Sulphur 408 Sept-Oct 2023
30 September 2023
TGU catalyst poisoning and deactivation
CLAUS TAIL GAS TREATING
TGU catalyst poisoning and deactivation
With the aid of a rigorous kinetic model for TGU hydrogenation reactors, incorporating catalyst deactivation mechanisms, designers and operators can forecast the life expectancy of reactor catalyst beds.
Catalyst deactivation is the loss over time of catalytic activity and/or selectivity. It is a problem of great and continuing concern in the practice of industrial catalytic processes. Costs to industry for catalyst replacement and process shutdowns total billions of dollars per year, and in sulphur recovery, TGU catalyst expenses account for at least $50 million per year plus the cost of unloading and loading. This does not include lost profit from downtime for unplanned outages, which can exceed $1 million per day at a sulphur constrained facility.
Time scales for catalyst deactivation vary considerably; for example, with cracking catalysts, longevity is measured in seconds; in ammonia synthesis the iron catalyst may last for 5-10 years. However, all catalysts inevitably decay. In TGUs, typical life is 5-6 years, although many operators can use the same catalyst charge through two turnaround cycles, and some have successfully operated for 10-12 years. Severe cases of deactivation have life shortened to a few months. There are two known remarkable longevity records – 18 and 20 years.
TGU catalysts are largely cobalt and molybdenum on an alumina support, a support which is used widely in the process industry and for the Claus process. This body of knowledge is a strong reference regarding deactivation. Argyle and Bartholomew3 provide a comprehensive reference. TGU catalysts are not specifically included in this reference so experience as informed by sulphur recovery industry experience and research is presented.
Deactivation can be classified by stress type: chemical, thermal, and mechanical. Mechanisms are multiple: poisoning, coking, fouling, thermal degradation/sintering, vaporisation or sublimation, metal/support interactions, and attrition/crushing. Activity loss in a well-controlled process happens slowly. However, process upsets or poorly designed hardware can bring about rapid failure.
Many are the paths for heterogeneous catalysts to decay. For example, a solid catalyst may be poisoned by any of several contaminants in the feed. Its surface, pores, and voids may be fouled by hydrocarbon-related processes. Oxygen or chlorine in the feed gas can lead to deleterious effects. Similarly, changes in the oxidation state of the active catalytic phase can be induced by reactive gases such as O2 or SO3 in the feed. Furthermore, the process environment causes aging by the very exposure to process gas, moisture and normal operating temperature.
Hydrothermal aging
Hydrothermal aging causes irreversible loss of surface area of alumina and titania supports. The mechanism is the transformation of the surface structure from water interacting with hydroxyl groups on alumina. Surface area and activity are lost in the first days to weeks of operation, depending on the temperature and water concentration. This is a form of sintering driven by water vapour and temperature, but at lower temperatures.
The surface of fresh catalyst has a large area and numerous active sites. Reformation occurs early in operation, ultimately reducing the surface area by about 30%. The surface then becomes stable, declining slowly over years. In this way, γ-alumina is converted to β-Al(OH)3 (boehmite, bayerite or gibbsite)5 . Surface hydroxyls can also condense, dehydroxylating the surface. Further, diffusion of surface Al atoms results from the breakage and reestablishment of surface Al-O-Al bonds. Loss of specific surface area lowers catalyst performance as the number of Al-OH surface sites drops in proportion to the loss.
The mechanical coalescence of smaller particles forming larger spheroids as well as trapped voids (rather than catastrophic structural collapse) reduces surface area. The process progresses by establishment of filets at contact points, then gradual reformation and merging. For example, coalescence of eight micro spheres into one results in a single particle with twice the radius and half the surface area.
Active metals can also migrate or undergo crystallite growth under hydrothermal conditions, reducing the active site number density. Water vapour promotes sublimation and migration, which act to grow larger crystallites or slabs with fewer sites, reducing dispersion and lowering activity. The sulphide form is less volatile and more resistant to migration than the oxide.
