Sulphur 412 May-Jun 2024
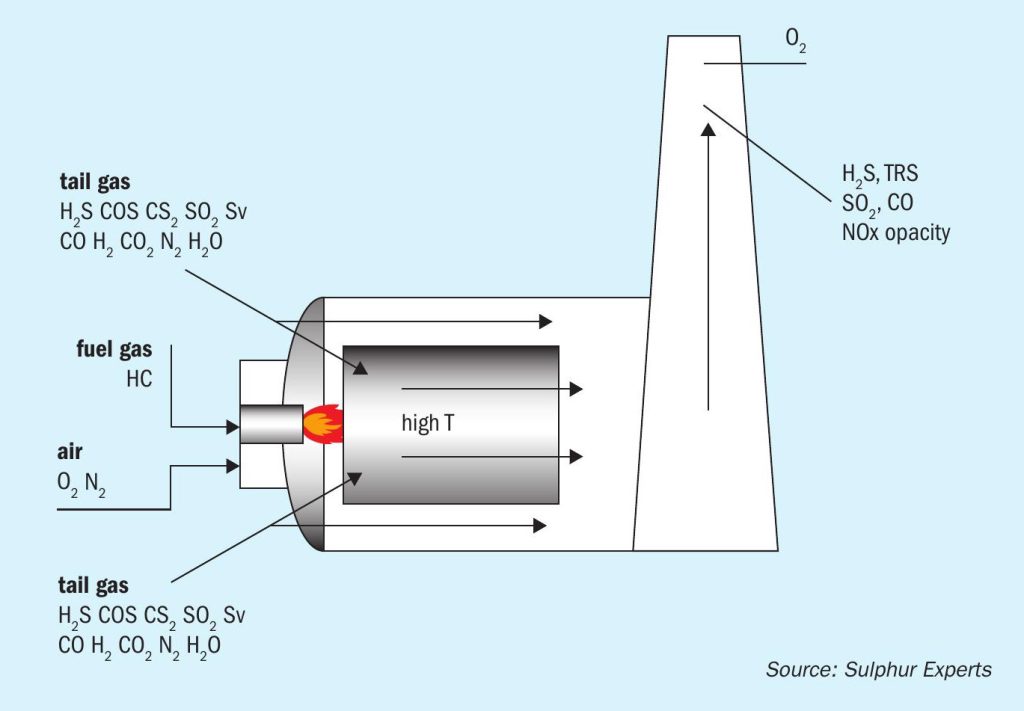
31 May 2024
A better understanding of SRU incinerators
SRU INCINERATOR OPTIMISATION
A better understanding of SRU incinerators
Sulphur Experts outline the steps required to determine optimised SRU incinerator operating conditions. Although a proper determination of the ideal SRU incinerator operating conditions for any given facility is complicated by a combination of inconsistent permitting standards and poor understanding of the role of the SRU incinerator, the payoff for incinerator optimisation is a significant decrease in natural gas usage with corresponding savings in operating costs, a decrease in CO2 emissions, and a simultaneous reduction in NOx and SO3 emissions.
The vast majority of the world’s sulphur recovery units (SRUs) are required to process their tail gas streams in an incinerator prior to releasing them to the atmosphere. These incinerators, also commonly called thermal oxidisers, serve two primary purposes. The first purpose is to acceptably combust certain regulated chemical species present in the SRU tail gases before releasing them to the atmosphere. The second purpose is to release the incinerated tail gas to the atmosphere under conditions that will ensure that the residual amount of these same regulated chemical species is well dispersed and diluted in the atmosphere, so that when they eventually reach ground level they will be less than the regulated maximum ground-level concentrations.
Although both combustion and dispersion are improved by increasing the incinerator operating temperature and the excess oxygen concentration, increases in both of these parameters also requires more fuel. Since this incinerator fuel is almost always some type of hydrocarbon stream, most commonly natural gas, hotter operation with more excess oxygen corresponds directly to an increase in CO2 emissions and higher operating costs. In the ideal case, therefore, the incinerator temperature and the excess oxygen concentration would both be maintained at the lowest possible values needed to meet the combustion and dispersion requirements for a given facility. This optimised operation will satisfy both the environmental requirements for the SRU while minimising operating costs and CO2 emissions.
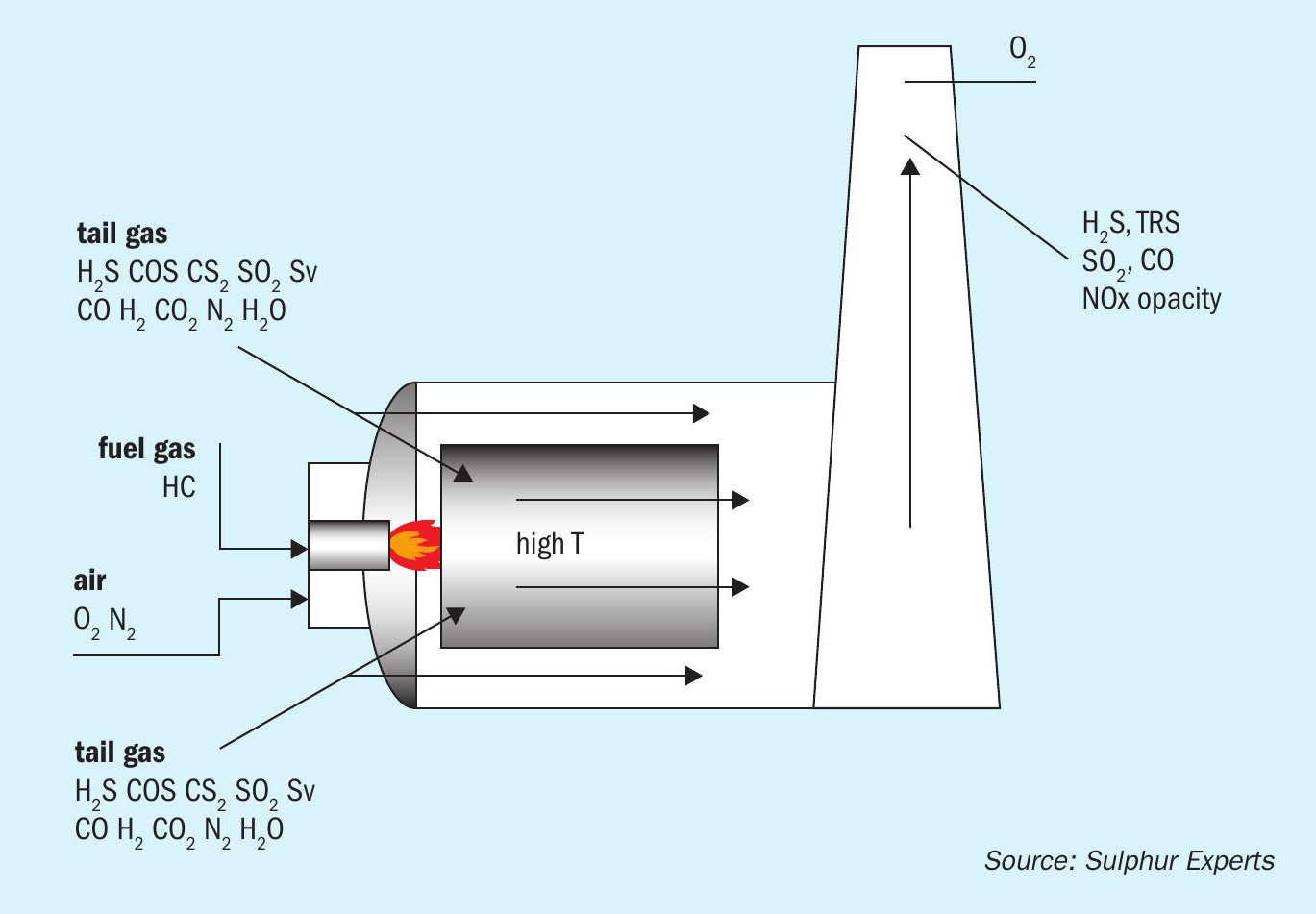
While some jurisdictions have long recognised this desire to balance all aspects of SRU incinerator operation against regulations and have provided clear guidance on how to determine the ideal point, other jurisdictions have not yet invested the time or effort. The USA is one such jurisdiction. USA SRU incinerators, on average, operate at temperatures and excess oxygen levels far above what is actually required to meet their permit requirements, with most SRU operators unaware of the exact regulations which govern their incinerator operations and also generally uninterested (until now) in pursuing incinerator optimisation opportunities.
Two recent trends, however, have begun to change this mindset in the USA: the increased price of natural gas and the increased focus on quantifying and then reducing CO2 emission sources.
Components of interest
The list of regulated chemical species which are almost always present in the SRU tail gas being sent to the incinerator include: H2 S, TRS (H2 S + COS + CS2 – collectively known as total reduced sulphur), SO2 , and CO.
The quantity of each of these components present in the incinerator feed stream(s) depends on the upstream SRU efficiency and operation.
Another commonly regulated chemical group, volatile organic compounds (VOCs), which include aromatic hydrocarbons such as benzene, toluene, ethyl-benzene, and xylene (BTEX), while not usually present in SRU tail gas streams, may be present in some cases.
In addition, although NOT present in SRU tail gas streams, NOx, and SO3 may be created in the SRU incinerator itself under certain conditions and contribute to plume opacity which may be regulated.
