Sulphur 414 Sep-Oct 2024
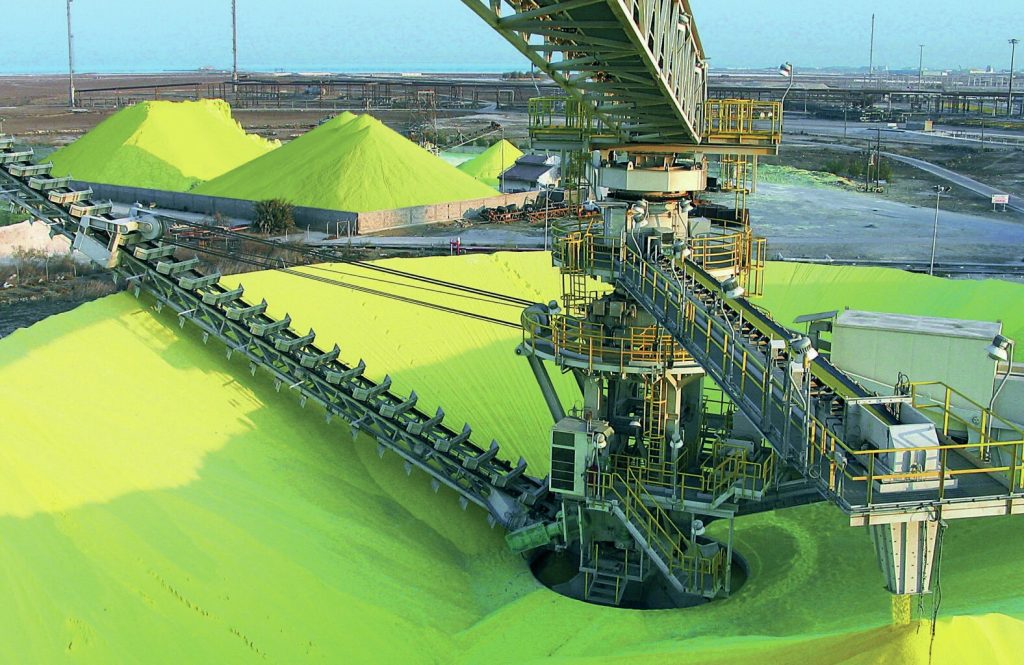
30 September 2024
A history of sulphur forming
SULPHUR FORMING
A history of sulphur forming
Transporting sulphur as a dry bulk solid can lead to it breaking into small particles which create dust. Over the years, various forming processes have been developed to try and minimise dust formation and produce the strongest, most resilient formed sulphur particles.
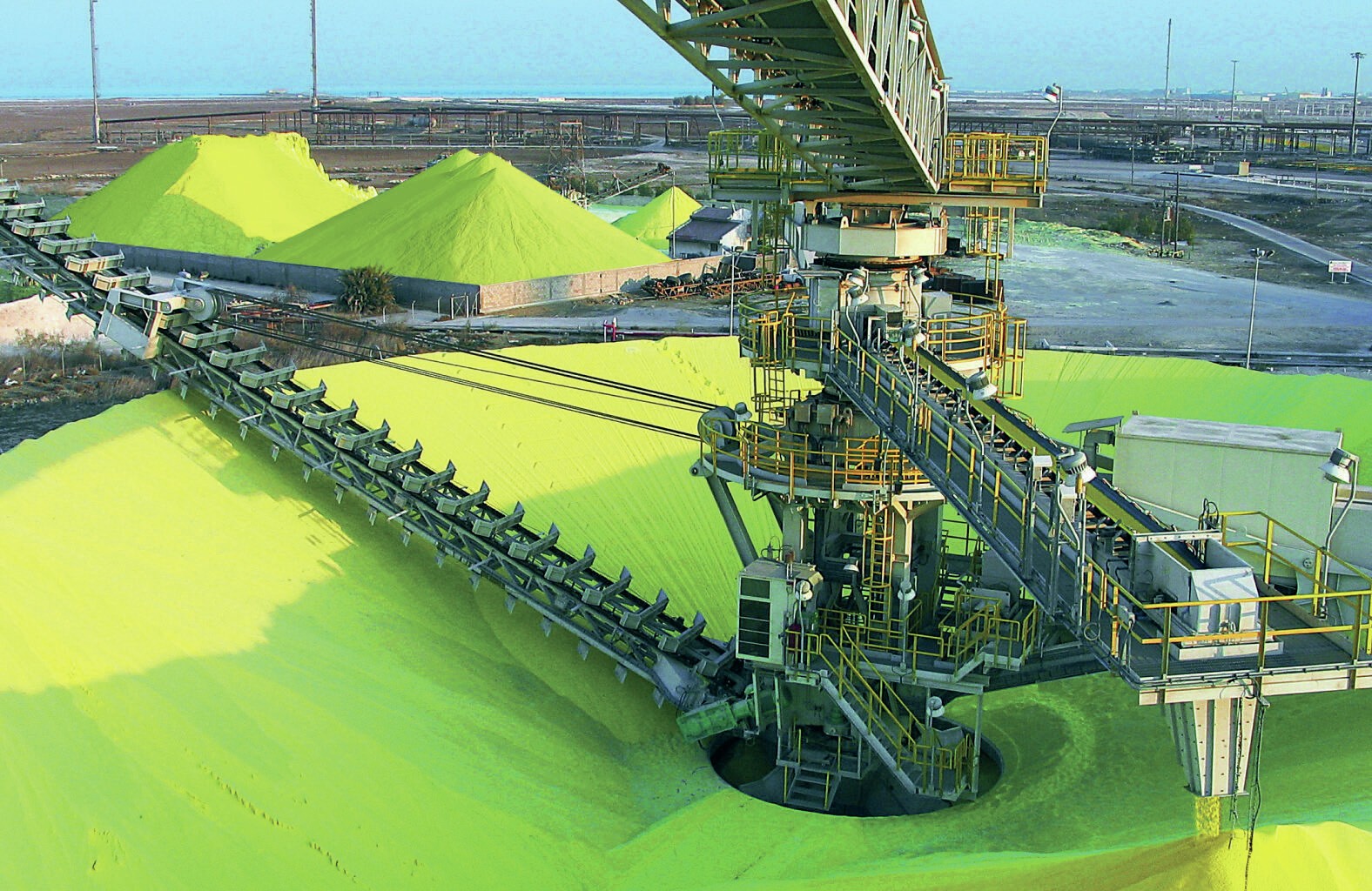
While sulphur emerges from a Claus plant as a liquid, and a sizeable minority of sulphur is still consequently stored and transported as a liquid, keeping large volumes of sulphur at high temperatures creates challenges for transportation, and these days most of it is transported long distances as a bulk solid. However, this in turn can create its own problems, and this has led to a number of different alternatives for forming solid sulphur.
In the early days of the industry, molten sulphur was simply poured into large open air vats, sometimes up to hundreds of thousands of tonnes in size, and left to solidify, then recovered mechanically as large crushed lumps of sulphur. However, sulphur is extremely brittle, and this process created a large amount of sulphur dust, which can be a fire and explosion hazard, as well as allowing wind-blown sulphur dust to be carried to neighbouring sites and properties, eventually breaking down and acidifying. One of the reasons for a move to storing and shipping sulphur as a liquid was to avoid these problems, and by the 1980s, around 50% of all sulphur transported internationally was as a liquid, with that figure reaching 95% in North America.
But receiving cargoes of sulphur as a liquid requires specialised equipment, including heated lines and tanks, which not all customers had available, and this restricted the client base for those producing sulphur. A better way of transporting solid sulphur over longer distances needed to be found.
Slate
Although the first sulphur forming processes were based on both wet and dry prilling (see below), sulphur forming on a large scale really began with the slating system developed in Canada in 1969 by Vennard & Ellithorpe, later part of Procor Ltd, and eventually Enersul. Slate sulphur is formed by pouring molten sulphur onto a moving belt, where it is solidified into a continuous slab with a thickness of around 5 mm by indirect water sprays. After quenching in water, the sulphur is discharged from the end of the belt and breaks into