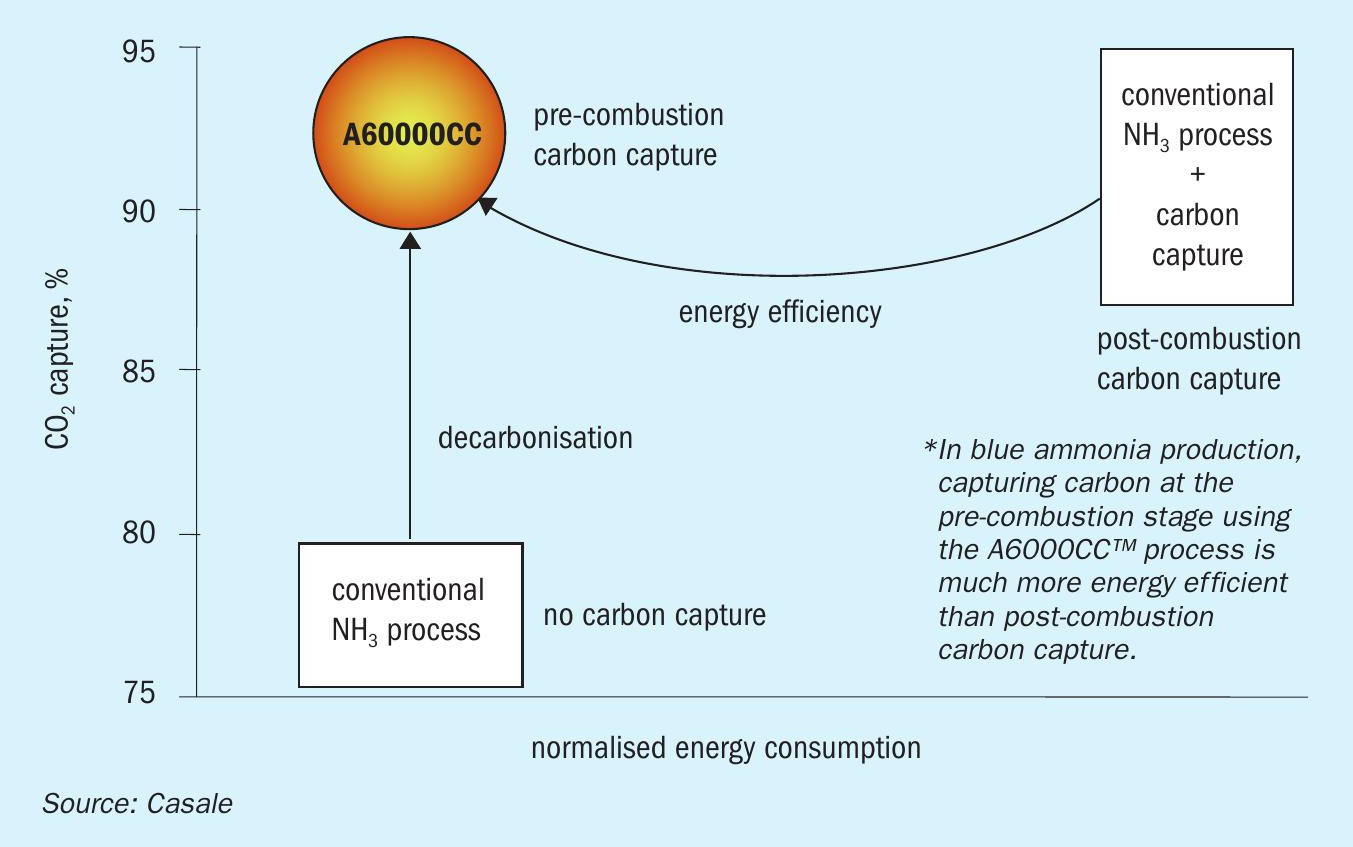
- A pure autothermal reformer (ATR) process
- Carbon dioxide is recovered in a single CDR section installed in the plant’s front-end.
- A hydrogen rich stream, taken downstream of CO2 removal section, is used as a furnace fuel gas for the various pre-heating services.
- The CO2 separated after purification and compression is delivered at a pressure above 150 bar
- The use of a liquid nitrogen wash system keeps the synthesis loop inert free.
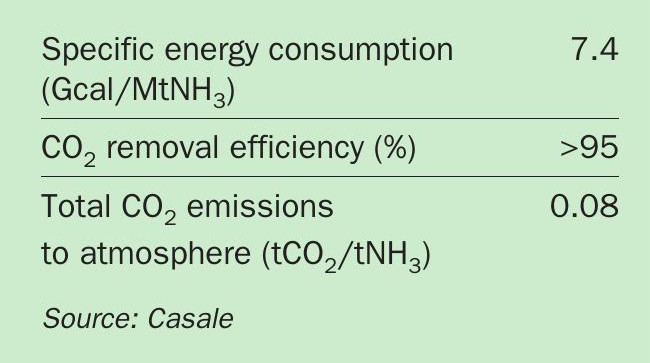
Capturing carbon capture at the pre-combustion stage using the A6000CC™ process (Figure 4) is much more energy efficient than post-combustion carbon capture. That includes both energy consumption within the BL (battery limit, i.e., the perimeter of a specific industrial process) and that used by utilities.
The main components incorporated into the A6000CC™ scheme – the autothermal reformer, ASU, CO2 capture units and ammonia converter – are well known and widely referenced at similar operational scales. The wide adoption of the underlying technology at similar plants means that Casale’s blue ammonia production process does not pose any new technical or operational challenges.
The A6000CC™ process performs well (Table 1) and is suitable for installation at new plants and for updating existing plants. Casale does, however, provide other technology options (H400CC™ and H1000CC™ ) for blue revamps, as discussed below.
