Sulphur 409 Nov-Dec 2023
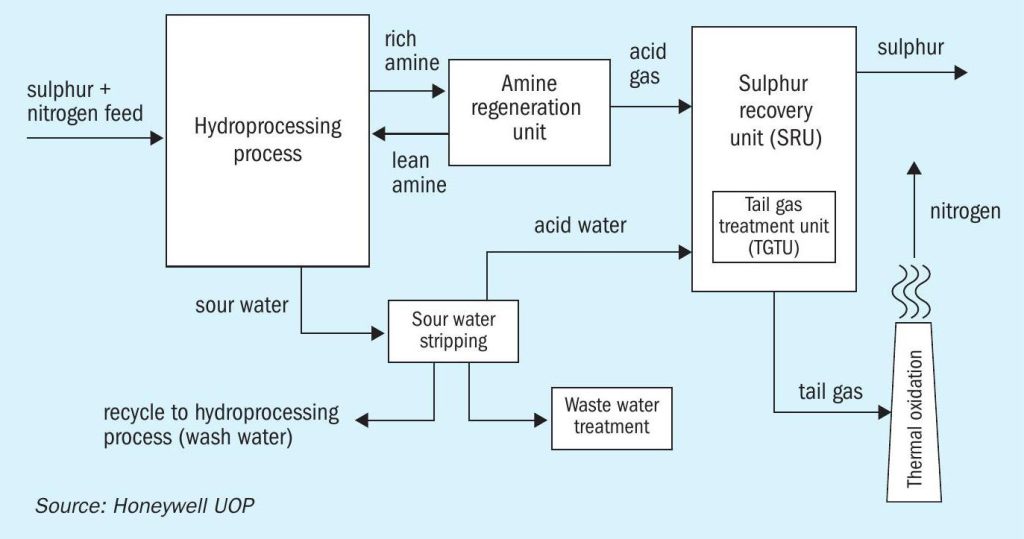
30 November 2023
Optimising refinery assets with fertilizer production
HYDROPROCESSING WASTE TREATMENT
Optimising refinery assets with fertilizer production
Honeywell UOP’s nViro Hydro process provides an alternative solution to conventional hydroprocessing waste treatment utilising a sulphur recovery unit and tail gas treating unit. Janet Ruettiger of Honeywell UOP discusses the benefits of nViro Hydro which include improved operational efficiency, creating a new revenue stream and reduced capital outlays, operating expenses and water use.
Refineries are major long-term investments that operate over many years spanning decades. As technology, consumer needs, product values, and environmental regulations evolve, refineries adapt. In today’s economy and environment, refiners must account for not only every dollar spent, but also consider whether they are making the best use of every molecule at their disposal.
Hydroprocessing complexes are a critical component of almost any refinery. Hydrotreating reactions remove sulphur and nitrogen contaminants from hydrocarbon feedstocks to produce clean fuels and petrochemical feedstocks, and hydrocracking reactions break long-chain hydrocarbons into smaller chains to increase the yield of valuable products. Flexibility to increase feed throughput and/or feed quality in their hydroprocessing unit(s) can help refiners maintain profitability, meet changing production targets, manage variation in feedstock supply and/or offset the shutdown of obsolete assets.
If constraints are met in the current hydroprocessing design, incremental advances in technology (i.e., higher activity catalyst, slimmer reactor internals, etc.) are typically implemented during turnarounds to optimise and relieve constraints. However, the combination of throughput increases, feedstock changes, and tightening emission specifications can create an effluent treatment bottleneck in refineries, putting a strain on existing sulphur recovery and wastewater treatment sections.
The proprietary UOP nViro™ Hydro solution provides an alternate waste management solution for green-field or brown-field hydroprocessing complexes. Compared to the conventional treatment processes, nViro Hydro can improve operational efficiency, create a new revenue stream, and reduce capital outlays, and operating expenses1 .
