Sulphur 392 Jan-Feb 2021
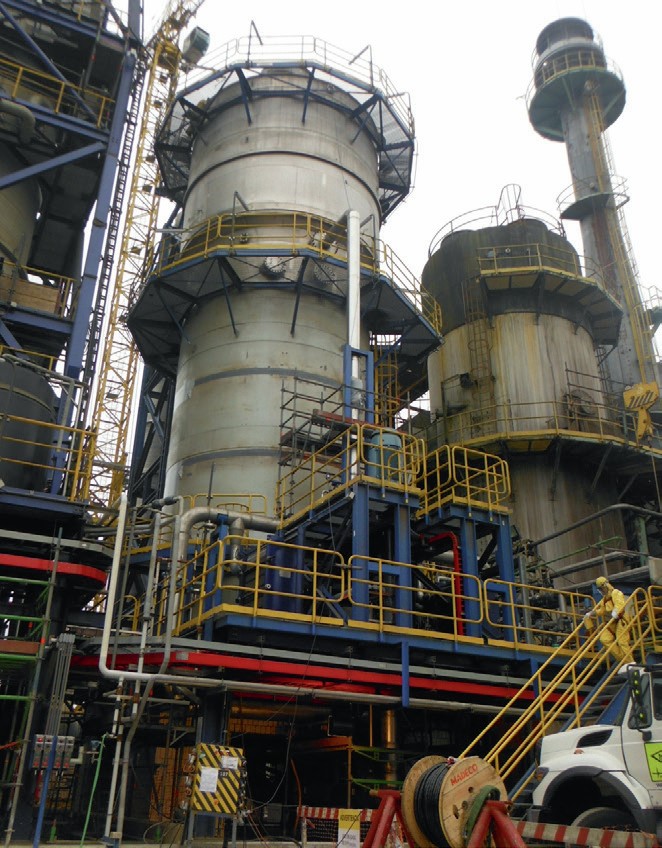
31 January 2021
Sulphur + Sulphuric Acid 2020
CONFERENCE REPORT
Sulphur + Sulphuric Acid 2020
The coronavirus outbreak necessitated a ‘virtual’ CRU Sulphur + Sulphuric Acid conference last year, held in November 2020.
Disappointing as it was not to be able to visit the attractive Dutch city of The Hague, CRU’s virtual conference application offered a palatable alternative, and certainly made the travel costs lower. The app was a slicker one than I have seen for some other virtual conferences, and offered some networking opportunities via virtual exhibition stands and chat windows, while the conference sessions were presented live, with opportunities for questions and answers. It’s not a full substitute for the real thing, but it is unfortunately something that we are all going to have to live with for a few more months at the very least.
Markets
Peter Harrison presented the usual sulphur market overview. Supply had been abundant going into 2020, he said, with IMO regulations helping boost refinery output, but as the pandemic hit, Q2 saw major refinery cutbacks, leading to 20-40% cuts in production rates. Although these had recovered, refinery sulphur output was still down 10-20%. This led to increasing tightness in supply and demand in Q3 moving into Q4 2020, with prices climbing. The question was where the ceiling might be. Peter suggested that Chinese stocks (currently around 3 million tonnes) are becoming active as prices reach $90-95/t, and this might help stabilise prices.
On the phosphate side, 2020 had seen a small fall in demand, but demand growth was likely to return in 2021, to the tune of another 1.5 million t/a of sulphur. Likewise industrial demand was down last year, but should return to growth in 2021. However, while 2021 will see an increase in sulphur supply on 2020, overall supply is likely to still be down on 2019. China is commissioning new capacity in both oil and gas processing, while the US has seen 400-600,000 t/a lost from refinery cutbacks. There is likely to be a global production rebound from new projects in 2021, especially in the Middle East, but demand growth will average above supply growth, narrowing market oversupply, and possibly leading to some tightness to remain in molten sulphur markets. Out to 2024-5, however, the new project pipeline becomes much smaller, while increased metals demand, especially for nickel leaching, will start to kick in from 2023. Looking to the longer term, lithium mining will also provide more demand.
Brendan Daly followed with an overview of the sulphuric acid market. Prices were weak in 2019 and this continued in 2020, leading to some very low points in April, even going negative in some markets. Prices have recovered somewhat since then but remain subdued. Imported volumes into markets such as India and Chile were 300,000 tonnes down on the previous year in Q2, but up in Q1 and Q3. Export acid volumes had increased, but at a slower rate, and declined in Q3 as Chinese internal market demand rebounded, leading to less Chinese export availability. Chilean demand remains weak, with imports down to 2.7 million t/a for 2020, compared to 3.5 million t/a in 2019. Chilean copper-based acid demand is likely to recover in 2021, Brendan said, but over the period 2021-25, closures will roughly match expansions, and imports will fall to 1.8 million t/a by 2024. Peruvian availability meanwhile will decline due to an increase in domestic consumption, with Peru’s exports falling to 1.0 million t/a.