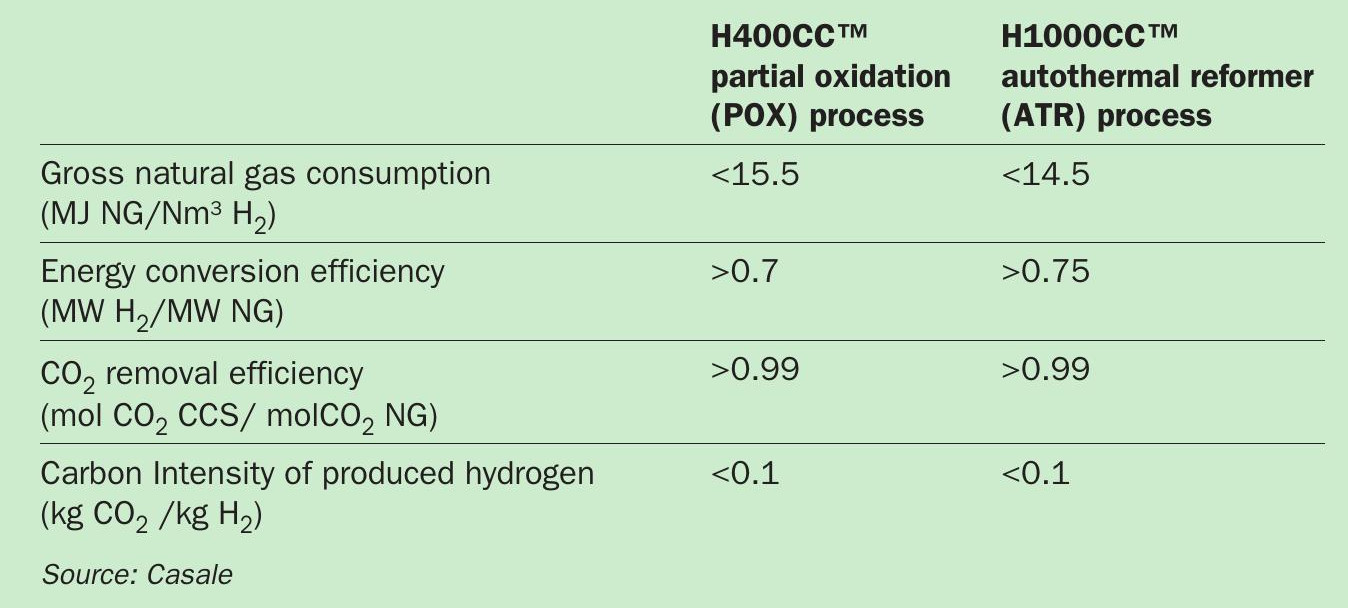
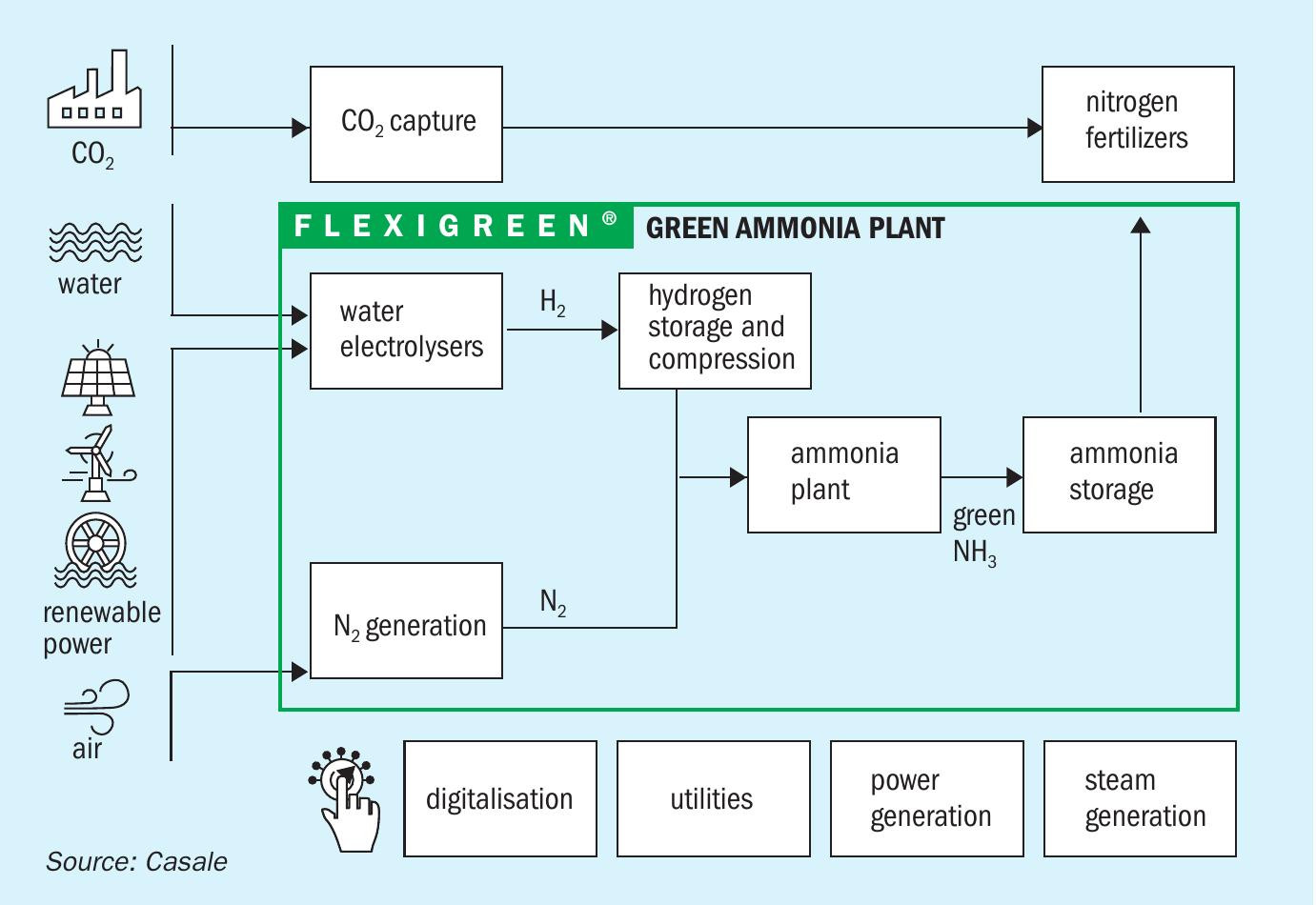
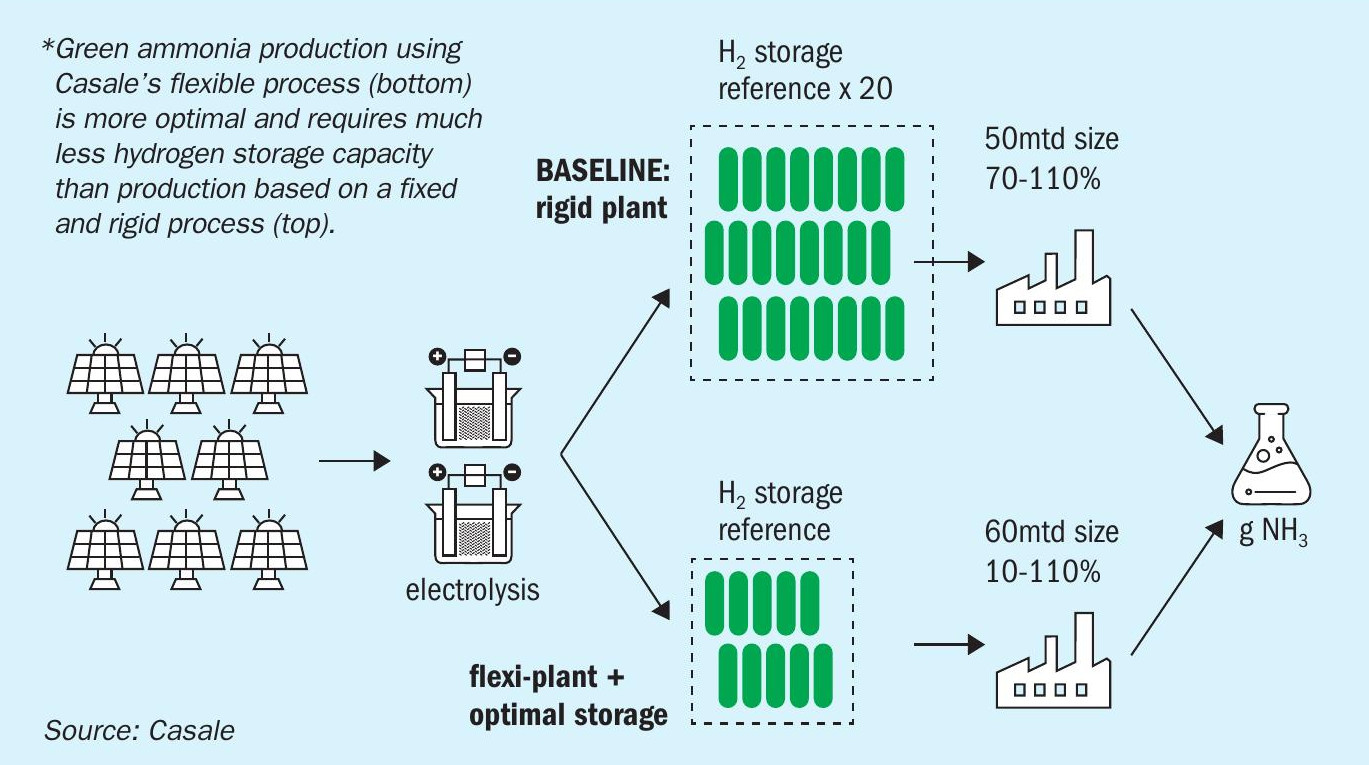
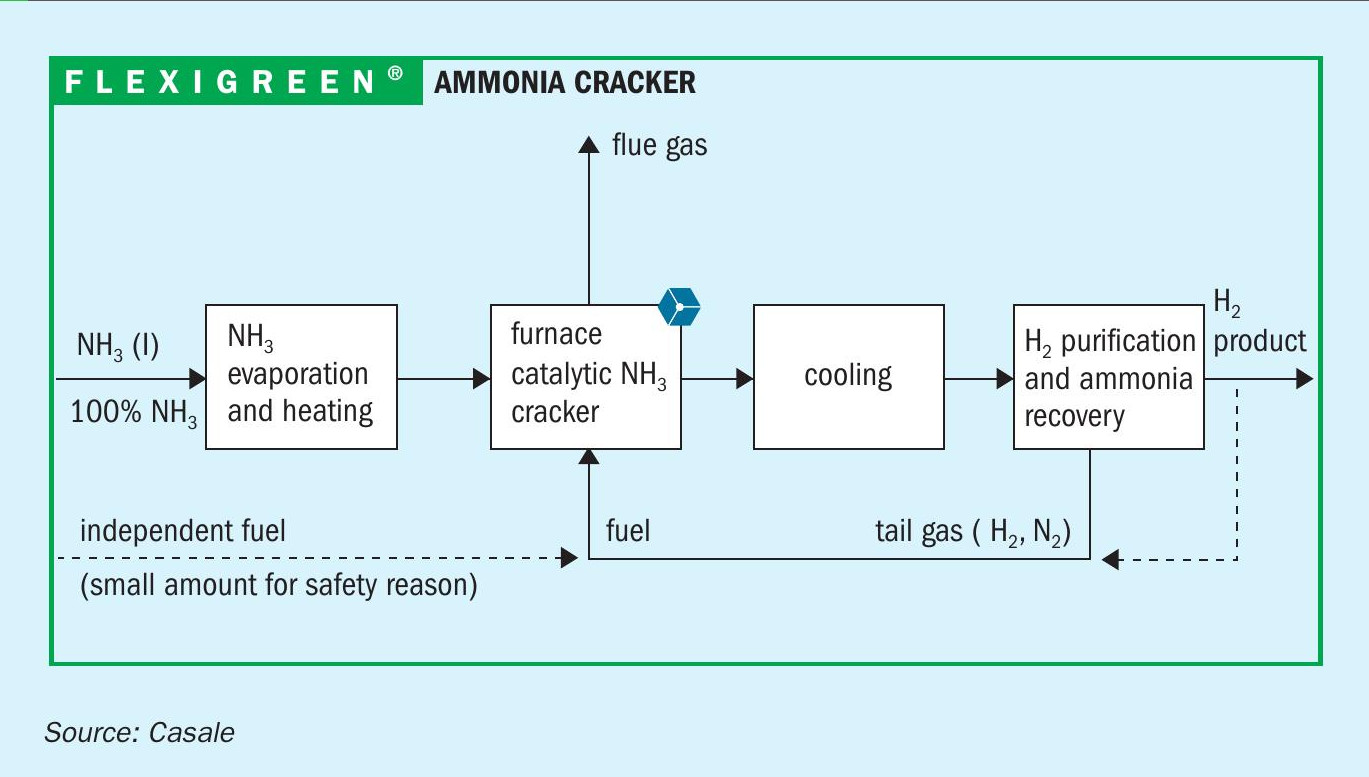
Casale offers two blue hydrogen production processes in its technology portfolio (Table 2). These are based on different syngas generation strategies:
- The H400CC™ process generates syngas through partial oxidation (POX). It can achieve blue hydrogen capacity of up to 100,000 Nm3 /h in a single line
- The H1000CC™ autothermal reformer (ATR) process is designed to achieve blue hydrogen capacity of between 200,000-400,000 Nm3 /h in a single line.
