Sulphur 390 Sept-Oct 2020
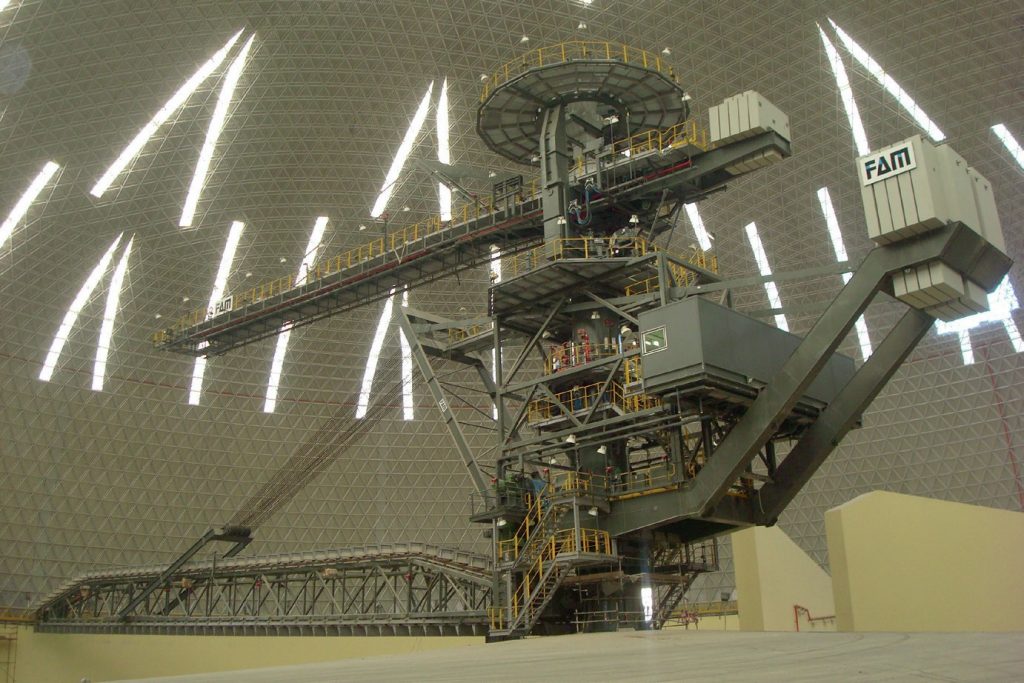
30 September 2020
Abu Dhabi: sulphur giant
ABU DHABI
Abu Dhabi: sulphur giant
In a few short years Abu Dhabi has grown to become the world’s largest sulphur producer and exporter, and new sour gas projects will lead to additional sulphur recovery capacity, provided they can overcome economic challenges.
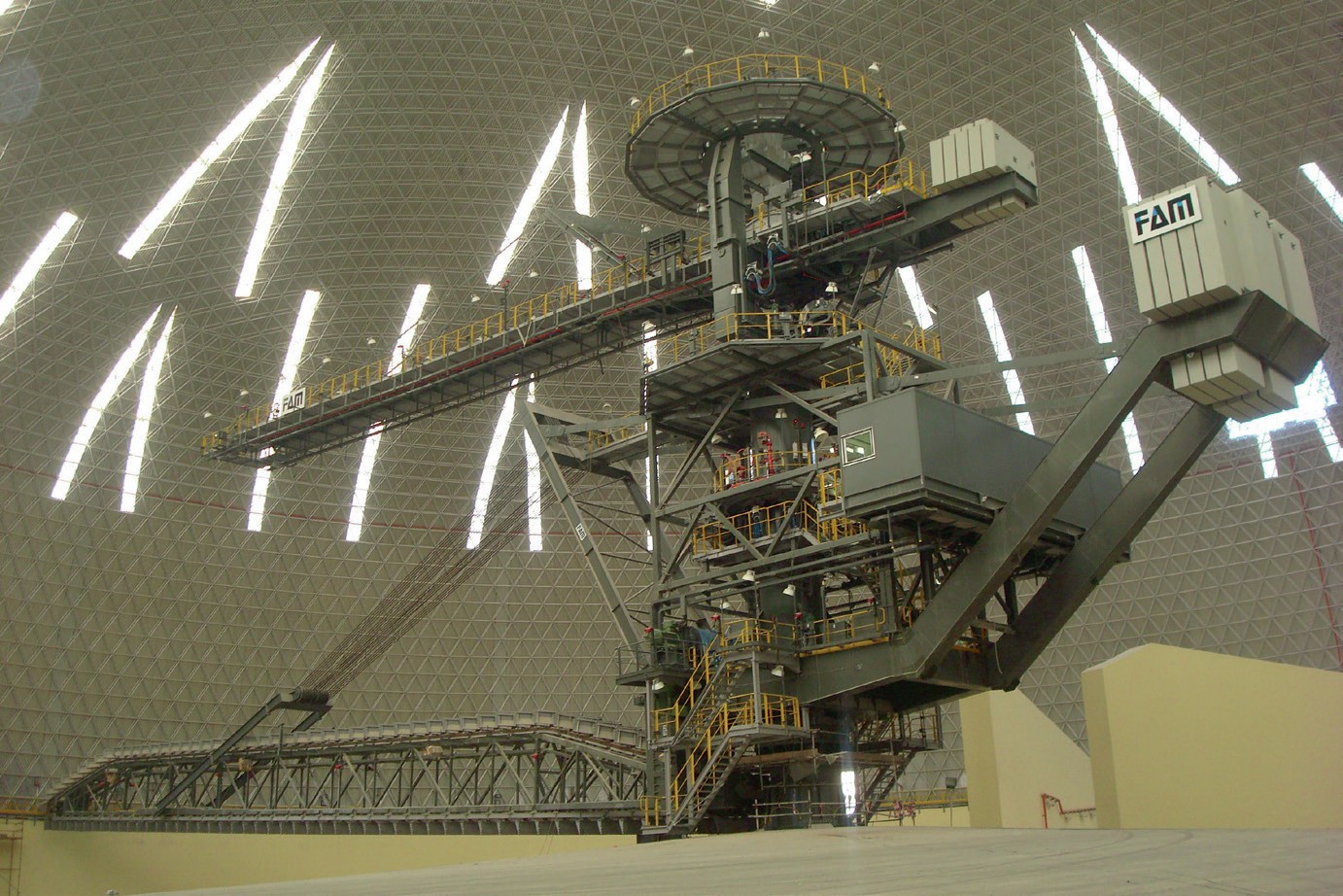
The oil-rich Emirate of Abu Dhabi, capital of the United Arab Emirates (UAE) has grown rapidly over the past decade to become the world’s largest exporter of sulphur. Most of this sulphur has come as a by-product from sour natural gas processing, as the Emirate tried to produce enough gas to power its breakneck growth.
The pace of Abu Dhabi’s growth has been astonishing. In 1970, the population of Abu Dhabi was 46,000. In 2016, including non-residents and resident noncitizens, this had mushroomed to 2.9 million, with the city of Abu Dhabi accounting for half of that. The city now sprawls far from the original island onto the mainland and across several neighbouring islands recovered from the sea. At the same time that its population has expanded, growing demand for electricity, for lighting, air conditioning, domestic power and desalination of sea water, has increased faster still, with peak demand rising sixfold from 3.3 GW in 2000 to 18.3 GW in 2020.
Meeting this rapid growth in power demand has been a considerable challenge. Abu Dhabi has great potential for solar energy, and has already completed a large 1.2 GW solar array at the Noor Abu Dhabi site, and in July gave the go-ahead for constructing a new 2 GW solar array at Al Dhafra, which is due to be operational by 2022. Likewise, Abu Dhabi has looked to nuclear power as a solution, and this August switched on the first of four reactors at the $32 billion 5.6 GW Barakah nuclear power site – the other three reactors are due to come on-stream over the next three years. However, building a nuclear power station has taken ten years, and in the meantime, the speed of increase of electricity demand has meant a concentration on natural gas as a solution – gas turbines are relatively quick and easy to set up. Consequently, at present, over 90% of Abu Dhabi’s power generation comes from natural gas.