Conventional sulphur recovery scheme
A simplified conventional scheme for hydro-processing waste treatment (Fig. 1) utilises a sulphur recovery unit (SRU) and a tail gas treating unit (TGTU) to convert hydrogen sulphide (H2 S) to elemental sulphur. From these processes the elemental sulphur is collected and can be sold as a commodity. In the conventional scheme, the ammonia (NH3 ) waste travels with the H2 S through the SRU and is eventually released into the atmosphere after being converted into N2 and/or NOx. Not only is the value of the NH3 not captured in this scheme, but the NH3 takes up useful capacity in the SRU, limiting optimisation. While the conventional scheme mentioned earlier includes tail gas treatment, the requirement for tail gas treatment varies regionally based on emission regulations. Some refiners may operate without tail gas treatment, while others may be facing mandatory capital expenditures to comply with regulations and maintain operation.
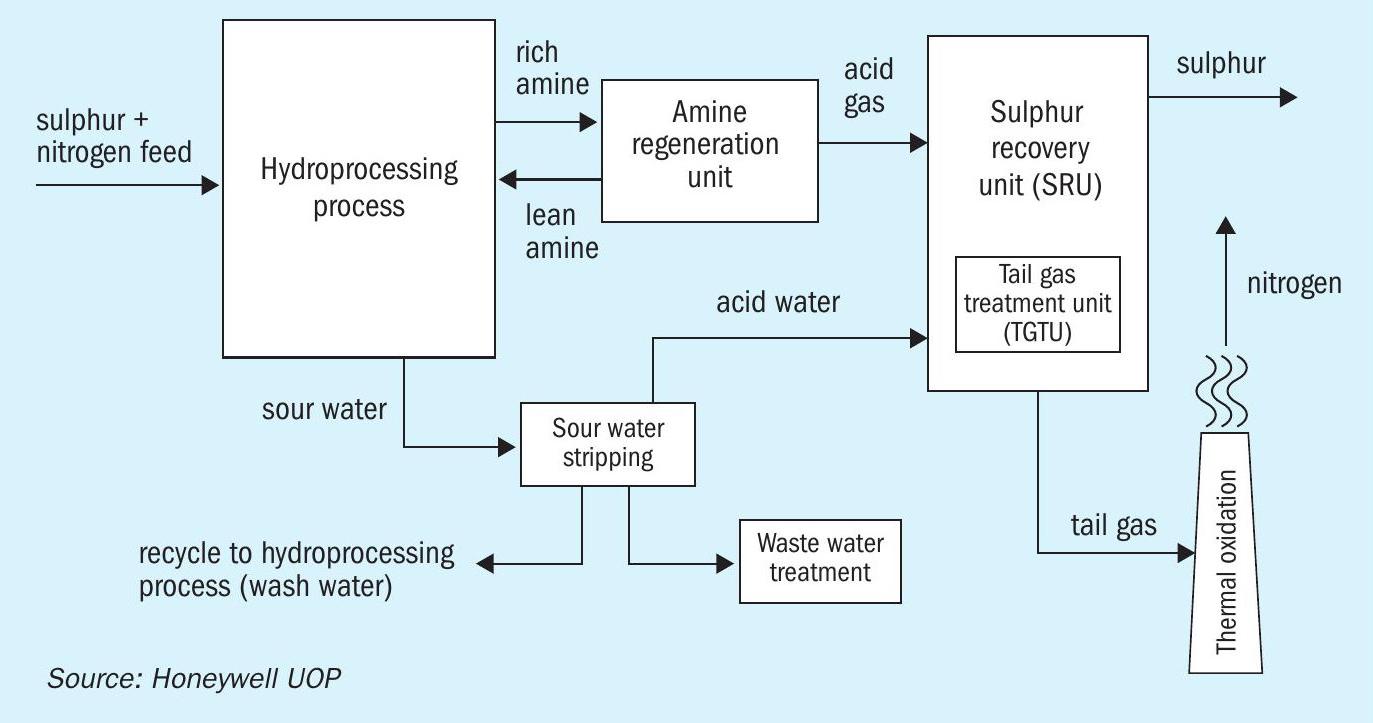
nViro Hydro: Sulphur (and nitrogen) recovery solution
The UOP nViro Hydro solution (Fig. 2), is a proprietary process for the treatment of acid gas and sour water from a hydroprocessing complex and offers an alternative approach to conventional sulphur recovery. nViro Hydro can be implemented in new complexes at a lower capital cost than the conventional scheme (with TGTU)1 , or it can be added to an existing complex (utilising the existing SRU to limit capex) as a tool to relieve optimisation limiting constraints or as an alternative to the addition of a TGTU to meet emission specifications.
