Sulphur 406 May-Jun 2023
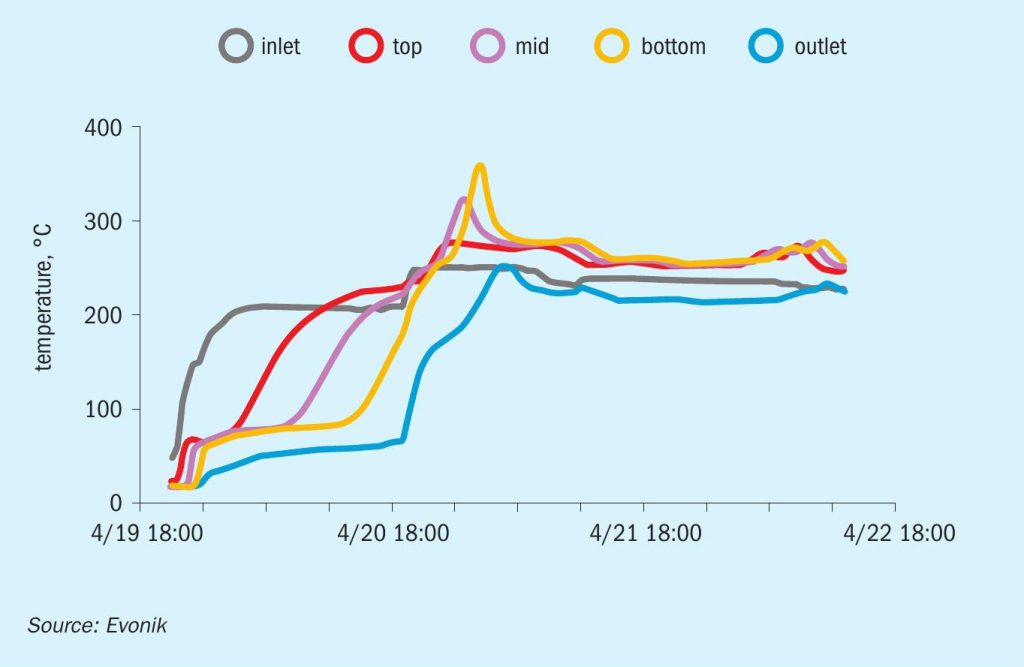
31 May 2023
Reaping the rewards of recycling
CLAUS TAIL GAS TREATING
Reaping the rewards of recycling
With the challenges facing the global refining industry, refiners should review their current practices to see how they can stay competitive and continue to thrive in today’s market. This means improving operational efficiencies and producing products at a lower cost, whilst ensuring performance and safety. Brian Visioli of Evonik explores the development of catalyst reuse and how recycled hydroprocessing catalysts can be successfully applied in tail gas treating units to deliver cost and performance gains.
Businesses must always maintain a close eye on the cost of their day-to-day operations, but perhaps more so than ever today given the economic headwinds facing the global economy that show no sign of abating. Many industries – including the refining and chemical industries – are faced with a multitude of new challenges. Refineries are under more strain than ever, with rising costs, market volatility, tightening environmental legislation, and the potential for a mild recession all piling on the pressure.
Transitioning to greener, more sustainable manufacturing processes is critical for the industry to reform and revitalise its operations to reduce waste, cut pollution and minimise impact on the environment. Factor in the lingering effect of the pandemic, with its disruption to refinery output by delayed maintenance schedules, and it is clear to see why refineries need to find cost-effective ways to increase operational efficiencies and maximise productivity and profitability – all without compromising on performance or safety.
Catalyst reuse can serve as a starting point to achieving this without having to modify current operational processes.
Benefits of recycling
Refiners who only consider fresh catalysts for replacements may have a preconceived notion that they have a performance advantage in terms of conversion, selectivity, pressure drop, or active life over recycled catalysts. However, advances in catalyst re-use technology have closed this gap to rival and, in some cases, improve performance – with the additional benefit of requiring a lower level of investment and no changes to refinery facilities or production methods.
Catalyst reuse schemes are not a new development; for more than 40 years, the refining industry has successfully reused hydroprocessing catalysts through ex-situ reactivation to capitalise on their economic and environmental gains. Of the 150,000 t of replaced hydroprocessing catalysts in refineries each year, more than 20% are catalysts which have been regenerated or rejuvenated via ex-situ processes, which translates to approximately 30,000 t of reused catalysts being installed per year.
One of the key reasons why refineries should consider catalyst rejuvenation is the cost savings it can deliver, largely because they have a lower replacement cost than fresh tail gas catalysts.
