Sulphur 386 Jan-Feb 2020
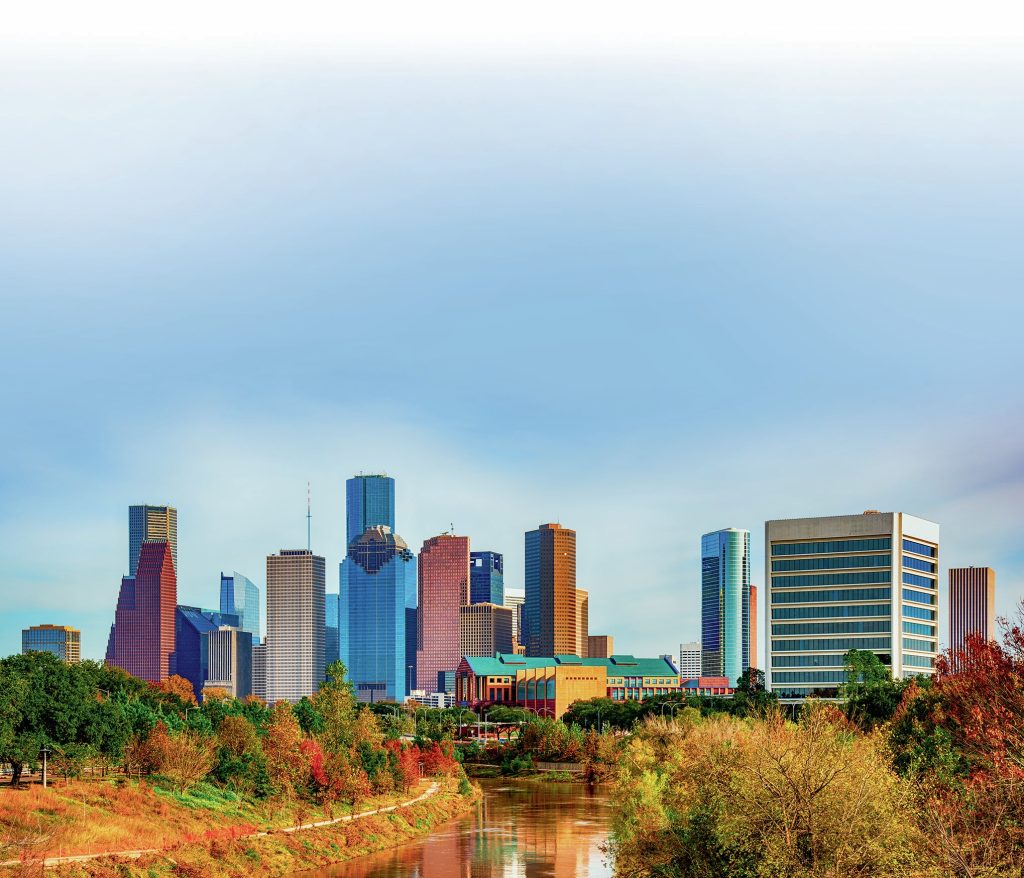
31 January 2020
Sulphur + Sulphuric Acid 2019
CONFERENCE REVIEW
Sulphur + Sulphuric Acid 2019
CRU’s Sulphur + Sulphuric Acid 2019 conference was held in Houston last November.