Natural gas
The UAE held the seventh-largest proved reserves of natural gas in the world at 215 trillion cubic feet (6.0 trillion cubic metres) in 2018, with most of this in the Emirate of Abu Dhabi. However, since then there have been a string of new gas discoveries which have moved it up to sixth place. In November 2019, Abu Dhabi’s state-owned Abu Dhabi National Oil Company (ADNOC) announced the discovery of 58 tcf of conventional gas and 160 tcf of unconventional gas, in addition to new oil finds, and in February this year came news that this may have been added to with another 80 tcf (2.2 tcm) of gas, with the discovery of the shallow water Jebel Ali reservoir, between Abu Dhabi and Dubai. The new giant field has the prospect of being the largest single gas field discovery since Galkynysh was found in Turkmenistan 15 years ago. Both Abu Dhabi and Dubai will develop the field jointly, according to a statement by their respective rulers, over the coming decade.
In the meantime, however, most gas production in the UAE will remain in Abu Dhabi, from a combination of onshore and offshore fields. Gas production in the UAE rose to 62.5 bcm in 2019, running behind consumption at 76 bcm. The UAE as a whole has been a net importer of gas since 2008, with the growth of the city of Dubai having been equally as breakneck as that of Abu Dhabi but without – until now – the gas reserves to power it. As a result, a pipeline was constructed across the shallow waters of the Gulf from Qatar, which operates the largest gas field in the world – the North Field. The Dolphin pipeline has been supplying an average of 25 bcm of gas since 2008, although this figure dropped to 19.5 bcm in 2019. At the same time, since 1973, ADNOC has also been exporting natural gas as LNG from the offshore Das Island terminal. This was expanded to encompass a third LNG train in 1994, and exports ran at around 7.7 bcm in 2019. Of course, Das Island was set up before the UAE became a net gas importer, but now it remains locked into long term export contracts. Somewhat counter-intuitively, therefore, a floating LNG storage and regasification unit was also installed off Dubai in 2014, joined by a second in 2016, and Dubai imported 1.6 bcm of natural gas as LNG in 2019.
The UAE’s rapid growth of gas demand for electricity production noted above soon outstripped the capability of the Dolphin pipeline to supply gas, and so Abu Dhabi has turned to its large onshore reserves of sour gas to make up the shortfall. The largest sour gas project has been Shah, detailed below, the completion of which has turned Abu Dhabi into the world’s largest exporter of sulphur, but sulphur tonnages are also boosted by the processing of sour associated gas and sour gas from other fields at the Habshan complex.
The UAE’s future needs for gas will be reduced by the start-up of the solar and nuclear power plants, which will be supplying 25% of the country’s energy needs by 2023. However, recent years have also seen relations between the UAE and neighbouring Qatar sour over a number of issues, and in 2017 the UAE, together with Saudi Arabia and a number of other Gulf states, broke off relations with Qatar. Though things have thawed a little in the intervening years, there is a general consensus in the UAE to try and end its dependence on Qatari natural gas imports, and so new sour gas projects will vie with additional LNG imports as potential sources of gas for the nation.
Oil and refining
The UAE holds 6% of the world’s proved oil reserves, and 96% of those reserves are in the Emirate of Abu Dhabi. Reserves were increased by 7 billion barrels in November 2019 with the new offshore oil and gas discoveries. The country produced 4.0 million bbl/d of petroleum and other liquids in 2019, of which about 3.1 million bbl/d was crude oil and the remainder was condensate, natural gas liquids, and refinery processing gain. This makes the UAE, and particularly Abu Dhabi, the third-largest oil producer in OPEC after Saudi Arabia and Iraq. The state-run Abu Dhabi National Oil Company (ADNOC) plans to increase this to 5 million bbl/d by 2030, primarily by using enhanced oil recovery (EOR) at the company’s existing oil fields.