Casale has been able to develop this new business area due to its experience and track record in syngas generation. The achievable carbon intensity for both blue hydrogen processes is lower than 0.1 kg CO2 /kg H2 , while their energy consumption is in line with standard plants. Notably, Casale already has an ATR in operation with an equivalent hydrogen production capacity of more than 600,000 Nm3 /h.
Green ammonia plants
The green ammonia project pipeline is developing fast. Indeed, some new green ammonia plants expected in the next decade are up to ten times larger than blue ammonia plants.
As stated previously, meeting company climate goals or compliance with legislation are among the main motivations behind green ammonia projects. The ability of these projects to, firstly, deliver the lowest possible carbon emissions and, secondly, benefit from access to sustainability-linked finance is also advantageous.
Casale’s green ammonia production process (Figure 5) is based on the experience gained from designing and revamping hundreds of ammonia plants worldwide. By integrating its own proprietary and third-party technologies, Casale can customise the design of green ammonia plants and offer these in a wide range of capacities.
Casale can take complete responsibility for all the sections of the green ammonia plant including those sections with technologies supplied by third parties. The company is recognised as a global ammonia market leader and a benchmark technology provider for key sections of the green ammonia plant, such as the Haber Bosch loop.
Casale’s design experience builds on an extensive track record. Its reference list includes more than 90 new onstream hydrogen and nitrogen plants using fossil fuel feedstocks. Casale can also provide hundreds of references for completed revamp projects.
The key features of Casale’s green ammonia plants design are:
- The very high flexibility of its ammonia synthesis loop. This offers a capacity range of between 10-110 percent, versus the 70-110 percent range of standard ‘rigid’ loops.
- The incorporation of dynamic tools to fully exploit this capacity flexibility and minimise the levelised cost of ammonia (LCoA) production.
- A reliable and mechanically robust design capable of dealing with fluctuating renewable power (or green hydrogen) supply.
- The plant’s fast response time to sudden changes in the boundary conditions (such as power supply changes).
- Minimal hydrogen storage volumes, where required by the project. These can be 20 times smaller than in standard plants.
- Offers better green ammonia production performance compared to other available technologies.
Combined, these design features offer a green ammonia plant that is flexible, efficient and economically viable, as has been demonstrated by various Casale projects and published reports. Importantly, the inherent flexibility of Casale’s green ammonia design (Figure 6) guarantees a much lower LCoA compared to alternative rigid designs.
The digital control of the green ammonia plant – because it functions under erratic power and hydrogen supply conditions – is of paramount importance for efficient and reliable operation. Digitalisation via an advanced process control system also enables the safe and steady operation of the plant.
Green ammonia plants generally function under challenging operating conditions. These include very different loads (linked with the hydrogen supply profile) and specific ramp-up and ramp-down variations. Ultimately an inability to control this properly has the potential to damage plant operations by affecting catalyst life and equipment reliability. Digitalisation can, therefore, decide the difference between a profitable and a loss-making plant.
Casale provides a dynamic tool as part of the plant’s digitalisation and control system. This tool evaluates the plant’s boundary conditions and prevents adverse events from happening.
A simple dynamic analysis is carried out to assess plant’s operating behaviour under cyclical feedstock conditions. Casale’s advanced process control system is then able to smooth and stabilise the operation of the synthesis loop (e.g., the operating pressure and temperature of the catalytic beds). This helps protect the mechanical reliability of synthesis loop components.
Ammonia cracking
This is another technology of paramount importance to the energy transition. When ammonia is used solely as an energy carrier, effective cracking technology is vital, as it is needed to convert ammonia into high quality hydrogen for subsequent power generation.
Ammonia cracking is not a completely new technology – it is used, for example, to generate syngas for the start-up and shutdown of ammonia plants. But in today’s energy markets ammonia cracking needs to meet a number of specific additional challenges, such as:
- Generating high purity hydrogen at high pressure
- Operate as an efficient and continuous process with zero or very low environmental impacts
- Use modern and effective cracking catalysts
- Offer a high ammonia-to-hydrogen conversion ratio
- Handle large volumes of ammonia from big plants
- Provide start-of-run (SOR) versus endof-run (EOR) operation on a continuous basis
- Combine pure hydrogen production with power generation.
Casale offers a couple of catalytic cracking processes. These were developed to meet the following goals:
- Produce high purity hydrogen up to grade 5 quality, if required
- Function without the need for a hydrogen compressor
- High ammonia-to-hydrogen conversion at the battery limit
- Prolonged catalyst life (SOR and EOR conditions are met)
- Guarantee equipment longevity and lower capex – via the selection of the correct materials
- Offer combined hydrogen and power production.
The development of these new ammonia cracking processes has benefitted from Casale’s unmatched experience with ammonia synthesis. The ability to properly select materials for the synthesis section, for example, can make the difference between a plant that operates reliably and efficiently and a poorly performing, malfunctioning plant.
Casale’s ammonia cracking processes are self-sustaining and operates without requiring significant external power or other fuel sources. They also provide a feedstock-to-hydrogen conversion efficiency of up to 80 percent.
Conclusions
Our fertilizer manufacturing, chemical industry and power sector clients have a window of opportunity to decarbonise their operations to help avoid the disruption that climate change will ultimately bring. That applies to legacy plants as well as new plants.
The energy transition and the necessary shift to a net zero society are making clean, low-carbon production technologies (both ‘green’ and ‘blue’) for hydrogen, ammonia and methanol of paramount importance to the future of our world.
Sustainable power and chemical production remain a challenge, especially the avoidance of negative environmental impacts and the need to reduce carbon footprints. Nevertheless, Casale offers – and is continuing to develop – a broad range of technologies and products to meet the global sustainability challenge.
Casale’s blue and green schemes for hydrogen, ammonia, and methanol production are efficient and viable, being based on technologies that are already available and installed across a large number of references globally.
With its extensive know-how and dedication to innovation, Casale is fully committed to helping our society on the long journey toward a low-carbon future.
THYSSENKRUPP UHDE
Clean ammonia production – challenges and solutions
The traditional use of ammonia as a feedstock for nitrogen fertilizers is long established and well known. Nowadays, however, ammonia’s use as an energy and hydrogen vector is gaining more and more attention.These emerging yet fast-growing end-markets are prompting the development of new process technologies and plant set ups for ammonia production, either via renewable energy (‘green’ ammonia) or by combining conventional fossil fuel processes with carbon capture (‘blue’ ammonia).
This article discusses the production challenges triggered by the growing demand for green and blue ammonia – and highlights the solutions developed by thyssenkrupp Uhde to address these.