In the nViro Hydro process, the main waste products, hydrogen sulphide and ammonia, are upgraded into a combination of both elemental sulphur and ammonium sulphate ((NH4 )2 SO4 ), a chemical that is commonly blended as an ingredient in multi-nutrient NPKS fertilizer blends.
Utilisation of waste ammonia to produce ammonium sulphate with the nViro Hydro process allows for a number of economic, operational and environmental benefits beyond what is capable with a conventional sulphur recovery scheme1 .
Economic and environmental value of ammonia
Ammonia is a key ingredient in the production of ammonium sulphate and other ammonia-based fertilizers. Utilising waste ammonia optimises the treatment process from both an economic and environmental perspective. Ammonia is both economically valuable ($270-$354/t in July 2023 for grey ammonia)2 and CO2 intensive to produce. The most predominant production method of ammonia, the Haber Bosch process, produces between 2.3 and 5.2 tonne CO2 per equivalent tonne of NH3 depending on the region of production and efficiency3 . Less CO2 intensive ammonia production methods, such as blue and green ammonia, are available, but come at a premium ($299-384/t and $750-$799/t for blue and green ammonia in July 2023)2 . Leveraging of waste ammonia in the nViro Hydro solution gives refiners an advantage relative to other ammonium sulphate production methods.
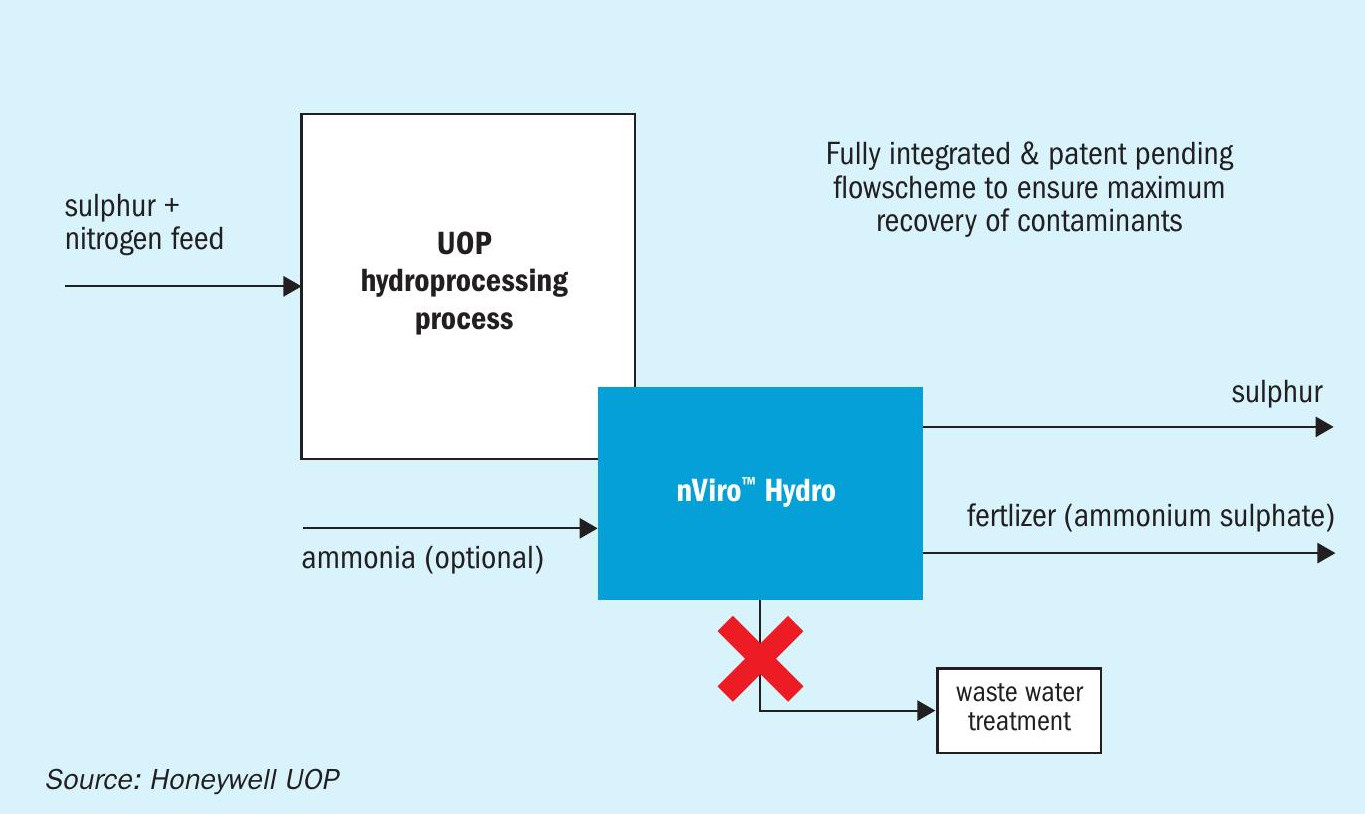
Ammonium sulphate as a profit increasing byproduct
The value of ammonium sulphate production from nViro Hydro compared to the conventional solution depends on the relative pricing of ammonium sulphate versus sulphur. The chemistry of ammonium sulphate production gives nViro Hydro an economic advantage over sulphur production, multiplying the yield of ammonium sulphate by nearly 5 times the amount of sulphur that is converted on a mass basis due to the mass of the ammonia and oxygen in the ammonium sulphate molecule4 .
This results in an increase in total product value from nViro Hydro relative to conventional sulphur recovery, with contributions from both increased yield of byproducts and the fact that ammonium sulphate often carries a higher value than elemental sulphur (Fig. 3).
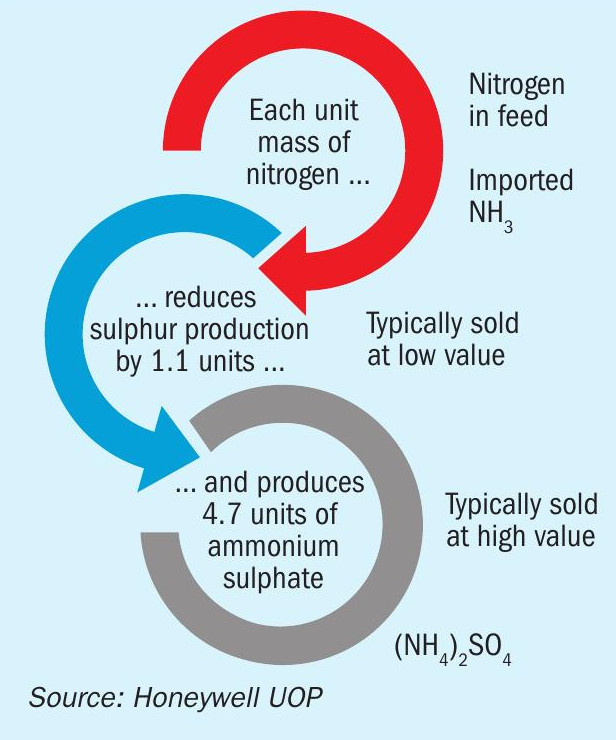
About 50% of global elemental sulphur recovered ends up in fertilizers anyway, including phosphates and ammonium sulphate, but via a more arduous and less efficient route with multiple conversion processes5 .