Fig. 1 shows a representation of the species of interest in the SRU incinerator.
Applicable regulations
SRU incinerator regulations in the USA are complicated by the fact that they have both a federal (Environmental Protection Agency – EPA) component and a state component, and that regulations are often very site-specific depending on a plant’s history and their specific permitting process or relationship with the local authorities. They are also often further complicated by the fact that regulations may contain some mixture of allowable SRU incinerator stack exit emissions and allowable maximum ground-level concentrations (MGLC), with no clear relationship between these two categories defined in the regulations nor understood by the SRU Operator.
The first step in determining the required SRU incinerator operating parameters for any site is a careful reading of all site-specific operating permits.
Compliance monitoring
For most SRU incinerators, the only emission component actively and continuously measured is SO2 , usually by an online analyser most commonly known as a continuous emission monitoring system or CEMS. While it is technically possible to add CO and NOx measurements to that same instrument, in practice it is very uncommon. H2 S and TRS measurements are technically very difficult if not impossible to achieve since the amount of SO2 relative to these components results in interference problems for the CEMS instrument.
Therefore, instead of continuous measurements of H2 S, TRS, CO, and NOx, concentrations are commonly determined by conducting a “compliance test”, in which a state-approved testing company using state-approved analytical methods determines these values during a relatively short test period. In many cases this compliance test is conducted only once, soon after the SRU incinerator was first brought into operation. In other cases the compliance test needs to be repeated at certain intervals, usually once every one to three years.
Although certain conditions must be met for the compliance test to be valid, such as the SRU operating near its design capacity, the operating parameters for the incinerator itself during the compliance test are left up to the operator. Consistent with the general confusion regarding how an SRU incinerator must operate, the compliance test parameters chosen by the operator are often arbitrary; using the incinerator design conditions, the EPA start-up conditions, previous test conditions, etc. This often leads to compliance tests being carried out at the wide range of conditions; 1,200°F (650°C) to 1,400+°F (760+°C) and with 2 to 5+% of oxygen.
A compliance test conducted at most of these “arbitrary” conditions will almost always result in emissions for all components being much less than allowable limits since:
- SO2 is usually much less than allowable limits because of good upstream SRU operation, and is unaffected by incinerator conditions (ignoring moderate dilution effects);
- H2 S, TRS, and CO limits are also usually much less than allowable limits again primarily because of good upstream SRU operation (discussed in following section), although very hot incinerators with too much excess oxygen further reduces these residuals;
- Although NOx and SO3 will increase with hotter temperature and excess oxygen content, there is usually not enough at any of the SRU incinerator conditions to exceed allowable limits.
If and when the initial compliance test passes, the SRU operator almost never experiments with different (i.e., cooler) temperatures and excess oxygen contents to discover if these would also result in a “pass”. This means that the original arbitrary test condition then becomes the approved “pass” condition and dictates the required operation from that moment on. In short, operating conditions that were given little or no thought during the initial compliance test now become mandatory ongoing conditions and are simply replicated if regular compliance tests are needed.
