Sulphur 414 Sep-Oct 2024
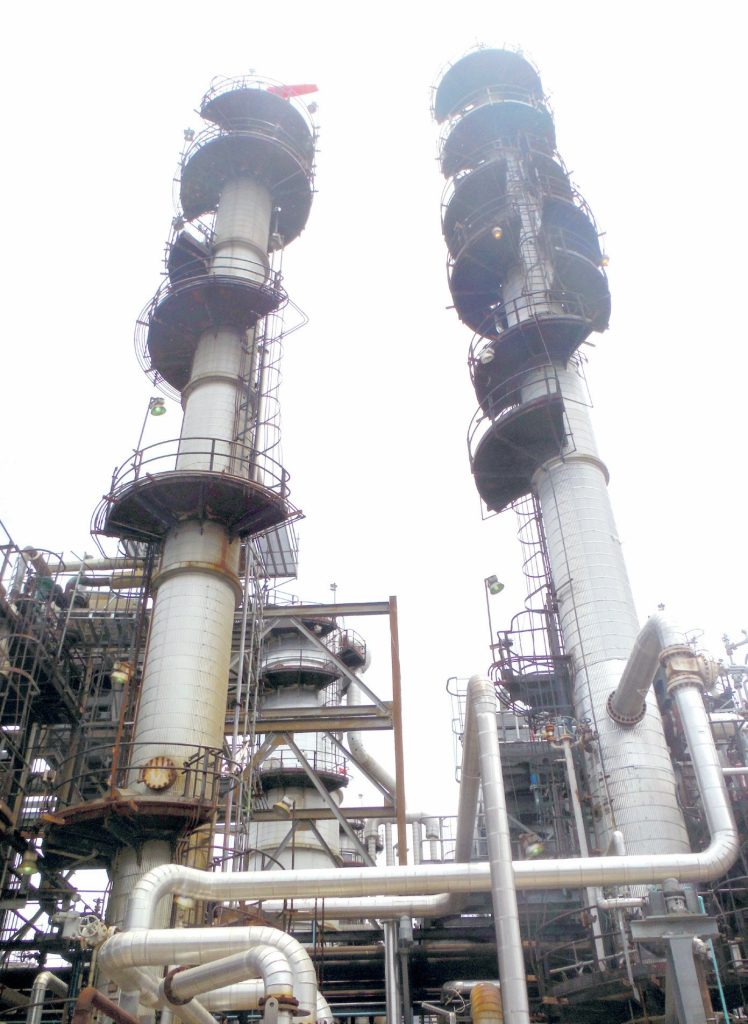
30 September 2024
A big plus for sour water strippers: low GWP ammonia recovery
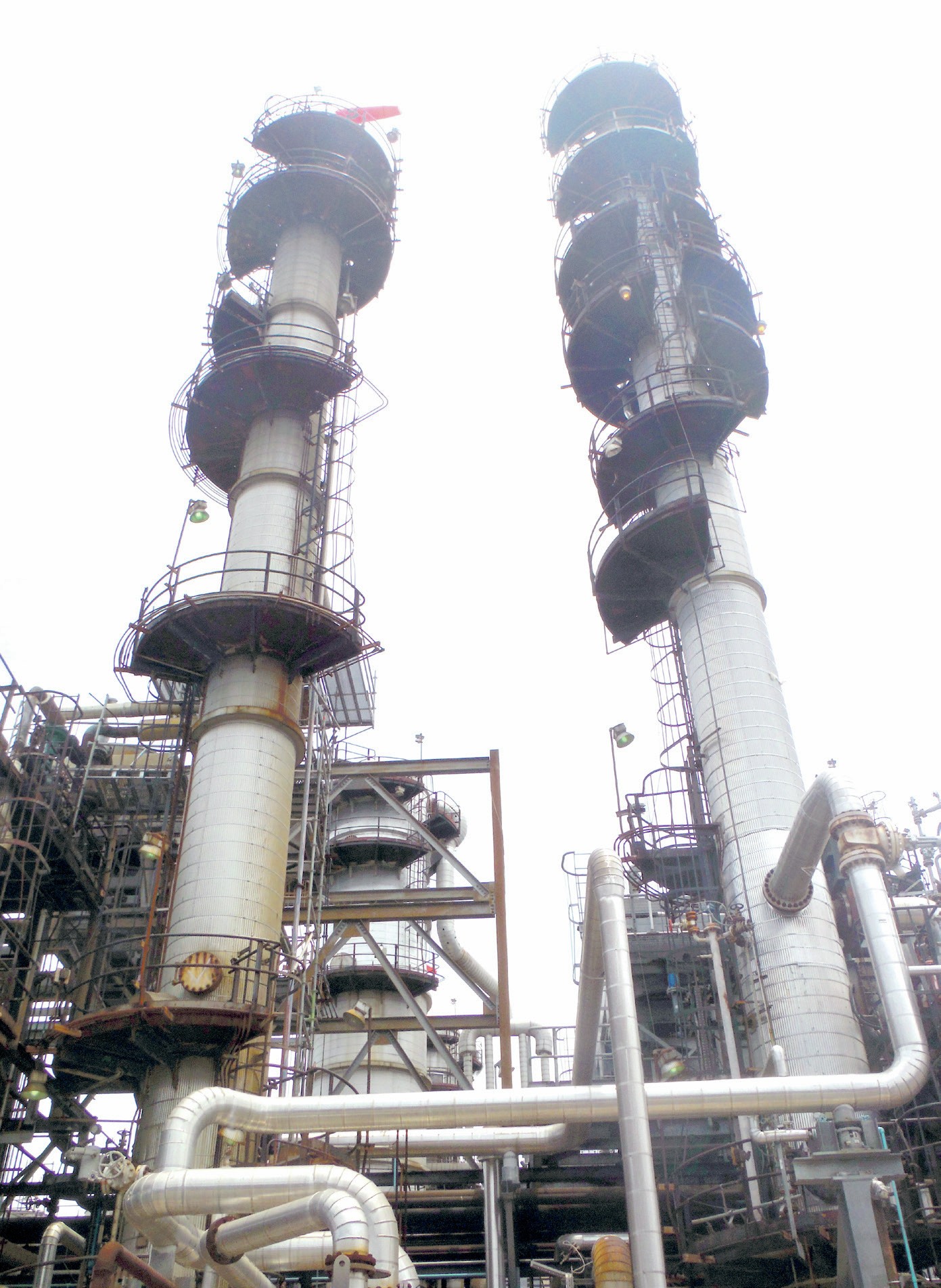
SOUR WATER STRIPPING
A big plus for sour water strippers: low GWP ammonia recovery
Refinery sour water strippers are an often overlooked resource of low GWP ammonia. Martin A. Taylor and Charles L. Kimtantas of Bechtel Energy Technologies and Solutions, Inc. (BETS) show the results of a study on reusing an existing SWS as one of the major systems in a SWSPlus unit for the recovery of ammonia for sale. Relative cost factors will compare a complete SWSPlus unit versus reusing an existing SWS.
With concerns about global warming potential (GWP100) and the carbon intensity (CI) of processes growing, the use of ammonia (NH3) as a hydrogen carrier and fuel is generating more and more interest. One source of low GWP ammonia that is commonly ignored is from refinery sour water strippers (SWS). However, that ammonia exists with hydrogen sulphide (H2S) and is routed to a Claus sulphur recovery unit (SRU) for combustion, resulting in the destruction of the ammonia on the path to recovery of the sulphur. Other emissions (NOx, CO, CO2, PM10) are also increased by the processing of SWS gas in the SRU. Bechtel’s SWSPlus® technology can be used to separate the ammonia and hydrogen sulphide into separate streams, which enables a high-value, low CI, saleable ammonia product plus a cleaner feed to the SRU.
