Fertilizer International 522 Sept-Oct 2024
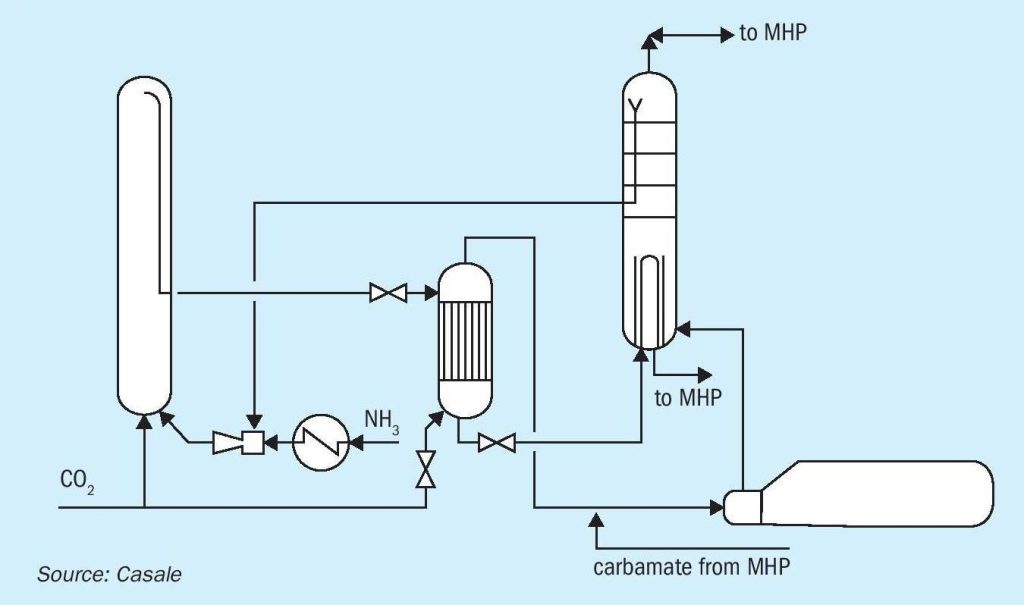
30 September 2024
Nitrogen technology showcase
Nitrogen technology showcase
We highlight recent production advances and innovations in nitrogen fertilizer production from Casale and Stamicarbon, two global leaders in process technology.
CASALE
HYPER-U – a novel high efficiency self-stripping urea process
Since the 1970s, the ammonia or self-stripping process has offered an alternative to the CO2 -stripping process for urea synthesis, and is valued for its competitive energy consumption and operational costs.
The CO2 -stripping process decomposes carbamate at synthesis pressure using CO2 . The self-stripping process, meanwhile, relies on heating and requires purification at medium pressure (MP) due to the presence of excess ammonia in the urea solution.
The self-stripping process, although initially viewed as more complex than CO2 – stripping, was later successfully adopted because of its efficient steam consumption and ease of operation. The advantages of self-stripping process include its:
- Horizontal layout
- Smaller high-pressure equipment
- Reliable operation
- Excellent energy performance.
It does have some drawbacks, however, such as the need for dual-pressure purification stages, separate ammonia recovery, and the requirement for noble materials in the HP stripper.
The introduction of heat recovery from medium-pressure carbamate vapour resulted in a major improvement in the steam consumption of the self-stripping process. This type heat integration became standard in new and revamped plants in the 1990s. Since then, however, no significant improvements in energy optimisation have been made, with this seemingly having reached a plateau.
Modern CO2 -stripping processes include a medium-pressure purification stage as a key feature to lower their medium-pressure (MP) steam consumption. Any further improvement in the efficiency of self-stripping is a challenge as it requires further reductions in MP steam consumption in the HP stripper without destabilising the steam network. This is only possible by dramatically improving heat recovery. Indeed, heat recovery must nearly double to compete with the best CO2 -stripping processes.
Casale has now developed an improved self-stripping process, known as HYPER-U, that cuts medium-pressure steam consumption further and reduces cooling water needs. The main innovation is the introduction of an additional carbamate decomposition step before the conventional medium-pressure section. This enhances heat recovery while reducing low-pressure (LP) steam and cooling water needs.
HYPER-U process
The most innovative features of HYPER-U are the ‘hybrid-stripping’ and ‘combi-reactor’ concepts.