The ammonium sulphate produced by the nViro Hydro process can be sold directly as a powdered material, or if desired an additional compaction step can be added to the nViro Hydro process which may increase the value of the ammonium sulphate and/or make the product more marketable.
The global demand for ammonium sulphate is expected to grow at a compounded rate of ~2.6% per year through 20276 .
Because feedstocks that are processed in hydroprocessing units, such as vacuum gasoils (VGO), diesels, deasphalted oils (DA)), coker gasoils (CGO), etc. tend to contain orders of magnitude higher feed sulphur than nitrogen, the yield of ammonium sulphate is set by ammonia availability, and elemental sulphur is produced with the remaining H2 S in the sulphur recovery section which remains a significant part of the design1 . In addition to waste ammonia, additional ammonia can be imported to increase ammonium sulphate production, depending on customer objectives.
Debottlenecking existing SRUs
Fertilizer production aside, an nViro Hydro retrofit can be a powerful tool to help refiners free up capacity in their existing assets to allow for better optimisation of their hydroprocessing complex. Refiners facing constraints in their SRU can add nViro Hydro to their complex to facilitate throughput increases with the potential to multiply the profits from their hydroprocessing units. Likewise, feedstock flexibility will increase with additional sulphur recovery capacity. In a hydroprocessing unit, the nViro Hydro system is added to the existing equipment to minimise capital expenditure, and ammonia import is an option that can be explored to increase the range of optimisation or debottlenecking of the SRU.
Another feature of the nViro Hydro system which sets it apart from the conventional sulphur recovery scheme is that it eliminates the requirement for wastewater treatment from the hydroprocessing waste treatment section1 . This can help refiners with constraints around existing wastewater treatment capacity.