Green ammonia – the process challenge
Green ammonia is produced from hydrogen generated from the electrolysis of water using renewable power. This process avoids CO2 emissions – unlike the conventional natural gas based production of ammonia that predominates today.
The key challenge associated with green ammonia production is the fluctuation in renewable energy, i.e., the electricity supplied from a wind farm or solar PV power plant (Figure 1). These energy supply variations must be addressed and compensated for in the design of the downstream electrolysis and ammonia synthesis processes.
While most established electrolysis technologies have the capability to adjust to load changes from fluctuations in electrical output from renewable power plants, this is a major challenge for a conventional ammonia synthesis loop design – since traditional fertiliser production processes do not need to have the flexibility to cope with this kind of intermittency.
If not adequately addressed, with suitable process design and control measures, intermittent plant operations can have costly and damaging consequences – such as the collapse of the reaction in the ammonia converter and production curtailments.
Ultimately, such events will adversely affect the economic viability of the project by imposing capex and opex penalties. Therefore, to build a credible business case, the intermittency of renewable electricity, its varying price and other conditions, must all be considered early in the project’s development phase.
Optimising green ammonia plant design – the RHAMFS® analysis tool
When it comes to the design of the green ammonia plant, the ideal solution should offer operational flexibility yet minimise technical inefficiencies. The key to this is combining:
- The most appropriately sized intermediate energy storage – provided by batteries and/or buffer vessels for hydrogen
- With inherent process flexibility – in terms of the plant’s turndown and ramp-up/ramp-down capabilities.
An important point to make here is that providing too much process flexibility, which can be both unnecessary and too costly, is also undesirable. Instead, a project-specific (technical-economic) analysis is needed to develop the optimum flowsheet for the green ammonia process.
thyssenkrupp Uhde has, in fact, developed an analysis and optimisation tool – known as RHAMFS® – specifically to perform such an assessment early in the project design stages. The RHAMFS tool determines the most viable energy storage size for the plant and the optimum process flowsheet using a life cycle cost approach. The assessment takes account of the project’s renewable energy profile or grid power supply requirements (e.g., load shedding and power arbitrage).The tool also incorporates all of thyssenkrupp Uhde’s technology and integration know-how.
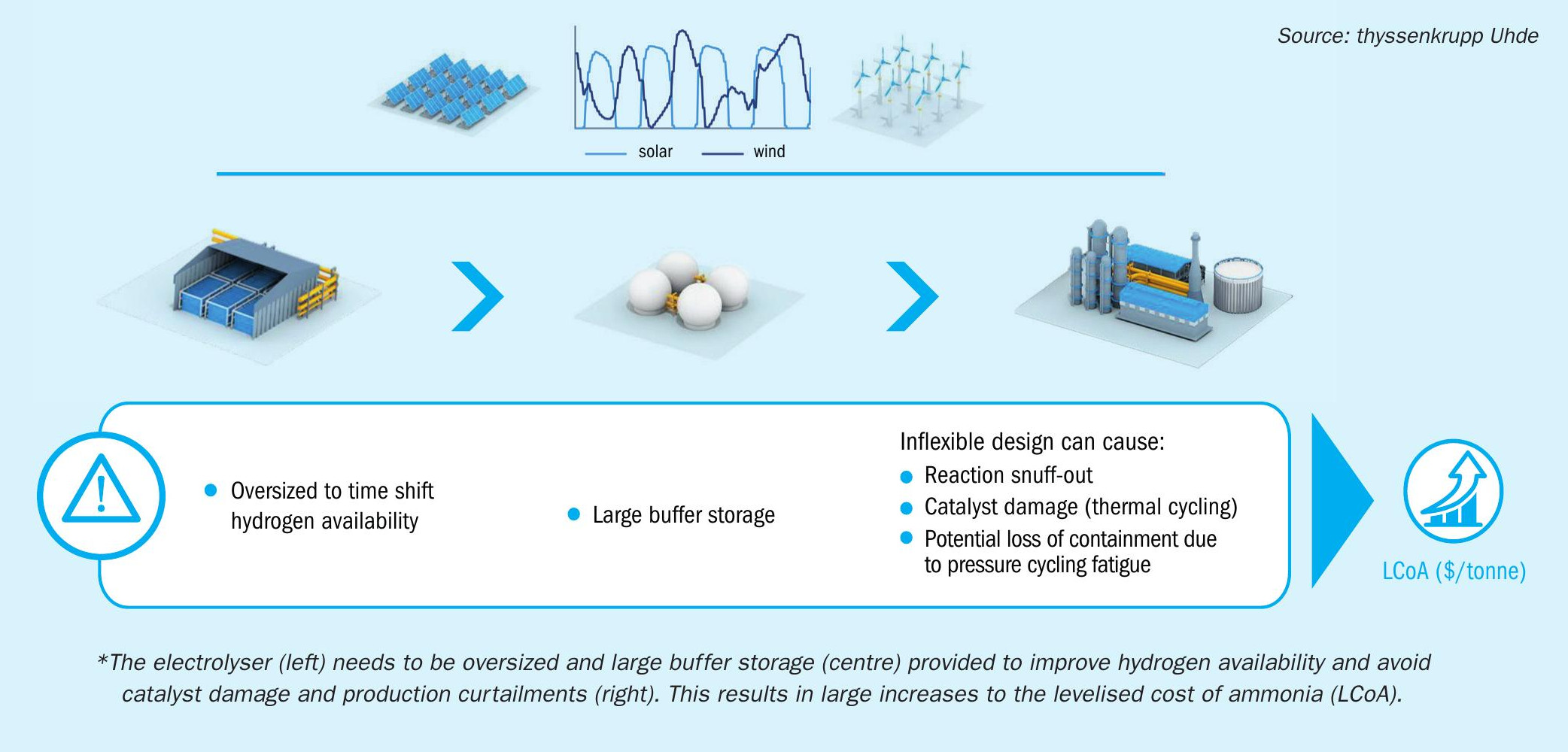
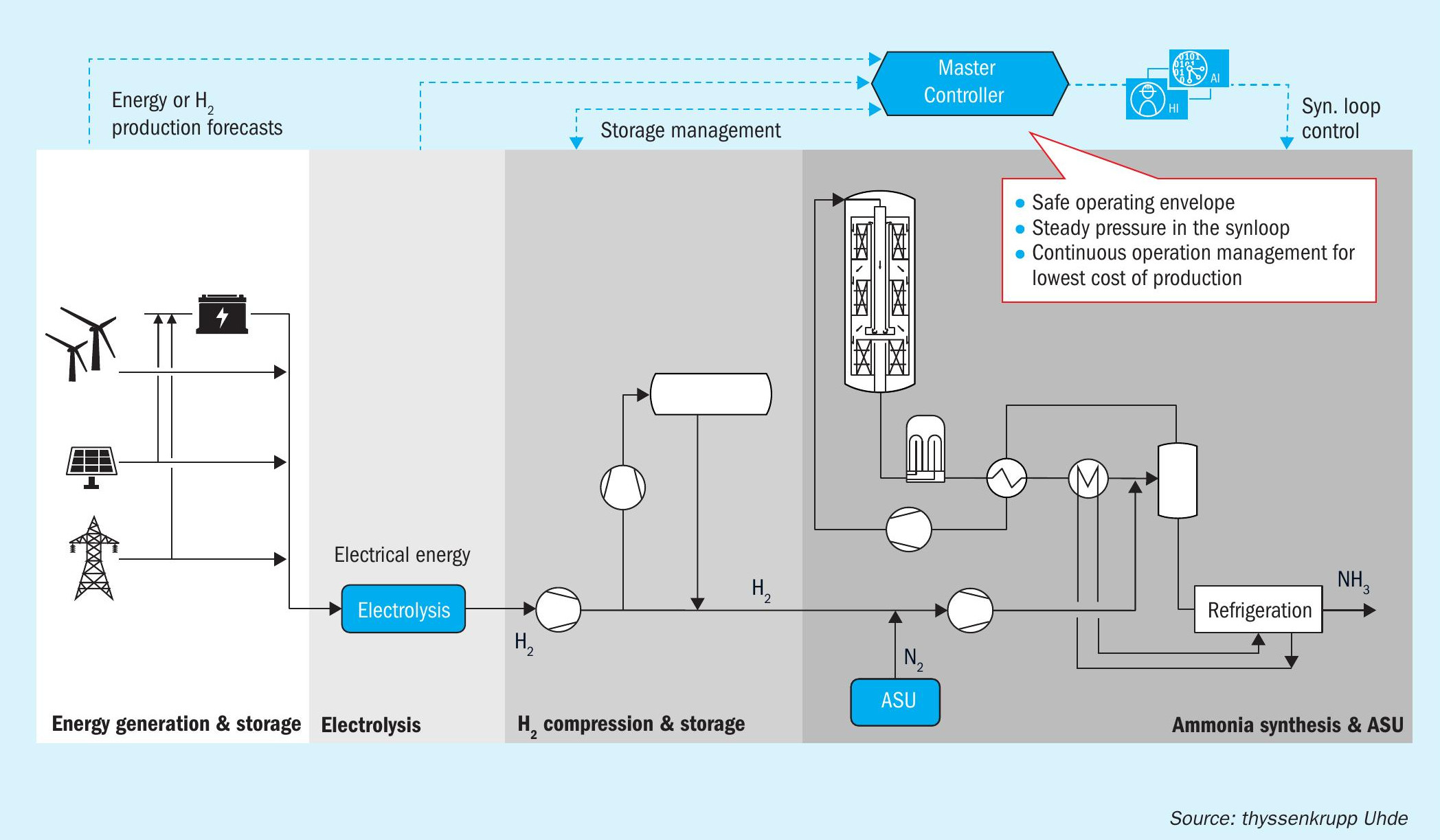
Optimising green ammonia production – the Master Controller®
The reliable operation of today’s green ammonia plants requires new process controls capable of seamlessly managing their dynamic production conditions.
In practice, the actual pattern of renewable energy supply is likely to deviate from the predicted or measured power profile used as the design basis of the plant. Under these circumstances, managing plant performance is a major challenge – one that can prove to be too difficult for conventional plant controls. Instead, a dynamic digital control system is generally necessary to ensure trouble-free plant operation, as well as minimising production costs at all times.