The HYPER-U process adopts a hybrid approach that blends the best aspects of both CO2 -stripping and self-stripping processes, resulting in much higher efficiency. A minor portion of CO2 is fed to the bottom of the high pressure (HP) stripper. This drastically lowers the amount of ammonia that needs to recovered at medium-pressure by reducing the amount of free ammonia in the urea solution leaving the HP section (simplified flowsheet, Figure 1). This in turn favours greater heat recovery by allowing the condensation of carbamate vapour at a higher temperature profile.
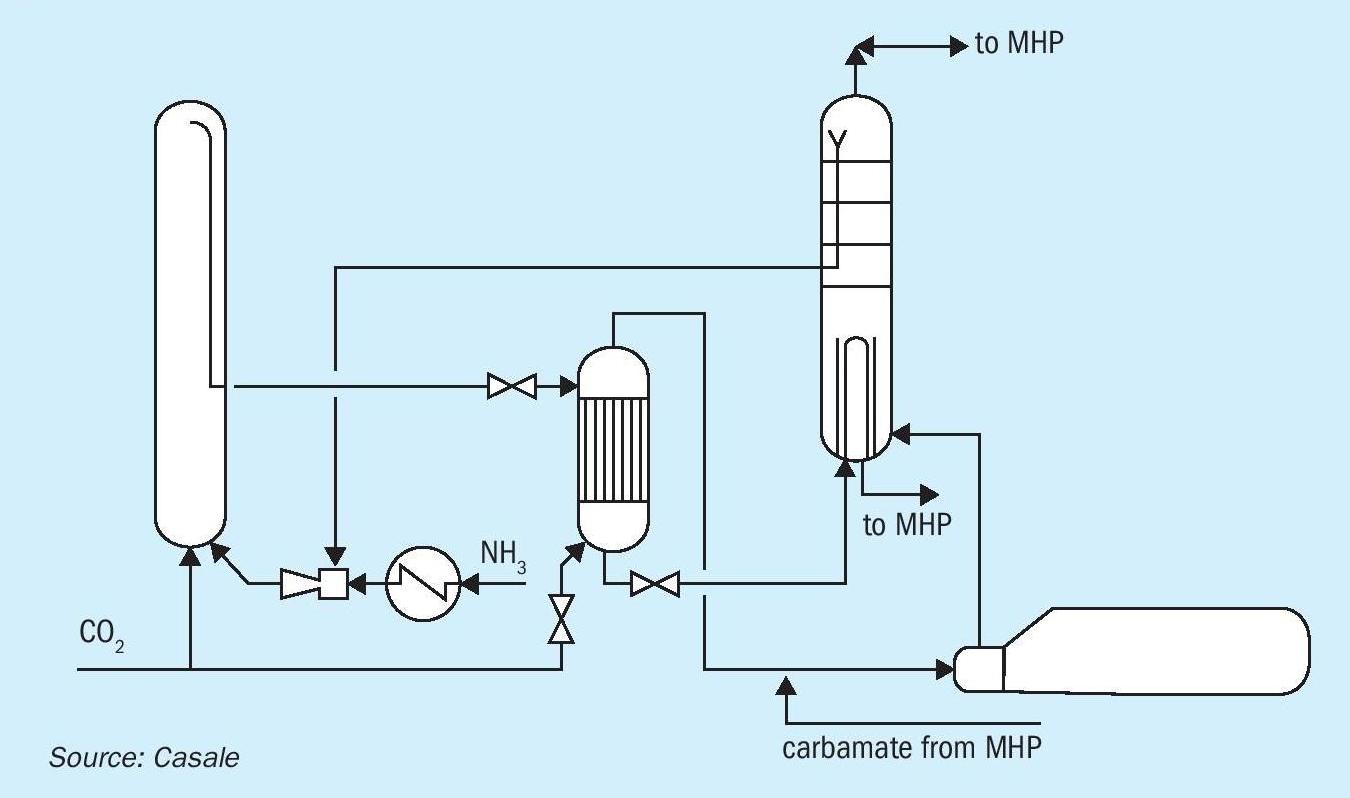
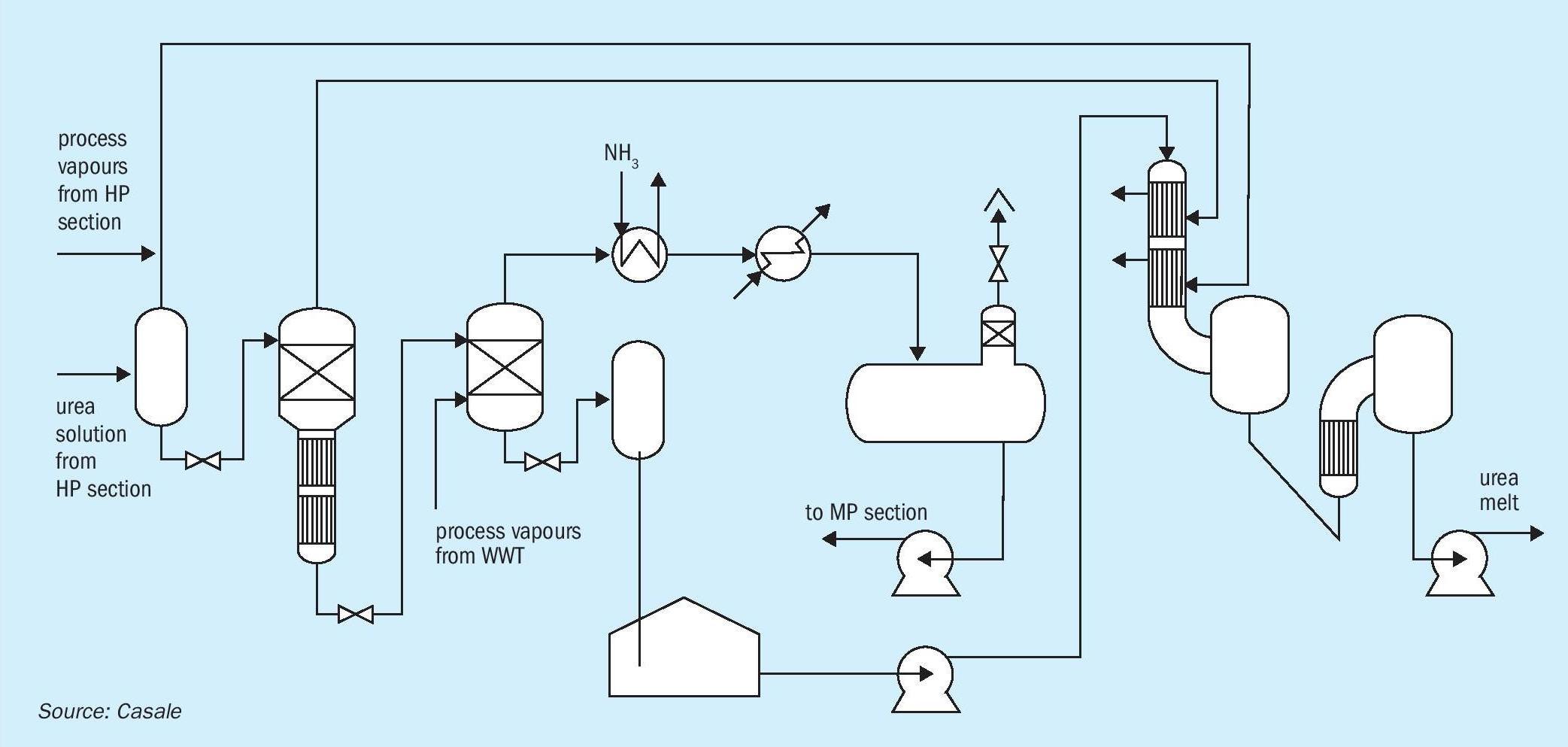
Vapour from the HP stripper is partially condensed in a kettle-type heat exchanger, generating steam at 5.0-6.0 barg. However, most of the condensation occurs in a vertical combi-reactor. Essentially, this is a combined HP condenser-reactor vessel that is comprised of a tube bundle and trays. The volume of the combi-reactor ensures that the conversion of CO2 into urea begins by providing an adequate residence time. Excess heat from the condensation of high-pressure carbamate vapour is removed via direct process-process heat transfer. The heat released is then used for carbamate decomposition at 30 barg.
A critical aspect of the HYPER-U process is the inclusion of an extra carbamate decomposition stage. The urea solution from the HP stripper is first expanded to 30 barg and fed to the tube bundle (tube side) in the combi-reactor. Direct process-process heat exchange provides effective carbamate decomposition even at 30 barg. Following the 30 barg purification stage, the urea solution is then fed to the conventional medium-pressure sections for final purification.
This final carbamate decomposition stage at 3.5 barg also incorporates another innovative concept. Instead of heating the urea solution via a shell-andtube exchanger using LP steam, carbamate decomposition occurs in a column with a packed bed – with the heat of reaction provided by process vapours from the waste water treatment (WWT) section. Using the heat of condensation of WWT vapour for LP carbamate decomposition is advantageous as it offers direct heat integration. Using WWT vapour in this way has another major advantage: it avoid the use of several pieces of equipment normally required for this service.
