Sulphur 409 Nov-Dec 2023
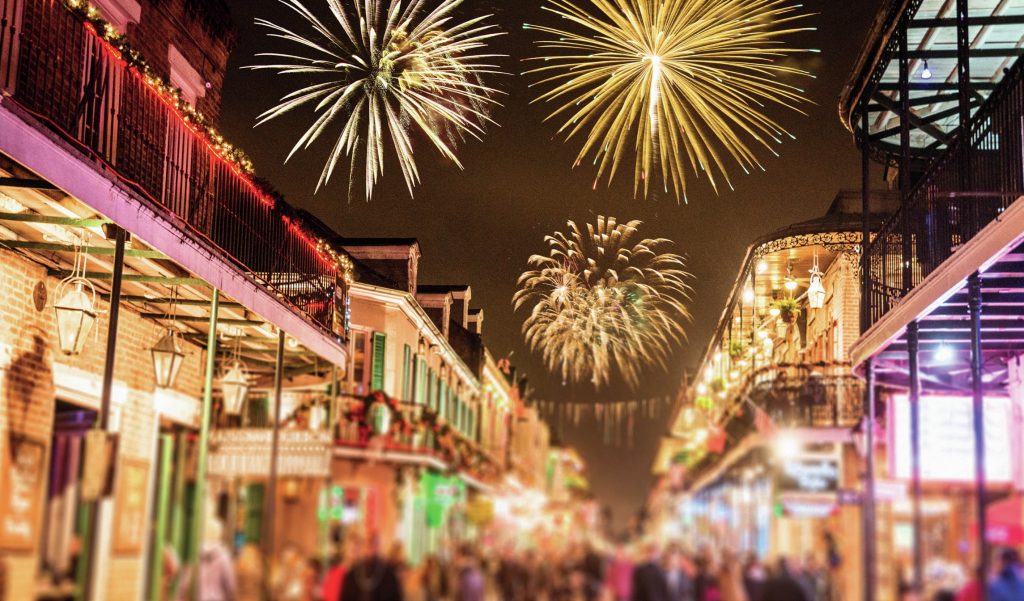
30 November 2023
Sulphur + Sulphuric Acid 2023
CONFERENCE REPORT
Sulphur + Sulphuric Acid 2023
A report on CRU’s annual Sulphur + Sulphuric Acid conference, held in New Orleans, USA, 6-8 November 2023.
CRU’s 39th Sulphur + Sulphuric Acid Conference and Exhibition convened in New Orleans, 6-8 November 2023, with more than 400 delegates in attendance. This year the programme was enhanced by having more panel discussions, promoting greater interaction between attendees and speakers. A key feature on the morning of the first day of the agenda was the troubleshooting clinics, one on sulphur recovery moderated by Elmo Nasato of Nasato Consulting and the other a troubleshooting clinic for sulphuric acid plant operators run by Steve Puricelli of EXP, Hannes Storch of Metso, Stuart Hinze of JR Simplot and Hanno Hintze of Aurubis. The rooms were packed with attendees keen to learn from the experts and share their experiences. In addition, following the success of the short 15-minute technical showcase presentations introduced at last year’s conference, the technical showcases returned this year with an expanded programme of presentations covering sulphur and sulphuric acid process technology and equipment.
Market papers
On Monday afternoon the conference proper began with a review of the major markets, beginning with a review of the US economy by Keith Belton of the American Chemistry Council. Inflation remains an issue for the world economy, he said, with an average of 5.9% this year slowing to 4.4% next, and interest rates slowing growth. Global GDP is expected to rise by 2.6% this year and slow further to 2.4% next. The strong dollar and high oil prices are also an issue for energy importing nations like Europe and China. The industrial sector is worst hit. Global manufacturing indexes have been in decline for the past two years. China also faces its debt-ridden property sector and weaker global demand for goods. Oil production growth is slowing, rising to just over 102 million bbl/d next year, with a considerable overhang of capacity.
In the US, there is considerable uncertainty over the economy, with a retrenchment in consumer spending and falling goods demand, and though inflation is also falling, it remains stubborn, and the risk of recession remains high. US chemicals demand has been relatively weak this year, with most sectors seeing a fall in domestic demand and considerable destocking. But US oil and gas output continues to be a bright spot, with increased demand in Europe due to the loss of Russian output. Refinery utilisation factors continue to be at around 90%, and gas-based chemicals like ammonia and methanol continue to be globally competitive. He also highlighted the potential burden of increased regulation on the industry, but conversely, the Inflation Reduction Act has helped galvanise new project activity.