When a spent hydroprocessing catalyst has reached the end of its cycle life, it can be removed in one of three ways. The least desirable (and most costly) method is waste landfill disposal, where you not only lose the inherent value of the catalyst but must pay an additional fee to dispose of the catalyst in a hazardous landfill. While processing for metal reclamation is a more favourable approach, there is still a processing cost as the less-valuable components of the catalyst particles, such as the alumina substrate, still need to be disposed of in the landfill.
The best and most cost-effective option is to reactivate the catalyst for reuse. This process involves oxidation to remove carbon and sulphur compounds while preserving the useful parts for application elsewhere in the refinery. Their applications include the hydro-treating of naphtha, atmospheric gas oil and fluid catalytic cracker feed hydroprocessing. Recycling catalysts not only extends their valuable life, but it also significantly reduces the number of hazardous spent (used) catalyst waste sent to landfill.
Financial gains
With several similarities between hydro-processing catalysts and tail gas treating catalysts, the reactivated catalysts can be ideal to apply in Claus tail gas treating. Both applications employ metals such as cobalt and molybdenum, supported on a carrier containing aluminum, silicon, zeolites, or in combination. Additionally, they both need to be converted to a metal-sulphide state for activity toward the desired reactions, and both consume hydrogen as a reactant in the desired reactions.