Concentration of the urea solution – up to 96.5-99.7 weight percent depending on the product finishing technology – is carried out in a single or double vacuum evaporation section (simplified flowsheet, Figure 2). The first stage evaporator uses carbamate vapour (at 30 and 18 barg) from the medium-high and medium-pressure carbamate decomposers as a heat source. The condensation curve of the vapour at 30 barg follows a higher temperature profile than is possible conventionally. This enables the urea solution to be concentrated to up to 95 weight percent using only heat recovered from process streams without relying on steam. Consequently, HYPER-U achieves a 60 percent higher steam saving, compared to the conventional self-stripping process where MP carbamate vapours are used to concentrate urea solution to 84-85 weight percent typically.
The heat integration strategy also includes the traditional ammonia preheating step that captures the heat of condensation from low-pressure carbamate vapours.
HYPER-U also incorporates carbamate pre-heating: carbamate is recovered downstream of the HP loop at 110-115°C. This is in contrast to the conventional self-stripping process where carbamate solution is recovered at 80-85°C. This higher temperature, made possible by operating at 30 barg pressure, increases steam production in the HP carbamate condenser by approximately 40 kg/MT.
Steam and cooling water saving strategy
The overall heat integration strategy of HYPER-U is to maximise the use of process heat sources to replace low-pressure steam. Condensing carbamate vapour at 30 barg along an elevated temperature profile makes it possible to exploit enthalpy in a way that is impossible in the conventional self-stripping process. Consequently, overall steam demand for urea purification and concentration is drastically reduced.
The lower steam demand in downstream plant sections, by limiting the duty of the HP stripper, avoids upsetting the steam network. Reducing medium-pressure steam consumption in the HP stripper results in less 5.0 barg steam being produced in the HP carbamate condenser. It is crucial, to balance LP steam demand and production, to minimise the steam demand for purification and concentration. The heat integration strategy achieved with HYPER-U reduces the supply of 20 barg steam to the HP stripper without needing to make up the 5.5 barg header. The consumption of 20 barg steam of the HP stripper is approximately 20 percent lower than in conventional self-stripping processes.
A notable positive side effect of enhanced heat recovery with HYPER-U is significantly lower cooling water consumption. Maximising the heat recovery for process use reduces the amount of heat wasted in cooling water. Overall, a 12-14 percent cooling water saving can be achieved.
Other advantages
HYPER-U’s hybrid-stripping concept also influences the size of the HP stripper.
Conventionally, in modern self-stripping, the temperature within the HP stripper tubes follows a linear profile, ranging from 189°C at the top to 203-204°C at the bottom. Whereas in HYPER-U the bottom temperature is kept at 195-197°C and the duty is correspondingly 20 percent lower. HYPER-U also has a positive impact on the cost of the HP stripper as maintaining the same steam pressure reduces the required surface area.
The cost of ammonia recovery equipment, such as ammonia condenser and MP absorber, is also reduced due to hybrid-stripping. This is because the free ammonia content of the urea solution leaving the HP stripper in HYPER-U is 40 percent lower. The cost of the HP ammonia pumps and their overall power consumption are also reduced as the flow rate of ammonia handled by these pumps is cut by 20 percent.
Conclusions
The HYPER-U process offers a significant improvement in energy performance compared to conventional and established self-stripping technology. Notable features include:
- The hybrid HP stripper design – which uses a minor CO2 stream to lower free ammonia.
- The ‘combi-reactor’ – a combined vertical HP carbamate condenser and reaction vessel. This reactor enables direct process-process heat exchange for carbamate decomposition at 30 barg.
These features, by enabling efficient heat integration in the purification sections, offer reduced LP steam demand. Consequently, the duty of the HP stripper is reduced by 20 percent compared to conventional self-stripping processes. Similarly, the consumption of MP steam from the CO2 compressor turbine is also lower.
Comprehensive heat recovery in the carbamate recovery section also reduces cooling water consumption by 12-14 percent, reducing make-up water and the electricity used by cooling towers and pumps.
The overall performance of the HYPER-U process is competitive with all urea processes currently available, whether these are based on self-stripping or CO2 stripping technology. Moreover, because fewer and smaller pieces of equipment are used, this excellent energy performance is achieved without increasing capital expenditure.
STAMICARBON
Operator training simulators: ensuring successful urea plant start-up
In this article, Stamicarbon’s Rahul Patil and Nikolay Ketov explore how the use of digital tools – including an operational training simulator developed by Stamicarbon – enables the smooth start-up and operation of modern urea plants, thereby enhancing overall plant efficiency and safety.