Generally, fresh TGU catalyst has a specific surface area of 300–350 m2 /g, which rapidly declines to 240–260 m2 /g, then is relatively stable, declining over years until “spent” at approximately 120 m2 /g. Catalyst activity also declines with aging, and spent catalyst expresses about half of the activity of fresh catalyst. Hydrothermal aging tends to occur uniformly throughout the catalyst bed and activity declines over the useful life.
Thermal degradation and sintering
Sintering is a thermal process which causes fairly rapid agglomeration of base (micro) particles into substrate, or of active metals into fewer, larger crystallites. The sulphide form of the active metals is fairly stable and provides some resistance to sintering because sublimation temperatures are higher than for the oxides. Temperature exposure that causes sintering (500– 1,000°C) is well above the normal operating range for a TGU, but can be experienced in some units under upset conditions, especially upon introduction of oxygen.
Thermally-induced catalyst deactivation results from (1) loss of surface area caused by crystallite growth of the catalytic phase, (2) loss of support area from support collapse and of catalytic surface area from pore collapse on crystallites of the active phase, and/or (3) chemical transformations of catalytic to non-catalytic phases. Supported metals sintering and redispersion has focused on the dynamics of metal crystallites: (1) crystallite migration, (2) atomic migration, and (3) (at very high temperatures) vapour transport.
Steam and thermal deactivation are believed to occur by separate mechanisms, differing primarily in the mode of mass transport. With steam, surface- or vapour-phase diffusion predominate; whereas, thermally, bulk- and grain-boundary diffusion predominate. It has been suggested that voids-trapping within catalysts steamed to low surface areas can be considerable3 .
Aging from thermal cycling has a mechanical aspect. Expansion and contraction of the catalyst induced by temperature changes in the presence of water vapour causes permanent destruction of the microporous structure. This is a normal aging process and occurs over an extended period owing to the inherent character of fixed-bed configurations used in TGU applications. The crush strength is reduced and fines are produced by attrition.
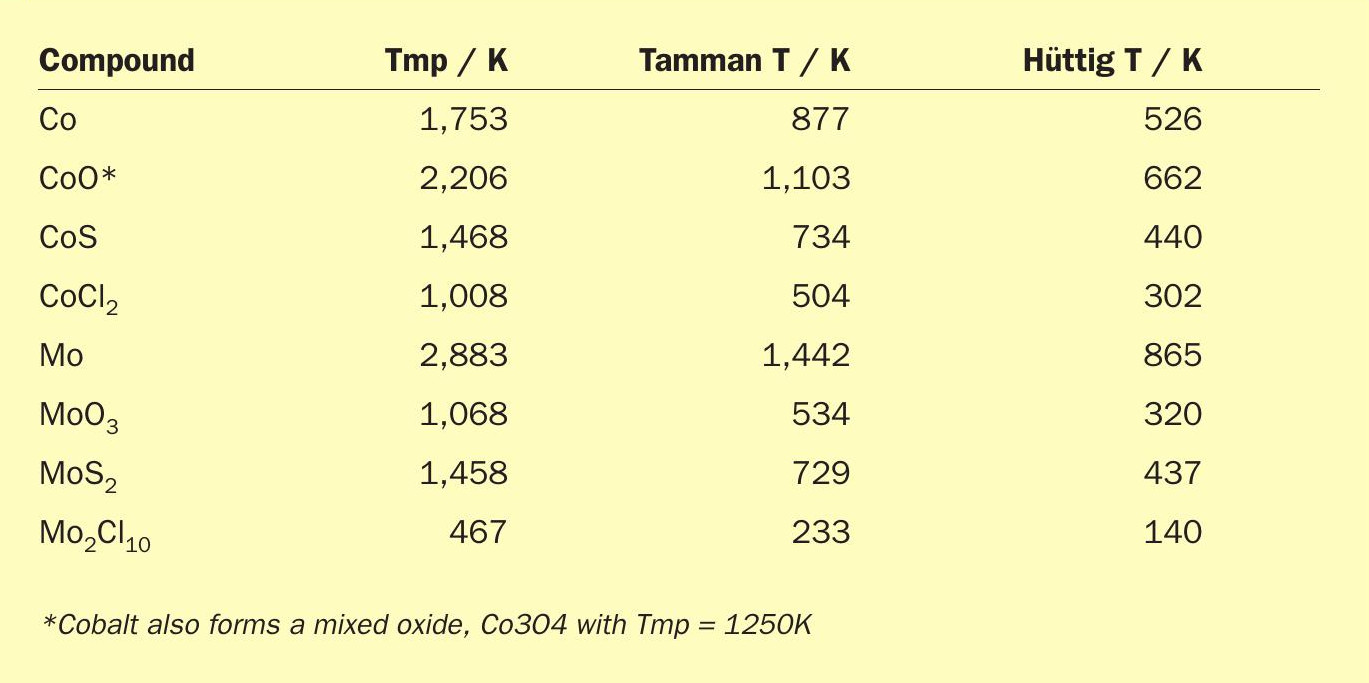