History
SWSPlus was originally known as WWT when first developed by Chevron in the 1960s. It is a two-column SWS where the first column produces a high concentration H2S + CO2 stream and the second column produces a high concentration NH3 stream which can be further purified for sale. The process was patented in 1967 and the first unit was licensed outside of Chevron the very next year. In 2011, the process technology was sold to Bechtel Energy Technologies & Solutions, Inc. (BETS). When any technology has been around for that long, putting a new set of eyes on it will invariably allow for improvements. The first improvements were awarded patents in 2018 (prompting a rebranding as SWSPlus) and there are now a total of four patents issued with three others pending. In various ways, they focus on capex, opex, and product purity.
At the time of writing, there are a total of 27 licensees of the technology, most recently at a biorefinery in the Los Angeles, California, area, where the relatively small amount of acid gas could not be flared due to strict environmental regulations. Instead, SWSPlus recovered the NH3 and another home was found for the H2S in the refinery. Thus, SWSPlus acted as an enabling technology for the project.
Isn’t ammonia dangerous?
A frequent query received when discussing the technology is around the safety of handling NH3. The answer is that yes, it is dangerous, as are H2S, propane, octane, and benzene. Do you have those in your refinery? Table 1 shows the relative values for LEL, autoignition temperature, minimum ignition energy, and two US-based exposure limits for workers (8-hr TWA and 15-min STEL).
The table shows that the LEL, autoignition, and minimum ignition energy values for NH3 make it a safer chemical than the counterparts. It is only when compared to health hazards that propane and 100 octane become less hazardous. The 15 minute STEL for propane is not listed as it becomes an asphyxiant before becoming a toxin.
Global warming potential
GWP100 is the phrase used to describe the global warming potential over the course of 100 years for a given chemical process. Sphera, a third party consultant, was hired by a potential licensee to evaluate the GWP100 of SWSPlus compared to the Haber Bosch process, which is the worldwide standard for production of NH3 from natural gas and air.
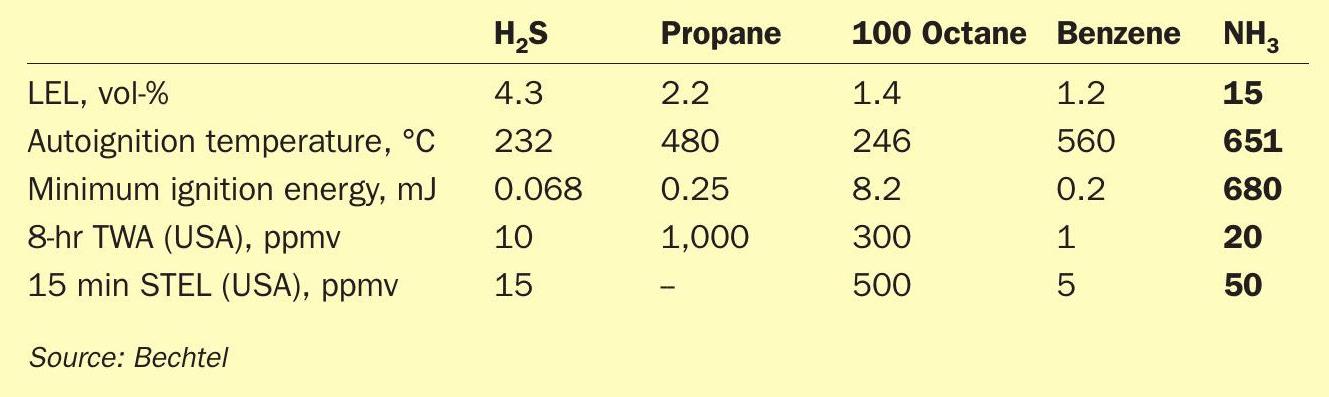
The study considered an incremental tonne of NH3 from an existing Haber Bosch facility against an incremental tonne of NH3 from a refinery using SWSPlus. Specifically, the values for steam, electricity, caustic (used in the purification process), sulphur recovered, and ammonia recovered came from BETS for the SWSPlus process and the GaBi database for the Haber Bosch process. For clarity, steam changes in the SRU were considered in the study.
Fig. 1 shows the results were a 54% lower GWP100 vs “grey” NH3 and 17% lower than “blue” NH3. If a refinery is being pushed to be more environmentally friendly in the form of GWP100 or carbon intensity, then SWSPlus is a valuable addition.
