Sulphur 408 Sept-Oct 2023
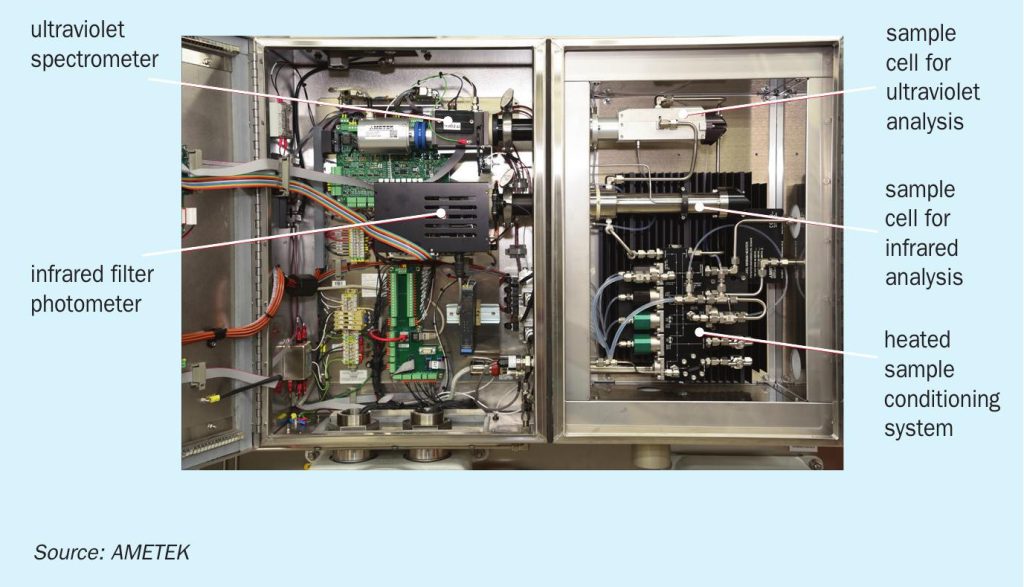
30 September 2023
Keep your sulphur recovery unit online and efficient
Worldwide, there are more than 2,500 individual sulphur recovery units (SRUs) installed, predominantly at refineries and natural gas processing facilities. Given the stoichiometric nature of the H2 S conversion to elemental sulphur in every SRU, the precise and quick control of the combustion air to the main burner is key to maintaining high sulphur recovery efficiencies (SRE) and low SO2 emissions. This is particularly challenging when the compositions of the acid gases feeding the SRU changes, as it can lead to increased SO2 emissions and negatively impact refinery/gas plant throughput. Especially in refineries dealing with two acid gas streams, amine acid gas (AAG) and sour water acid gas (SWAG), with the SWAG typically experiencing more hydrocarbon carry-over events, the impact can be more pronounced.
With the emerging greater application of bio feedstocks in refineries, whether through full conversion or co-processing, there is a growing need to improve prediction and better control the emissions from SRUs. The introduction of bio feedstocks is leading to requirements to operate SRUs at much lower capacities than originally designed and with almost continuously fluctuating acid gas compositions. These changes have a detrimental effect on the ability to control the SRU with fixed air-to-acid-gas-ratios and feed-back correction from the tail gas analyser. Consequently, there is a higher risk of upsets in the SRU, which could potentially result in environmental violations.
In addition, there is an increasing emphasis on decarbonisation and sustainability within the refining industry, leading to a shift in the approach to maintaining emission standards. The inability to properly maintain the air demand of an SRU during upsets can result in higher fuel gas demands and shorter operating windows, which all can be reported as a larger CO2 footprint. It is therefore essential to maintain stable operation in an SRU and to avoid unplanned shutdown and restart events.
In gas plants, a noticeable trend is the reduction of H2 S concentration in the acid gas due to the depletion of the wells feeding the plants. As a result, meeting sulphur recovery efficiency requirements may become more challenging. This places greater importance on ensuring tight control of the unit’s air demand to address this potential challenge effectively.
Conventional SRU control and Comprimo’s ABC
Comprimo’s Advanced Burner Control (ABC) and conventional SRU control both manage feed gas flow rate variations via feedforward ratio control, but not in the same way. Conventional SRU control uses the main and trim air valves fully independently; the main air valve is controlled in direct ratio to the SRU feed gas flow, while the trim air valve is only controlled by the tail gas quality controller. Some variations of this philosophy may exist in the industry, such as tying the trim air control valve to the sour water acid gas supply, but the fundamental principle remains the same – each valve acts independently. The drawbacks of this strategy, such as slow and inaccurate feed gas ratio control via the main air valve and limited tail gas quality control capacity via the trim air valve, are overcome by the different strategy Comprimo’s ABC applies.
ABC controls both the main and trim air valves simultaneously and utilises each valve’s specific strength in the best manner; it provides rapid and accurate total air response to any change in acid gas feed flow rates combined with enough tail gas quality control capacity. While the total air flow controller manipulates the small (thus rapid) and accurate trim air valve in response to any air demand change, the main air valve is continuously adjusted to ensure that the trim air valve stays within its operating capacity. Shortly after that response has been provided, the trim air valve returns to its optimal position to wait for new air demand changes.