In a few cases, the compliance test will fail at the initial arbitrary test condition, most commonly because of some combination of too much CO entering the incinerator (poor upstream SRU operation) or a strict CO emission limit. In these cases, the incinerator temperature is increased until a “pass” is achieved, and again this becomes the new regulated temperature with no more effort expended to reduce the CO inlet concentration nor to re-examine the permitted CO emission limit.
In reality, any incinerator operating condition that meets the permitted values during a compliance test can easily become the new approved conditions. The SRU operators simply need the incentive and the will to find the “ideal” conditions rather than just accepting the traditional values, and then to conduct another compliance test to prove the validity of the new, better condition. The “incentive” is that ideal conditions will usually significantly reduce operating costs, reduce CO2 emissions, and even reduce emission rates of some pollutants such as NOx and SO3 .
Typical SRU incinerator inlet compositions
In the USA, the federal EPA requirement that an SRU incinerator emit less than 250 ppm of SO2 means that the total amount of sulphur species (H2 S, COS, CS2 , SO2 , elemental sulphur) present in the SRU tail gas (the incinerator feed) needs to be at or less than that value (ignoring dilution affects from the incineration itself). To meet this requirement, most SRU designs include an amine-based tail gas treating unit (TGTU) that easily keeps the SRU tail gas sulphur species concentration to much less than 250 ppm. Based on 40 recent Sulphur Experts’ tests on USA-based sulphur plants where measurements were available, the “average” or “median” value for H2 S concentrations exiting the TGTU and entering the incinerator were assumed to be 50 ppm of H2 S plus 15 additional ppm of COS and CS2 (65 ppm total), for modelling purposes.
For an SRU incinerator that has clear emission limits assigned to it (ppm values or mass limits that can be converted to equivalent ppm values), destruction efficiencies and corresponding emission limits for H2 S and TRS can be modelled using simulation packages specifically designed for this purpose. These simulators require not only the incinerator inlet conditions, but also require information about the incinerator construction itself (i.e., residence time, “mixing efficiency”, etc.). Although this means that every specific site would require its own site-specific model, for illustration purposes an “average” incinerator design was used along with varying incinerator feed H2 S concentrations to generate the curves presented in Fig. 2.