The effect of temperature on metal and oxide sintering depends on the driving forces for dissociation and diffusion of surface atoms: both are proportional to the fractional approach to the absolute melting point temperature (Tmp ). Thus, as temperature increases, the mean lattice vibration of surface atoms increases; when the Hüttig temperature (0.3Tmp ) is reached, less strongly bound surface atoms at defect sites (e.g., edges and corner sites) dissociate and diffuse readily over the surface, while at the Tamman temperature (0.5Tmp ), atoms in the bulk become mobile. Accordingly, sintering rates of a metal or metal oxide are significant above the Hüttig temperature and very high near the Tamman temperature4 . The data in Table 1 are for compounds of cobalt and molybdenum, active metals in TGU catalysts. For reference, the operating temperature of a TGU reactor is 200– 300°C (473–573K).
Promoters and impurities affect sintering and redispersion, affecting metal atom mobility on the support; in the latter case, dissociation and migration decreases at high melting points. Similarly, support surface defects or pores impede surface migration of metal particles – especially micropores and mesopores with pore diameters about the same size as the metal crystallites.
Sintering rates are exponentially dependent on temperature, fitting the classic Arrhenius relationship. The references cited above give example rates and activation energies on alumina and other supports, although TGU catalysts are not explicitly included. Eact varies from 30 to 150 kJ/mol and decreases with increasing metal loading and increase in the following order with the atmosphere: NO < O2 < H2 < N2 . Metal– support interactions are weaker (bond strengths of 5–15 kJ/mol); with few exceptions, thermal stability for a given metal decreases with support in the order Al2 O3 > SiO2 > carbon. Extending this approach to lower temperature operating ranges in TGUs provides reasonable representation of observed aging-rate-related deactivation.
Sintering rate data were historically fitted to a simple power-law expression (SPLE):
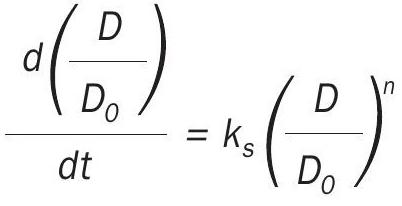
where ks is the sintering rate constant, Do the initial dispersion, and n is the sintering order (3–15 for typical catalyst systems). The SPLE assumes surface area or dispersion ultimately reaches zero when, in fact, for a given temperature and atmosphere, a non-zero value is observed. The general power-law expression (GPLE) adds a term to account for the observed asymptotic approach:
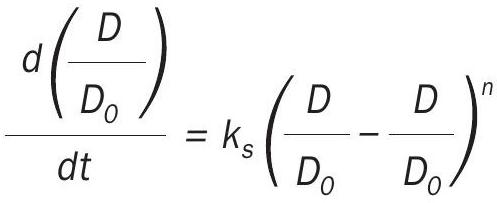
This gives a limiting dispersion Deq at infinite time. The order of sintering, m, is found to be either 1 or 2 as shown by Fuentes and coworkers5,6 and by Bartholomew and coworkers7-9 .
