Nitrogen+Syngas 385 Sept-Oct 2023
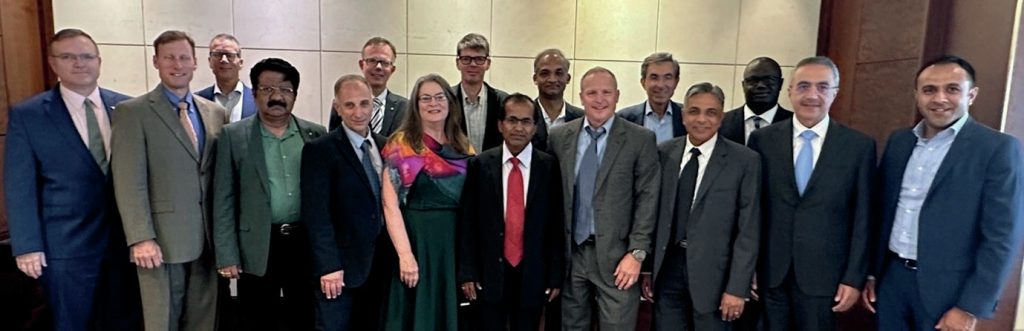
30 September 2023
Ammonia Safety Symposium
CONFERENCE REPORT
Ammonia Safety Symposium
Venkat Pattabathula, a member of the AIChE Ammonia Safety Committee, reports on the American Institute of Chemical Engineers’ Safety in Ammonia Plants and Related Facilities Symposium, held in Munich, Germany, from 20-24 August 2023.
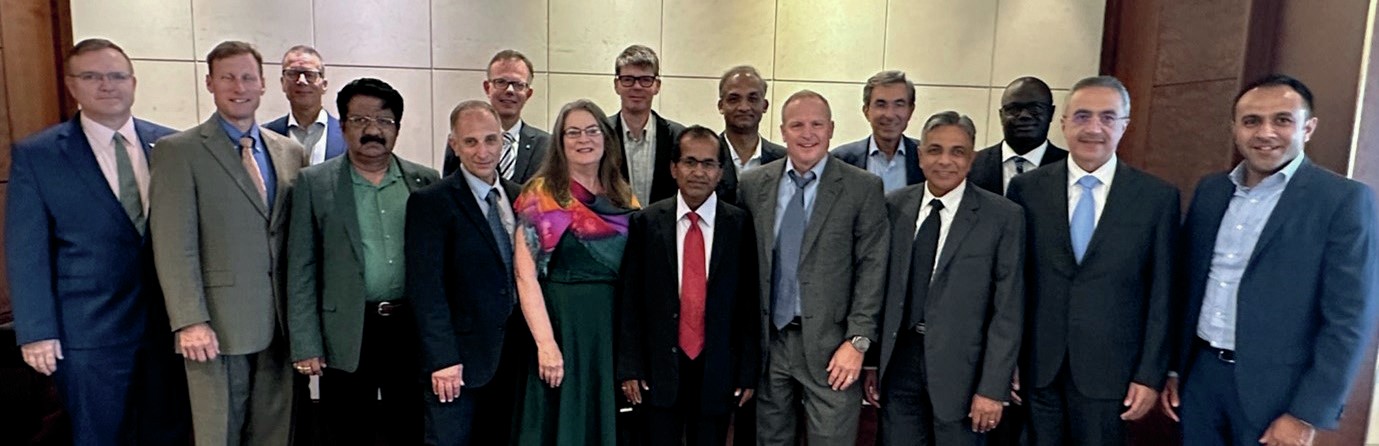
The Ammonia Safety Committee is dedicated to improving the safety of plants that manufacture ammonia and related chemicals, such as urea, nitric acid, ammonium nitrate, and methanol. The conference’s objective is to improve the safety performance of the ammonia industry. This is achieved by sharing information on incidents, safety practices, and technology improvements in presentations and open discussions.
From 20-24th August 2023, 360 engineers from more than 30 countries and 100 companies attended the AIChE’s 67th Annual Ammonia Safety Symposium at The Westin Grand Hotel in Munich. Attendees who participated in the Symposium included plant managers, production managers, safety managers, process/reliability engineers, and everyone responsible for the safety and performance of ammonia plants or handling facilities, to hear worldwide experts discuss the latest advances in safe production and use of ammonia, case studies, and lessons learned at these symposiums.