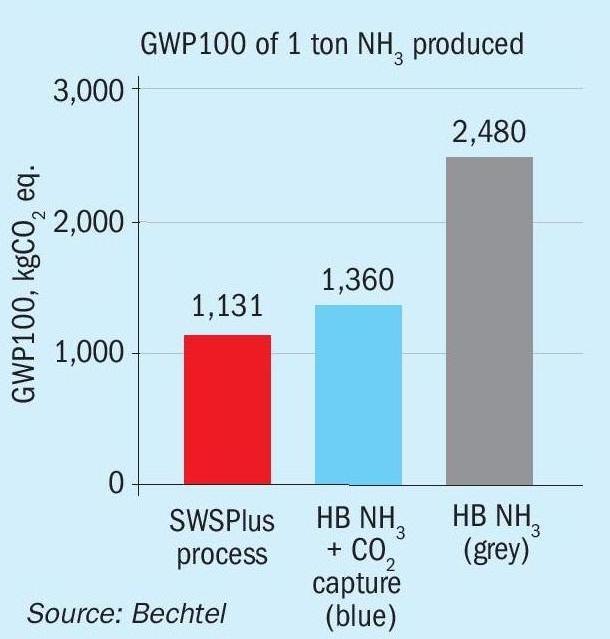
Benefits of NH3 removal
Integration of SWSPlus into a refinery allows processing of higher nitrogen and higher sulphur crudes without SRU expansion. It also mitigates the potential of ammonium polysulphide salt deposition in the SRU and increases SRU capacity. It adds NH3 as a revenue stream for the facility and can do so at half the capex expenditure compared to an additional SRU train (Claus, TGTU, Degassing, Thermal Oxidiser). Best of all, no new air permit is required for anhydrous ammonia recovery!
The chemistry benefits of NH3 removal from a refinery Claus unit are well documented elsewhere and so will not be repeated here, except to summarise by saying removing one tonne of NH3 can make room for processing approximately three tonnes of H2S in the Claus unit.
Process walk-through
There are typically four steps in processing: feed preparation, acid gas stripping, ammonia stripping, and finally purification/ liquefaction. Fig. 2 shows a sketch of the first three steps of the SWSPlus process.
Step 1: Feed preparation
Sour water from the refinery is typically generated at medium to high pressures in contact with various hydrocarbons. When released to a lower pressure for storage in an atmospheric tank, lighter hydrocarbons along with some H2S and NH3 will be released, so the first destination of sour water is a degassing vessel. Flashed vapours are sent to flare or a sour gas recovery system. The liquid is sent to a deoiler, which makes the first attempt at removing free hydrocarbon phases from the sour water. The sour water is then sent to at atmospheric storage tank for process stabilisation, feed homogenisation, and surge capacity.
Step 2: Acid gas stripping
The sour water is pumped through some heat integration with the ammonia stripper’s bottoms stream before being sent to the first distillation column, the acid gas stripper. The acid gas stripper is a reboiled distillation column. It does not generate enough water overhead to make its own reflux, so a water wash is used instead.
Note this is not the same chemistry which occurs in a traditional SWS – simply breaking an acid-base bond and creating steam to carry it upward. In an acid gas stripper, multi-component distillation occurs. Here, we want to let the H2S (and any CO2 present) escape as vapours through the top of the acid gas stripper but keep the ammonia in the aqueous phase. SWSPlus technology keeps NH3 in the resultant acid gas to under 50 ppmw, resulting in a high purity H2S stream, which is perfect for feeding to a Claus unit or sulphuric acid unit.
Step 3: Ammonia stripping
From the acid gas stripper, the process water is sent to the ammonia stripper, which operates at a significantly lower pressure than the acid gas stripper.
This column is a reboiled and refluxed distillation column whose liquid product is stripped water. That stripped water will contain typical levels of NH3 compared to a SWS, for example, 50 or 25 or 10 ppmw, as desired. H2S is typically single digit ppmw or less. The vapour product contains ammonia in a highly concentrated stream (90+%) along with any H2S not removed by the acid gas stripper.