Next came the ever-popular sulphur market presentation, delivered as usual by CRU’s Peter Harrison. The past 12 months, he said, had seen sulphur prices swing from overperforming to underperforming, from highs of over $400/t f.o.b. Middle East in mid-2022 to around $90/t at present. Looking to the next few years, he predicted that sulphur demand for phosphate production was likely to plateau in China and the US, but Morocco will see large incremental demand for its phosphate projects; up to 3 million t/a from 2022-2028, with additional demand also coming from Saudi Arabia. The market rebound and strongest additions are likely to be in 2023 and 2024. A recovery in the phosphate market will be followed by additional demand for lithium processing in the US at the same time that refinery closures or conversions reduce sulphur output, leading to more US import demand. Refining also continues to add Chinese sulphur production, leading to import demand narrowing by around 2 million t/a over the forecast period. Meanwhile Indonesia’s fast growing nickel industry could add another 4 million t/a of sulphur demand. Overall Peter therefore saw the sulphur market moving into deficit from next year, with additional production cuts in Europe and the US only partially offset by new supply in the Middle East, and strong demand growth in Morocco and Indonesia, driving average global prices higher in the longer term, although stocks in China and Saudi Arabia may cushion markets in the short term. The traded sulphur market could reach 44.8 million t/a by 2028, with the UAE increasingly dominant on the export front. Looking beyond the end of the decade, the coming phaseout of oil could still be matched by new sour gas sulphur at least to the 2040s, when a deficit could emerge.
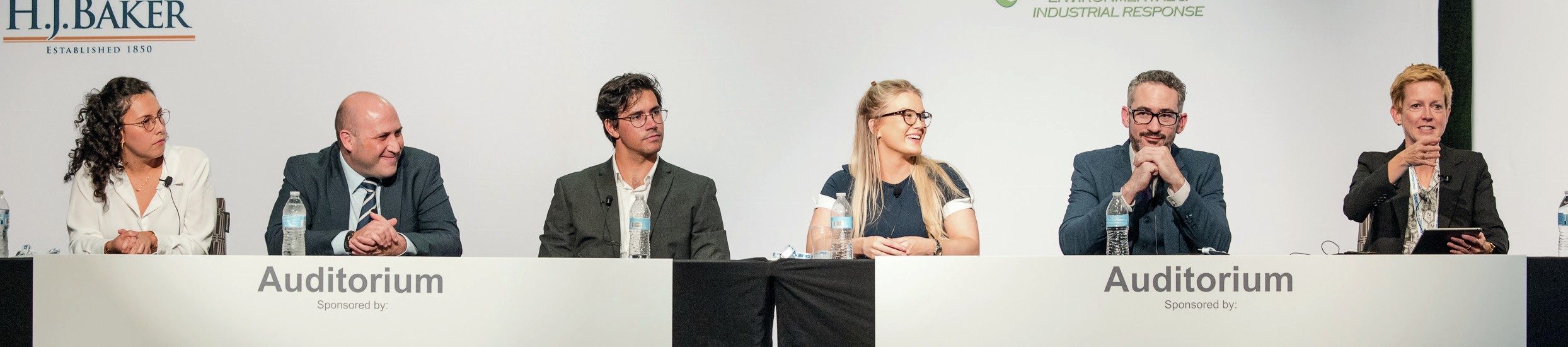
The sulphuric acid paper was presented by Viviana Alvorado of CRU. Acid demand growth has been boosted by Indonesia’s need for acid for minerals processing, allowing Chinese producers to decide when they wish to export. New Chinese smelter capacity is adding 3 million t/a more acid to the mix this year and next. Across the Pacific, Chile is seeing increased demand for acid for copper and importing around 3.7 million t/a this year. As previously mentioned, US lithium production will also see North American acid demand increase, though most of this will be met by local sulphur-burning acid plants. In general, increased supply integration, i.e. building domestic acid capacity, is likely to limit global acid trade requirements over the next few years. Seaborne acid trade is falling from 16 million t/a in 2022 to 14.4 million t/a in 2024. This is likely to mean less sulphur-burnt acid on the market, giving smelter acid a greater share and possibly bringing down prices as a result.