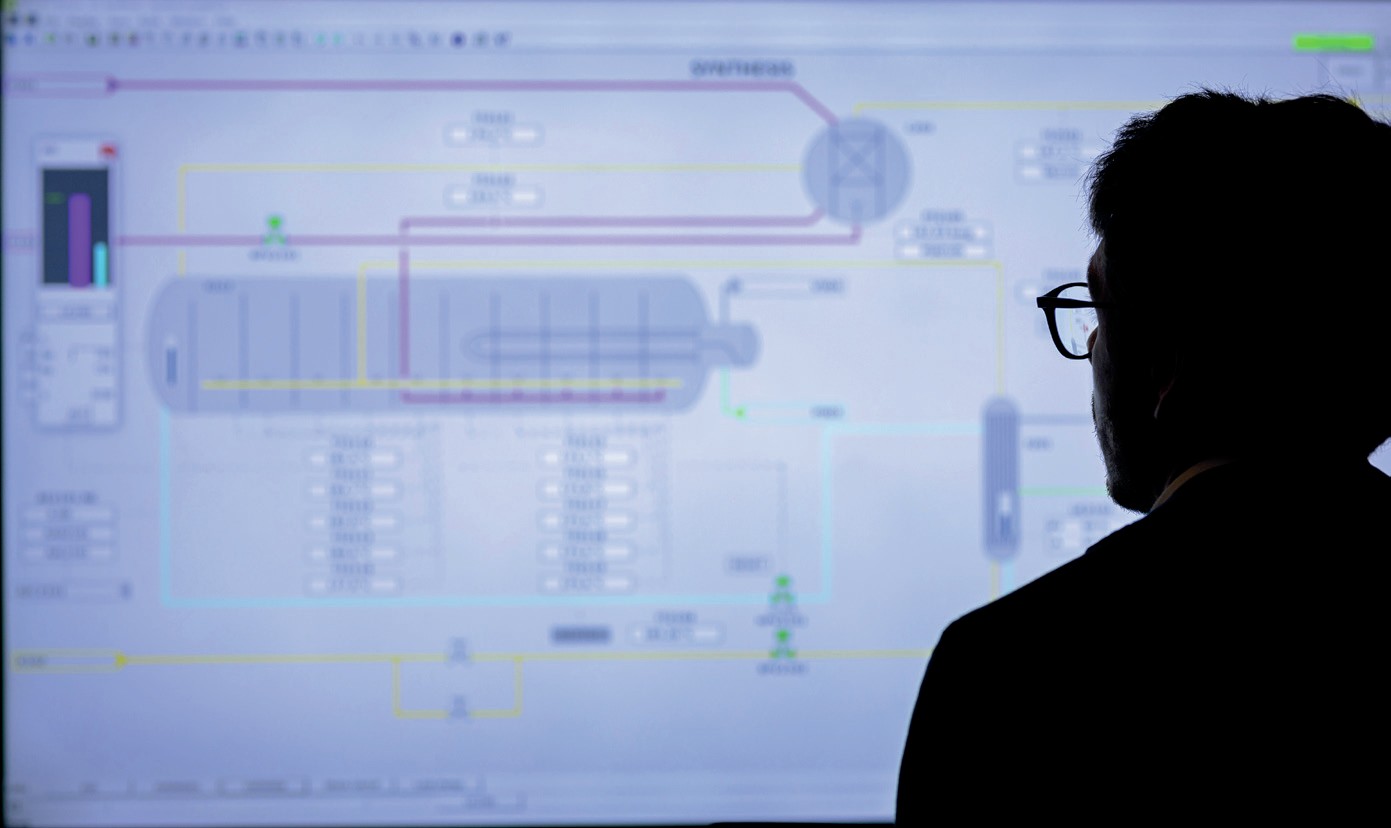
Modern urea plants require successful solutions to the complex challenges they face in order to ensure efficient, safe, and cost-effective operations. The successful integration of digital tools during plant start-up and subsequent operations is therefore a landmark development that marks a significant advance for the fertilizer industry.
Notably, operator training simulators, by providing comprehensive training and preparation for plant operators, have emerged as a critical digital solution.
Urea technology
Stamicarbon, the nitrogen technology licensor of MAIRE S.p.A., is a market leader in urea technology globally. The Netherlands-headquartered company is continuously innovating and introducing new solutions that extend the lifetime of urea plants, reduce emissions and lower their energy consumption.