Zero accident vision
This year’s keynote speech; Zero Accident Vision – What would it take? was presented by Volker Andresen, Sustainability Director of the International Fertiliser Association (IFA). Volker started his speech with a universal truth: “nobody wants to get hurt.”
He began with a brief history of workplace safety, from the divine protection sought by stone age hunters and gatherers to the first known set of employment laws to ensure safety and prevent workplace accidents, dating to ancient Egypt. In the modern era, at the beginning of the industrial revolution, the English Parliament passed the first factory work regulations in 1802, setting limits on working hours and establishing minimum standards for hygiene, health, and worker education. However, it was a century until checks were made that the laws were being adhered to, when in 1898 Sir Thomas Morrison Legge was appointed the first British medical factory inspector. After World War One, the International Labor Organisation (ILO) was established in 1919 under the Treaty of Versailles to promote social protection, workers’ rights, and the improvement of working conditions globally. Yet according to the ILO in 2023, work still kills more people than wars globally.
Turning to the ammonia industry, Volker said that the International Fertilizer Association, founded in 1927, remains the only global fertilizer association, with a mission to promote the efficient and responsible production, distribution and use of plant nutrients. It has 470 members from 80 countries across the entire fertilizer value chain. IFA’s member and stakeholder surveys confirm that safety is on everybody’s mind. Safety (including security) is the number one driver of the industry’s reputation. To improve the overall reputation, stakeholders need to believe that this industry is committed to creating global best practices in product safety and security. In 2018, the two-year IFA 2030 scenario planning reconfirmed the importance of safety and security for keeping our industry’s license to operate in the 2020s.
IFA’s surveys suggest that the main occupational safety issues include: lLack of personal protective equipment; inadequate procedures and controls; insufficient training (especially of contractors); poor internal communications; fatigue, stress, distractions; and human errors, including complacency. Meanwhile the main process safety issues include: insufficient process safety procedures; poor process safety controls; inadequate hazardous material storage and handling; improper segregation of incompatible chemicals; equipment failure and malfunction; and lack of emergency preparedness.
IFA members formally agree on the 12 Safety, Health, and Environment (SHE) Principles:
- Striving for zero harm
- Demonstrating company leadership and management commitment
- Setting annual objectives, targets and key performance indicators
- Complying with local laws and embracing global best practices
Members have developed IFA’s Safety Handbook to benefit the entire fertilizer industry; it is 58 pages long and available in English, Arabic, Chinese, Spanish and Portuguese. Its first chapter describes the major principles behind positive safety management: PDCA – Plan, Do, Check, Act – and successful execution; POPMA – Policy, Organisation, Planning, Measuring, Auditing.
Since 2001, IFA has also published its annual safety benchmarks. These are 100% voluntary, confidential and free, and include Lost Time Injury Rate and Total Recordable Injuries and can help measure the effectiveness of safety management systems and compare them against the industry’s best safety performers, allowing companies to develop organisation-specific key performance indicators. Members can participate online in English, Chinese, and Russian.
Online education includes webinars with IFA Green Leaf Award winners and safety and security classes of IFA’s Sustainable Fertilizer Academy. In-person education includes security workshops with organisations like the US Army in sub-Saharan Africa and the roll-out of a chemical identification test kit with pocket wizard, which IFA helped the World Customs Organization to develop. Written education includes IFA’s Safety Handbook and a product security poster campaign for its retailer and distributor network in Sub-Saharan Africa.
So how can we turn a zero accident vision into reality? Safety expert advice includes making the ‘Must Win Battle’, led by senior company staff. Companies should apply existing best practices and systematically melt the “accident iceberg” – an acknowledgement that for every incident that is recorded, there are many near misses which perhaps are not but from which key learnings can be taken. Companies should build partnerships with everyone involved; employees, contractors, first aiders, firefighters, and regulators. Complacency is the enemy!
Volker concluded by noting that technology is now bringing unprecedented opportunities for sefty improvement via areas such as robotics and automation, collaborative robotics, smart wearable technology, sensor-based hazard detection, AI-based safety analytics and Virtual Reality training sessions, and allows for new out of the box thinking, such as drone inspections for hazard elimination, the introduction of smart traffic safety sensors. Some companies have used a safety blackboard to report incidents anonymously with no names mentioned. Safety is not a destination, but a never-ending journey.