However, there are also considerable differences to note between the two types of catalysts and their applications. For example, the quantity of active metal applied to hydroprocessing catalysts is commonly much greater than that on tail gas treating catalysts. Also, hydroprocessing catalysts do not typically encounter species containing oxygen atoms when processing fossil fuels, and the operating pressure is significantly higher in hydro-processing (up to 140 bar, or higher) compared to tail gas treating. These differences influence which types of deactivation typically occur during operation, which in turn has an impact on whether the catalyst can be reused.
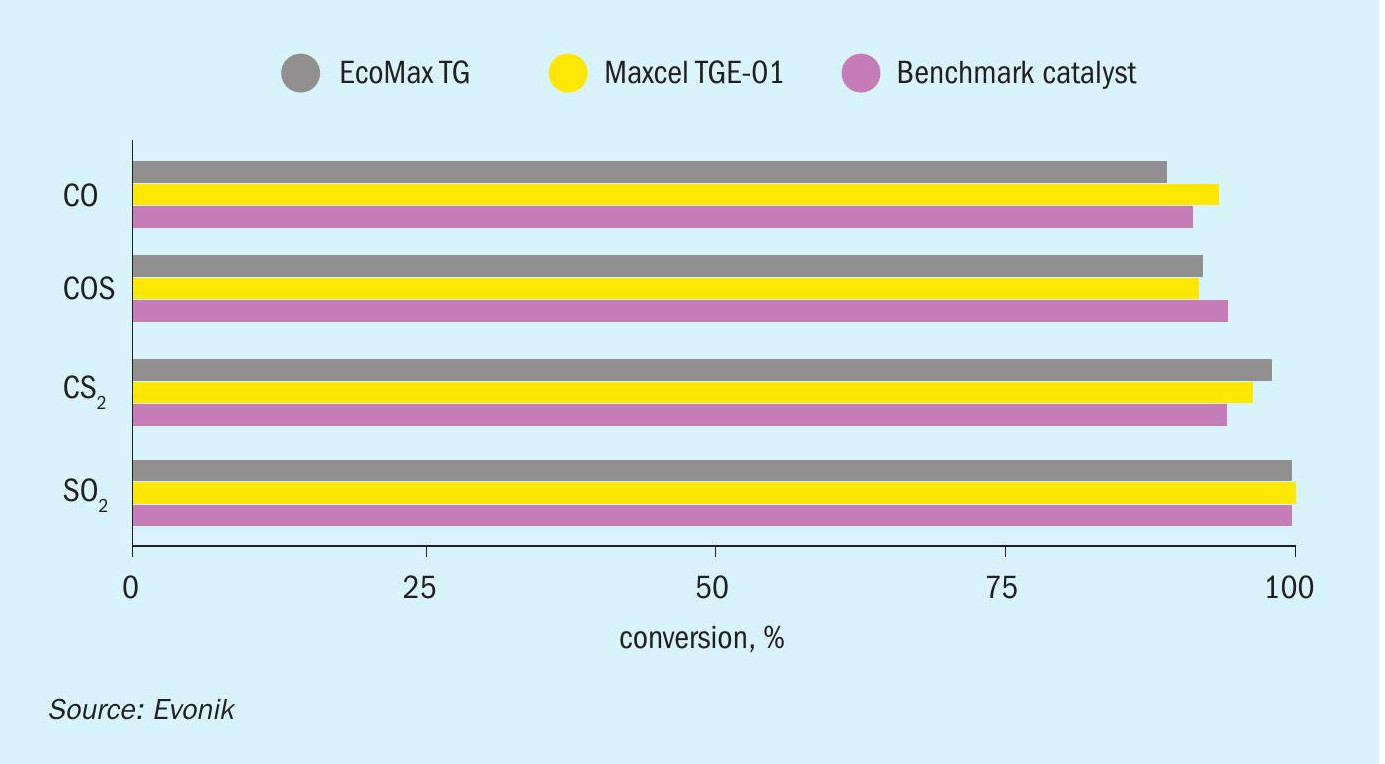

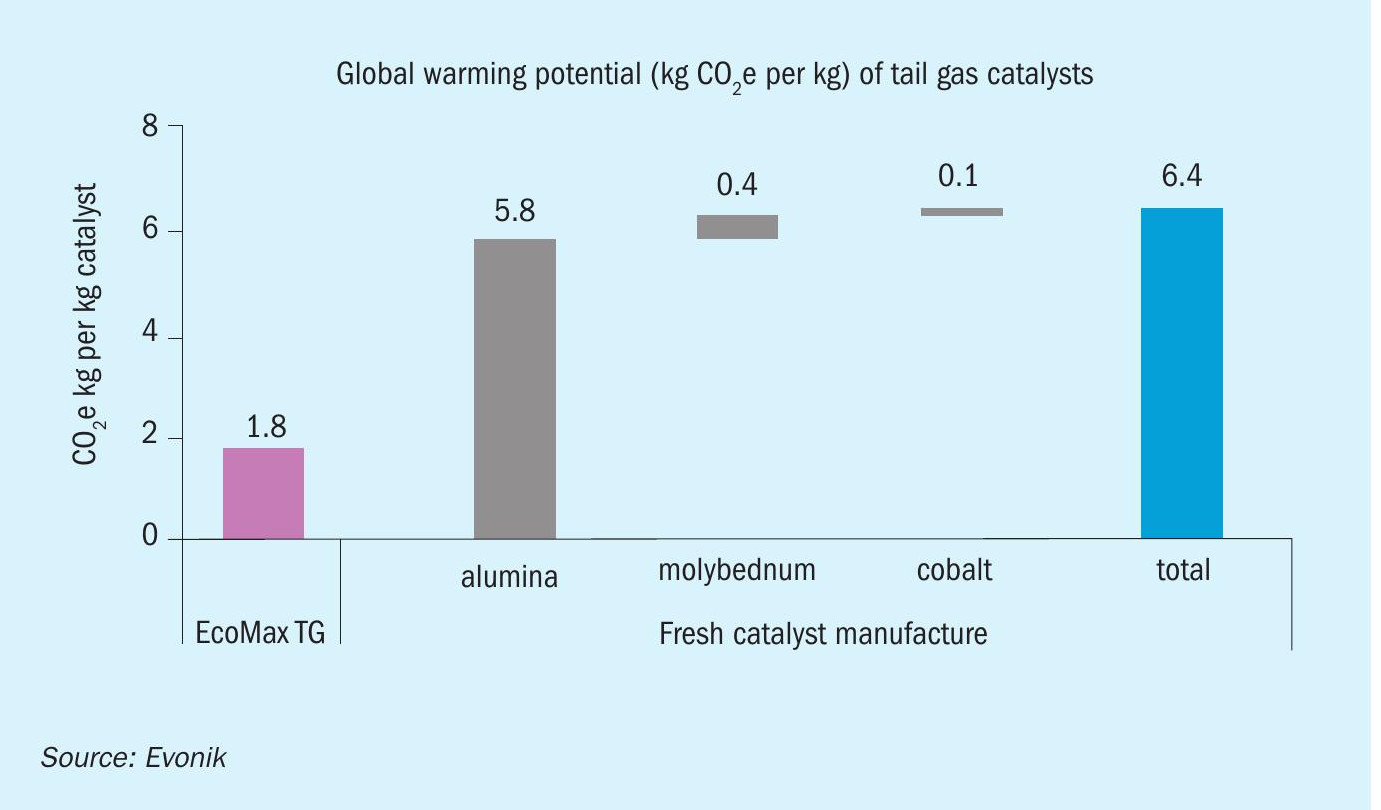
Evonik identified an opportunity to develop a catalyst – EcoMax TG – to fully utilise the useful components of a spent hydroprocessing catalyst. This patented method for treating spent catalysts from a hydroprocessing unit removes contaminants and optimises the catalyst for use in a tail gas treating hydrogenation reactor. As a result, EcoMax TG has brought substantial financial benefits, in the region of a 20-40% reduction in cost compared to typical fresh tail gas catalysts.