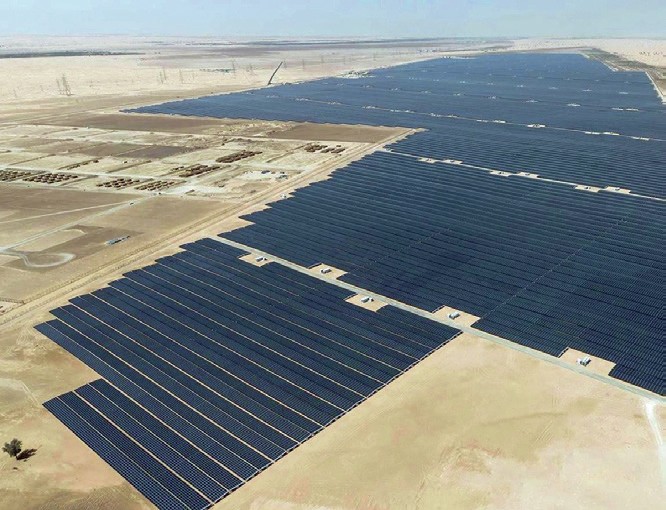
There are four downstream refineries in the UAE. The largest complex is at Ruwais in the west of Abu Dhabi, with a capacity of 837,000 bbl/d, divided into two refineries, the older Ruwais Refinery East (420,000 bbl/d) and the more modern Ruwais Refinery West (417,000 bbl/d), completed in 2015. The other three smaller refineries are at the Emirates of Jebel Ali (140,000 bbl/d) and Fujairah (82,000 bbl/d) and there is another smaller refinery, Umm Al-Narr, in Abu Dhabi city itself (85,000 bbl/d).
There was a plan to expand the Fujairah refinery, which sits on the UAE’s Indian Ocean coast, east of the Straits of Hormuz, by 250,000 bbl/d, with Brooge Petroleum & Gas Investment (BPI) and Sahara Energy Resources DMCC involved, but this has now been scaled back. Instead BIA is completing a more modest 25,000 bbl/d refinery designed to produce low-sulphur fuel oil that complies new IMO new regulations requiring ships to use marine fuels with a sulphur content below 0.5%.
Meanwhile, ADNOC announced plans in May 2018 to develop Ruwais into the world’s largest refining and petrochemicals complex by increasing refining capacity to 1.5 million b/d by 2026, at a cost of $45 billion. Wood Group has been working on the FEED project, and OMV and Eni – who are also partners in ADNOC Refning – have taken stakes in the venture. The expansion will take place in two stages, adding 200,000 bbl/d of capacity by 2024, and building a new 400,000 bbl/d greenfield refinery at the site by 2026. In the meantime, ADNOC is changing the configuration of the existing refinery to allow it to process up to 420,000 bbl/d of ADNOC’s heavy, sulphur-rich Upper Zakum grade, freeing up the more desirable light sour Murban grade for export. This $3.5 billion upgrade is expected to be complete by 2022, and was reported by the company in August 2020 to be 73% complete. As part of the upgrade, ADNOC Refining has contracted China’s Wison Engineering Services Ltd to replace ageing sulphur recovery units at the Ruwais refinery with more efficient units.
Sour gas
As previously mentioned, Abu Dhabi’s turn to its major sour gas reserves has been due to a combination of factors, from a need to process associated gas from sour crudes and avoid flaring, to a need for additional gas to feed power production, and a desire to achieve self-sufficiency in gas production.