The potential dispositions of the NH3 are incineration, anhydrous ammonia (via either compression or refrigeration), and aqueous ammonia. Fig. 3 shows the purification and liquefaction steps which may be used to render the NH3 recovered from the ammonia stripper saleable. The ammonia can also be used to generate heat or power by combusting the NH3 in an incinerator with appropriate heat/energy recovery.
Case study
As a case study, consider a facility which processes 500 US gpm of sour water in a single SWS. It has 1,000 ppmw NH3 and 2,000 ppmw H2S with typical values of contaminants such as CO2, mercaptans, and hydrocarbons. An expansion opportunity presents itself wherein recovery of ammonia would offset an increased Claus SRU load. For simplicity, assume the total sour water load remains constant, while noting mild to moderate increases in flowrate would only help the economics of the project.
The objectives are to reuse the existing asset (the SWS), add a revenue stream, and do so while being mindful of the carbon intensity of the facility.
In considering reuse of the existing column, many refiners desire to use it as the first of two in a SWSPlus. This is not normally possible considering the higher temperatures and pressures required in the acid gas stripper. There are various mechanical issues that result, not to mention the different diameter requirements at the higher pressures. In addition, metallurgical requirements are different in the acid gas stripper.
However, if repurposed as an ammonia stripper (that is, the second column in a SWSPlus) then the SWS column does well. The existing column operating temperature and pressure can be left as is. In that case, the only chemistry change is a composition with less H2S and CO2. In an SWSPlus unit, most of the H2S and CO2 are removed by the acid gas stripper, so the partial pressure of H2S would be significantly reduced in the repurposed ammonia stripper. From a metallurgy perspective, it is a friendlier application than the original design.
If wall thickness measurements indicate the temperature and pressure can be modified to improve performance, then that means:
- potentially higher capacity;
- more efficient purification steps;
- lower utility costs in those steps;
- more efficient compression (lower hp).
In this case study, changes in existing asset operating pressure are not considered.
SWS equipment reuse considerations
In maximising the reuse of existing assets, and assuming similar overall sour water flow, the same degassing drum and pumps, the same feed preparation tank, the same column (as the ammonia stripper), and the same feed/bottoms exchanger will be used. There is notable optimisation to be done regarding trays vs packing and potentially increasing the duty of the feed/bottoms exchanger vs steam prices, both of which are application specific.
Results
In this example, Fig. 4 identifies which parts of the SWSPlus are repurposed. As can be seen, only two of the existing pieces of equipment (charge pump and overhead cooler) could not be reused. Put another way, almost half of the equipment required for ammonia recovery and purification can be reused from an existing SWS. The most expensive item, the column, is reused.
Table 2 provides representative information regarding equipment and utilities. All equipment successfully reused is labelled “Acceptable”. The acid gas stripper operating pressure increases the horsepower requirement of the charge pump and stripped water pump. The overhead duty of the ammonia stripper also increased.
Regarding utilities, Table 3 shows MP steam is required due to the operating temperature of the acid gas stripper’s reboiler. Because of the low quantity of H2S in the ammonia stripper, that reboiler duty actually decreases. The electrical requirement significantly increases, primarily due to the addition of compressors to make anhydrous ammonia via compression. If aqueous ammonia is desired, the power consumption is typically 2 /3 this value.
Plot and capex are significant concerns in any revamp. Based on full spacing requirements, the required plot can increase by 50% compared to the original SWS. Note the columns can be remote from each other. This excludes tankage, of course, and full spacing requirements are frequently compromised during retrofits. Capex requirements relative to a grassroots SWS are about 2.1 times the cost, that is to say, an SWSPlus unit is around 3.1 times the cost of a stand-alone SWS. Put another way, this approach is about 30% less than a new SWSPlus.
Conclusions
SWSPlus is a proven technology with a lower GWP100 than Haber Bosch ammonia production. It expands SRU capacity by removing NH3 from the feed and adds that NH3 as a revenue stream to the refinery. SWSPlus can be retrofitted to an existing SWS if plot is available, even remotely, and capex is 30% less than a grassroots SWSPlus.