Safety incidents
The key safety-related papers were:
Secondary reformer outlet transfer line rupture
On February 17, 2022, the Dyno Nobel Plant in Waggaman, LA, experienced a rupture of the Secondary Reformer outlet transfer line of its 2300 t/d KBR ammonia plant. Fortunately, there were no injuries from this incident. This loss of containment resulted in a significant fire, damaging adjacent equipment and instrumentation. This paper reviewed the incident and the troubleshooting of the other front-end reactor effects and remedies undertaken to repair the transfer line and restart the plant.
It was determined through the extensive root cause analysis that the failure was ultimately caused by a liner weld that had failed and, when inspected and tested, appears to have been originally of poor quality, with some lacking full penetration depth. Analysis revealed that hot cracking likely occurred in the extension welds during fabrication. Additionally, deviations were made from the original liner slip joint design drawings, such as the mating direction of the sliding joint being found reversed from the design drawings.
The refractory layer in the middle segment was also found to have undergone alkali hydrolysis throughout its entire thickness. Alkali hydrolysis is a reaction in which the cement that binds the refractory is converted into carbonates in water and CO2 , causing cracking and decreasing strength and stability. It was determined that after installation, the refractory had not been adequately protected from atmospheric CO2 and had not dried for months until commissioning. It was also noted that there had been extensive delays in the dry-out process during plant commissioning of the bubble alumina refractory material after pouring. This delay left the refractory in a state where rapid deterioration permitted a gas path to form to the pressure shell and exposed the shell to temperatures well over the design conditions.
The transfer line was rebuilt to the intended design with more rigorous QA/QC controls to ensure a higher liner standard and refractory installation.
Failure of secondary reformer due to top dish head rupture
After more than 41 years of trouble-free service, a fire jet with an explosion occurred due to loss of containment from a secondary reformer top dish head at Fauji Fertilizers. A crack in the pipe base metal allowed the premature entry of air into the flammable process gas environment ahead of the burner, where it ignited, causing failure of the refractory, exposing the metal surface to high temperatures of burning gas, resulting in a dish-head rupture. The dish head was restored by welding an insert patch, three-dimensionally formed from a carbon steel plate, using in-house resources and plant production was resumed in just 15 days.
Secondary reformers’ failures are rare in the industry, and the risks associated with such failures are normally very high. The explosion at FFC resulted from a weld crack in the air inlet pipe of the burner. This crack formed a passage that let air into the reformer, ahead of the burner, where flammable process gas ignited, and this failed the refractory, thus exposing the metal surface to very high temperatures above the design values and eventually resulting in loss of containment. The failure’s root cause was weakness in the design, which the designer improved in later years at new plants. However, this improvement was not carried out on this ~41-year-old equipment due to a lack of communication and documentation sharing. Learning from the incident, a robust action plan was developed to address vulnerable areas and mitigate risks associated with ageing plants, including improved liaison with the process licensor and document sharing, RBI and PSM systems implementation and establishment of an Asset Reliability and Integrity department.
Mixed feed reheater manifold and piping failures
A significant failure occurred on the mixed feed reheater (B-901) 304H stainless steel outlet piping system at Nutrien number 3 ammonia plant in Point Lisas, Trinidad in July 2022. This paper explored the failure of the piping and presented an analysis of the causal factors. The effects of creep, sigma phase embrittlement and solidification cracking are examined, and the lessons learnt were highlighted.
During start-up operations a hissing sound was heard near the mixed feed reheater. Insulation was seen dislodged from the area where the hissing sound was being emitted, prompting an immediate plant shutdown. Further investigation revealed multiple cracks on the mixed feed reheater outlet manifold and associated outlet piping from B-901 to the B-701 primary reformer. Repairs and partial replacement were conducted on the failed sections to return the plant to production, with the intent of a complete replacement during the October 2022 turnaround.
Type 304H stainless steel is widely used in the industry and has shown good performance overall. However, it is recognised that 304H stainless steel is susceptible to sigma phase embrittlement after prolonged periods of high-temperature operation. Detailed review and selection of electrode specification is necessary to ensure the produced ferrite content is within the recommended electrode specification to avoid sigma phase embrittlement and solidification cracking. The presence of the sigma phase is directly related to reduced creep ductility, as was observed in the failures. Solidification cracking can be prevented during welding with adequate quality control.