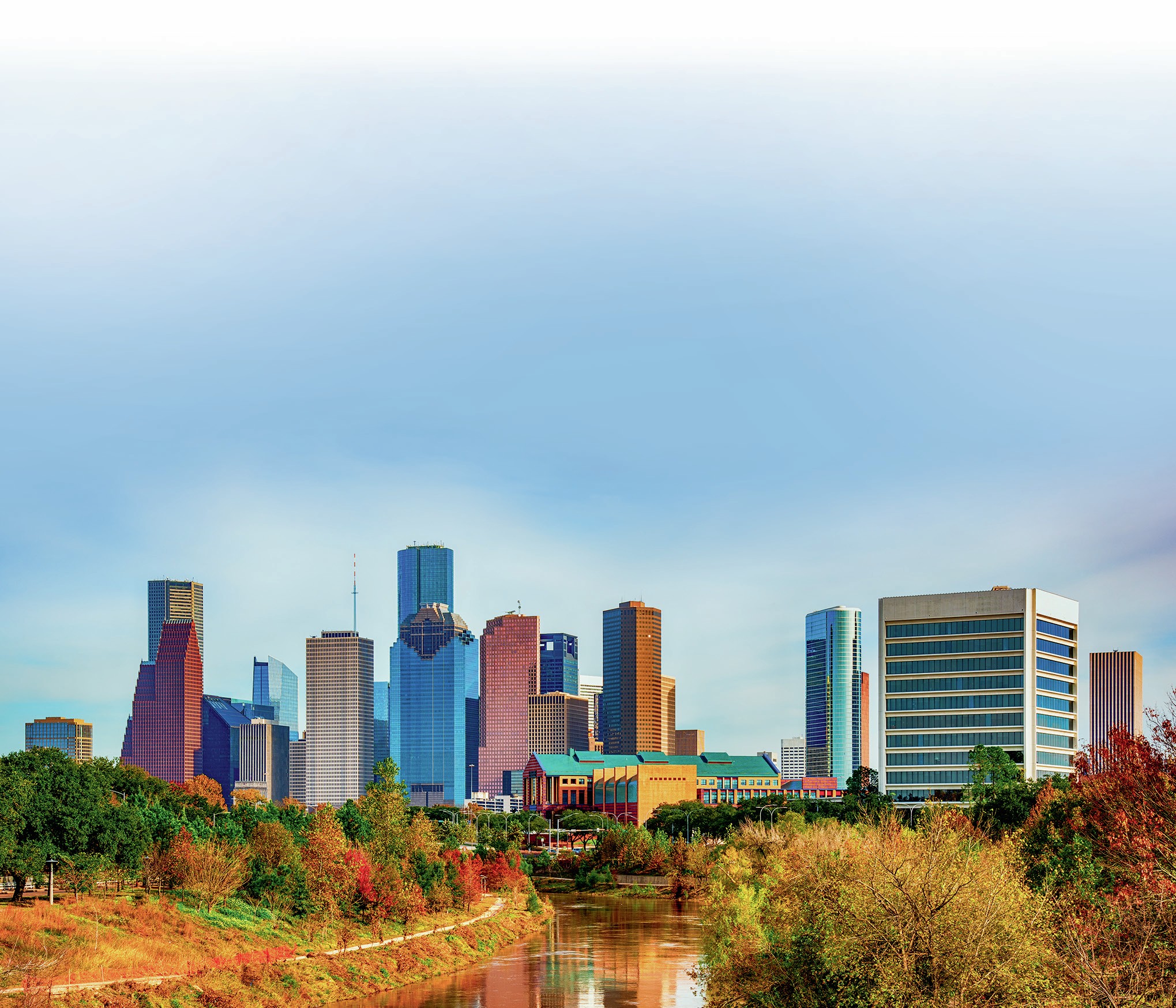
Lower sulphur prices marked a correspondingly slightly quieter than usual Sulphur + Sulphuric Acid conference at the start of November 2019. One of the major announcements at the head of the conference was CRU’s acquisition of Coking.com, a US-based company providing consulting, technical support, field services, training, and industry conferences to oil refineries around the world. The acquisition includes the Refcomm Refining Community conferences in Galveston and worldwide, and may change the makeup of the Sulphur conference going forward.
Global economy
To set the scene for the conference, CRU’s economist Ross Cunningham gave a macroeconomic outlook. Global GDP growth was 3,2% in 2018, he said, but this is forecast to drop to 2.5% in both 2019 and 2020. The fall is mainly due to falling GDP in advanced economies; from 2.3% to 1.6% and then 1.3% in 2020. Emerging markets, conversely, have stayed relatively buoyant, averaging 4.7% growth in 2018, down to 3.8% in 2019 but back to a predicted 4.4% for 2020. The main growth in these economies is no longer in China, where growth continues to slow, but places such as South America and India.
At the time of the conference no oil shock to the world economy was predicted; CRU’s view on the global oil price was for Brent Crude to average $63/bbl in 2020. Supply is plentiful in non-OPEC countries, especially the US, and there are large new fields under development in Norway and Brazil. However, other risks to the world economy of course include continuing tensions in the Middle East, as well as the effects of easing of monetary policy, and potentially any impact from OPEC oil production cuts. The US-China trade dispute also continues to generate uncertainty.