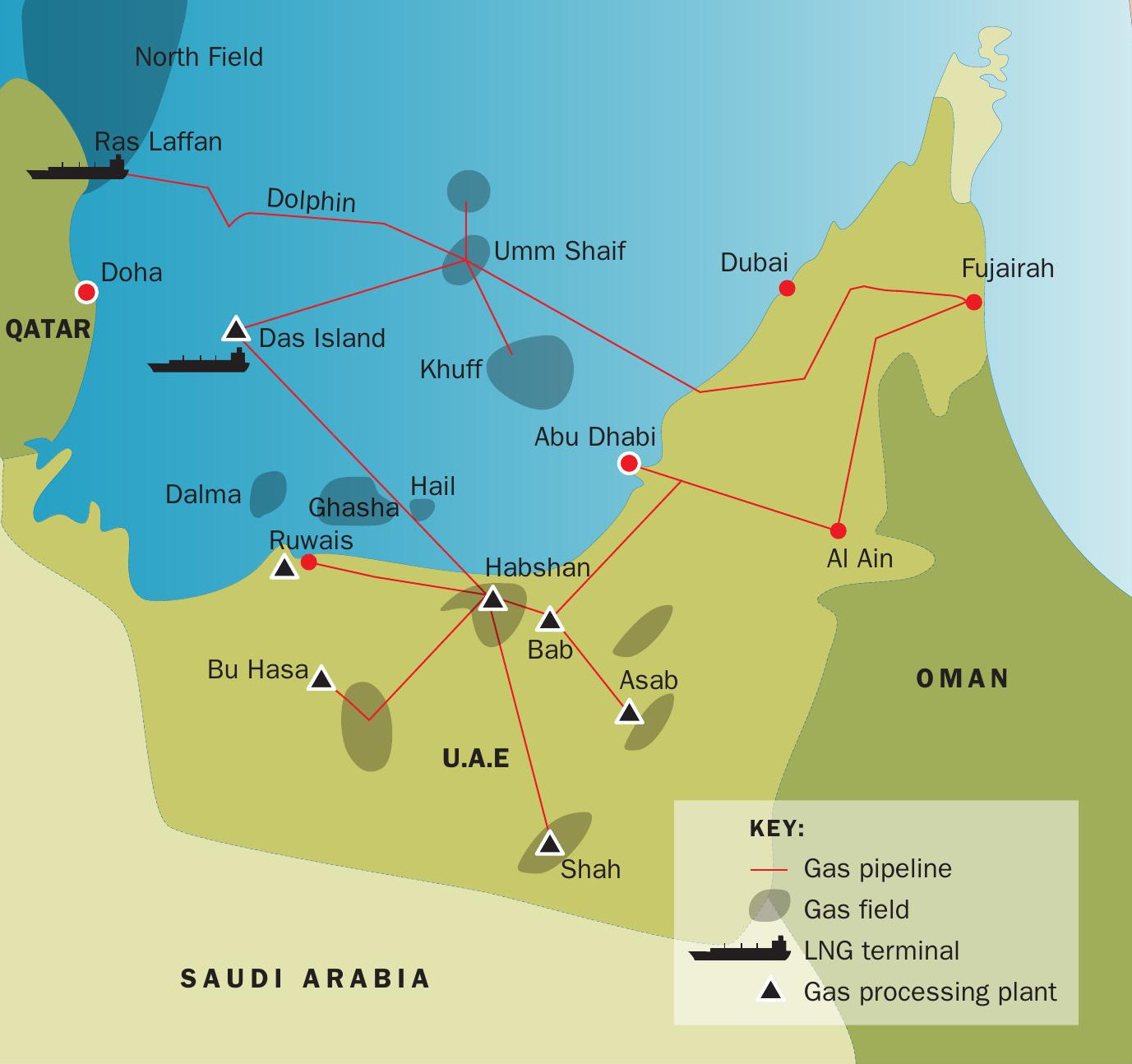
Sour gas and liquids processing happens at several sites in the Emirate (see Figure 1).
- Asab (‘Asab-0’) began life as a natural gas liquids plant, debottlenecked and uprated to a capacity of 450 million scf/d. In 2000, it was joined by the Asab Gas Plant, 7 km away, with a capacity of 870 million scf/d of non-associated gas from the condensate-rich Asab reservoirs. The gas here is reinjected for pressure maintenance, while the condensate is sent by pipeline to the Ruwias refinery for processing.
- Bab is also a natural gas liquids extraction train processing 150 million scf/d from oil production in the neighbouring oil field. Acid gas separated from processing operations is sent to Habshan for further treatment and sulphur recovery.