Refiners who could otherwise increase their hydroprocessing throughput, if it weren’t for a constraint in their sulphur recovery section, can use nViro Hydro to increase by-product value (which gives a positive NPV and typical payback period of 1-2 years1 ) and increase production of fuels/petrochemicals.
For an even larger impact, nViro Hydro can also be implemented as part of a larger scope project with UOP’s hydroprocessing experts to further optimise feed and throughput in the hydroprocessing unit through adjustments like catalyst, reactor internals and cycle length.
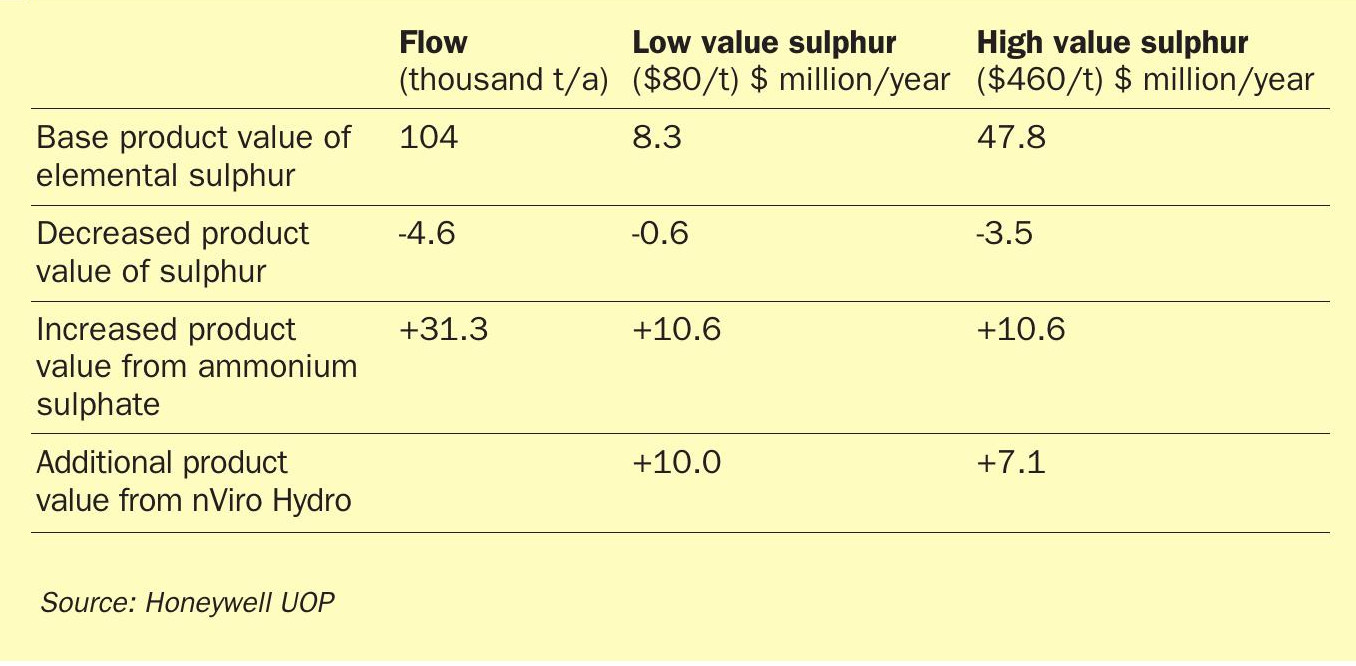
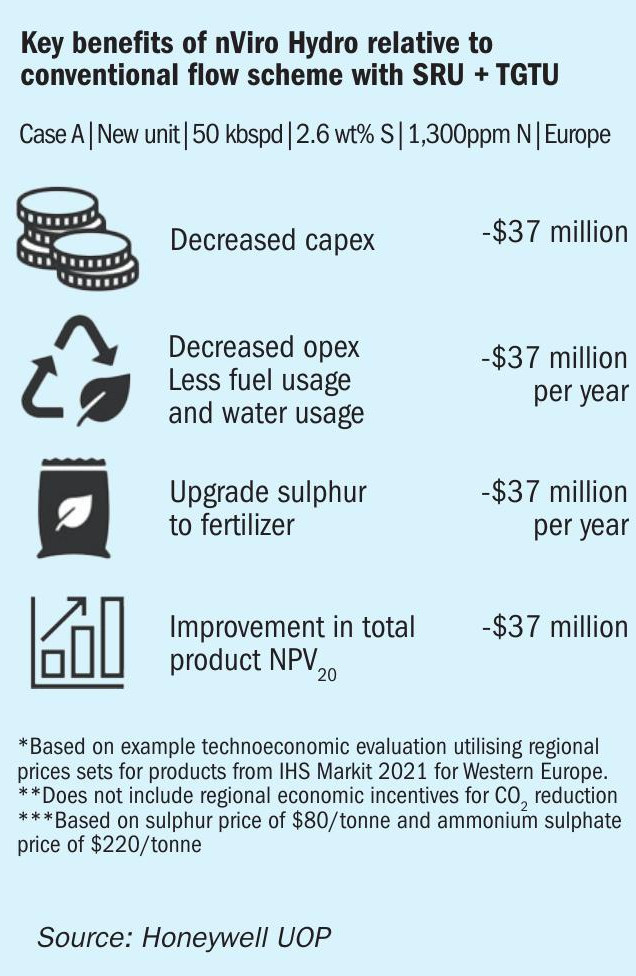
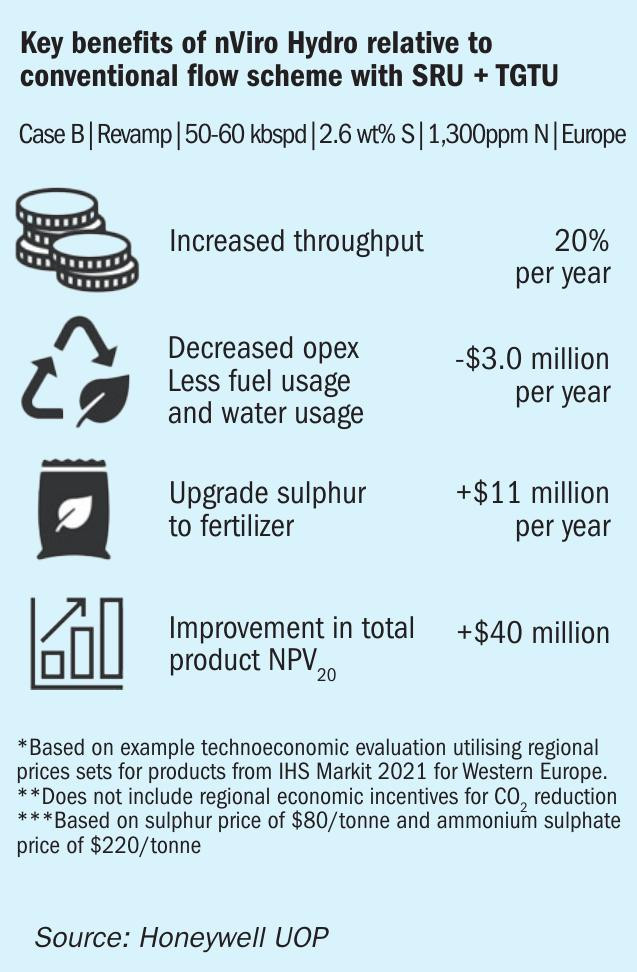
Reduced operating expenses and CO2 footprint
In addition to the aforementioned applications of nViro Hydro, it can also be applied as a pathway to reduce utility consumption, opex and CO2 emissions without an adjustment in the production of fuels or petrochemicals from the complex7 . nViro Hydro reduces the load on the existing SRU, waste water treatment system and eliminates the need for the TGTU. nViro Hydro is also optimised to maximise energy recovery, benefitting both operating expenses from utilities and scope 2 CO2 emissions7 . This will be dependent on each customer’s existing configuration and goals.
Case study A: New hydrocracking complex
In this case study an oil and gas company is building a new hydrocracking unit at one of its existing refineries. The unit is designed to process up to 50,000 barrels of vacuum gasoil (VGO) per stream day. The VGO has a sulphur content of 2.6% and a nitrogen content of 1,300 parts per million by weight. Building the system with nViro Hydro instead of a conventional waste handling system will deliver significant financial benefits8 , which are summarised in (Fig. 4).