Using Fig. 2, the “typical” SRU tail gas feed H2 S of 50 ppm would need to be incinerated at around 850°F (455°C) to reduce the concentration to 10 ppm (residual) in the incinerator exit and around 975°F (525°C) to result in 3 ppm (at 3% excess oxygen). These values are much less than the 1,290°F (700°C) “average” incinerator temperature actually in use by USA incinerators.
Even in the “worst case”, with 300 ppm of H2 S present in the SRU tail gas, suggesting a very poorly operated TGTU, 1,075°F (580°C) is all that is needed to have a 10 ppm residual H2 S, and 1,200°F (650°C) for 3 ppm.
Although identical modelling can be conducted for COS, CS2 , and TRS, they are not included in this article due to the fact that there is usually (but not always) a much smaller amount of them in the SRU tail gas than H2 S, and so destruction of these components to an acceptable value is almost always achieved whenever the conditions for acceptable H2 S destruction are met. So again, destruction of these components also does not require the very hot temperatures at which most SRU incinerators actually run.
For those SRU incinerators without specific H2 S or TRS emission requirements, but that still want to adhere to the State’s MGLC requirements, finding the acceptable incinerator temperature is complicated by the fact that dispersion modelling is required for the SRU incinerator exit gas. Again, modelling packages specifically designed for this purpose and acceptable to State authorities are available. These simulators require not only the incinerator outlet conditions and incinerator design information, but also require site-specific meteorological data. Again, although this means that every site should have its own site-specific model, for illustration purposes an “average” incinerator design and “default” meteorological conditions were applied to determine the MGLC for H2 S for a variety of SRU incinerator exit temperatures and exit H2 S concentrations. These data were used to generate the curves presented in Fig. 3.
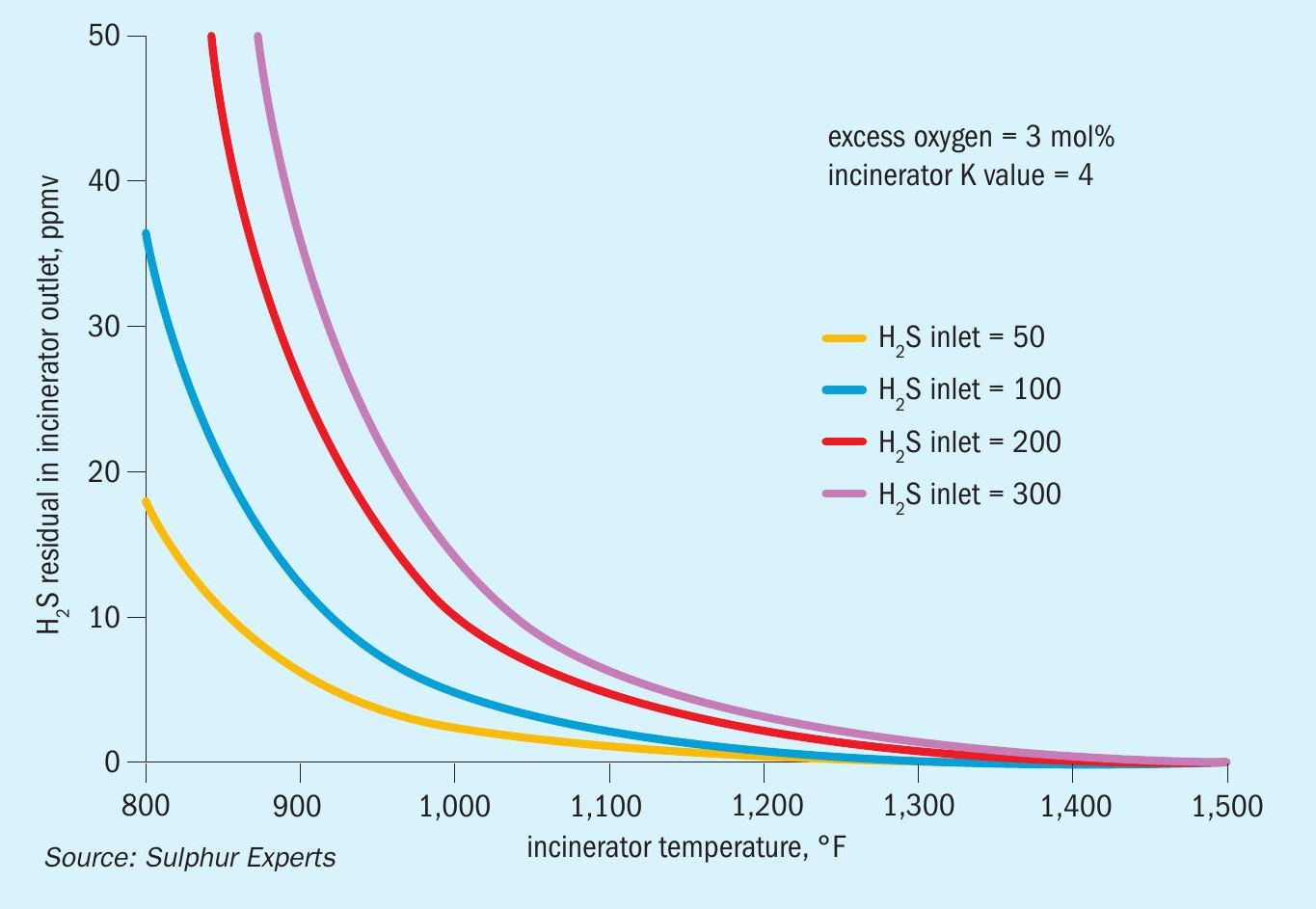
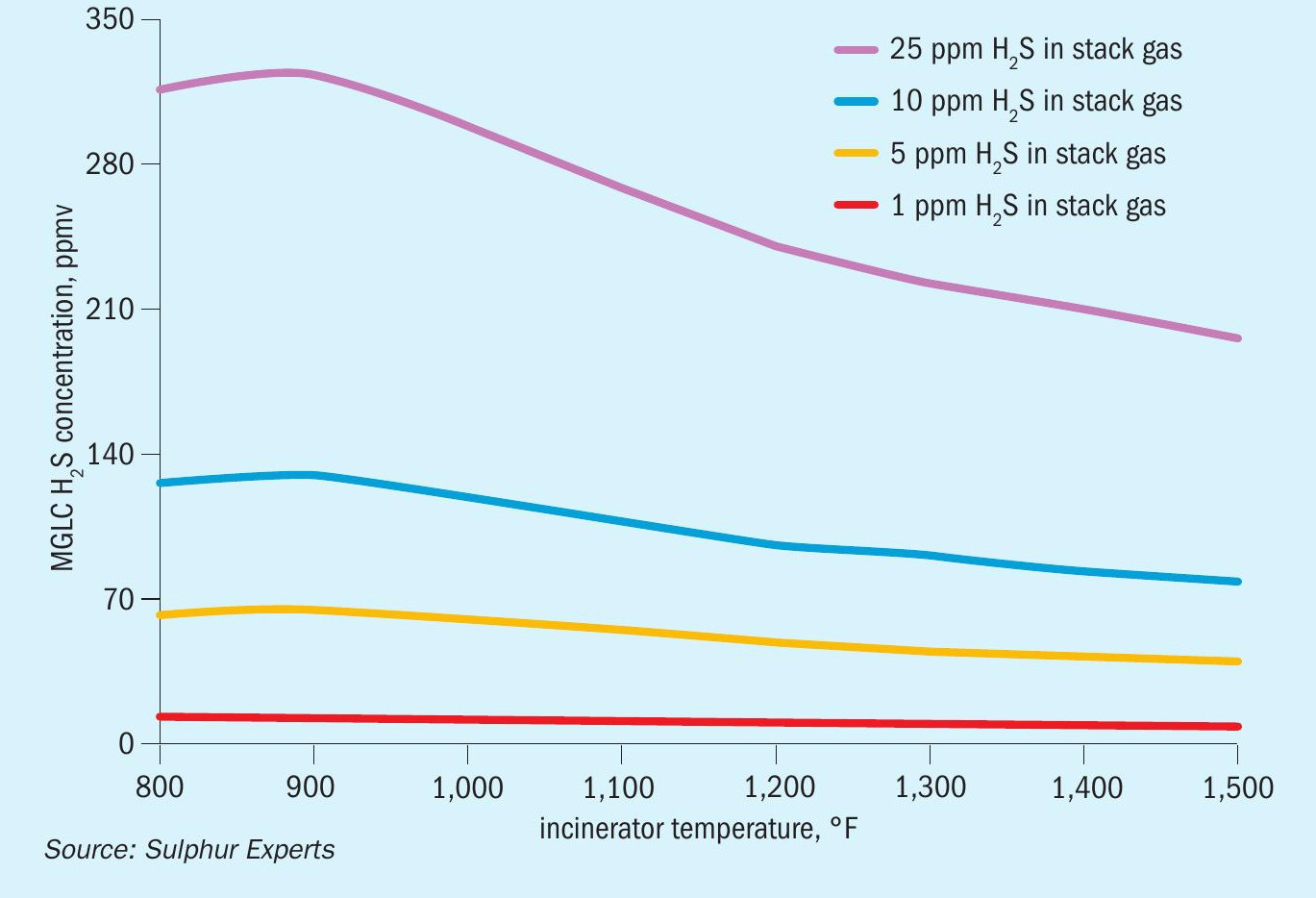
These curves can be used in conjunction with State MGLC regulations to determine acceptable emission temperatures and concentrations. For example, the Texas requirement of 120 ppb for ground-level H2 S would require (for this specific modelled “average” incinerator design and “default” meteorological conditions) there be slightly less than 10 ppm of H2 S leaving the stack at any modelled temperature. Combining this knowledge with the data from measured COS + CS2 values in USA SRU incinerator inlet streams data means that an incinerator temperature of 850 to 900°F (455 to 480°C) would be suitable for a “typical” SRU operation with 50 ppm of H2 S in the SRU tail gas, and around 1,100°F (590°C) even in the “worst case” of 300 ppm of H2 S in the SRU tail gas. Even in California, where the MGLC is 30 ppb for H2 S, SRU incinerator temperatures of no more than 1,200°F (650°C) would suffice.