In oxidising atmospheres, γ-alumina and silica are the most thermally stable carriers; in reducing atmospheres, carbons are most stable. Steam accelerates support sintering by forming mobile surface hydroxyl groups that are subsequently volatilised at elevated temperatures. Chlorine similarly promotes sintering.
Sulphur condensation
If the reactor is operated at or below the sulphur dewpoint, liquid sulphur can accumulate within the catalyst pores. This is typically associated with a problem in the upstream SRU coalescer operation or a blocked rundown line. It is also notable that sulphur condensation within the micropore structure is possible because the bulky S8 molecule formed is larger than some of the micropores.
Whereas SO2 is converted to sulphur and water on Co/Mo active sites, the resulting sulphur remains on the Co/ Mo sites and is hydrogenated to H2 S. However, if SO2 conversion is achieved via the Claus reaction on alumina, it produces a S6 or S8 molecule which must desorb, diffuse and re-adsorb on Co/Mo to be converted to H2 S. The S8 molecule can effectively become stuck, unable to vacate the catalyst pore, so condenses and blocks it. This can be reversed simply by increasing the temperature in the bed and re-vaporising the condensed sulphur. Sometimes, this is easier said than done. For example, the designer may have failed to provide enough margin to the preheater to cover this operating scenario or is restricted to using condensing steam which limits the temperature.
Excessive sulphur entrainment from upstream SRU condensers and coalescers or blocked sulphur rundown lines can also increase the likelihood of reaching the sulphur dewpoint within the TGU catalyst bed (not just in the catalyst pore). SulphurPro® evaluates the dewpoint temperature margin within the catalyst bed, which is crucial to predicting deactivation by this mechanism.
Fouling
Fouling is the physical deposition of species onto the catalyst surface that causes activity loss from blockage of sites or pores. Examples include mechanical deposits of carbon and coke in porous catalysts as well as condensation of sulphur. Carbon-and coke-forming processes also involve chemisorption of different kinds of carbon or condensed hydrocarbons that may act as catalyst poisons. Carbon can be a product of CO disproportionation, while coke is produced by decomposition or condensation of hydrocarbons on catalyst surfaces and typically consists of polymerised heavy hydrocarbons. Nevertheless, coke forms may vary from high molecular weight hydrocarbons to primarily carbon such as graphite, depending upon the conditions under which the coke was formed and aged.
Coking and sooting
Carbon and coke formation on supported metal catalysts can restrict access via build-up on active metal sites or support, or blind active metal sites. Carbon may (1) chemisorb strongly as a monolayer or physically adsorb in multilayers, blocking access of reactants to metal surface sites, (2) completely encapsulate a metal particle and thereby fully deactivate it, and (3) plug micro- and mesopores, denying access of reactants to many internal crystallites.
Deactivation of supported metals by carbon or coke can occur either chemically from chemisorption or carbide formation, or physically and mechanically from blocking surface sites, metal crystallite encapsulation, and pore plugging. Destruction of catalyst pellets by carbon filaments occurs in other applications but has not been observed in TGUs. Blocking of catalytic sites by chemisorbed hydrocarbons, surface carbides, or relatively reactive films is reversed by regeneration with controlled oxidation. Regeneration of TGU catalysts is seldom practiced because of poor success controlling the required mild oxidising atmosphere in the plant environment.
Coking is accelerated on super acid sites that result from SO2 adsorption or sulphate formation in the upper portion of the bed before SO2 is extinguished. The biggest effect is when aromatics, heavy hydrocarbons or olefins are present.