The failures have brought awareness to the importance of adjusting inspection test plans to capture all potential damage mechanisms adequately. Inspection test plans for in-service operation and fabrication/repair activities should be provided. Emphasis should be placed on inspection and possible asset replacement to mitigate against these damage mechanisms in aging facilities.
Two-phase flow in a high-speed compressor
The centrifugal air compressor of the ammonia plant at the MOPCO site in Egypt consists of high pressure and low pressure stages which had a damaging effect on the two-phase flow of the high-pressure stage due to a malfunction in the intercooler of the high-pressure section. A full investigation into the incident determined that improper assembly of the third intercooler bundle during a major overhaul in June 2014 led to damage to sealing strips so that hot gas could bypass the bundle rather than flow through it. The malfunction of the mechanical condensate trap prevented the condensate from flowing outside the cooler; this then caused carry-over of condensate with the gas flowing towards the compressor fourth stage suction, i.e. two-phase flow affecting the HP rotor behaviour established a high shaft vibration at average rotor speeds, which was thought to be imbalanced during the preliminary analysis.
Corrective actions included inspection of all compressor minor and major parts. All clearances were measured and adjusted to tolerance ranges. The intercooler stage bundle was replaced with a new one and the intercooler stage shell cleaned and painted using a new heavy-duty paint. The mechanical trap was replaced with a large sized and capacity one (1 inch to 2 inches) with a sight glass and electronic sensor connected to the DCS to ensure the trap was always in service. It was also added to the preventive maintenance plan for mechanical traps, which is checked weekly. MOPCO also replaced the level switch with an advanced high-sensitive type to ensure accuracy, replaced the journal bearing NDE side with a new pad and replaced the entire HP rotor.
Hydrogen plant relief line failure
On May 7, 2010, a relief line piping failure associated with the low temperature shift converter (LTSC) in Chevron’s Pascagoula refinery occurred. This event happened during a shutdown of the hydrogen plant to address mechanical issues with the gas turbine downstream of the LTSC. To maintain temperatures in the LTSC and shorten startup duration, the startup line was used to vent the heat-up gas to relief downstream of the reactor. The line failure was attributed to fatigue caused by an unusual failure mechanism; acoustic-induced vibration due to the line not being designed for the full gas flow rate. This event highlights the importance of having and following well-written procedures, recognising and mitigating risk, and completing thorough risk assessments through the management of change process.
The operator training program was updated to include acoustic induced vibration awareness and the risk associated with venting full process flow through atypical vent locations. Cautions were added to the normal startup and shutdown procedures to warn against routing full process flow through these vent lines. These lines were also locked closed (due to the low frequency of these valves being used) and tagged with the same warning.
Unprecedented catalyst migration problem
In August 2021, the 2,000 t/d ammonia plant of Petrokimia Gresik in Indonesia experienced an increasing pressure drop on the synthesis loop, from 6.3 kg/cm2 to 8 kg/cm2 . Ammonia converter basket breakdown was causing unprecedented catalyst migration to some synthesis-loop equipment and increasing pressure drop, most notably on the unitised chiller tube annulus. The plant rate was reduced to 75% and at risk of getting lower than the turn-down rate. The ammonia converter basket was then repaired, and many methods and efforts were made to remove the migrated catalyst from the equipment, especially the chiller tube annulus.
Much effort was required to remove the catalyst trapped in the annulus of the unitised chiller. The most effective method after several attempts was a combination of water circulation with air blowing using an air compressor. Limited cleaning access for the synthesis loop heat exchangers caused residual catalysts to remain in the dead-zone area. This residual catalyst could migrate to downstream equipment and cause further blockages. Good teamwork between the operations team, process engineers, and maintenance team was the key to successfully achieving rapid fabrication of the cone strainer and its smooth installation. Close monitoring of the delta pressure cone strainer is necessary to determine the program for cleaning the strainer as soon as needed. mitigation for catalyst migration of ammonia converter to downstream equipment should be provided for the new ammonia plant.
Next year’s Symposium will be in San Diego, CA, USA, on 8-12 September 2024.