Nitrogen+Syngas 393 Jan-Feb 2025
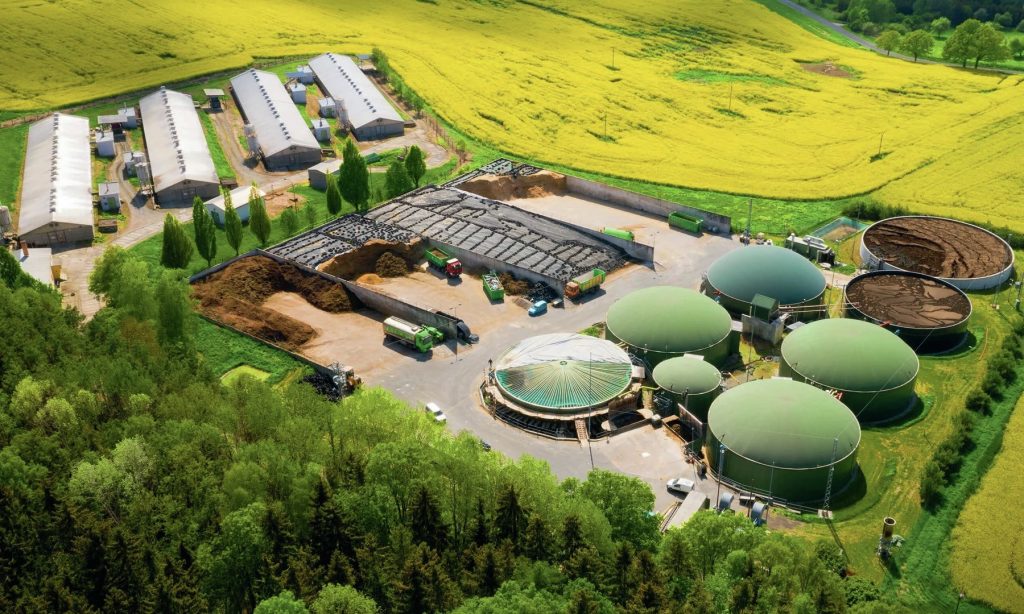
31 January 2025
Biomass as a feedstock
FEEDSTOCK
Biomass as a feedstock
While there is still a considerable push for use of biomass waste as a lower carbon feedstock for chemical production via gasification to syngas, biological processes such as fermentation are increasingly gaining traction as an alternative.
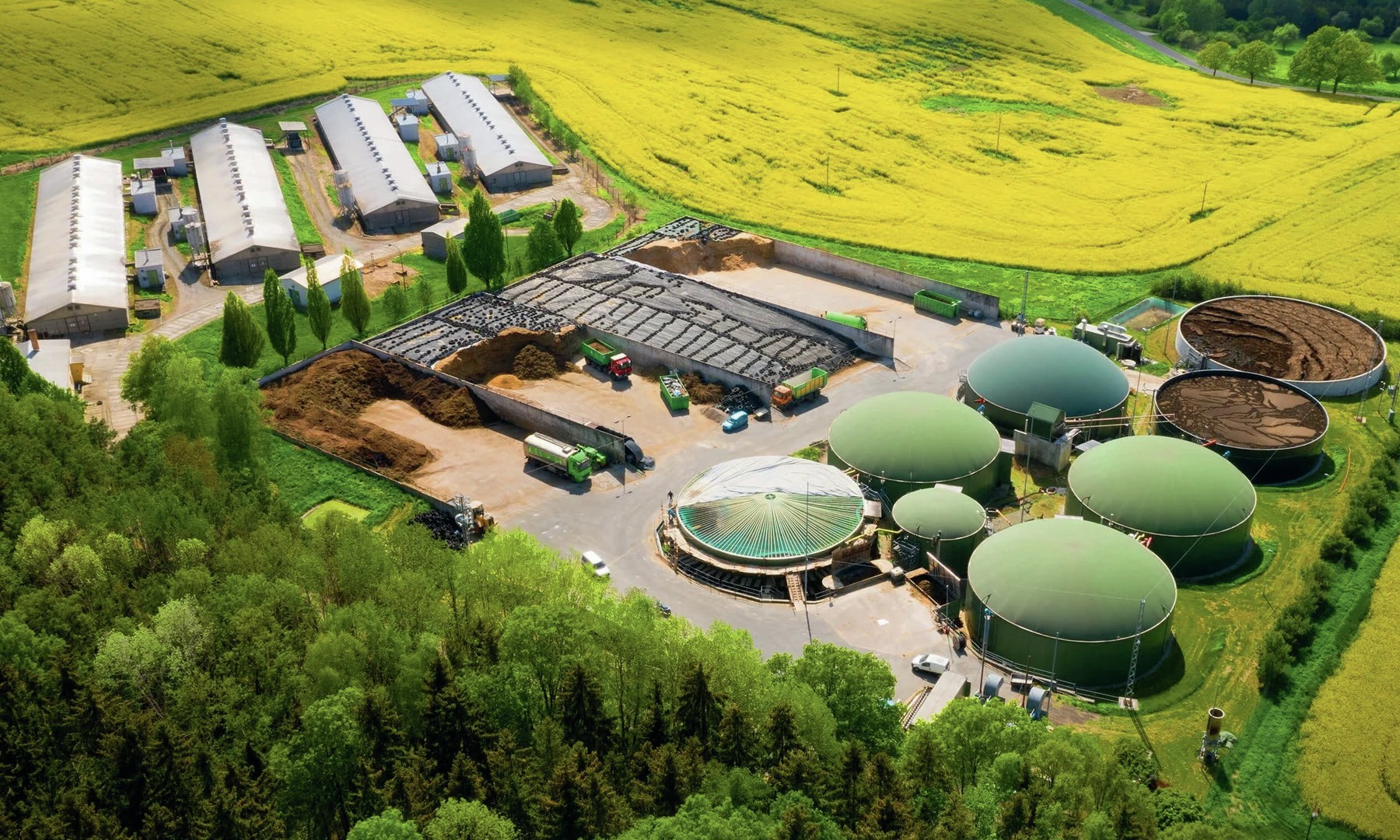
As the chemical industry pivots towards lower carbon production, most of the focus has been on hydrogen from electrolysis or using carbon capture and storage to sequester carbon dioxide (‘green’ and ‘blue’ technologies respectively). However, using biomass as a feedstock has also long been another strand of low carbon production. Generally speaking, biomass to chemicals routes focus upon either biological conversion, typically via fermentation, or chemical routes, with gasification the main strand.
Gasification
Gasification is the most versatile technology, as it is able to handle the widest variety of types of biomass, as well as related feeds like municipal solid waste (MSW). While gasification still generates CO2 during conversion, it is at least in theory from a renewable source which would generate CO2 and even methane (more damaging in terms of carbon equivalent) during the process of natural decay anyway, and which is presumably also drawing CO2 from the air as replacement biomass is planted and grown.
Biomass feedstocks are generally classified into four main groups: woody biomass, herbaceous biomass, marine biomass and manures. Woody biomass and herbaceous plants with low moisture contents are the primary choices because they do not require as much energy in drying to remove the moisture; every kilogram of water requires an additional 2.2 MJ of energy to process. Agricultural wastes such as bagasse, sugar cane trash, rice husk, rice straw, coir pith, groundnut shells etc are also potential feedstocks, although pulverisation is needed prior to use as feedstock to enhance their bulk density and reduce transportation cost.
One of the issues for large scale use of biomass gasification is the collection step; generating enough biomass to run a reactor at constant rates. Attention has therefore often focused on the paper processing industry, where large scale collection of trees already occurs. Sweden, Canada and the US, as major pulp and paper producers, have all experimented with gasification of so-called ‘black liquor’, a liquid mixture of pulping residues like lignin and hemicellulose together with inorganic chemicals from the Kraft process such as sodium hydroxide and sodium sulphide, for example. Black liquor is a toxic waste stream which paper producers must treat and dispose of, and so gasification to produce useable products or energy seems a good fit. However, while this remains a promising angle, take-up so far has been limited and only four black liquor gasification plants are currently in operation.