If no measures are taken, as in conventional SRU control, the air flow response is non-linear in an SRU, especially for main air control. ABC takes this into account using proprietary functions to establish linear responses at any plant load and repositions the trim air valve to its optimal position. Where conventional SRU control uses separate main and trim air flow transmitters, ABC utilises only a common air flow transmitter, thereby reducing engineering, hardware, and maintenance costs, while providing a more accurate combustion air flow. Ultimately, ABC outperforms conventional SRU control in maximising sulphur recovery efficiency through its superior tail gas quality control optimisation.
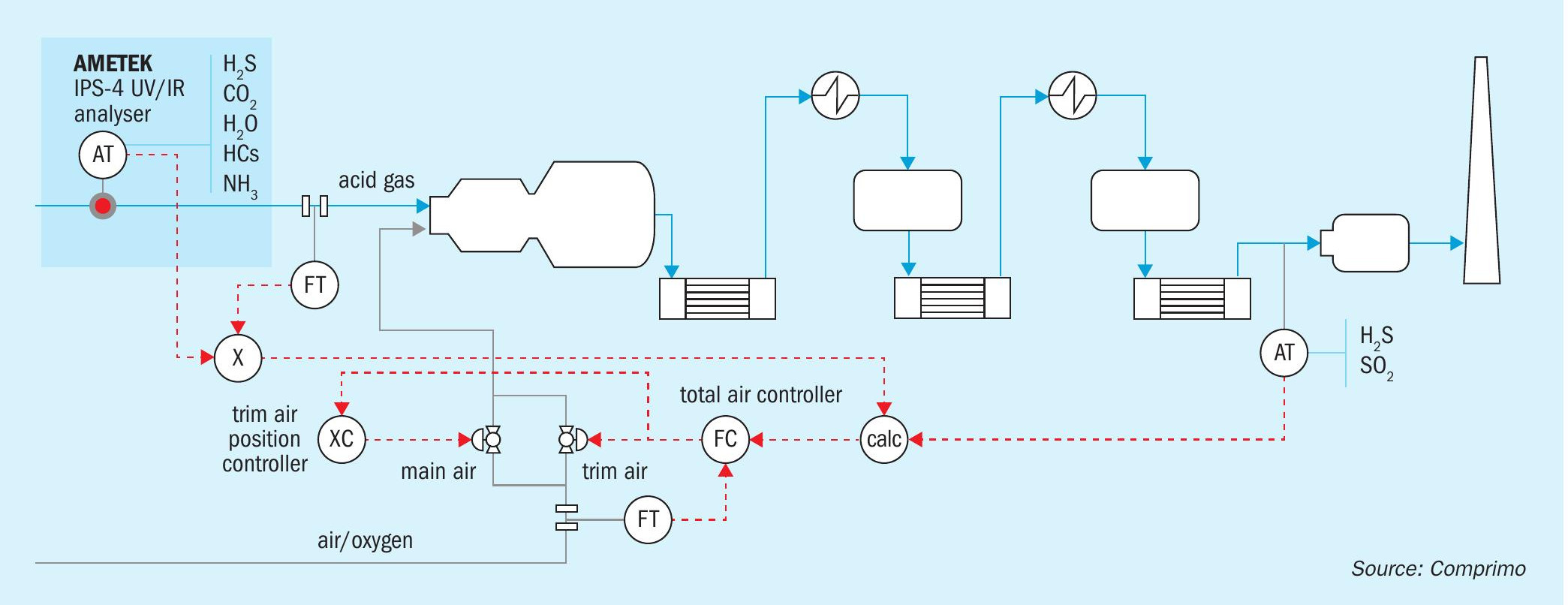
2ACT™ Solution
Although Comprimo’s ABC is an important improvement over conventional SRU control, it still lacks the ability to react to rapid changes in feed gas composition. The feed-forward part of both ABC and a conventional combustion air control system takes the acid gas flow rate into consideration, but not its composition. Both ABC and the standard control designs rely solely on feed-back from a tail gas analyser that is typically located after two or three Claus stages. As a result, there is a significant time delay between a change in feed at the front end of the system and its subsequent impact to the tail gas.
The 2ACT Solution, represented in Fig. 1, addresses this problem by enhancing ABC with the addition of an AMETEK IPS-4 UV/IR analyser upstream of the SRU. This analyser monitors all the acid gas feed components (H2 S, CO2 , H2 O, hydrocarbons, NH3 ) by continuously sampling the acid gas. This revolutionary development determines and uses dynamic air-to-acid-gas-ratios and improves the existing feed gas flow compensation by adding molecular weight compensation to precisely provide the required air supply to the SRU main burner. As a result, the required combustion air quantity to the SRU main burner is continuously calculated within seconds and adjusted through ABC, in direct response to all possible changes the feed gas can encounter, such as flow, temperature, pressure and composition. This results in a more accurate air-to-acidgas-ratio control and improved SRU control robustness. For a typical SRU, this means that the impact of changing acid gas compositions can be managed up to 6-7 minutes quicker with the 2ACT Solution.
The 2ACT Solution, formerly known as ABC+, has undergone further developments to simplify the probe and sample conditioning system, overall analyser integration and system safeguarding, leading to its rebranding.