Improvements against the industry standard
The important qualities of a tail gas catalyst are performance, economics and environmental impacts. Catalyst performance is quantified by testing catalyst conversion performance under identical controlled conditions. The performance of a traditional benchmark catalyst, EcoMax TG, and Maxcel TGE-01 (a fresh extruded tail gas catalyst from Evonik) at example conditions is shown in Fig. 1.
Performance testing has also been completed on a commercial installation of EcoMax TG at a US Gulf Coast refinery, which showed an exceptional conversion of COS and CS2 compared to traditional catalysts. This advantage is brought about because of the high cobalt and molybdenum content of the EcoMax TG catalyst, compared with traditional tail gas catalysts. Therefore, by reactivating spent hydroprocessing catalysts, the higher metals in the catalyst can be leveraged at a substantial discount compared to manufacturing the tail gas catalyst with a higher metals content.
The economics of tail gas catalysts are a function of the cost of the catalyst components itself, manufacturing cost, transportation cost and catalyst density. To standardise the effects of different types and locations of manufacturing, tail gas catalyst costs may be computed per unit volume. The comparison in Table 1 is based on actual fill cost, thereby removing the density variable. Because EcoMax TG manufacturing does not require re-building a catalyst from raw materials, it can be procured at a significant cost savings versus traditional tail gas catalysts.
Sowing the seeds for sustainability
On top of the economic advantages of repurposing hydroprocessing catalysts for TGTUs, refineries can also unlock significant environmental benefits.
The ecological effects of using EcoMax TG compared to a freshly manufactured tail gas catalyst using virgin raw materials were evaluated using a life cycle assessment (LCA) based on Evonik-internal manufacturing data as well as data from peer-reviewed publications. The LCA compared the carbon footprint between the two products using a “cradle to gate” methodology. Fig. 2 illustrates the difference between manufacturing a fresh tail gas catalyst using virgin raw materials and replacing the traditional catalyst with Eco-Max TG.
For example, a typical tail gas treating unit (TGTU) may require 30 t of tail gas catalyst resulting in a carbon footprint of 190 t CO2 e (6.4 kg per kg catalyst). However, by replacing the traditional catalyst with EcoMax TG, the total carbon footprint would be reduced by nearly 140 t CO2 e – a substantial reduction in environmental footprint. This difference is in large part down to the fact that no new metal raw material (aluminum, cobalt, or molybdenum) mining is required with EcoMax, as would be the case for a freshly manufactured catalyst, and consequently no additional processing or transportation.
Furthermore, as outlined above, reusing the catalyst reduces waste that would otherwise be disposed of in landfill. The catalyst reuse method is also less energy intensive than the process of forming particles to make a fresh catalyst. So, taken altogether, the numerous Scope 3 emissions – indirect emissions associated with “upstream” processes that are tied up in making a fresh catalyst – are effectively avoided with the more sustainable EcoMax TG catalyst.
Case Study: EcoMax in the field
The EcoMax TG catalyst was chosen by an oil refinery located in the US because of its ability to deliver the required level of conversion activity at the lowest cost. The facility has two sulphur recovery units (SRU), each with its own tail gas treating units and a design capacity of 50 t/d.
The refinery requested that the tail gas catalyst was preactivated, so Evonik’s pre-activation treatment, UltraCAT® TG was applied to speed start-up after its installation and offered both products in a unique, complete package that met the specific requirements of the refinery. UltraCAT® TG preactivation requires that the catalyst be loaded under inert (nitrogen) conditions. After installation, the startup procedure begins with the reactor running at the optimal temperature so the Claus tail gas can be introduced. The temperature wave shown in the chart in Fig. 3 coincides with the introduction of Claus tail gas into the warming tail gas reactor.
Performance of the EcoMax TG catalyst was as expected and enabled the refinery to meet the SO2 emissions requirements as well as reduce costs across the refinery.
Moreover, the successful installation of EcoMax TG in the refinery has, crucially, demonstrated a reduced dependence on fresh cobalt and molybdenum metals. Consequently, refiners can reap the double benefit of decreasing their carbon footprint while enhancing circularity without any adverse effect on performance levels.