thyssenkrupp Uhde has developed such a proprietary advanced process control system. Known as Master Controller, this adjusts the load of the ammonia plant to the available and forecasted power, while also taking account of the loading and unloading of the intermediate storage elements (Figure 2).
Master Controller also considers a myriad of other technical and safety parameters – in the electrolysis, hydrogen storage and the ammonia unit – on a real time basis when setting up the plant for the forecasted power supply scenario. The control system offers the ability to:
- Maximise plant utilisation
- With a minimal hydrogen storage requirement
- While maintaining the efficiency benefits of an integrated approach.
In summary, thyssenkrupp’s proprietary Master Controller:
- Offers seamless integration with upstream hydrogen generation
- Manages plant operations dynamically to ensure high availability against intermittent feed supply
- Maintains critical pressure and temperature parameters within the synthesis loop to keep these within the equipment and process design limits
- Can be deployed across any electrolysis technology to achieve end-to-end powerto-ammonia production.
Blue ammonia
Blue ammonia production combines a conventional, natural gas based ammonia process with carbon capture to reduce CO2 emissions to the atmosphere. Carbon dioxide streams are generally removed using:
- Carbon capture and utilisation (CCU)
- Carbon capture and sequestration (CCS) to permanently store CO2 underground in a suitable geological formation.
Although there is no recognised definition of blue ammonia production, in term of the necessary CO2 capture rate, many current projects are calling for 90-95 percent removal.
Essentially, there are two alternative industrial methods for producing hydrogen and ammonia from natural gas – steam methane reforming (SMR) and the auto-thermal reformer (ATR) process. Both production routes have a similar overall energy consumption and generate similar volumes of carbon dioxide.
SMR and ATR also have two identical points in the process where CO2 is emitted:
- The reforming section. This consist of steam reformer flue gas in the SMR process and flue gas from a fired heater in the ATR process – both being available at atmospheric pressure.
RHAMFS TOOL CASE STUDY
thyssenkrupp Uhde performed a RHAMFS assessment on a 700 t/d green ammonia plant in Australia. This was subject to a variable hydrogen feed which, throughout the day, ramped-up/ramped-down between 60-120 percent of the plant’s nameplate capacity per hour.
The assessment identified that substantial reductions in hydrogen storage (>50%) were possible for a plant turndown as low as 10 percent, a threshold which is well within the capabilities of the Uhde ammonia synthesis loop design. The resulting saving in the levelised costs of ammonia (LCoA) amounted to 3.8 percent (Figure 3).
Based on the optimum flowsheet identified via RHAMFS, detailed process modelling was performed to mimic dynamic plant performance for location-specific renewable energy and hydrogen generation profiles. Master Controller, thyssenkrupp Uhde’s digital plant control system, was then enabled to manage the plant’s performance. As a result, the green ammonia plant operated trouble free at between 10-100 percent of nameplate capacity, with ramp-up/ramp-downs of between 60-120 percent of the maximum load possible per hour (Figure 4).