In many cases, the H2 S and TRS concentrations present in the SRU tail gas are already less than the incinerator emission limits and less than the EPA limit where incineration is not required. In these cases, in theory, the stream could be released to atmosphere directly and a decision regarding some type of incinerator “standby” operation (keeping it hot only for an upset condition where incineration is required) may be appropriate.
The final SRU tail gas component that may require incineration is CO. Although the front-end Claus process used by SRUs actually generates significant CO concentrations from thousands of ppms up to percent levels, the amine-based TGTU technologies used by most SRUs employ a catalyst that reacts this CO to a much smaller concentration. If the TGTU catalyst is working well, CO concentrations leaving this unit would never exceed a few tens to a few hundreds of ppms.
For those SRUs that have no CO emission limits, the SRU tail gas CO concentration has no effect on the chosen incinerator operation and it can be adjusted to suit the H2 S/TRS requirements only.
For those SRUs where the CO in the SRU tail gas is already less than the incinerator emission limit, which is the case for most well-run SRUs with “moderate” CO emission limits of 250 to 1,500+ ppm, again the amount of CO in the tail gas has no bearing on how to best run the incinerator and it can be adjusted to suit H2 S/TRS requirements only.
For those sites with strict CO emission limits in the tens of ppms, again the tail gas from a well-run SRU may already meet even these strict requirements, and destruction of H2 S/TRS will remain the limiting factor. It is only in the relatively few cases where the amount of CO in the SRU tail gas exceeds the emission limit when good incinerator CO destruction will be needed.
In these few cases, the required incinerator temperature depends on the inlet CO concentration and the CO emission limit. As with the H2 S modelling, CO destruction efficiency and corresponding stack gas content can be modelled using simulation packages specifically designed for this purpose. Again, every site would require its own site-specific model, but for illustration purposes an “average” incinerator design was used against a variable incinerator feed CO concentration to generate the curves presented in Fig. 4.