With the implementation of the 2ACT Solution, the SRU achieves exceptionally stable control without requiring any operator intervention, even in the following scenarios, based on actual 2ACT Solution installations:
- Hydrocarbons carry-over at a rate of:
– 2.0 mol-% total hydrocarbons (CH4 equivalent) per 10 seconds
– 2.8 mol-% total hydrocarbons (C4 H10 equivalent) per minute
- H2 S and CO2 acid gas concentration changes of 15 mol-% at a rate of 4.0 mol-% per minute
- Changes in air demand (air-to-acid-gasratio) of 10–15% within seconds.
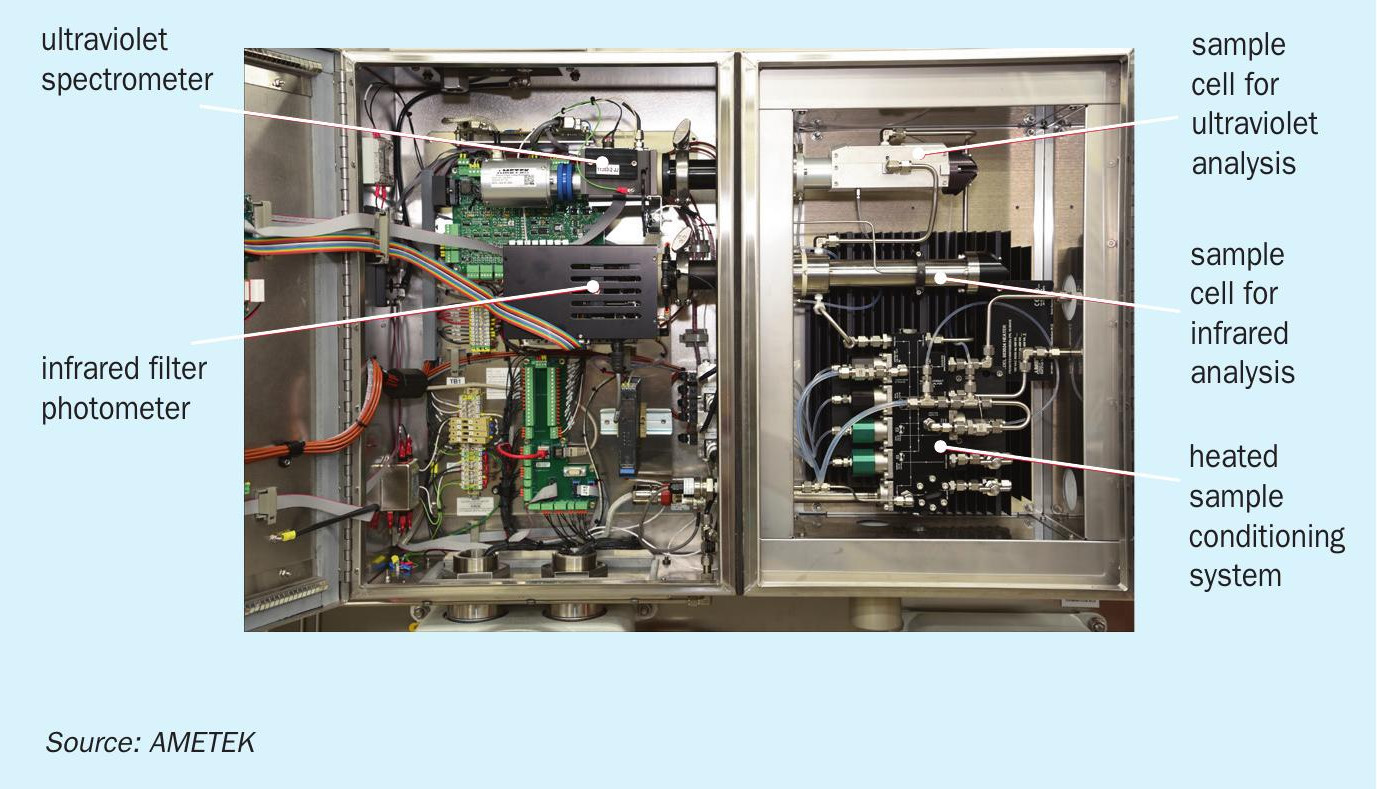
AMETEK IPS-4 acid gas feed analyser and HAG probe
The AMETEK IPS-4 analyser, shown in Fig. 2, is a built for purpose analyser for the 2ACT Solution. It uses two technologies to measure the key components in acid gas streams in a single analyser, without cross-interference. The ultraviolet spectrum is used to measure H2 S and NH3 and the infrared spectrum is used to measure CO2 , H2 O, total hydrocarbons (THC) and also NH3 . Each analyser is configured to automatically zero the analyser by flushing the measuring cell with nitrogen. The analyser can be manually spanned if required with calibration gases.
The IPS-4 acid gas feed analyser is installed with a heated acid gas (HAG) sampling probe. The HAG probe is a fully integrated, electrically heated sample handling probe assembly designed for this purpose. It is equipped with double block integrated shut-off valves that allow servicing without removal from the process. The probe has a serviceable membrane filter to capture entrained liquid. The probe (and sample line) is temperature controlled to ensure that no sample condensation occurs which is key to reliable gas composition measurement. High and low temperature alarms are incorporated for the probe and the sample line.