Brendan Daly of CRU presented the phosphate market paper. Phosphate prices have broadly declined from their 2022 peak due to weaker demand and easing supply disruption, but there has been an uptick in the second half of 2023 towards $600/t c.fr for MAP/DAP. Chinese phosphate exports were higher year on year for Q1-Q3 2023, but have slowed due to renewed export restrictions, with Morocco’s new capacity not yet making a difference to the market. In India, a significant (31%) cut to the DAP subsidy is expected to impact upon demand for the remainder of this year and into 2024. On the production site, US phosphate production continues to decline due to falling rock grades. Court cases on countervailing duties against phosphate imports from Russia and OCP have found in favour of the overseas companies, which may help lower US prices. New phosphate capacity is still mostly (ca 75%) coming from Morocco and Saudi Arabia, but net demand growth appears to be running ahead of capacity, leading to a deficit by 2027. Lithium iron phosphate demand for batteries is growing rapidly, and could reach 2 million t/a P2 O5 by 2030, though it remains concentrated in China for now. Overall, Brendan saw prices likely to correct lower in the short term before rebounding in the medium-longer term.
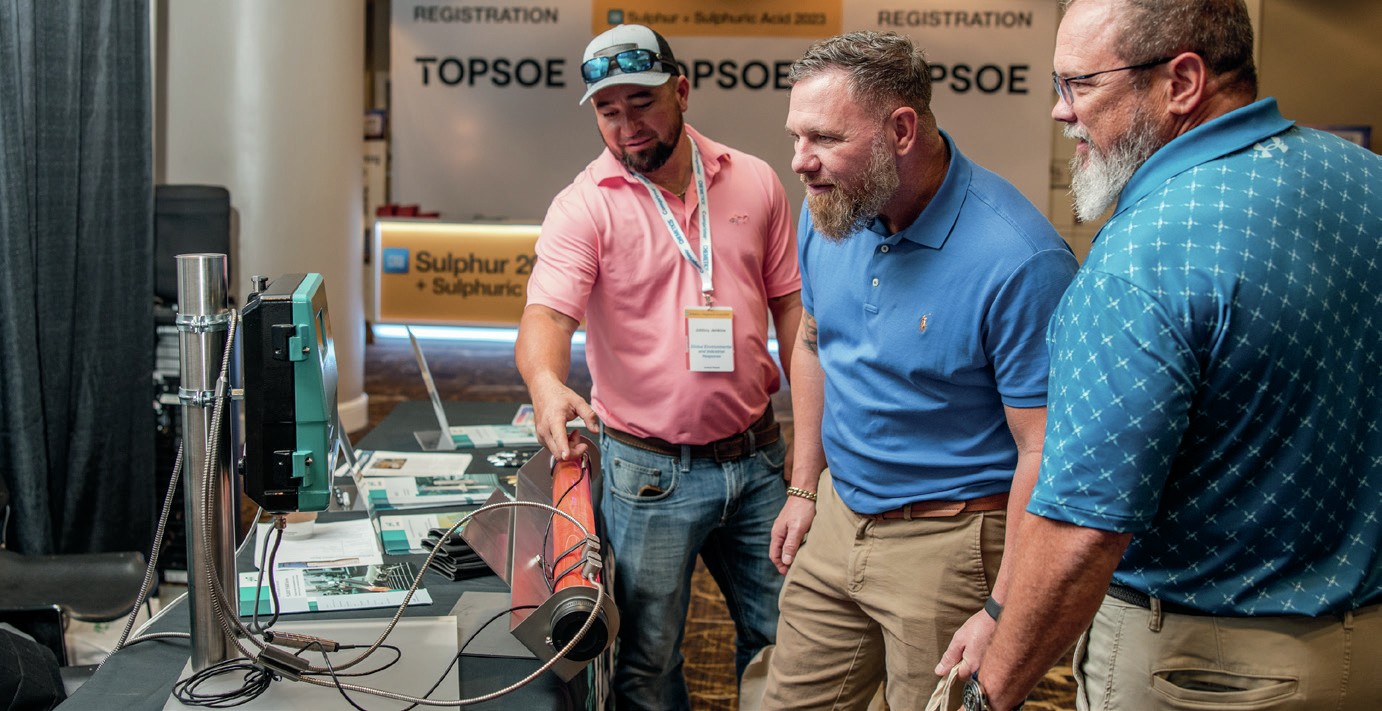
The last of the afternoon’s market presentations was given by Aaron Wade of CRU’s new Exawatt purchase and consultant Kaitlin Gebbie, and addressed challenges and opportunities for sulphur in the energy transition. The rapid expansion of battery use is an upside for sulphuric acid demand. Sulphuric acid is needed for nickel sulphate, and both lithium and phosphate for LFP. Total demand will depend on which technologies win out. For example, lithium can be recovered from brine processing, mineral processing or sedimentary processing. The latter are carbonates and so typically require much more acid, up to 45 tonnes per tonne of lithium carbonate recovered. Thacker Pass and Rhyolite Ridge may add 2.8 million t/a of acid demand in the US by 2028. However, environmental concerns may discourage leaching use and tailings disposal.