Known promoters of coking, sooting and carsul formation include:
- olefins from refinery gas as fuel or poor-quality hydrogen makeup;
- refinery hydrogen (e.g., reformer) containing aromatics or BTEX and chlorides;
- acid gas enrichment streams containing BTEX.
In addition to hydrocarbon structure and reaction conditions, both the extent and rate of coke formation depend on the acidity and pore structure of the catalyst, increasing with acid strength and concentration. Thus, coking is driven by SO2 , therefore, coking will be more severe in the top of the bed and at the first active reaction front. Coking in TGU catalyst beds proceeds from top to bottom but can also occur thoroughout the bed to some degree.
Sooting commonly occurs when sub-or near-stoichiometric natural gas firing is used in SRU start-ups and shutdowns, or by improperly operating the inline reheat burners or reducing gas generator (RGG). Sooting is minimised by using a good quality high intensity swirl type burner for RGG, or avoided completely with an indirect TGU preheater.
Fine soot particles accumulate on the surface of catalyst and fill interstitial areas, restricting diffusion from the bulk to the catalyst surface and increasing pressure drop through the bed. Soot can even block macropores and restrict access to mesopores and micropores. This type of deactivation typically occurs at the top (inlet) of the catalyst bed and can create a rigid crusty structure. It causes loss in catalyst performance and also increases pressure drop through the catalyst bed, thus lowering hydraulic capacity,
Another cause of sooting is the deposition of carbon within the catalyst pores from disproportionation of carbon monoxide:

This effectively blocks the metal sites and reduces activity. Hydrogen and water vapour inhibit the path, although hydrogen partial pressure is quite low under TGU conditions. Disproportionation proceeds slowly under TGU low pressure conditions, and because CO is considerably reduced through the bed, it occurs mostly in the upper portion of the bed, advancing as catalyst is poisoned, and the reactive front moves down the bed.
Poisoning
Poisoning is the strong chemisorption of reactants, products, or impurities on sites otherwise suited for catalysis, operationally a species whose adsorption strength is higher than other species competing for catalytic sites. Adsorbed poisons such as sulphate may induce changes in the electronic or geometric structure of the surface. Poisoning can be reversible or irreversible. An example of reversible poisoning is the deactivation of acid sites by nitrogen (ammonia, cyanide) in the feed. Regardless of reversibility or irreversibility, the poison’s effects are the same. Many poisons occur naturally in feed streams that are treated in catalytic processes.
Sulphation
Sulphation results from the interaction of SO2 and H2 O on the catalyst surface, causing gradual build-up of sulphate, and reducing the effective surface area. In the TGU, SO2 concentrations are low and SO2 is fully converted across the reactor bed. The strong chemisorption of SO2 is generally reversible. While sulphate on alumina is key to Claus catalysis, this inhibits hydrolysis of COS and CS2 . With oxygen slip, SO2 forms sulphate, which is permanent, and If SO3 is present it will sulphate the alumina.
A significant impact of SO2 is raising the acidity of alumina which promotes coking. Chemisorbed sulphate has a strong interaction with electron distribution on the alumina surface, creating super acid sites. Hydroxyls on the catalyst surface serve as weak Brönsted acid sites with acid strength inversely proportional to the O-H bond strength. Sulphur dioxide additionally pulls electron density away from the O-H bond, making the H sufficiently acidic to catalyse coking or carsul formation.
Carsul
Carsul is akin to coking coincident with polymerisation, adding another dimension to hydrocarbon contamination. When C3+ hydrocarbons enter the TGU reactor they can crack on the catalyst’s acid sites and combine with sulphur across the catalyst surface3 . A tenacious carbon-sulphur polymer is formed called Carsul, which coats the catalyst and builds up, potentially blocking the macropores and preventing access to catalyst interior. Cracking tendency is worst at high temperatures, especially above 450°F (232°C). BTEX is particularly nasty in this regard as the cracking occurs deeper in the catalyst pore structure. High acidity and the presence of SO2 drives this reaction; sulphur is required, so it tends to form at the reactor inlet, moving progressively down the bed.