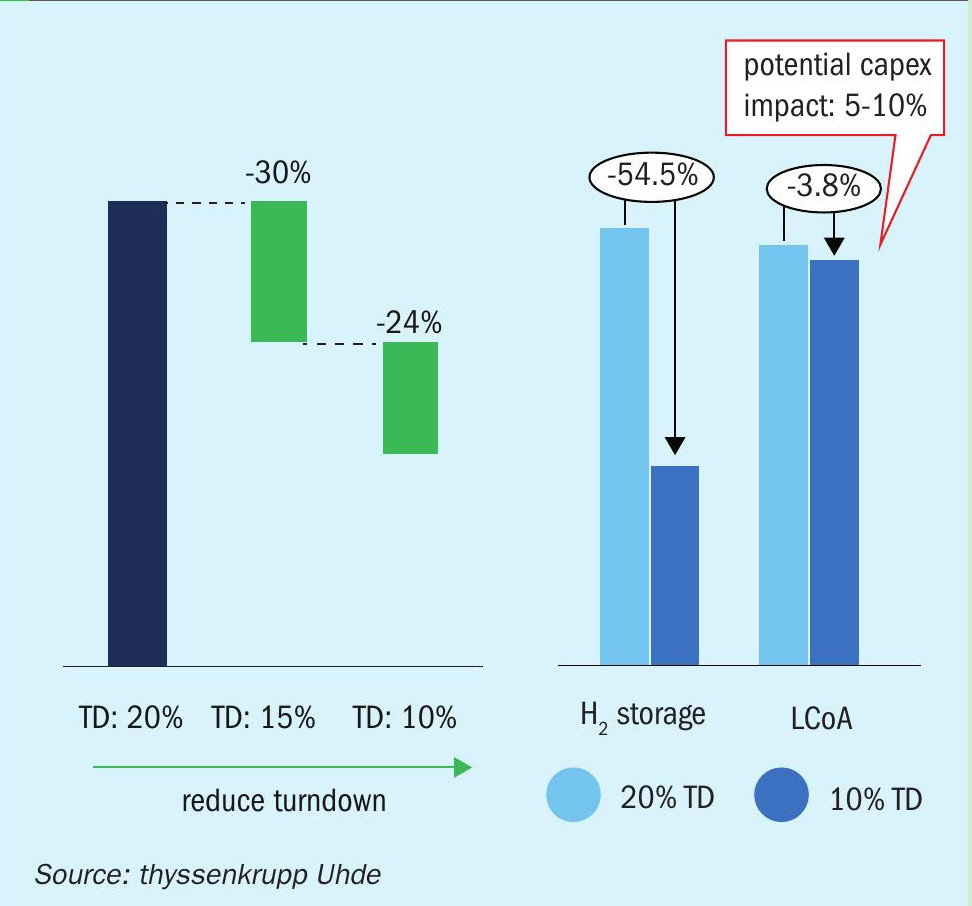
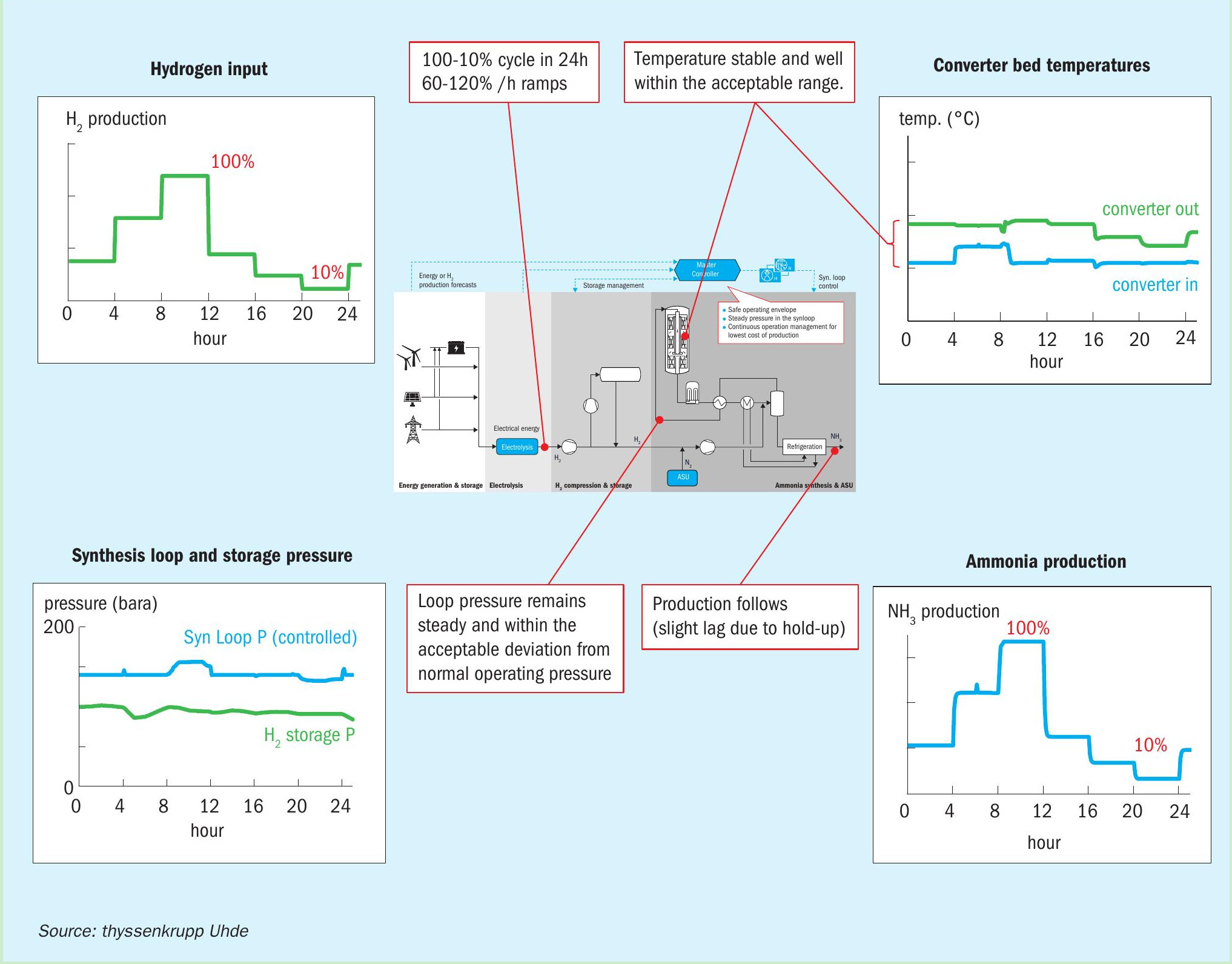
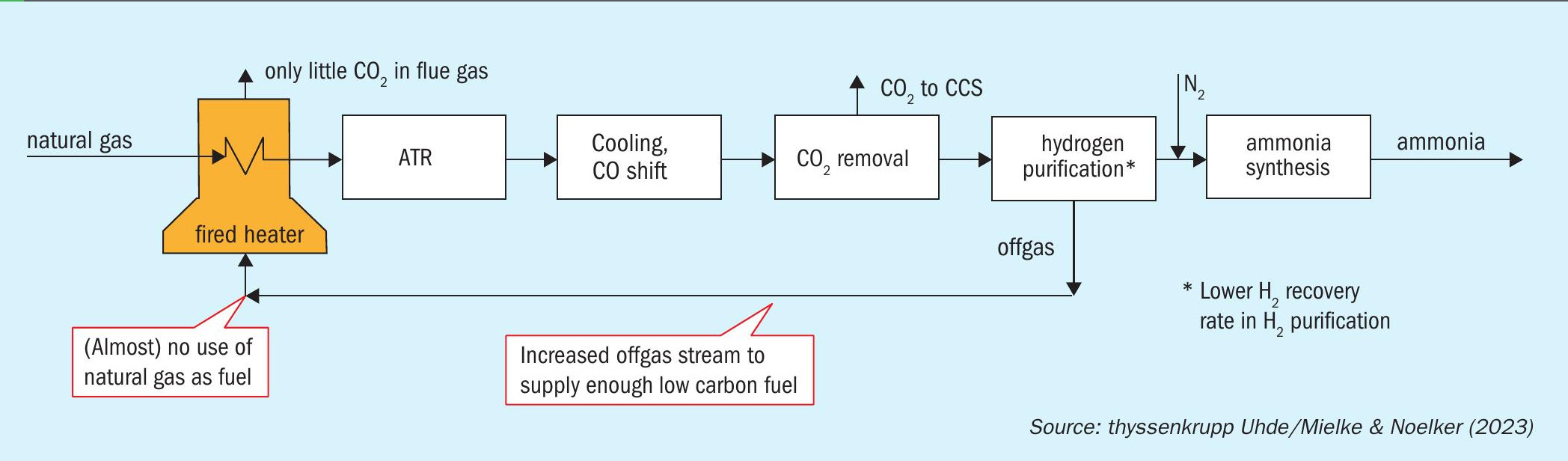
- The CO2 removal unit. This is where carbon dioxide is separated from the process gas.
The carbon dioxide stream from the CO2 removal unit is the larger of the two emissions points. It usually generates CO2 with a purity of more than 99 percent and is sequestration-ready, i.e., it is a pure carbon dioxide stream generated by equipment that is already part of the ammonia process. It is therefore logical that the CO2 emissions generated at this point are the first to be reduced, as the only additional capex is for compression and export infrastructure.
However, higher carbon capture rates require further effort and investment, as an additional unit (e.g. a scrubbing unit) for separating the CO2 from the flue gas needs to be installed to generate a pure carbon dioxide stream, prior to compression for export.
One significant difference between SMR and ATR processes is the split in CO2 emissions between these two points: about 70 percent of total CO2 is generated at the CO2 removal unit in the standard SMR ammonia process, while in the ATR process it is about 85-90 percent. (The reason for this is that CO2 is left in the process gas in the ATR process, as the heat for the reforming reaction is supplied from the combustion of a portion of the feed gas, and not by external combustion.)
This means that, intrinsically, ATR can deliver a higher rate of CO2 reduction, without the installation of an additional flue gas scrubbing unit. Normally, however, the ATR process will still need equipping with flue gas scrubbing, if reduction rates above 85-90 percent are required.
Some customers are understandably reluctant to do this because extra capex, opex and operator effort are required to install an additional process unit that is not present in a conventional ammonia plant.
The improved autothermal reformer
thyssenkrupp Uhde has therefore developed an alternative, more cost-effective solution for the ATR process that can reduce CO2 emissions by up to 99 percent, if desired.
Much of the current focus for blue ammonia production is on ATR process technology. That is because future ammonia plants for the energy sector are expected to be large plants – and ATR plants offer a capex advantage over SMR plants, especially at larger production capacities.