The HAG Probe provides the motive force required to circulate the sample through the analyser system and only requires a single process tie-in point/ connection. Preferably nitrogen is used to drive the built-in aspirator.
Ideally, the sample probe is installed as far upstream from the SRU main burner as possible, where it can accurately sample the acid gas stream compositions that are processed in the SRU. Typical locations for the sample probe are anywhere downstream of the amine regenerator and sour water stripper reflux drums. Another option, but less favourable, is downstream of the knock-out drums.
Field results from case studies
Over the last 15 years, Comprimo has designed and implemented the 2ACT Solution for 14 SRUs around the world, in both refineries and gas plants, in brownfield revamps as well as greenfield projects.
In this section, three case studies are presented showing the performance of the 2ACT Solution during process disturbances, for a refinery SRU and two gas plant SRUs.
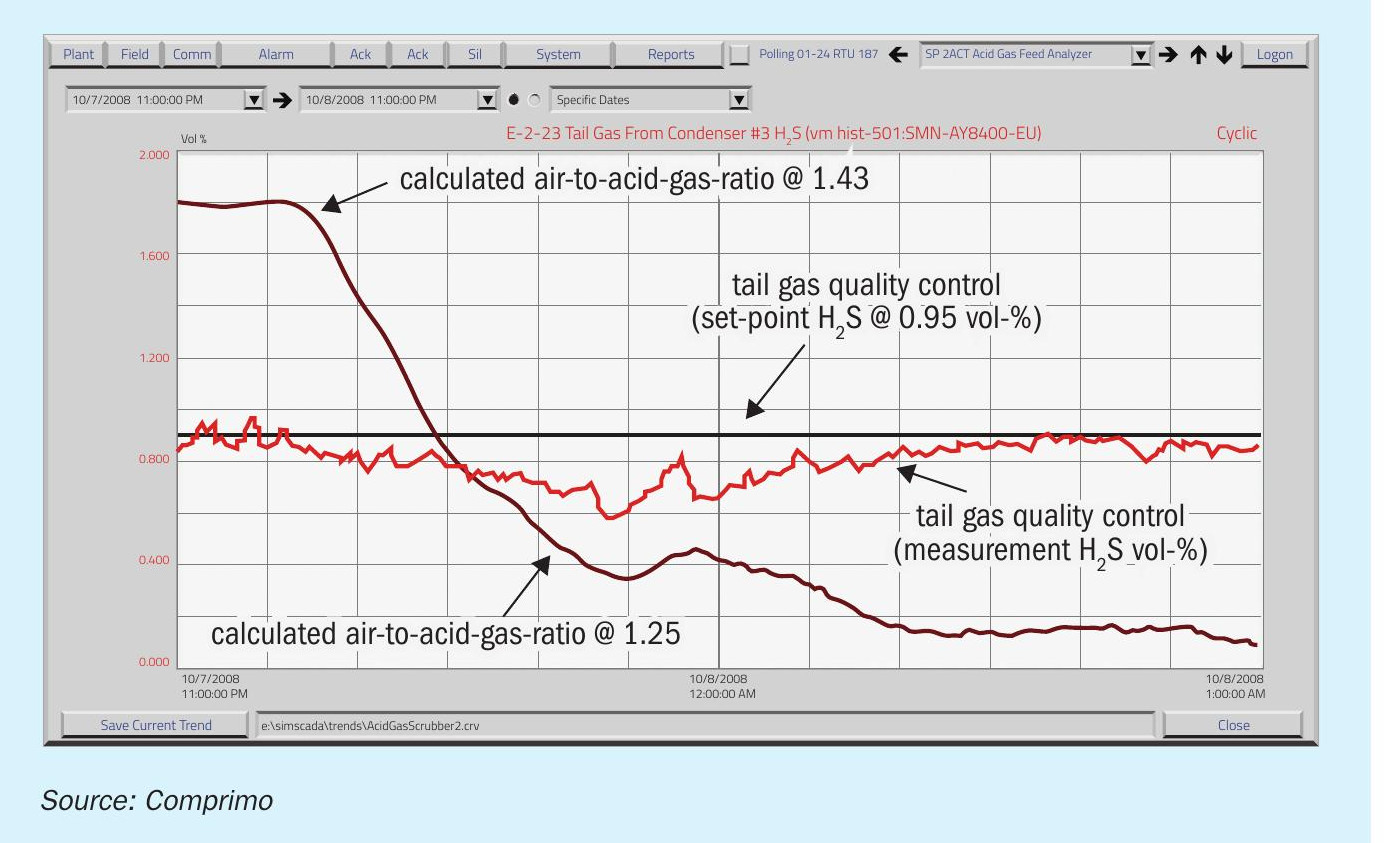
Case study 1
Gas plant: 2+1 SUPERCLAUS® – one single train
The initial version of the 2ACT Solution (formerly known as ABC+) was installed at the Simonette gas plant in Alberta, Canada in 2008 and operated successfully for ten years until the SRU (two Claus reactors followed by a SUPERCLAUS® reactor) was decommissioned in 2018 as part of the conversion to acid gas injection. The Simonette gas plant was an example of a challenging SRU control application. The plant processed gas from over 65 wells using four main pipelines, including one as long as 110 km. In the various raw feed gas streams, the H2 S content ranged from 2% to 16%.