Stamicarbon is renowned for its pioneering urea production technology, including the introduction of the CO2 stripping process – a landmark invention – in the 1960s. Since then, the company has been improving and perfecting urea technology to optimise operational performance.
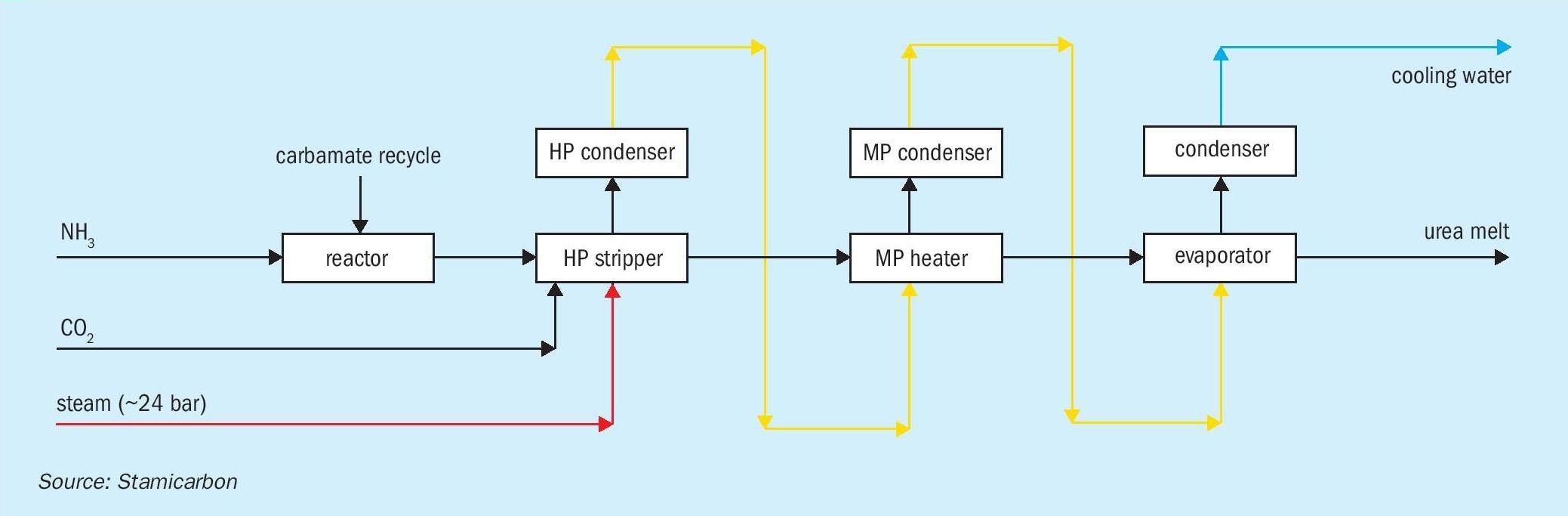
Stamicarbon’s most recent breakthrough in urea technology is its Ultra-Low Energy (ULE) design. This technology significantly enhances the energy efficiency of urea production. The core improvement introduced by this innovation is that process heat – in the form of steam – is used three times in the ULE design (Figure 1) instead of two in the conventional urea process.
The primary advantage of the ULE design is the significant energy savings delivered by introducing a medium-pressure (MP) recirculation section. This section captures steam heat three times. It is configured to flash and then reheat carbamate at medium pressure using the heat of reaction and condensation. This reheated carbamate then recovers heat via evaporation. As a result, steam consumption and cooling water consumption can be reduced by up to 40 percent and by about 16 percent, respectively, compared to traditional CO2 stripping. This process configuration also achieves an impressively low steam consumption of less than 560 kg per tonne (kg/t) of urea, versus approximately 870 kg/t in traditional CO2 stripping processes.
Alongside Stamicarbon’s extensive experience in designing new plants, the ULE concept can also be used to revamp existing urea plants, regardless of the original technology provider.
Stami digital suite
Stamicarbon, building on decades of pioneering urea technology, has developed a suite of digital services that enhance operational effectiveness and boost productivity at urea plants – as well as supporting employee training. Creating a realistic digital model of a urea plant requires extensive experience and specialised knowledge to accurately simulate the complex physics of urea and carbamate mixtures.
Stamicarbon’s process monitor tool is one of the key technologies featured in this digital portfolio. This monitor offer superior prediction capabilities by using a knowledge-driven mathematical model of the urea plant.