Elsewhere, India’s Tuticorin smelter is unlikely to return to production. Moroccan demand is growing rapidly, but acid imports are projected to fall as more sulphur burning acid capacity is built. Morocco absorbed much of this year’s surplus because acid was so cheap, but may not do so in future.
US offhsore imports have climbed as local availability drops due to outages. Demand prospects are stronger from 2021, though smelter supply is also strengthening, and imports should thus remain relatively flat.
Finally, Chris Lawson offered a perspective on the phosphate market. There has been strong Chinese demand for soybeans and corn, but domestic phosphate production was disrupted by the Covid-19 outbreak – Hubei Province is a centre of the Chinese phosphate industry. In general, agricultural markets have been relatively resilient to the coronavirus outbreak compared to many others, and so demand has held up, with particular strength in Brazil and the US, and some increase in Russia and Australia, though it has fallen in China and Africa.
Sulphur technology
In the sulphur sessions, Attila Racz of Jacobs Comprimo looked at how oxygen enrichment of a sulphur recovery unit can feed into design optimisation considerations, via a case study of an existing unit that was revamped to a much higher capacity. Amine regeneration and the sour water stripper units were also debottlenecked as part of the revamp.
Jenna Dalhman of Nesta and Bernhard Schreiner of Linde also talked oxygen enrichment, but this time extending low level (28%) enrichment to low load operation at Neste’s Naantali refinery in Finland.
Exxon, BASF and Fluor, the latter in the form of Thomas Chow, also presented on oxygen enrichment, with a case study on COPE oxygen enrichment and a description of Fluor’s new OEC2RP or oxygen enhanced Claus carbon dioxide recovery process.
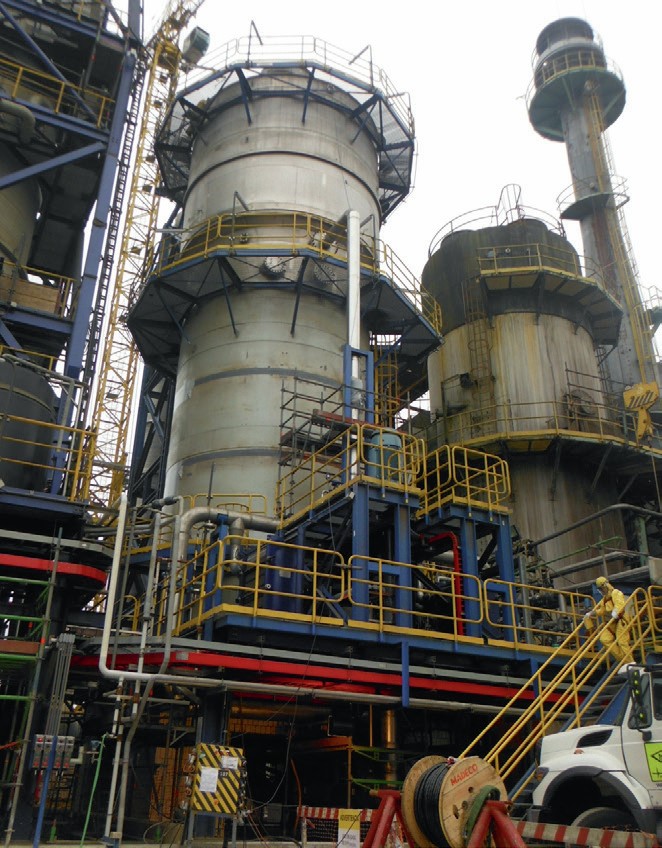
Siirtec Nigi have developed a technology called SplitOxy which, as the name suggests, splits the oxygen addition, feeding it both at the Claus burner as well as into the rear channel of the waste heat boiler, creating a second reaction chamber (as the gas is above auto-ignition temperature) which can be varied without affecting the main process burner. An installation in Colombia in 2020, complicated of course by Covid, has increased capacity by 80%.
Elsewhere in the Claus process, Sandeep Sutar of Saudi Aramco looked at enhancing SRU efficiency through predictive monitoring, part of the w ay data driven approaches are enhancing operating efficiency these days, including monitoring of feed quality, amine and acid gas distribution monitoring, to prevent hydrocarbon and ammonia carryover. Meanwhile, temperature measurement challenges in a Claus reactor was the subject for Deniz Keles of Thermometrics, showcasing a range of measurement probes to help ensure safe and efficient operation.