To recreate process disturbances, during the first week of start-up after the 2ACT Solution went online, tests were carried out by purposely creating changes in the acid gas feed composition. These changes in H2 S, CO2 and THC content were obtained by shutting down or introducing variant raw gases to the plant.
A frequently occurring change in acid gas composition was caused by the exclusion of raw gas with high H2 S concentration (approx. 16%), which was caused by pigging of pipelines or compressor station failures. A change in H2 S content in the acid gas from 65% to 50% in about 30 minutes was a very common occurrence, in combination with changes in flow rate and THC.
Before implementing the 2ACT Solution, this phenomenon caused frequent SUPERCLAUS® reactor bypass trips due to high H2 S resulting in SRE losses and noncompliance with regulatory SO2 emission requirements. Panel operators were unable to efficiently determine the precise timing or the amplitude of the upset to be expected, and thus could not take countermeasures.
The control response of the 2ACT Solution to this commonly occurring change in acid gas composition is illustrated in Fig. 3. It can be seen that the H2 S concentration in the tail gas (red line) stays very close to the set-point at 0.95 vol-%, (straight black line) even though the air-to-amine-acid-gas-ratio (brown line) is changing significantly and rapidly from 1.43 to 1.25. This is equal to a change in air demand of 13%. It should be noted that the time involved in the process to shut off the incoming pipeline is quite different than the time required to open it again (24 minutes versus 6 minutes); during both events the control system managed to control the tail gas quality, without initiating a high or low DCS alarm, let alone activating the high high H2 S trip.