- The Buhasa natural gas liquids plant has two trains each designed to process 300 million scf/d of associated gas, with the plant typically exporting 7,500 tons per day of NGL to the Ruwais fractionation plant. In addition, Buhasa exports sales gas, with surplus gas being routed to Habshan for injection.
- Das Island processes gas for export as LNG. Liquid sulphur is produced which is taken by a dedicated 9,200 dwt liquid sulphur tanker, the Janana.
- The Habshan gas plant was built in 1983. Continuous expansion has taken it to 10 gas processing trains, 10 sulphur recovery units and eight gas injection compression trains, with the capacity to process and sweeten 4.73 million scf/d of feed gas from onshore reservoirs. The latest phase, Habshan-5, is sited 11 km away from the main Habshan Gas Plant, and was completed in 2013 by Tecnimont. It includes ‘rich’ and ‘lean’ streams, processed separately. Rich processing facilities constitute two trains designed to process 1.3 billion scf/d of gas from offshore gas from Umm Shaif, as well as onshore associated gas from the Thamama-B and Thamama-G reservoirs, to produce gas liquids and sales gas. The ‘lean’ facilities comprise two trains designed to 850 million scf/d of gas from the main Habshan Gas Plant (HGP) to sweeten and dehydrate the gas before sending it back to HGP.
- The Ruwais natural gas liquids plant is located within the Ruwais refinery complex, where it receives gas liquids from HGP, Habshan-5, Bab, Asab and Buhasa as well as raw LPG from the Ruwais refinery for treatment and fractionation. Ruwais refinery also recovers sulphur from acid gas and sends this to the sulphur terminal for export.
- Thammama C has a 450,000 scf/d gas gathering and processing plant which recovers and granulates sulphur. The sulphur, around 800 t/d, is taken by road shipment to the terminal at Ruwais.
Shah
While all of the foregoing generate sour gas and hence sulphur, the largest step change has come from the Shah sour gas field development, about 210km southwest of the city of Abu Dhabi. The $10 billion project is being developed by ADNOC Sour Gas, a 60-40 joint venture between Adnoc and Occidental Petroleum. Shah processes 1.0 billion scf/d of highly sour (23% H2 S) gas to generate 500 million scf/d of sales gas, as well as condensate and NGLs, and 10,000 t/d of sulphur. The four sulphur recovery units – the largest in the world – each have a capacity of 2,500 t/d of sulphur production.
Recovered sulphur is taken by pipeline 11 km to a sulphur granulation plant, and from there it is loaded onto rail wagons for transport 265 km to the export terminal at Ruwais. In 2018 ADNOC Sour Gas installed a sulphur remelter at the Shah granulation plant to recover sulphur lost during transportation via conveyors and transport operations.
ADNOC gave the go-ahead to a 50% expansion of capacity at Shah in 2018, expanding it to 1.5 billion scf/d of gas processing, with an additional 5,000 t/d of sulphur production. The project was due for completion in 2023, but Covid disruptions and ADNOC’s review of its operations could push that back.
Investment delays
Indeed, Abu Dhabi has started to scale back some of its planned sour gas project developments this year, as falling oil and gas prices and prospects for lower demand cause a rethink of projects. One of the major casualties has been the Ghasha megaproject, an umbrella for the Hail, Ghasha, Dalma, Nasr, and Mubarraz offshore sour gas schemes, designed to turn Abu Dhabi into a net gas exporter, and involving the construction of 10 artificial islands and two causeways. Italy’s Eni, Germany’s Wintershall, and Austria’s OMV have taken major stakes in the project, and Petrofac was awarded the $1.65 billion EPC contract for Dalma in February, only to find the contract cancelled in April. The project was due to begin production of another 1.0 billion scf/d of sour gas by 2024, but the high development costs have been causing anxiety among ADNOC’s partners, and a delay now looks certain.
Another planned project was the Bab sour gas project, originally designed to be on a similar scale to the Shah project (1.0 billion scf/d of sour gas), with a price tag estimated at $10 billion, and a joint venture development company with majority ownership by ADNOC. The gas at Bab is even sourer than at Shah, with an average H2 S content of 33%. It has been suggested that up to 20,000 t/a of sulphur may need to be extracted in order to process the gas. However, partner Shell exited the project in 2016, and so far no announcement of a revised tender has been announced.