The extension of catalyst reuse technology to tail gas treating has been made possible thanks to Evonik’s unique experience in both hydroprocessing catalyst recovery and sulphur recovery catalysis.
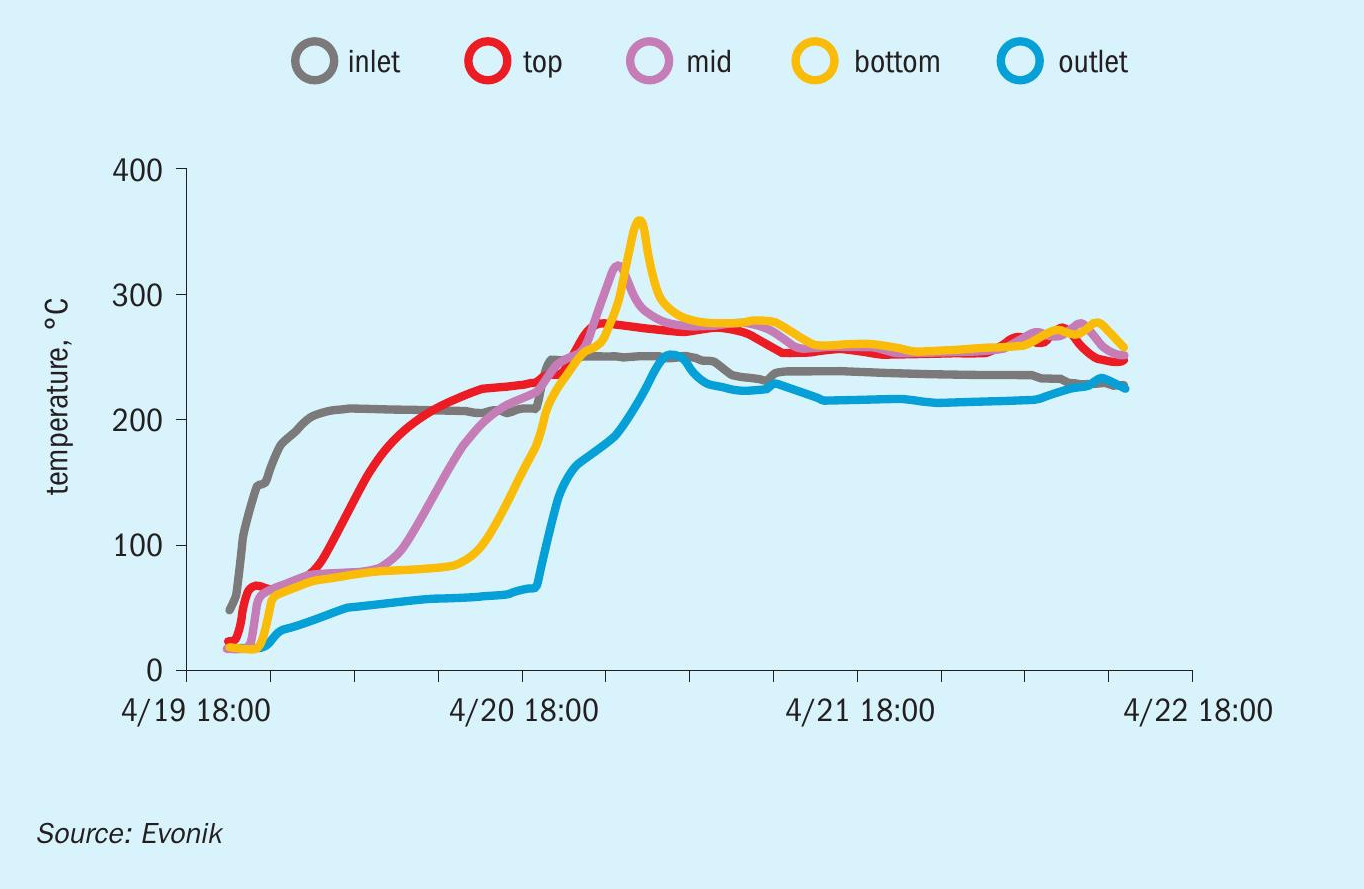
Summary
Recycling hydroprocessing catalysts and applying them in tail gas treating units can help refiners to address these challenges. With the technological advancements from Evonik, refiners now have a credible and practical option to use a more cost-effective catalyst that does not sacrifice performance or require an overhaul of current production processes – with added environmental benefits.
The use of a regenerated or rejuvenated hydroprocessing catalyst (EcoMax TG) in tail gas treating can offer considerable economic and environmental gains for operators.