Moving downstream, Lorraine Huchler of Martec and consultant Elmo Nasato focused on the water side of sulphur recovery units, and avoiding water-related failures in the waste heat boiler and condensers, especially when revamps have focused on increasing capacity, pressure and temperature, via a more holistic design approach. Nathan Hatcher and Simon Weiland of Optimized Gas Treating also presented a case study of sulphidation corrosion in a Claus waste heat boiler.
Gerald Bohme of Sulphur Experts looked at pre-sulphiding of tail gas treatment unit catalyst, and how to handle it, with due caution as to self-heating when interacting with oxygen and managing temperature rise, potential H2 S breakthrough, and other considerations.
David Inward, of the memorably named Sick AG, presented a hot, wet extractive infra-red analyser for measuring emissions from the final stack of an SRU, to ensure that it remained within compliance of local air quality limits.
Finally, Inshan Mohammed of Sulfur Recovery Engineering reported on a troubleshooting assignment for accelerated corrosion within the regenerator column of an acid gas enrichment unit. Cracking was found in welds using ultrasonic measurement, but the conclusion was that this was not accelerated – previous visual and non-destructive testing inspections had simply failed to identify it.
Sulphuric acid technology
As usual, running in parallel with the sulphur technology sessions were two sessions on sulphuric acid technology. Plant design and construction was a fertile topic for some of the major licensors. Outotec presented on the importance of the gas cleaning section of a metallurgical sulphuric acid plant as ore feeds decline, leading to higher impurity levels which, if not tackled through enhanced scrubbing/ electrostatic precipitation techniques etc, will impact upon the longevity of the downstream acid plant. They also presented a second paper which looked at the coronavirus pandemic, and how it had necessitated a much greater reliance for operators on online support from licensors and constructors, and the digital tools which can be used to deal with this. On a related topic, Boris Pickering of Chemetics discussed capital spends, and how to minimise them when designing one of the current generation of ‘mega’ acid plants.
From the theoretical to the practical; Andres Mahecha-Bohero of NORAM Engineering compared and contrasted two case studies of designing acid tower replacement systems; an acid tower replacement for a sulphur burning plant in North America, which used an all metal alloy tower, and a replacement at a copper smelter in South America, where a brick-lined carbon steel tower was used. Michael Baerends of Fluor meanwhile explored the commissioning and start-up of a wet gas sulphuric acid (WSA) plant, and the teething troubles encountered, including stack analyser issues, and heavy misting in the condenser.
Revamping always offers issues, but in particular when it is a revival of a 30-year old plant. Ayman El Hafeiz of AZFC in Egypt was tasked with this, and described how via collaboration with DuPont-MECS the plant was brought back into service.
On the subject of catalysts, Marten Granroth of Haldor Topsoe and Tom Brouwers of DuPont MECS both presented their companies new grades of sulphuric acid catalyst – VK-38 for Topsoe and XLP-310 for MECS respectively. Much more information on both of these can be found in our article on pages 28-35.
The topic of mist eliminators brought two papers. Allesandro Gulla of AWS described GX – a new gas-liquid coalescing filter medium, and experiments carried out at laboratory and pilot plant scale to determine the best formulation for it in terms of separation efficiency and pressure drop. GX candles now offer 100% separation efficiency for droplets larger than three microns, and 99% efficiency for sub-3 micron particles. Ali Goudarzi of CECO, meanwhile discussed a candle filter retrofit to meet more stringent NOx emissions.
Corrosion, another perennial topic for acid plants, was covered by Michael Davis of the Nickel Institute, who looked at the use of nickel alloys in the highly corrosive environment of a sulphuric acid plant, while James Cook and Keith Robinson of AirBTU explored the issue of sub-dewpoint corrosion, and how temperature mapping and computational fluid dynamics can be used to identify areas of a heat exchanger that might be subject to such corrosion, and design to minimise them.
The final two papers covered spent acid recovery, where Martin Joksch of P&P presented his company’s acid concentration unit, and Victor Machida of Clark Solutions described a small (150 t/d) modular sulphuric acid plant designed for the Kalium project in Brazil which processes glauconite ore with sulphuric acid, combining sulphur burning and metallurgical acid sections of the process, to generate potassium and magnesium sulphate, and aluminium and iron oxides. The plant is a single absorption unit with tail gas scrubbing and a novel heat recovery section using an intermediary fluid.