Another change in acid gas composition was obtained by introducing natural gas to the upstream amine regenerator. The THC content in the acid gas feed was increased from 0.9 vol-% to 2.9 vol-% within ten seconds which is illustrated in Fig. 4. As a result, the calculated air-to-acid-gas-ratio immediately showed a significant increase in air demand of 9%. After an initial modest H2 S concentration spike at the tail gas analyser, the response of the control system was very satisfactory as within several minutes the H2 S concentration returned to its set-point. Also at the reverse upset, where THC content was rapidly decreased again, an identical response was observed. Conventional control systems are not able to respond to these changes adequately and timely. In fact, a hydrocarbon carry-over of this magnitude would cause major upsets causing acid gas flaring and emission violations.
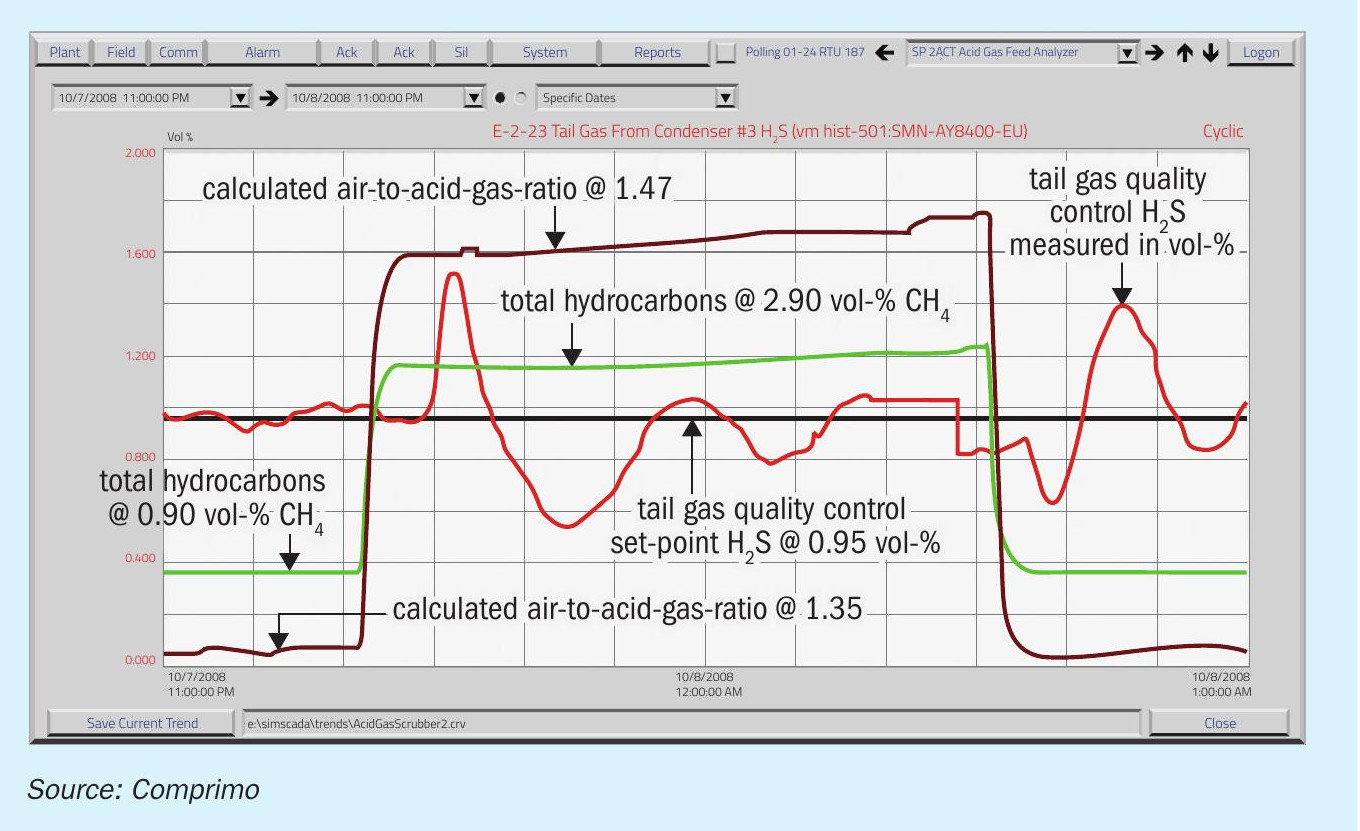
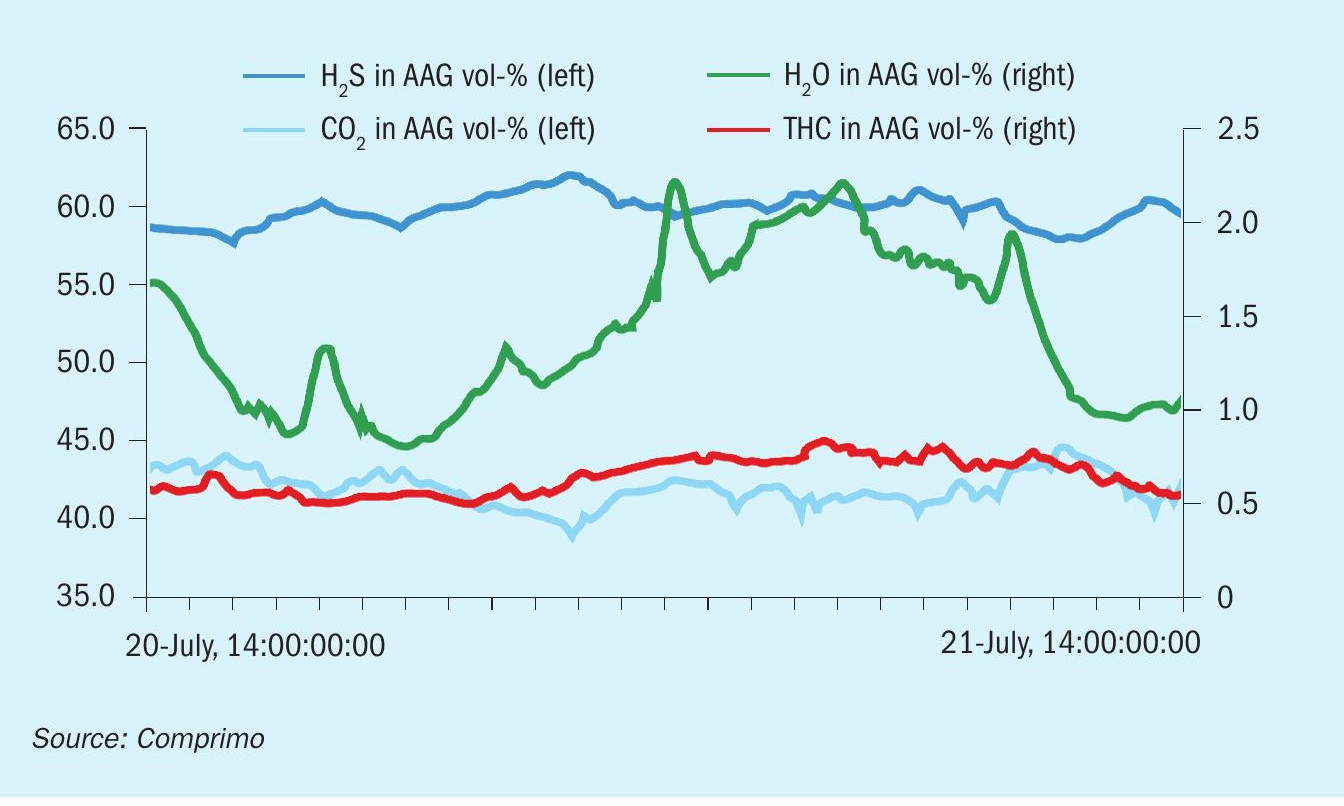
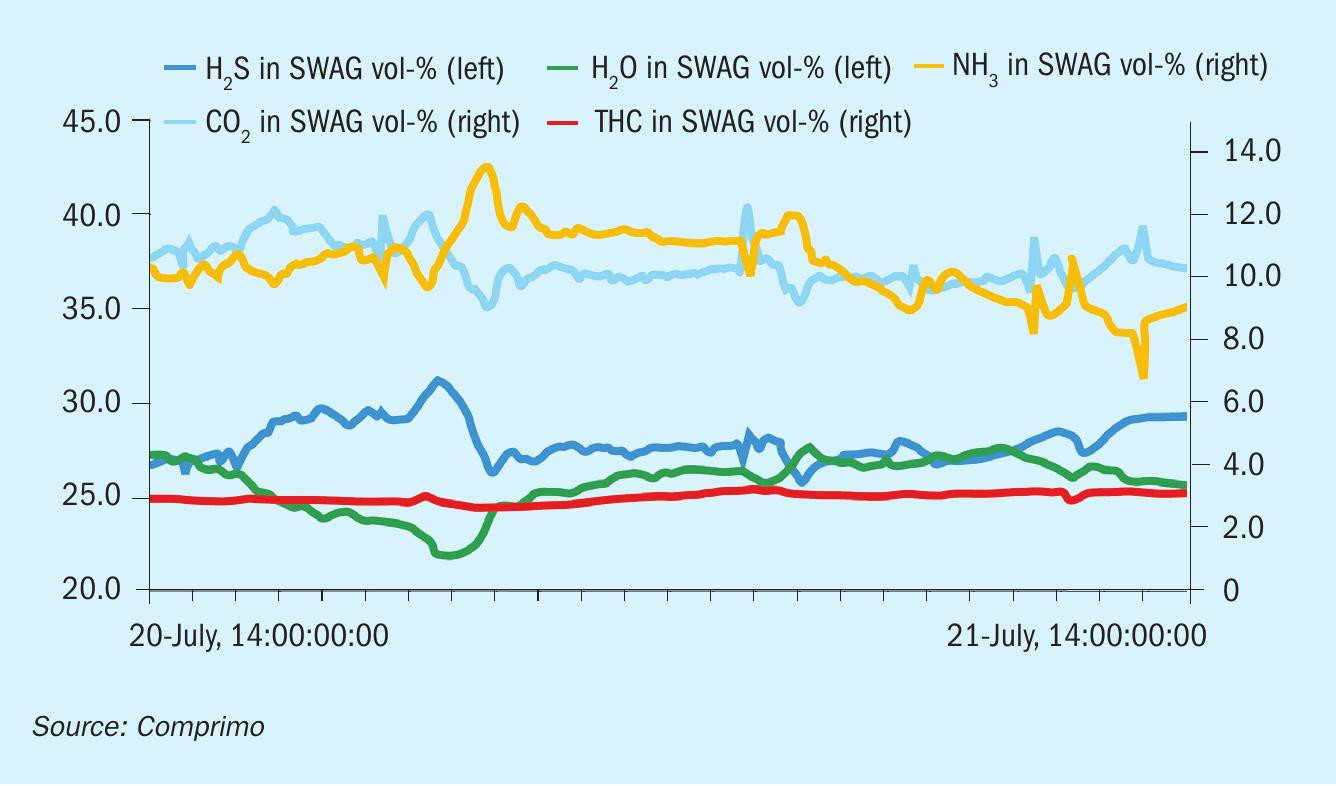
Case study 2
Refinery: 3+1 EUROCLAUS® – two trains
The first 2ACT Solution at a refinery was implemented in 2013 in the United Kingdom for two identical parallel SRUs. Both SRUs are based on Comprimo’s EUROCLAUS® technology with two Claus reactors and a hydrogenation reactor, followed by a common selective oxidation reactor. The two SRUs are fed with amine acid gas (AAG) from two parallel amine regeneration units (ARU) and sour water acid gas (SWAG) from a sour water stripper unit (SWSU), fed by a fluid catalytic cracker unit (FCCU). The tail gas from the hydrogenation reactors is routed to the common selective oxidation reactor.
