Sulphur 407 Jul-Aug 2023
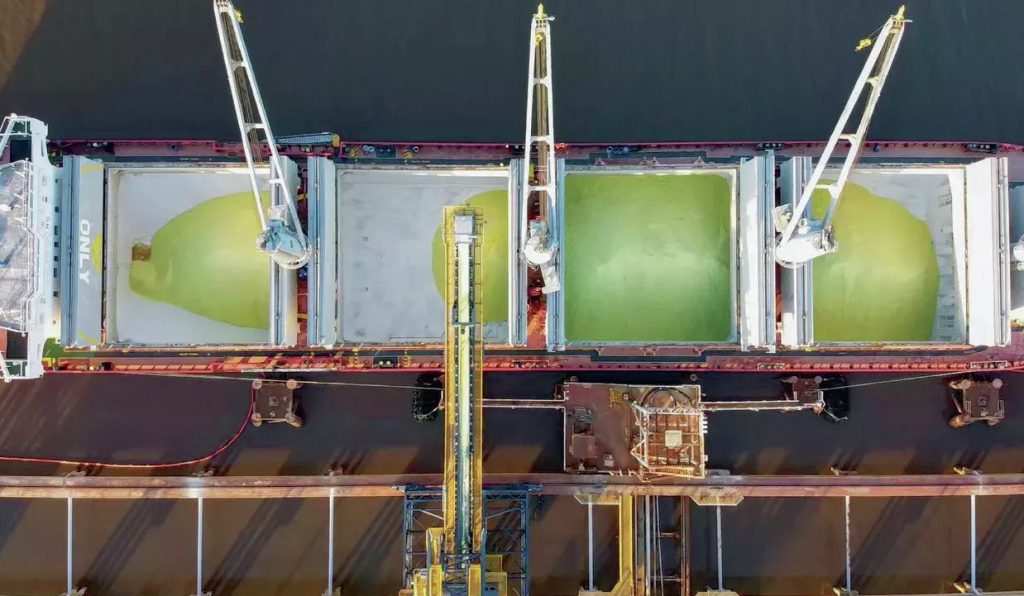
31 July 2023
Sulphur dust suppression
DUST
Sulphur dust suppression
Sulphur dust is one of the greatest hazards when producing and handling solid sulphur, and methods for its suppression are vitally important to prevent fire and explosion.
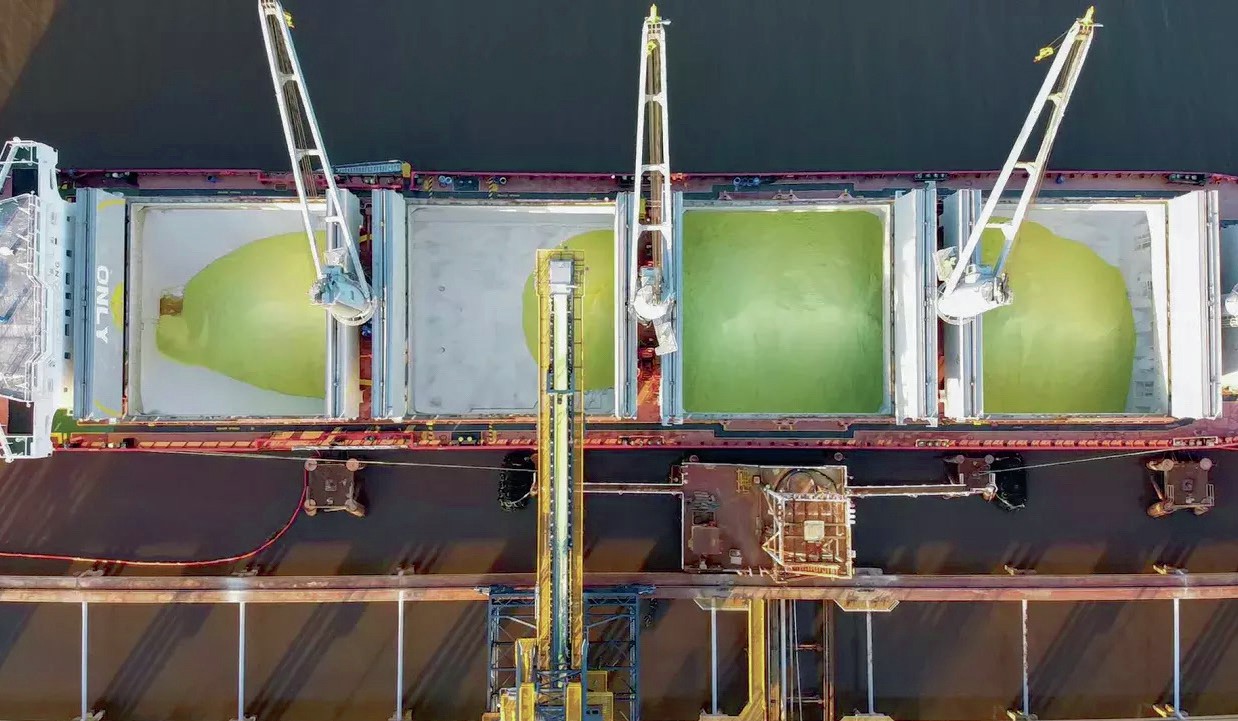
While sulphur is a fairly benign substance in terms of toxicity and is a solid at room temperature and pressure, making handling fairly easy, it has various characteristics which can be problematical if not looked after. As is detailed in the article elsewhere in this issue (pages 44-53), it is very brittle and friable, which means that rough handling can cause it to break into progressively smaller pieces.
The condition of the sulphur begins with the sulphur recovery unit (SRU) which is producing it. Running outside of normal temperature limits, the inclusion of contaminants, or even catalysts used in the degassing process can all contribute to the properties of the formed sulphur, and the proportion of polymeric sulphur molecules which can reduce friability.
But undoubtedly the greatest influence comes from the forming process itself. One complication of sulphur is the crystal phase change between the higher temperature monoclinic form to the orthorhombic crystal structure, which occurs at around 95°C. The speed at which the sulphur is cooled during forming and at what temperature it is subsequently stored can affect this phase change. Sulphur has a very high specific heat capacity and acts as an insulator, so the bulk solid can retain heat for a considerable period. The monoclinic form is stronger than the orthorhombic form, and rapid cooling can preserve the monoclinic form in the cooled sulphur, but this will gradually change over time as the sulphur ages. The phase change is also exothermic and contribute to caking.