On a regional basis, US growth is slowing as the boost to the economy from fiscal policy fades, with manufacturing output down. At present unemployment is low and consumer confidence still holding up, but the current expansion of the US economy is the longest in history, and the probability of recession is at its highest since the global financial crisis. In the Eurozone, the soft growth patch persists. Manufacturing is down and trade negative. France and Spain are doing well, but Germany and Italy, the Eurozone’s largest manufacturing and exporting economies, growth is low. China is continuing to manage its economic slowdown and turn to environmental improvements and poverty reduction, but the trade war with the US has been a surprise, and China continues to be more exposed to its effects than the US. Much rests on the current ‘Phase 1’ deal.
TECHNOLOGY PAPERS
The technology section of the conference occupied a day and a half of parallel sessions on the Wednesday and Thursday, accompanied by two workshops, one a sulphur operations and troubleshooting ‘clinic’ moderated by Elmo Nasato, the other a workshop on heat recovery from sulphuric acid plants, including Rick Davis, Garrett Palmquist of MECS, Hannes Storch of Outotec, Michael Fenton of Chemetics, and Nelson Clark of Clark Solutions.
Digitisation
A number of papers looked at the application of new digital technologies to the sulphur and sulphuric acid industries. Michael Ku of Applied Analytics Inc described the application of artificial intelligence to sulphur recovery control, via a system of sensors measuring H2 S and SO2 levels at various points in the process, which are coupled with an adaptive AI model to fine control Claus plant efficiency.
Collin Bartlett of Outotec showcased Outotec’s digital tool solutions for its sulphuric acid plants, including development of its PORS system to include a gas cleaning and acid plant optimiser module.
In China, Wylton has developed its own ‘intelligent sulphuric acid’ system, based around a distributed control system (DCS) and ‘big data’ analysis system, and Kan Ming Han of Wylton described the system’s genesis and operation.
Finally, Patryk Szafaran and Marten Granroth of Haldor Topsoe presented Topsoe’s own suite of sulphuric acid plant monitoring and control software, including DynSOx and the connected services solution ClearView.
Sulphur recovery
On the sulphur recovery side, John Bourdon of Streamline Innovations Inc presented his new redox process for hydrogen sulphide removal; Valkyrie. The process uses a patented chelating agent, Talon, used in waste water treatment, as a regenerable scavenger to remove H2 S in an automated, modular process. The process has been operated at two demonstrator units in Texas since 2017 removing H 2 S at levels of up to 1.6% in a 25 million scf/d plant, with OPEX savings compared to a triazine unit of between 50-90%.
Frends Jensen of Haldor Topsoe showcased an alternative to tail gas treatment to push a 99.3% efficient sulphur recovery technology to the 99.9% typically required today. So-called TopClaus integrates Topsoe’s wet gas sulphuric acid (WSA) process and can recycle acid to the Claus reaction furnace to achieve 100% elemental sulphur recovery. The oxygen in the acid helps enrich the Claus feed in much the same way as conventional oxygen enrichment.
Oxygen enrichment continues to be a way of increasing the efficiency and throughput of a Claus plant, and Diego Scilla of Siirtec Nigi described his company’s SplitOxy process, which injects oxygen stepwise, allowing for intermediate removal of reaction heat, and postponing part of the combustion to a secondary chamber at the rear of the waste heat boiler, where the gas temperature is still high enough for further H 2 S conversion. It has recently been used in a revamp of an SRU in South America, boosting sulphur production from 52 t/d to 90 t/d.
On a similar subject, Fluor’s COPE oxygen enriched Claus process can be combined with ExxonMobil’s FLEXORB SE tail gas treatment, as described by Richard Bazata of Fluor and Jenny Seagraves of ExxonMobil respectively. They also described the option of using Fluor’s OEC RP 2 oxygen enhanced Claus carbon dioxide recovery process as an add-on, generating CO 2 for enhanced oil recovery use.
With the growing importance of shale gas in the US, Juan Marrugo-Hernandez of ASRL looked at producers’ experience with what appears to be an increasing concentration of H 2 S within a fracked gas reservoir over time. It is suspected that interactions between biocides and corrosion inhibitors in the fracking fluid with sulphur compounds in higher temperature reservoirs (>100°C) may be leading to degradation of the sulphur compounds into H 2 S.
Some producers, however, are facing the opposite problem – falling H 2 S levels as sour gas wells become exhausted, leading to turn-down issues in operating a Claus plant. Dharmeshkumar Patel of Sulfur Recovery Engineering addressed the design challenges, and simple changes that can be made such as converter bed deflector plates or deflector plate realignments, which can help ameliorate them.