Sulphur output
Most of Abu Dhabi’s sulphur output now comes from Shah and Habshan. Up to 4,500 t/d of liquid sulphur was originally sent by truck from HGP to Ruwais for granulation and export, but there is now a pipeline to take the sulphur to Habshan-5, where there are an additional four sulphur recovery units to process the separated acid gas from both rich and lean streams to produce 5,200 t/d sulphur. The Habshan Sulphur Plant handles all of this sulphur, granulating up to 10,000 t/a for onward transport along the rail line for export at Ruwais. Habshan-5 also features the capacity to store up to 180,000 tonnes of sulphur in a covered stockpile.
Shah adds another 10,000 t/a of sulphur granulation capacity, and this is taken by rail to the Ruwais port terminal.
The Ruwais Sulphur Handling Terminal has facilities for handling road deliveries of liquid sulphur via an unloading pit, from which sulphur is transported to a 40,000 tonne capacity liquid storage tank. Liquid sulphur in the storage tank is pumped to a day pit through sulphur filters via a transfer pump, from where the sulphur is pumped to granulation units. There are nine granulation units each with a capacity of 1,000 t/d. Each granulator is provided with its own dedicated wet scrubber. Sulphur product from the granulators is collected at conveyors equipped with dust collection systems and transferred to bulk storage. There are two bulk storage buildings, one circular, with 40,000 tonnes capacity and a linear warehouse with 110,000 tonnes of capacity. There is also a truck loading facility.
Rail deliveries of up to 22,000 t/a can be handled from the granulation plants at Habshan-5 and Shah. There is an additional 400,000 t/a arriving as liquid sulphur from the Das Island LNG facility, and 100,000 t/a from the next door Ruwais refinery.
Granulated sulphur is exported to ships through a shiploader system on a conveyor at the rate of 1,100 t/h. The 300m jetty can take vessels of up 65,000 dwt. The marine terminal is also used to unload liquid sulphur coming from the Janana liquid sulphur vessel in batches of approximately 8,000 tonnes. It is unloaded and transferred to storage tanks.
For export, ADNOC Logistics and Services operates a shipping fleet, including four very large crude carriers, 7 refined products tankers, 8 LNG vessels and three container ships. In 1993, the company launched the business of molten sulphur transportation with the acquisition of sulphur carrier Janana. The company also operates seven bulk carriers for delivery of ADNOC’s sulphur exports to North Africa and other locations. ADNOC signed a deal with Morocco’s OCP in 2017 for the supply sulphur out to 2025 for OCP’s phosphate production. In 2018 OCP received 2.6 million tonnes of sulphur from ADNOC.
A pause not a break
Abu Dhabi’s sulphur output has quadrupled over the past decade, from 1.7 million t/a in 2010 to over 7.1 million t/a today, catapulting it into the ranks of the world’s largest sulphur producers, such as China, Russia and the US, and – with little to no domestic demand to absorb this – in the process making it the largest exporter of sulphur in the world. In so doing, ADNOC has made a virtue of a necessity, and decided to focus on the whole sulphur value chain, treating sulphur as a valuable commodity in its own right rather than an unwanted by-product. It has begun to try to develop markets for sulphur, including sulphur-coated urea (ADNOC is also a urea producer, in conjunction with partner OCI), as well as phosphate fertilizer ventures in Africa, Asia, South America and Australia.
The current collapse in oil and gas prices, coupled with the completion of solar and nuclear power facilities, may have temporarily put the brakes on sour gas developments in Abi Dhabi, but commitments to increase oil production by 1 million bbl/d and become a net exporter of natural gas once more mean that this is likely to be a pause, rather than a break. It seems likely that by 2030, with the completion of projects such as the Shah expansion and the Ghasha sour gas project, we will be seeing even larger volumes of sulphur coming from Abu Dhabi, possibly turning it into the world’s largest sulphur producer.