Deactivation by Carsul is permanent, but it is completely preventable by keeping precursor hydrocarbons out of the feed. Certain streams are known to contribute to this headache, including using reformer hydrogen as supplemental hydrogen, using refinery gas as fuel for the RGG, and processing acid gas enrichment off-gas (AGE) because it usually contains heavier hydrocarbons and BTEX. Also, sulphur plants which process BTEX can pass those species to the TGU, especially with lean acid gas because of difficulty to generate high enough thermal reactor temperatures to destroy BTEX. Historically, activated carbon and silica gel beds have been used to scavenge BTEX from lean acid gas feeds to the SRU.
Reaction to produce inactive phases
Refinery units process crude oil which contains sulphur and metals, such as vanadium, nickel, arsenic, phosphorous, selenium, and zinc that act as catalyst poisons in many petroleum refinery processes. They can enter off gas streams from those units and make their way into refinery gas or the acid gas removal units. Although most of these metal poisons wind up on the catalysts in the units where they are processed, some migrate or are entrained into the vapour phase and can make their way into the acid gas and the SRU and TGU.
Dispersed metal sulphides are catalytic phases in TGU applications. If the metal catalysts are oxidised or reduced, by prolonged exposure to hydrogen without hydrogen sulphide, it will lose essentially all its activity. These chemical modifications are closely related to poisoning, although the distinction is loss of activity due to the formation of an altogether new phase, e.g., oxide or metal, rather than via the presence of an adsorbed species.
Metal loss through formation of volatile compounds, e.g., metal carbonyls, oxides, sulphides, and halides in CO, O2 , H2 S, and halogen-containing environments, can be significant over a wide range of even mild conditions. Carbonyls are formed at relatively low temperatures but high CO partial pressures; halides will form at relatively low temperatures and low concentrations of the halogen. However, the conditions under which volatile oxides are formed vary considerably with the metal.
Reaction of SO3 with γ-Al2 O3 produces aluminium sulphate Al2 (SO4 )3 and is a serious cause of deactivation of alumina-supported catalysts in several catalytic processes. It leads to support breakdown and pore plugging.
Summary of deactivation mechanisms
Poisoning and thermal degradation are generally slow processes, while fouling and some forms of chemical and mechanical degradation can lead to rapid, catastrophic catalyst failure. Some forms of poisoning and many forms of fouling are reversible; hence, they can be regenerated, but this is seldom practiced for TGU catalysts. Conversely, chemical, mechanical, and thermal forms of catalyst degradation are rarely reversible.
It is often easier to prevent rather than cure catalyst deactivation. Some poisons and foulants can be removed from feeds using guard beds, scrubbers, and/or filters. Fouling, thermal degradation, and chemical degradation can be minimised through careful control of process conditions, e.g., effective destruction of ammonia in the SRU, avoiding feeds with BTEX to the SRU or TGU, avoiding reformer hydrogen as make-up (BTEX + Cl), using natural gas instead of refinery gas for burner fuel (O2 slip, soot, olefins and heavy hydrocarbons, temperature excursions from changing stoichiometry) and avoiding SO3 formation in SRUs. Effective control of air or oxygen to maintain tail gas H2 S:SO2 ratio with some benefit for control at elevated 4–6:1 H2 S:SO2 ratio. Avoiding SO2 breakthrough or operation without hydrogen (coking) are vital.
Mechanical degradation can be minimised by careful control of heat-up rates and minimising thermal cycles. Proper catalyst handling during loading, avoiding mechanical shock from high velocity impact, is important to prevent breakage and attrition. Catalyst design addresses choice of carrier materials, impregnation techniques, catalyst particle forming methods, and calcining.
References