Tar formation
One of the major issues with biomass and waste gasification is tar formation. The presence of benzene and other heavier molecular weight compounds in syngas tends to cause problems, leading to incomplete combustion. High molecular weight tars act as promoters of high viscosity, and can cause blockages in fuel pipes and injector lines by condensation. Avoiding tar formation is a key consideration in biomass gasification, and usually requires a fluidised bed gasifier. Feedstock enters the bed and finely ground bed material is fluidised by air or oxidising agent at a temperature of around 700–900°C. Biomass is thermally broken down into gaseous compounds, and char is produced. The hot char and fluidising bed material cause further reactions to break long-chain hydrocarbons or tars into syngas components. Thus, a syngas product with very low tar content is produced with tar content less than 3 g/Nm3.
An alternative method is plasma gasification, where the extremely high temperatures help to reduce tars and convert all the organic material into syngas. Tar content as is reported to be up to 0.1% of that of an autothermal gasification processes. Arc discharges obtain thermal plasmas from DC or AC current or through radio frequency or microwaves. The oxygen demand in this process is small as compared to conventional gasification as most of the thermal energy is coming from an external energy source rather than exothermic reactions between the fuel and oxygen. However, in spite of considerable lab-scale work on this process, a recent survey of plasma gasification found only four commercial installations operational, all smaller scale and dealing with municipal waste. High costs and occasionally a negative thermal balance remain issues for the technology.
Fermentation
Fermentation is obviously used at a large scale for production of alcohols from some crop types, generally high sugar feeds like sugar beet or sugar cane. However, it is also attracting interest as a potential follow-up step to biomass gasification. So-called gasification-fermentation produces syngas as detailed above, which is then fed to anaerobic microorganisms that convert CO, CO2 and H2 to alcohols by fermentation. This process offers advantages such as flexibility of feedstock and syngas composition and lower operating temperatures and pressures compared to other catalytic syngas conversion processes. Bio-catalysts are also cheaper than the catalysts used in thermochemical processes. In comparison to hydrolysis-fermentation, gasification-fermentation can also utilise all of the organic components of biomass, including lignin, leading to higher yields. Overall carbon conversion is around 52%, compared with 41% for conventional gasification. Syngas fermentation microorganisms also do not require strict CO:H2:CO2 ratios, hence gas reforming is not required.
However, several issues must be addressed for successful deployment of the technology, including conversion efficiency of the gasification and syngas fermentation processes, the effect of some impurities on the bacteria, and the effect of CO:H2:CO2 ratios on syngas composition.
Biomethane
Since current ammonia/methanol processes are geared to use methane as a feedstock, the other major strand of biomass conversion is by using methane generated from biological sources. In this process. biological feeds are broken down by anaerobic bacteria to produce biomethane which can either be fed into a conventional gas grid or used for chemical conversion. Potential nutrient-rich sources can be agricultural waste, food waste, wastewater, and sewage sludge. Biogas production does also generate CO2 in the feed, which can be scrubbed and sequestered to produce net negative carbon emissions.
Ammonia production from biomethane is in the process of being scaled up from lab demonstration units to pilot and demonstrator plants. In December 2024, Yara announced that it has produced ammonia from biomethane at a demonstrator unit in Brazil, using methane from sugar cane waste. Yara says that by integrating lower-carbon fertilizers into its agronomic expertise, it could for example achieve a reduction of up to 40% in the carbon footprint of harvested coffee beans. In October last year, BASF also launched ‘biomass balanced’ ammonia which uses biomethane and some green hydrogen to produce a low carbon ammonia for polyamide production, and OCI Global and Rohm also announced a similar demonstrator run of bio-derived ammonia for low carbon methyl methacrylate production.
Cost and scale
As with all green technologies, the key questions remain cost and scale of production. Biomass is a difficult feed to scale beyond small local production, and so does not lend itself to large scale ammonia production might rely instead upon smaller scale, modular reactors. However, in theory it has the potential to be cheaper than other low carbon technologies such as electrolysis. As Europe moves towards higher carbon prices (see elsewhere in this issue) and implements its Carbon Border Adjustment Mechanism from 2026, so the push towards more ammonia production from biomass may grow stronger.