Edina Avdic of Enersul looked at re-melting of contaminated sulphur. Enersul has recently designed a ModEx Dirty Sulphur Remelter to assist with clean-up of contaminated sulphur and sulphur block base pads, avoiding landfill solutions which are increasingly attracting environmental penalties from authorities in Canada and elsewhere.
“The oxygen in the acid helps enrich the Claus feed in much the same way as conventional oxygen enrichment.”
Case studies
A number of case studies also provided practical advice for SRU operators. Ashraf Abufaris and John Nichols of BASF related their experiences with design of the Central Gas Plant III in Bahrain, where the high ambient temperature (and consequent high lean amine temperature) was used as a CO 2 absorption accelerator, avoiding using a costly amine chiller.
Marco Van Son of Comprimo described the integration of biofuels with a refinery sulphur complex – this forms the basis of the article on pages 52-57 of this issue. Ben Spooner of Sulphur Experts meanwhile presented ‘war stories from the foaming front’ – six different studies on amine foaming problems, their diagnosis and root causes, and how they were tackled, and Domenica Misale-Lyttle of Industrial Ceramics, in conjunction with ASRL, investigated waste heat boiler tube sheet corrosion mechanics, in particular the circumstances under which lower temperature wet sulphuric acid and wet sulphur corrosion can occur, symptoms of which can be masked by failure of ceramic ferrules and tube sheet metallurgy.
Sulphuric acid technology
Chemetics has been working on two huge 5,000 t/d acid plants for OCP at Jorf Lasfar in Morocco, scheduled to come on-stream in 2021-22. As part of the design they have included what they claim are the largest heat recovery systems in the world, using their Chemetics CES-Alpha system to generate medium pressure superheated steam at 10 barg and 205°C.
Collin Bartlett and Marcus Runkel of Outotec described work on a different kind of acid plant, this time for a pyrite roasting-based plant for Eti Bakir in Turkey. The 2,080 t/d plant and its associated roaster and gas cleaning plant are part of an integrated fertilizer complex, and also includes an auxiliary HEROS heat recovery system downstream of the acid plant to generate additional low pressure steam.
Other sessions covered emissions management, including NOx abatement, mist eliminator systems, and gas measurement. Marco Kennema of BASF also presented new data on the company’s second generation of O4-115 Quattro sulphuric acid catalysts, launched the previous year, and used in the final bed of a plant to make up for deactivation over time on-stream in the first three beds, leading to more stable operation and lower SO 2 emissions. An installation at DOMO Caproleuna showed that overall conversion levels continued to be over 99% even with first bed activity down to 47% over two years of measurements.
Corrosion
Corrosion protection is a perennial concern for sulphuric acid plant operators. Roland Gunther of Steuler KCH reviewed the different capabilities of a variety of materials for such purposes, including organic polymers and resin coatings, various types of rubber membrane fillers, thermoplastic sheets and ceramic tiles or bricks. Following on from this, Johannes Derfler of AGRU Kunstofftechnik described the use of partially or fully fluorinated fluoropolymer materials, which can have longer lifetimes and lower operating costs, depending upon the application.
Sulphur markets
Next Peter Harrison of CRU reflected upon sulphur’s price collapse in the second half of 2019. There has been much weaker demand, especially for American phosphates, becoming more evident as the year went on, leading to oversupply in spite of the supply situation not being huge. India and Morocco saw import growth, but there was less buying in China and Brazil. On the supply side, the Kashagan project in Kazakhstan was still ramping up to full capacity of 1.4 million t/a, although US production was down as refiners switched to lower sulphur crudes and Saudi exports were diverted into domestic demand growth.
China’s import decline has been due to closures in the phosphate industry, as DAP prices have been below the average Chinese production cost, leading to fewer opportunities for export. Chinese port stocks between May and July 2019 from 1.1 to 2.2 million tonnes of sulphur – a multi-year high.
On the other hand, there could be better demand from the metals sector, said Peter, with a restart for the Ravensthorpe HPAL nickel site and new HPAL plants in Indonesia, as well as Glencore’s new sulphur burning acid plant in the Democratic Republic of Congo, all of these together accounting for 1.7 million t/a of additional sulphur demand from 2019-22. Phosphate demand growth was also positive, although the increases were mainly from 2021 onwards, in Morocco, Saudi Arabia and the CIS.