Sulphur technology
Tuesday’s sulphur technology strand began with a paper by Alex Geiss of AMECO on his company’s recently constructed 2,000 t/h sulphur reclaimer for Keyera at South Cheecham in Alberta, Canada, one of the largest sulphur handling operations in the world. The setting makes for cold weather operating challenges during winter when temperatures can fall to far below zero, and the portal reclaimer also had to handle prilled sulphur and minimise dust emissions.
Richard Barrington of AMETEK/Controls Southeast described a predictive method developed for estimating the liquid level in sulphur run-down lines. It is critical to maintain an open vapour path from the condenser to the sealing device, he said, and CSI has observed problems in the field which appear to be caused by undersized run-down lines. Testing of the method against measured values has led to a set of formulas that can be used for calculating the liquid levels.
Ulrich Nanz of IPCO described the company’s two main forming technologies; the Rotoform pastillation process and the drum granulator, and their suitability for different throughputs, cleaning requirements, as well as formed product strength and water content.
Two panel sessions rounded off the first sulphur session; on safe and effective sulphur forming and handling, and on emissions from sulphur tanks and sulphur pit degassing.
Operator case studies
ENAP in Chile contracted Worley Comprimo to conduct a technical audit of the sulphur recovery section of their Aconcagua refinery on the Pacific coast. Marco van Son of Worley Comprimo described the approach to this and the steps taken to improve reliability and lower SO2 emissions.
Petronas revamped their refinery SRUs in 2010, since when they have been dealing with hotspots in the thermal oxidiser combustion chamber, leading to refractory failures and frequent maintenance shutdowns. Although some interim measures had been taken, the problem had not been resolved. Mohammad Azahar Ahmad of Petronas explained the issues and presented the findings of a technical review in 2021 which has made recommendations for tackling the problems on a long term basis.
Scott Kafesjian of Wood Group also tackled the subject of rejuvenating an old SRU with reference to a US refinery with a 46 year old SRU. Rather than scrapping and replacing the unit, Wood was able to modernise the unit and improve safety, reliability, operability, and recovery efficiency of the redundant SRU, thereby providing the owner confidence that refinery throughput would not be compromised by a sulphur recovery unit outage.
SRU design
A short session on Tuesday afternoon looked at issues in SRU design. New designs and retrofits of existing waste heat boilers (WHBs) are increasingly being used to generate higher pressure steam to accommodate higher heat loads, leading to increased operating issues, especially in kettle-type designs, where feedwater injection and internal recirculation are key attributes of shell-side performance. Elmo Nasato presented the results of some simulations to better understand the effects of feed water distribution on vapour hold-up in a kettle-style WHB. Appropriate placement and distribution of feedwater into the shell-side of the WHB can significantly reduce vapour hold-up within tube bundle regions undergoing high heat flux.
Marcus Weber of Fluor covered lessons learned from an owner/licensor perspective in the design and construction of several 500-1000 t/d multi-train sulphur recovery unit/tail gas treating unit projects. Structuring project execution in the right way between the licensor, owner and EPC contractor can lead to lower project execution risk in terms of cost and time and lower capex and opex cost.
Again a panel session on sulphur plant design closed out this section.
SRU innovations
Alina Green of WIKA presented her company’s sapphire-protected thermocouples for temperature monitoring in SRUs. WIKA have now adapted this technology for low pressure Claus applications and included a secondary containment system that is pressure tested to 100 bar.
Axens has recently developed a new titania-based catalyst called CRS 41, which has much higher porosity than previous generations of the catalyst while preserving mechanical integrity. As described by Johann le Touze of Axens, this facilitates the conversion of COS and CS2 at low temperature, which is essential if hydrocarbons are present in the acid gas feed.