The customer’s expectations were met when the 2ACT Solution was implemented, showing very precise and stable tail gas H2 S control at set-point +/0.05 vol-%. The 2ACT Solution has been running with excellent online time (> 95%) and satisfactory performance for both AAG and SWAG for ten years.
The following figures, captured on one specific day of operation (July 20, 2014), show three trends indicating important operating variables. The variations in acid gas composition measured by both AAG and SWAG feed-forward analysers are depicted in figs 5 and 6, followed by Fig. 7, which shows the variations in AAG, SWAG and O2 flow, together with the tail gas H2 S concentration.
Despite all sorts of fluctuations in AAG and SWAG feed composition (particularly for H2 S, CO2 , NH3 and water) and flow, the 2ACT Solution manages to maintain the tail gas H2 S concentration in a narrow bandwidth around the optimum tail gas operating set-point of 0.58 vol-% H2 S. This installation shows that the 2ACT Solution provides high SRE as well as high online reliability for SRUs in refinery applications.
Case study 3
Gas plant: 2 Claus + 2 CBA – two trains In 2020 the 2ACT Solution was implemented in a gas plant in Texas with two identical SRUs consisting each of two Claus reactors followed by two Cold Bed Absorption (CBA) reactors. The gas plant is part of an enhanced oil recovery (EOR) asset. The required SRE for the facility was set to increase in 2020, and the plant preferred to avoid the installation of a high capital investment new tail gas treating unit (TGTU). In order to meet the new SRE requirements, the customer was therefore interested in implementing the 2ACT Solution to improve the controllability of the facility, to improve the SRE and decrease SO2 emissions.