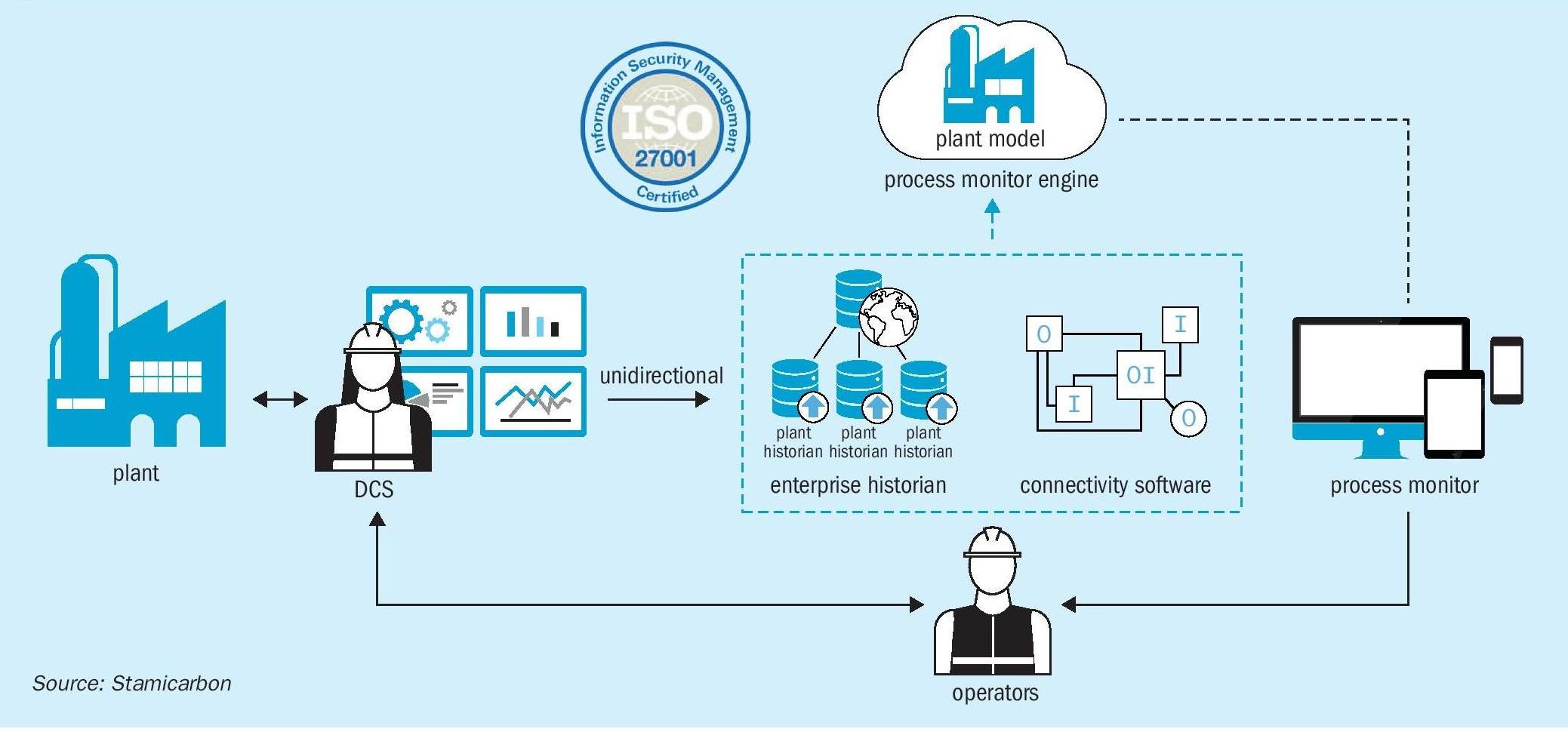
The model behind the process monitor is actually very similar to those used to design urea plants and, for example, includes mass and heat transfer equations, reaction kinetics, vapour-liquid equilibria, and hydrodynamic criteria that cover the entire plant. In total, the plant model consists of more than 5,000 linear and non-linear equations. A process flowsheet programme – developed in-house and based on these equations – then ensures fast solutions to large and complex operational problems.
The process monitor feeds real-time plant data into the digital plant model (Figure 2). This then calculates key performance indicators (KPIs), such as plant load, energy consumption and emissions, as well as soft sensor key variables, such as equipment efficiency, load, and reactor conversion. The processed data generated is then made available to plant operators and others via an intuitive dashboard.
The Stami digital process monitor has already demonstrated its effectiveness by improving decision-making and operational excellence at urea plants since the first references were installed in 2020. These have delivered higher plant loads and reduced plant energy consumption.