Forming processes roughly divide into those which produce dry sulphur and those which include entrained water with the sulphur. The main dry forming process is pastillation, whereby water is sprayed under a steel belt on which liquid sulphur drops are deposited to produce pastilles. Wet processes include granulation, where water is sprayed into a rotating drum to cool liquid sulphur that has been sprayed onto a seed curtain to form sulphur particles or ‘seeds’, and wet prilling, where liquid sulphur is introduced at the top of a forming tank for direct counter-current heat exchange, with water, used to produce prills that are withdrawn from the bottom of the forming tank.
In general wet sulphur generates less dust, as the water allows fine particles to agglomerate, but this is complicated by sulphur’s hydrophobic nature, which can prevent water from completely wetting particles. For this reason surfactants are often added to improve the water penetration into the sulphur.
Dust hazards
The main hazard associated with sulphur dust is fire and/or explosion. Sulphur burns if ignited, and when there is a large surface area to air ratio this can be rapid enough to cause an explosion. The lower explosion limit for sulphur is usually quoted as 35g/m3 , but finer particles can lower this to around 20g/m3 . Finer particles (<75 micrometers) are easier to suspend in the air, and also have a lower ignition temperature, and can be set off by static electricity sparks generated by sulphur particles rubbing against each other. Therefore, care must be taken to prevent static electricity accumulation in areas where solid sulphur is handled.
Smoking and the use of matches must be prohibited in all areas where sulphur dust is likely to be present. Naked flames or lights and the use of gas cutting or welding equipment should also be prohibited during the normal operation of the plant. It is also important to remove potential sources of ignition. To prevent excessive heat build-up, all equipment should be properly and securely installed to ensure the correct alignment of rotating shafts, belt tension etc. The surface temperature of plant or machinery should not be allowed to exceed 2/3 of the ignition temperature of sulphur dust (i.e. 127°C). Once sulphur burns or explodes, it also generates sulphur dioxide, which is toxic.