Case study B: Existing complex
An oil and gas company hydrocracking unit is currently operating the same feed as case A at the design capacity of 50,000 barrels of VGO per stream day, using a conventional flue-gas treatment scheme. The company wants to use new-generation catalysts with higher activity to increase hydrocracking unit throughput in the next cycle. However, they are constrained by their sulphur recovery unit.
By implementing an nViro Hydro revamp solution on their existing unit, at a cost of $29 million, the company, which was limited in throughput by their SRU will be able to increase hydrocracking throughput by 20% (with some ammonia import) and realise multiple financial and operational benefits9 summarised in (Fig. 5).
Case study C: Sulphur pricing sensitivity
Because the yield of ammonium sulphate is so favourable relative to elemental sulphur production, even in circumstances where the sulphur value becomes very high, product value is still increased with nViro Hydro (see Table 1).
Value creation through problem solving
In order to make the most profit from fertilizer production, logically sites with a significant amount of waste ammonia at locations with strong ammonium sulphate markets are preferred.
However, looking at the bigger picture, the best use case of nViro Hydro is for the refiner to use it as a tool to solve a problem, the impact of which may cascade outside the scope of waste treatment:
- to remove a sulphur recovery constraint to increase feed throughput and fuel yield 9 ;
- to comply with new emission specifications without a TGTU (with positive NPV) 1 ;
- to reduce Scope 2 CO 2 emissions without reducing fuel yield (with positive NPV) 7 ;
- to reduce demand on wastewater treatment (to enable plant optimisation) 1 ;
- to help meet regional fertilizer demand/ reduce reliance on imports.
References