As shown in Fig. 4, good CO destruction requires the incinerator to be relatively hot, at least 1,250+°F (675+°C), to achieve a meaningful reduction in CO concentration. Any apparent decrease in CO emissions at a temperature cooler than this is essentially due to dilution effects alone. Therefore, destroying CO in the SRU incinerator requires temperatures of 1,250+°F (677+°C), and up to 1,500+F (815°C) in some cases, obviously eliminating the opportunity to optimise the incinerator. In these cases it may be wise to either lessen the amount of CO entering the incinerator by improving the TGTU operation, or to revisit the permit CO limit against the large environmental cost of CO destruction.
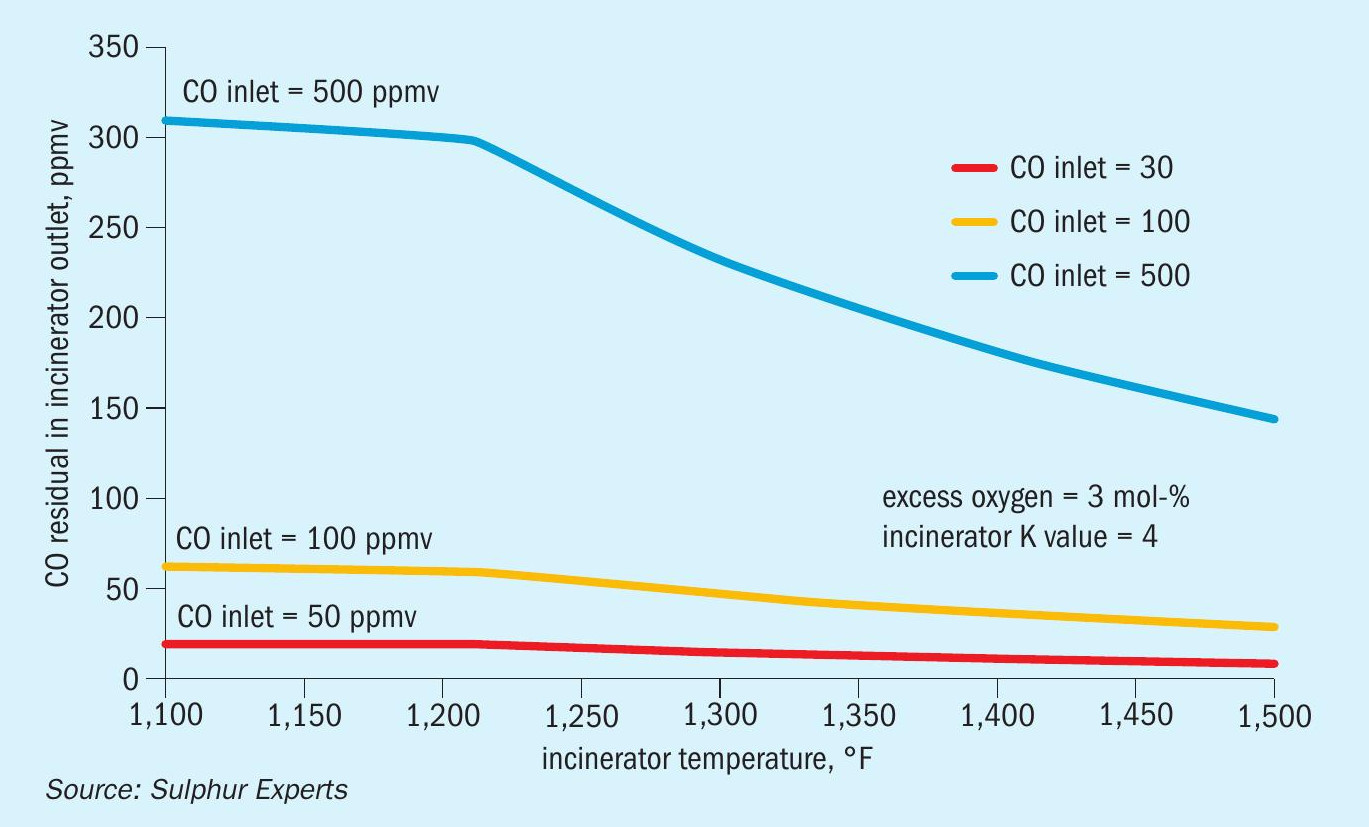
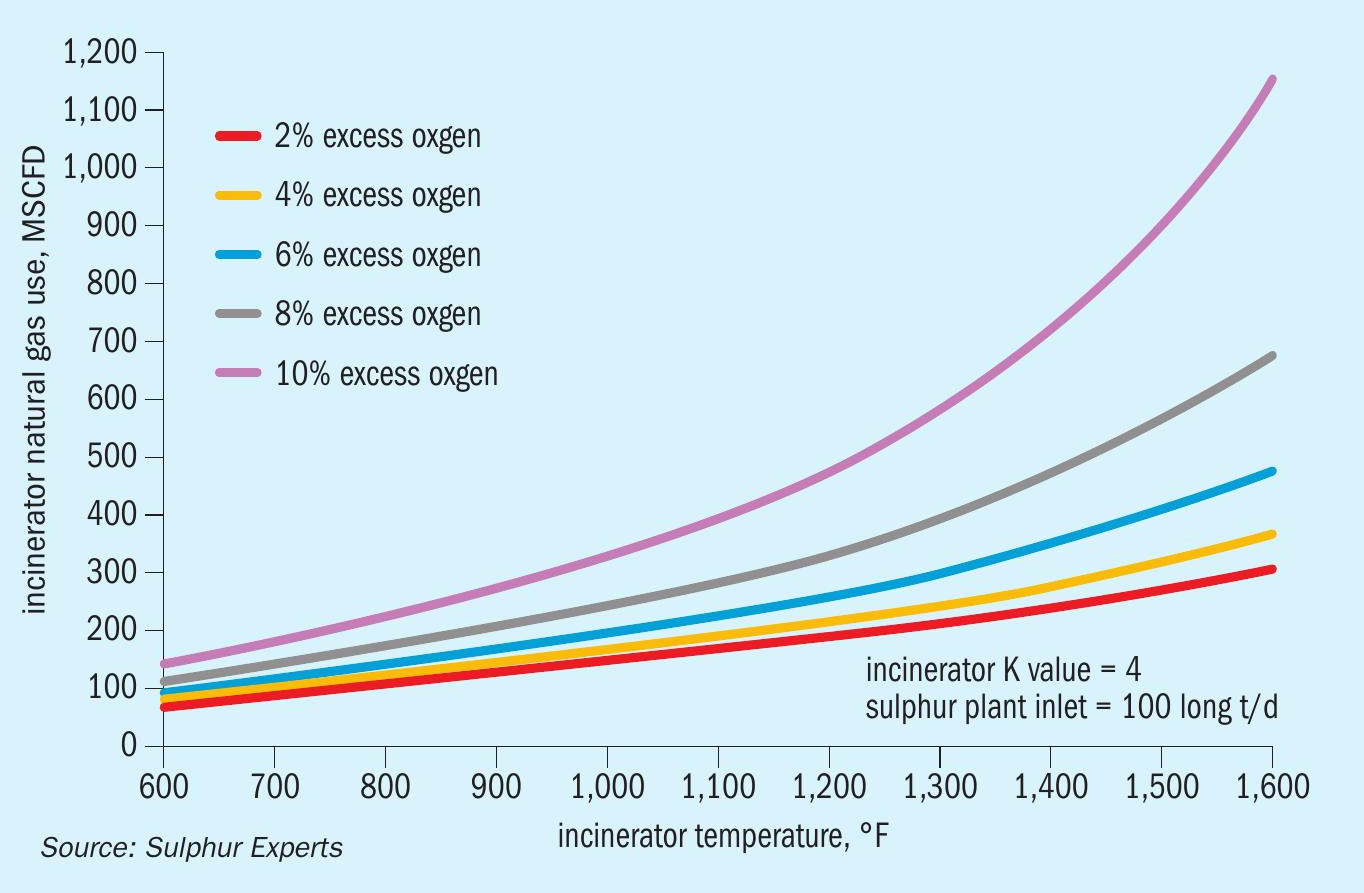
In many cases, the CO concentration (like the H2 S and TRS concentrations) in the SRU tail gas is already less than the incinerator emission limit. In these cases, again, incineration is not even necessary and a decision regarding some type of incinerator “standby” operation may be appropriate.
Incentive to optimise
As already mentioned, incinerator optimisation will reduce fuel gas consumption (usually natural gas) and the associated operating cost, reduce associated CO2 emissions, and reduce the formation of pollutants such as NOx and SO3 .
Recently tested USA SRU incinerators were operating with between 2% and 10% excess oxygen, with an average of 5%. Historical work on SRU incinerators has shown that excess oxygen less than 2% lowers destruction efficiencies, while excess oxygen significantly greater than 2% does not improve contaminant destruction efficiency but merely increases fuel usage (and associated operating cost, CO2 emissions, NOx and SO3 formation) with no other benefit. This is the reason why, in those few cases where excess oxygen requirements are included in permits, levels between 2 and 3% are usually stipulated.