Sulphur can be abrasive, so care must be taken to use equipment that can withstand prolonged exposure to sulphur. If the sulphur is being pneumatically conveyed into a processing system, the blower used to move this material through the air line must be sized to meet the demands of system. The use of 316 grade stainless steel is usually recommended for any equipment that is exposed to sulphur.
There is also the risk of corrosion, especially where wet sulphur is present. The carbon steel in long term contact with wet sulphur can produce ferrous sulfide on the surface. Water has a catalytic effect on the spontaneous combustion process of ferrous sulfide, and the initial self-heating temperature of fire sulphide can be reduced from 141°C when there is no water to only 40-60°C when water is contained. Humidity in the air can also promote self-heating performance of ferrous sulfide.
Dust minimisation
In order to prevent dust fires and explosions there are two basic strategies; to avoid suspensions of dust in the air, and to exclude sources of ignition. Dust formation can be reduced by reducing the number of transfer points and handling steps to a minimum, and try to minimise the use of front end loaders which can crush sulphur granules beneath their wheels.
Some grades of powdered sulphur can be non-free flowing and the material may tend to cake or pack. This characteristic can affect feeding of the conveyor, as wells as the discharge of the material from the conveyor. Because of this characteristic, it is important to select infeed transitions with the correct geometry as well as the provision of flow-aids, such as vibrators or agitators, to ensure trouble-free feeding of the conveyor.
Fine sulphur particles can adhere to the surface of conveyor belts and fall due to the vibration of the belt and the change in tension, causing the fine sulphur to be scattered along the belt, or be lifted to land on any horizontal surfaces. Storage in buildings can protect dry sulphur from the elements, but – given the explosive nature of sulphur – it also requires greater dust management. To prevent dust accumulation during storage and handling of sulphur, enclosures should be constructed with a minimum number of horizontal surfaces where dust can accumulate, and access to any and all hidden areas. Good housekeeping is a must, with inspection of and cleaning of dust residues at regular intervals.
When reclaiming sulphur from storage, gravity-based systems can produce less product damage, but rely on the flow characteristics of the sulphur, which can be impacted by caking in moist environments. Mechanical systems are more aggressive and impart more stresses onto the product.
Dust suppression
While dust minimisation and good housekeeping is essential for keeping dust levels down, dust formation cannot be prevented completely. The next step then is to suppress dust. Water can be sprayed at transfer points and load-out station; the wetted particles agglomerate to each other and to larger particles, making them more difficult to be picked up by air currents. However, as previously noted, water promotes the formation of acidity and wet sulphur corrosion. For this reason a maximum moisture content of 2% is recommended.
The effectiveness of water for dust control is also limited by the hydrophobic nature of sulphur. This can be overcome by the use of special water-based chemical surfactants. When air is mixed with the surfactant/water mixture, foam is generated. Foam is a very effective means of dust control, made up of small bubbles 100-200 micrometers in size. When it comes into contact with dust particles the bubble breaks, coating the particle. When several come into contact they coalesce into a larger particle and can no longer become airborne as dust. Foam suppression systems create 0.5-1.0% moisture on the specified transfer point according to the transfer rate. Foam is normally applied upstream of transfer points to reduce dust formation during transfer.
Fire
Even with preventive technology in place, there are rare occasions on which fire will nevertheless occur. Fire detection systems should be in place along the conveyor line, perhaps linked to automatic water spraying systems and interrupts to stop the conveyor and prevent fires entering a storage area or building.
When a sulphur pile is on fire, it is necessary to avoid directly impacting the sulphur pile or the ground around the fire point with a direct water jet because the air flow brought by the water column impacting the sulphur pile or the ground will disturb the sulphur dust and suspend the sulphur dust in the air, potentially reaching the explosion limit. The best way to extinguish fire is to use nozzles with good atomisation effect, A water curtain spray system can be used together to form a liquid mist screen of fire extinguishing agent and reduce the possibility of dust and sulphur suspended in the air.