As environmental SO2 emission regulations become more stringent, Tail gas treating options become limited. To potentially achieve lower opex, using a biological desulphurisation process as an alternative is becoming of increased interest. At the same time, demands for increased SRU capacity and reliability favour the use of medium and high-level oxygen enrichment. Fluor recently evaluated revamp options for an existing refinery with 3 x 100 t/d SRUs. Fluor’s COPE® II Oxygen Enrichment technology was selected to increase each train capacity to 150 t/d, with Thiopaq O&G bio-desulphurisation technologies used to achieve an H2 S treated gas specification of <25 ppmv.
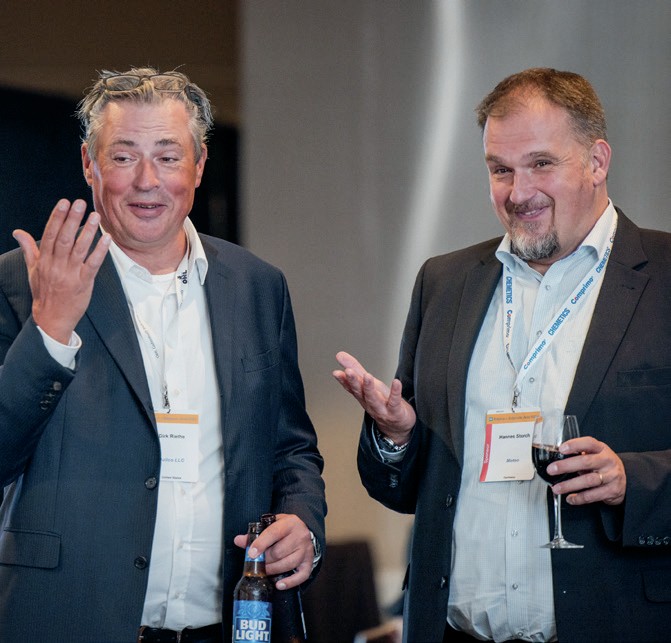
With the emerging greater application of bio feedstocks in refineries there is a growing need to operate SRUs at much lower capacities than originally designed and with almost continuously fluctuating acid gas compositions. These changes have a detrimental effect on the ability to control the SRU with fixed air-to-acid-gas ratios. Gerton Moelnar of Worley Comprimo described improvements to the Advanced Burner Control System – 2ACT – which incorporates and AMETEK analyser upstream of the SRU for continuous sampling and monitoring of the gas stream to dynamically change burner operation in fluctuating gas streams.
The changing sulphur industry
A final sulphur session on the last day looked at the future of the sulphur industry. David Savage from Matrix PDM Engineering considered ways in which supply and demand changes in the sulphur industry will create a need for expansion in sulphur infrastructure. Next a paper presented by Christian McDermott of Voovio Technologies and co-authored with Angie Slavens and Elmo Nasato highlighted the skills gap; a growing issue in many industries in the US and worldwide. Industrial manufacturers are losing experienced employees and the knowledge they have in their heads, built up over decades, is rarely written down or transferable. This leads to lack of standardisation in procedures and training, and can open up risks around incidents and production losses. The paper looked at how manufacturers can close these gaps using digital tools, in particular knowledge automation.
Sulphuric acid technology
The sulphuric acid session also began with papers looking at the ways that the industry may need to change in future. The energy transition is demanding more metals for batteries and electrical items, but simultaneously forcing a look at recycling and the ‘circular economy’. Marcus Runkel of Metso used recovery of metals from pyrite tailings using Metso’s fluid bed roasting process, and expanding its capacity from the previously typical 1,000 t/d of concentrate via the “Circoroast” process. This allows for larger throughput, due to the flexibility in the heat balance of the roaster and a more compact plant footprint.
Joan Fedderson and Samuel Johanssen of Topsoe presented the wet sulphuric acid (WSA) process as a way of treating lean SO2 concentrations in waste streams without the need for scrubbers. In the pulp and paper industry, WSA also increases the circular use of chemicals such as sodium and sulphuric acid, while in a refinery, the it can lead to a significant saving in CO2 equivalent compared to a Claus tail gas unit.
The years of covid forced the industry into new ways of operating. Collin Bartlett of Metso reflected on how the pandemic had changes structures of contracting and project execution, via remote working and digitalisation, and to what extent lessons learned during that time could or should become integrated into the way we work in future.
Catalysts and emissions
The pressure to reduce emissions of SOx and NOx is a constant one. Kassie Chanda of MECS reviewed emissions reduction options for acid plants. Scrubbing methods and mist eliminators can be employed for SO2 , SO3 and acid mist removal, including regenerative and wet scrubbers for SO2 removal. Nitrogen oxides can be converted to gases like nitrogen or soluble N2 O5 through processes like selective catalytic reduction (SCR/SNCR) and ozone oxidation.