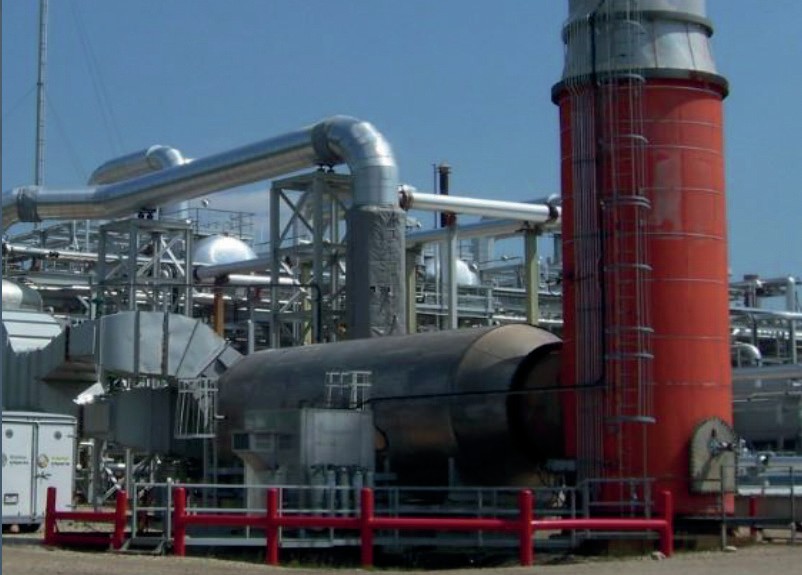
Fig. 5 shows the effect of oxygen concentration on fuel gas usage for a “typical” incinerator attached to a 100 long t/d SRU. Merely dropping the “average” 5% excess oxygen value to 2% excess oxygen and keeping the average temperature of 1,290°F (700°C), results in natural gas requirement declining from approximately 350 MSCFD (10 m3 /d) to around 210 MSCFD (6 m3 /d), a savings of 40%.
For this theoretical 100 long t/d facility, at a 2022 Q3/Q4 average price of around $6.5/million Btu, this represents nearly $400,000 in operating cost savings per year, plus a decrease in CO2 emissions of 3,100 t/a. Escalating the one theoretical 100 long t/d SRU to the USA as a whole (approximately 20,000 long t/d of production from SRUs) the potential savings rise to $80million and 620 thousand tons of CO2 emissions simply with this change alone. The savings for individual sites will obviously ratio up or down depending on the size of the SRU and the initial excess oxygen target, however, the potential savings of merely controlling the excess O2 does indeed appear to be worth the hassle of ensuring regular manual or automatic adjustment of the incinerator air flow rate.
Using the same Fig. 5 data and combining a reduction in excess O2 from 5% to 2% with a cooler operating temperature, from 1,290°F (700°C) down to 1,000°F (540°C), which would easily meet incinerator destruction requirements for most plants, the natural gas requirement declines from the starting 350 MSCFD (10 m3 /d) to around 140 MSCFD (4 m3 /d), a decrease of 60%. For the theoretical 100 long t/d facility, that is nearly a $600,000 annual operating cost savings plus a decrease in CO2 emissions of 4,650 t/a. Applied to the USA as a whole, this represents potential savings of $120 million and 930 thousand tons of CO2 emissions annually. Potential savings for individual sites will again ratio up or down depending on the size of the SRU, the initial excess oxygen concentration and temperature, and the final values. The potential savings, however, are large enough for most sites to spend the time and effort to conduct the type of evaluation presented in this paper.
One final potential route to save fuel in a SRU incinerator, in addition to evaluation and optimisation of the temperature and oxygen, is to mechanically upgrade the mixing / combustion efficiency of the incinerator itself. All of the destruction modelling shown in this article has been conducted using an “average” mixing efficiency (known as a “kinetic value”) of “4”. Fig. 6 shows examples of low and high “K” value incinerators, while Fig. 7 shows the effect of different kinetic values on the H2 S destruction efficiency, with improved (higher) kinetic values achieving the same H2 S destruction efficiency at a cooler and cooler temperature. Depending on the starting K value of a specific incinerator, and the fuel and CO2 savings associated with upgrading the incinerator, mechanical upgrades such as burner changes, checker walls, air blowers, or full incinerator replacements may pay for themselves relatively quickly.
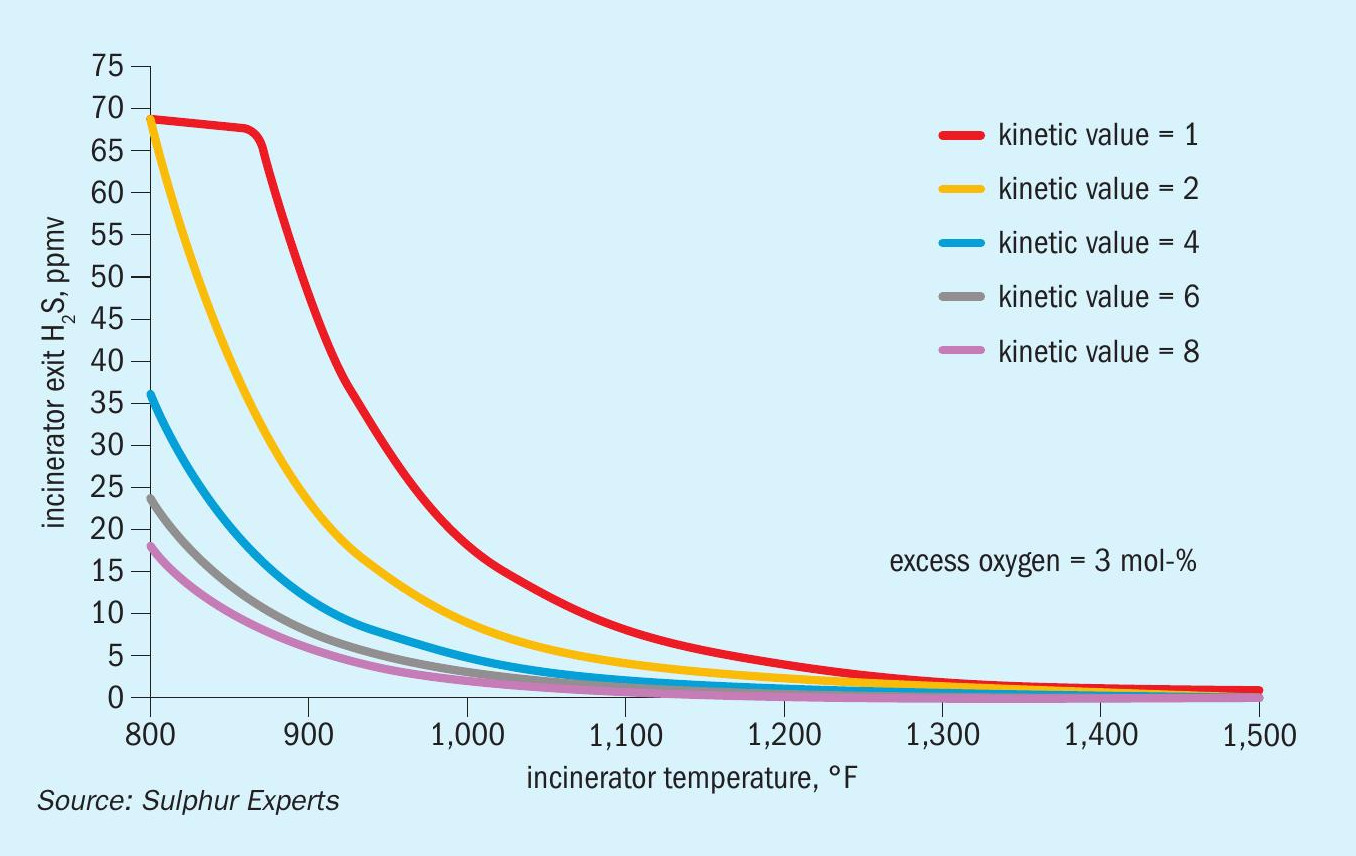
Additional considerations
There are also a number of other operating variables that might affect the ability of the SRU operator (and the permitting authority) to determine optimal operation. These are discussed briefly below.