Operator training simulator
Another digital tool developed by Stamicarbon, an operator training simulator (OTS), instructs plant operators on start-up and shutdown procedures, dayto-day plant operations, and various other operational scenarios. This high-fidelity simulator is an efficient training tool that helps operators understand the dynamic behaviour of urea melt and granulation plants. It also provides effective preparation for emergencies by simulating ‘upset’ conditions for plant operators in an entirely safe digital environment.
A significant advantage of the OTS is its ability to offer bespoke and tailor-made training to personnel, as it uses thermodynamic and kinetic models that are specific and unique to individual urea plants. The simulator provides plant operators with comprehensive training on the urea process and the dynamic behaviour of urea plants.
OTS training covers standard operating procedures including normal operation, plant start-up, blocking-in, restarting and draining. As already indicated, the models used by the OTS can safely simulate upsets at the plant. This allows operators to practice, as part of their training, bringing the urea plant back to normal operation in response to upset conditions.
The OTS can be configured to precisely replicate Stamicarbon’s Ultra-Low Energy urea plant design. This includes the process equipment, plant control, interlocking systems, and the safety trip system (STS). The simulator’s distributed control system (DCS) interface mimics the exact look and feel of an actual operations room. Additionally, it trains operating staff to run the plant at maximum capacity, while minimising steam consumption and ammonia losses. It also allows new and modified operating procedures to be properly tested before these are subsequently implemented. The resulting improvements in staff knowledge and experience lead to safer and more stable urea plant operations. By providing operators with a thorough understanding of urea plant dynamics, the OTS also helps to reduce plant start-up delays by avoiding unwanted start-up trips.
OTS – plant start-up case studies
One of the benefits of Stamicarbon’s Ultra-Low Energy design is its ease of operation compared to traditional plants. In particular, the design is more operationally stable by incorporating a MP recirculation section. This new design helps mitigate disturbances that can occur in traditional CO2 stripping plants when liquid is discharged directly from the stripper into the low-pressure section. Additionally, the safety and efficiency of Ultra-Low Energy plants can be further improved by OTS training to prepare operators for a variety of operational scenarios.
The 2,334 t/d capacity urea plant at Jinjiang Xinlianxin in China was the first facility to operate with Ultra-Low Energy technology following its successful startup in February 2021. Stamicarbon comprehensively trained the plant’s staff using its OTS prior to start-up. Consequently, having provided a thorough understanding of expected reactor and plant behaviour, the start-up went very smoothly without any issues from the first attempt.
Initially, the Jinjiang Xinlianxin plant operated at a turndown capacity. Then, after securing the feedstocks, the plant’s capacity was increased to more than 100 percent during the first week of operation. Notably, the plant was commissioned and entered production during the challenging Covid-19 lockdown period in China. Yet, thanks to the OTS, the staff were able to be trained remotely – allowing the plant’s start-up to proceed normally without the need for on-site support from Stamicarbon.
The training of operators at Gemlik Gübre’s urea melt and granulation plant in Gemlik, Turkey, is another example of the successful use of the OTS. The Gemlick plant is another Ultra-Low Energy design and has a production capacity of 1,640 t/d for urea and 500 t/d for urea ammonium nitrate (UAN).
Gemlik Gübre’s OTS is a tailor-made simulator that incorporates a high-fidelity, real-time model of the urea plant and is more than 98 percent accurate in simulating the plant’s dynamic behaviour. This OTS provides operators with comprehensive training and in-depth knowledge of plant behaviour – with this helping them to deliver:
- Faster start-ups
- Rapid recovery from plant upsets
- Higher plant on-stream time
- Increased plant safety
- Lower emissions
- Substantial operational cost savings over the plant’s lifetime.
Conclusion
Stamicarbon offers technological solutions, products, and services for urea plants that are tailored to the specific requirements of customers. The company’s solutions for urea synthesis – such as its Pool Condenser, Pool Reactor and Ultra Low Energy designs – result in increased plant efficiency, reduced operating and maintenance costs, and lower plant emissions. Adopting a full life cycle philosophy, Stamicarbon partners with its clients to design, build and operate urea plants, while continuously seeking improvements and providing support.
Stamicarbon, by leveraging its extensive expertise in nitrogen technology, in collaboration with sister companies from MAIRE S.p.A., offers a digital toolbox to optimise plant operations – both in urea production and other chemical processes. The Stami Digital portfolio includes a wide suite of digital services and is backed by proven track record of effective improvements in plant load and reductions in energy consumption.