“China’s import decline has been due to closures in the phosphate industry…”
Supply was still being impacted by delayed projects in the Middle East, but these would boost production growth after 2019, in places like Kuwait. Crucially, many of these supply additions would be in coastal locations. Overall, CRU saw the market balance peaking in 2020, with supply running ahead of demand out to 2024, leading to stock builds in Canada, Turkmenistan and Uzbekistan, but potentially no real change to the price environment. The current low prices would, he said, rebound slowly out to 2024, as demand recovers.
Dr Salah al-Awadhi of the Kuwait Petroleum Corporation (KPC) followed with a look at Kuwait’s current projects in the sulphur arena. He reiterated that the Middle East will be responsible for more than 40% of sulphur supply growth from 2021 due to new and upgraded refineries, sour gas production and the processing of sour crude, taking production from 17 million t/a in 2019 to 22.5 million t/a in 2024. Kuwait’s share of this will rise from 750,000 t/a to 2.5 million t/a, mainly due to the Clean Fuel Project, which is expanding two existing refineries, and the new Al Zour refinery, due for completion in mid-2021, with 600,000 t/a of sulphur production. Kuwait is moving to a monthly sulphur price like Adnoc and Muntajat, as quarterly pricing can lag market developments in the current more volatile sulphur market.
Sulphuric acid markets
CRU’s Nick Waters looked at the market for sulphuric acid. Chinese smelter exports are rising, and imports declining. Chinese acid exports were forecast to reach 2 million tonnes for the full year of 2019, and the country has been a net acid exporter since 2018. Most of these exports have been from Two Lions coastal sulphur burning plant, and the smelters are focused inland, but more smelter exports are forecast for 2020. Pyrite capacity is declining, balancing some of the new smelter capacity.
Elsewhere, exports from sulphur burning acid plants are expected to fall in 2020 as smelter supply recovers, although India is still having to import to cover the loss of the Sterlite smelter. Chilean imports have been rising, from 2.2 million t/a in 2017 to 3.4 million t/a in 2019, although this is expected to fall to 2.6 million t/a in 2020 as work is completed on smelter upgrades and the smelters return to production.
The major demand area for sulphuric acid continues to be phosphate fertilizer, and Mike Rahm, formerly of Mosaic, covered the market for phosphates. He described the market as ‘sick’, with the structural changes in the Chinese internal market one of the major culprits, coupled with flooding in the US that reduced phosphate applications and weak currencies for major exporters. Global demand fell by 0.8% in 2019, and by 2.6% in 2018, but shipments were up that year, leading to a large overhang of stocks into 2019 and lower shipments. Chinese demand has fallen faster than supply, leading to more availability for export, but more Chinese production is shutting down in the longer term.
Looking to the longer term, Mike saw agricultural fundamentals slowly improving as lower phosphate prices lead to a demand response. There is also positive growth in some regions, such as South America (especially Brazil), Africa, Asia outside China and India, and the CIS.
Industry trends
Tuesday’s commercial sessions concluded with two panel discussions. The first covered the International Maritime Organisation rules on sulphur content of bunker fuels, moderated by Peter Harrison of CRU, and included Adrian Tolson of Marine 2020, Ross Cunningham of CRU and Nils Dahlberg of Bery Maritime. CRU now estimate that IMO-driven refinery investments will contribute an extra 1.3 million t/a of sulphur supply during 2019-20. About 10% of the world shipping fleet in tonnage terms have installed exhaust scrubbers, rising to 15% by 2023, but in the meantime hish sulphur fuel oil (HSFO) demand is forecast of all from 3.2 million bbl/d to 1.1 million bbl/d, while marine gas-oil (MGO) demand will rise from 1.25 million bbl/d to 3.3 million bbl/d, and may attract a $200-240/t premium over HSFO. Alternative fuels such as LNG are cheaper than conventional fuels and more carbon efficient but supply remains limited to large ports and port infrastructure is expensive. Overall freight rates may rise by 15-20%.
The second panel discussion, chaired by Sulphur editor Richard Hands, looked at emissions in the sulphur industry, with Angie Slavens of UniverSUL consulting covering sulphur plant emissions and Eli Ben-Shoshan of DuPont Clean Technologies sulphuric acid plant emissions.