Downstream heat exchange
Because of the relatively high operating temperature of most SRU incinerators, some designers and operating companies choose to add heat recovery (steam generators, steam superheaters, process gas exchangers, etc.) immediately downstream of the incinerator. Although relatively uncommon in the USA but customary in Europe, a number of USA SRUs do have this type of design. In these cases, extra natural gas burned in the SRU incinerator is not “wasted” since it provides additional thermal energy for the exchangers to recover. The ability to or desire to decrease the temperature and excess oxygen in these units, therefore, must also consider the downstream heat recovery systems.
Volatile organic compounds (VOCs)
As discussed previously, most SRU incinerators do not have VOCs in the SRU tail gas or in the fuel gas being used in the incinerator. In some cases, however, there may be VOCs in the tail gas, i.e., where impure hydrogen streams are added to the TGTU process gas. In other instances, VOCs may be added via a separate stream to the incinerator (i.e., with flash gases), or they may be present in the incinerator fuel (i.e., where refinery fuel gas is used instead of natural gas). If the VOC content is large enough and if the incinerator permit stipulates a VOC limit, then these components require much hotter temperatures, similar to those required for CO destruction (1,250+°F), which may restrict the optimisation opportunities for the incinerator.
TGTU bypassing
The amount of H2 S, TRS, and CO leaving the SRU when the TGTU is in operation is very small, meaning little if any incinerator destruction is required for these components. If, however, the TGTU is bypassed, all of these concentrations, especially for H2 S and CO, will increase significantly. For SRUs where TGTU bypassing is not allowed or not possible, then this does not factor into the determination of an optimised incinerator. For plants which can and do occasionally bypass the TGTU, however, a hotter SRU incinerator would be required to meet the same emission guidelines for those bypass periods.
This leaves the permitting authority and the SRU Operator with two options: 1) use the temperature needed for TGTU bypass operations all of the time, just to be ready for the occasional brief bypass; or 2) ramp up to the hotter temperature only when the TGTU is bypassed, recognising that it may take a few hours to achieve the necessary temperature (since ramp-up rates are limited by mechanically-acceptable temperature change rates for the incinerator). A number of jurisdictions outside of the USA use a two-tiered incinerator temperature approach to manage the with- and without-TGTU cases, and the US EPA has already set acceptable conditions for SRU “start-up and shutdown” that may also be applicable to TGTU bypass cases (i.e., 1,200°F and 2% excess O2 ).
Incinerator quality
In a few of Sulphur Experts historical cases, SRU incinerators are so poorly designed or in such disrepair that they actually generate CO or soot (particulate matter – PM) in normal operation. Testing can confirm if this is true for any given incinerator and, in these cases, hotter temperature or more excess oxygen may be needed simply to overcome the poor design. Especially in these cases, mechanical upgrades to the incinerator (i.e. improvements in the “K” value) would likely pay out quickly in reduced fuel gas usage and CO2 emissions.
Incinerator turndown
Certain incinerator designs may also simply not be mechanically capable of operating with the reduced fuel and air rates associated with optimised operation; they were designed for “worst case” conditions and may not have the “turndown” ability to operate at 50+% below this maximum firing rate. Again, in these cases, it would be wise to consider mechanical upgrades to improve their turndown to use less fuel gas and air.
Applicability to other jurisdictions
Although the primary focus of this article was on USA SRU incinerators, the same methodology is applicable to incinerator operations in any country and any jurisdiction:
- determine the precise emission or MGLC limits in place;
- determine the concentrations of the controlled species in the SRU incinerator feed gases;
- conduct modelling and then field testing to determine the lowest combination of excess oxygen and incinerator temperature that will achieve the required emissions;
- evaluate needed permit changes or discuss options with permitting authorities;
- change the incinerator operation.
This exact procedure has been in place in Alberta, Canada for decades, and is known as the “stack top temperature reduction”, or STTR, program. Not surprisingly, Alberta SRU incinerators typically run between 600°F (315°C) and 1,000°F (540°C), with regular automatic or manual adjustments to the incinerator air flow, requiring significantly less fuel gas than comparable USA facilities.
Like in the USA, many other jurisdictions outside of Alberta have simply not put in the time and effort to understanding the exact SRU incinerator requirements for their specific facility. It is hoped that the incentives outlined in this article regarding fuel gas reduction, CO2 emission reduction, and reduced NOx and SO3 formation will also increase interest in this topic in other jurisdictions.
Acknowledgement
This article is an abridged version of a paper by Gerald E. Bohme and Peter J. Seville of Sulphur Experts Inc., “How better understanding of SRU incinerators can simultaneously save money and reduce emissions,” presented at the Laurance Reid Gas Conditioning Conference February 20-23, 2023, Norman, Oklahoma USA.