Martin Alvarez of Topsoe reflected on his company’s caesium promoted catalyst VK-69 via a series of case studies which highlighted its increased acid production and reduced SO2 emissions, and for challenging applications a new combination with VK38+ which can achieve even higher conversion levels or deal with specific bottlenecks that can be solved with extra activity.
The last of the trio of catalyst/emissions papers was presented by Alison Belgard of BASF, who described how 3-D printing of catalysts has allowed catalyst manufacturers to experiment with previously unattainable geometries. BASF’s new X3D catalyst now has three industrial references and demonstrated that its higher active surface area results in better SO2 conversion, lower pressure drop and savings in energy costs and sodium hydroxide consumption.
Acid plant design
Tuesday afternoons sulphuric acid session began with two papers on sulphuric acid converters. Steve Puricelli of EXP looked at choosing a converter design, with considerations ranging from stacked, staid and catenary configurations, cost/benefits of upgraded materials, when an internal heat exchanger is a good choice, and how various configurations affect reliability and maintenance.
Robert Crane of NORAM followed with two success stories in redesigning old converters. The first project required the re-design of a 3-bed into a 4-bed converter comprising two catalyst passes with each pass split into two parallel beds to meet a very aggressive project schedule. The second involved an old plant with two converters. NORAM and the client evaluated various replacement strategies, ultimately resulting in the decision to only replace the old 4-bed converter.
Clark Solutions described DrySeal™ a safer alternative for seal cups, required in candle filter mist eliminators, which is both self-draining and autosealing, easy to clean and install and does not require additional set-up steps.
Douglas Azwell of MECS next presented a new impaction-based mist eliminator called Prime Impact™ , which offers equivalent or improved efficiency at higher throughput and the same pressure drop as traditional impaction beds, resulting in the ability to debottleneck existing towers or design new or replacement towers with smaller diameters, thus reducing investment cost.
Acid plant operations
OMV installed new PFA fluoropolymer liners in their WSA plant at their refinery in Schwechat to help with corrosion issues. The plant design was also revised to allow process monitoring in operation and separate plant components during a shut down. Johannes Derfler of AGRU described the reasoning behind the choice of materials and the impact on plant operations.
Blake Stapper of Messler related a revamp of a spent acid decomposition furnace to improve plant throughput. The solution entailed introducing oxygen in two steps, both as an enrichment to the combustion air and by direct injection into the furnace.
Roland Gunther of Steuler described a case study in the replacement of the upper part of a co-current flow quench tower resistant, pre-lined workshop fabricated equipment.
Jan Bond of Amafilter recounted a recent project where a sulphuric manufacturing plant wanted to extend the service life of their sulphuric acid production units from 16 to 24 months by reducing the solid content in their liquid sulphur. As the liquid sulphur was stored for an extended period in the storage tank, this poised a significant challenge for filtration. Amafilter® developed, designed and built a two-vessel skid-mounted ceramic cartridge filter system which polishes the liquid sulphur, reducing the solid content to less than 5 ppm. As a result, the catalyst lifetime and maintenance interval were increased to over 24 months.
Gas cooling and heat recovery
Two operators papers by Petrokemia Gresik, one by Domenica Misale of Industrial Ceramics and another by Nelson Clark of Clark Solutions closed out the final acid session. Gresik redesigned the economiser of their acid plant. The new design changed the configuration from a single-compartment to a dual-compartment, with different materials and tube types for each compartment, and improves heat transfer, reduces corrosion, and lowers the SO3 gas temperature at the intermediate absorption tower inlet. They also modified their waste heat boiler after experiencing multiple failures due to leaking tubes positioned behind the ferrule on the hot side. The failure was resolved after modifying the ferrule by tapering its edge, effectively reducing gas turbulence.
Nelson Clark also highlighted his company’s heat exchanger design, SAFEHX® , which uses two tube bundles containing process fluid and an intermediate inert liquid detained in the shell. The latter is not only a heat transfer facilitator but also a physical barrier keeping the reacting fluids from coming into ontact. The two tube bundle configurations lead to a thermal gradient in the tubesheet, one that must be accounted for to prevent excessive dilatation stresses and consequently structural damage.
Next year CRU will be celebrating its 40th Sulphur + Sulphuric Acid Conference in Barcelona, 4-6 November 2024.