As part of the optimisation project, a new AMETEK IPS-4 acid gas feed analyser was installed at the outlet of the acid gas KO drum in each SRU. To integrate the 2ACT Solution the existing air control system was modified, in order for the on-line measured acid gas composition to be used to automatically calculate and modify the air-to-acidgas-ratio. The 2ACT Solution went online in 2020 and shortly after, tests were carried out by fully opening and fully closing the acid gas feed from one of the upstream units to one of SRUs, purposely creating changes in the acid gas feed composition.
Fig. 8 shows the performance of the 2ACT Solution to the compositional changes in the acid gas feed to the SRU during one of the process upsets. The H2 S concentration increased at a rate of 4.4 mol-% per minute, while the CO2 concentration and the THC content decreased at rates of 3.7 mol-% and 0.82 mol-% per minute, respectively. The 2ACT Solution responded rapidly decreasing the air demand by 7.6%, to maintain the tail gas H2 S – 2SO2 process value in a narrow bandwidth around its set-point of 0.2 vol-%.
This facility was able to meet the required sulphur recovery efficiency of 98.8+% on a continuous and long-term basis with this improvement of the SRU air control system. The 2ACT Solution provided a low-cost solution and prevented significant capital investment for a new TGTU to meet regulatory SO2 emission requirements.
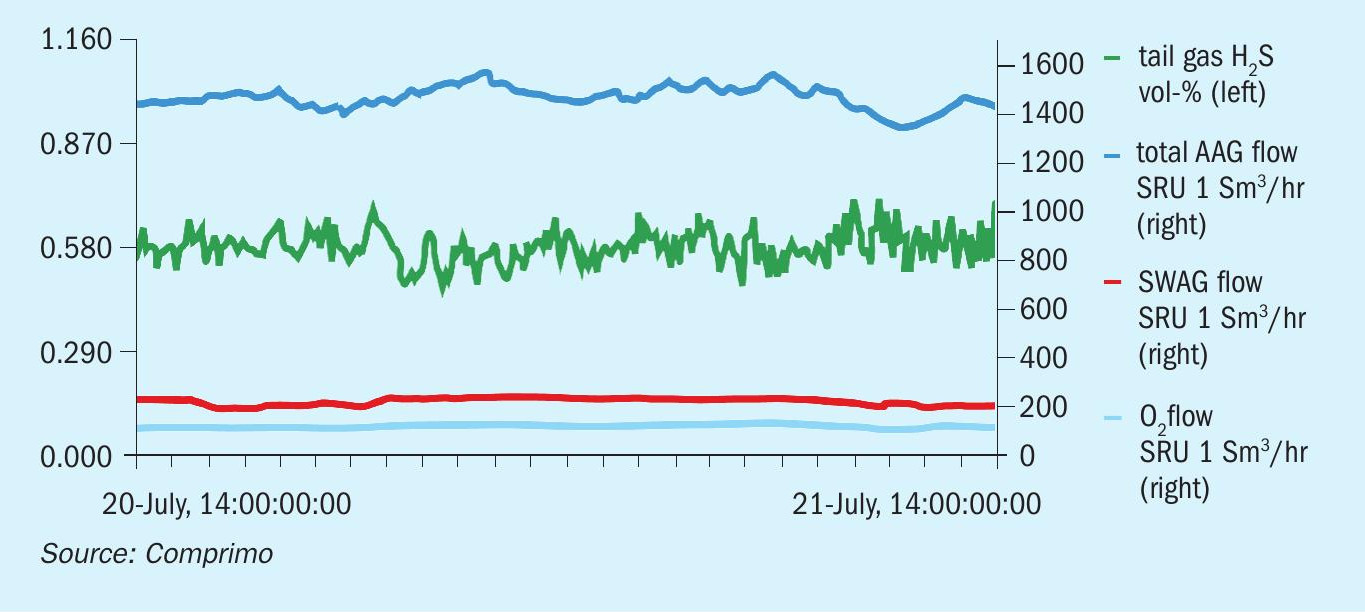

Conclusions
There are a multitude of different Claus based technologies that are being used in sulphur recovery units to meet specific emission targets. One commonality between all the technologies is that good control of the air demand is essential for minimising emissions as well as to protect the process from upsets. This may include SO2 breakthroughs in amine-based tail gas units that can lead to fouling and reduced performance and on-line availability of the system. With the tail gas analyser at the back of the unit, conventional control systems are unable to respond adequately and promptly to changes in feed compositions.
By implementing SRU air control based on acid gas composition measurement, such as with the 2ACT Solution, the impact of fluctuating acid gas feed compositions can be greatly reduced. The 2ACT Solution is a complete low-cost solution and by preventing even one SRU upset that would result in reduced gas plant/refinery throughput it can provide an immediate return on investment. The various installations in both refinery and gas plant applications globally, illustrate that the following benefits can be expected from its installation:
- reduced SO2 emissions and prevention of SRU incinerator stack regulatory SO2 violations;
- protection of TGTU catalyst, quench system and amine system;
- prevention of unplanned downtime or reduced throughput;
- closer operation to SRU nameplate capacity;
- reduced flaring; l less operator intervention required;
- safer, easier and faster SRU start-up as typically the acid gas composition is not known during start-up;
- instantaneous monitoring of varying AAG and SWAG feedstocks including varying co-processing rates and ratios of potential future bio-feedstocks for operational confidence and troubleshooting or debottlenecking of the SRU.
References