A key feature of the thyssenkrupp Uhde ATR process is its ability to minimise/ eliminate the carbon-carrying natural gas portion of the fuel used by the fired heater1 (Figure 5). Instead, the amount of hydrogen-containing offgas supplied to the fired heater is increased to such an extent that it completely covers the energy demand of the fired heater. Natural gas supply to the heater is reduced to virtually zero as it is only needed during start-up.
The only CO2 emissions generated by the fired heater are from residual amounts of CH4 , CO and CO2 left by the hydrogen purification unit. Using this pre-combustion solution, 99 percent of CO2 emissions can be avoided without the installation of an additional costly flue gas scrubbing unit (post combustion solution).
Geismar blue ammonia project
The number of clean ammonia projects has increased in recent months. This has been due to a combination of high ammonia prices and better financial incentives for reducing carbon emissions. At the end of 2022, the world’s largest fertilizer producer Nutrien awarded thyssenkrupp Uhde the engineering contract for a 3,500 t/d, single-train ammonia plant in Geismar, Louisiana (Fertilizer International 511, p8). This world-leading blue ammonia plant will use the ATR process described here (Figure 5) and achieve a carbon capture rate above 90 percent for storage via CCS.
Summary
There is an emerging new market for low-carbon ammonia as an energy and hydrogen carrier.
Yet the intermittency of renewable energy poses a challenge for the economical production of green ammonia. To address this, thyssenkrupp Uhde has developed a flexible, safe and reliable proprietary process for green ammonia based on renewable energy. This process, when coupled with innovative digital control systems, can provide a fully integrated solution for green ammonia production.
thyssenkrupp Uhde has also developed an optimised and cost-effective autothermal reforming (ATR) process for new blue ammonia plants. This process can reduce carbon dioxide emissions by more than 90 percent – without the need for an additional flue gas CO2 removal unit. The use of process gas as carbon-free fuel means more CO2 can be captured. The engineering on a large scale blue ammonia plant using this process is already underway in the United States.
References