smaller pieces. Slating appeared to solve the dust problem of crushed bulk sulphur, and in 1972 the port of Vancouver banned the export of all sulphur not formed into slate. However, the product remained in irregularly shaped pieces with sharp edges which tended to break during storage and transport, and eventually deteriorate to produce fine sulphur dust, necessitating water sprays to keep dust levels down, in turn leading to corrosion inside e.g. ship vessel holds. In 1974, the Canadian Industry Sulphur Forming Committee therefore commissioned the Sulphur Development Institute of Canada (SUDIC) to evaluate forming processes and recommend one for the Canadian sulphur industry. A number of forming processes were available, as detailed below;
Prilling
Prilling or pelletising could take two forms, wet or dry. Wet pelletising, such as the Sulpet process commercialised by Humphreys & Glasgow, involved allowing molten droplets of sulphur to fall through a body of water, leading to solid pellets which are recovered on a screen and dried. Other wet prilling processes force liquid sulphur in narrow streams into an agitated water bath. The low thermal conductivity, high specific heat, and long transformation time of sulphur make it necessary to maintain the pellets in suspension for as long as possible, allowing them to harden. This process produces spherical, uniformly sized pellets.
Taking a cue from fertilizer prilling processes, air/dry prilling allows droplets of molten sulphur to be sprayed into the top of a tower and fall under gravity against an upward flow of cooling air, with the length of drop calculated so that the sulphur is solid enough to survive the impact at the bottom. The first air prilling process was developed by Outokumpu (now Outotec) in 1962, but the technique was refined by Siarkopol in Poland and became known as the ‘Polish Prill’ process. It was first installed in Tarnobrzeg in Poland in 1966, and later spread across Alberta, including Shell’s Water-ton site, and at Aramco’s al Jubail site in Saudi Arabia. However, a series of fires at air prilling towers in the 1980s caused by electrostatic discharges igniting sulphur dust in the towers led to the process being largely discarded and superseded by other methods. More recently, Dutch based prilling developers Kreber have modified the sulphur air prilling process, with a closed loop of circulating nitrogen gas to remove the danger of fire, better integrated heat recovery and a wet scrubbing system to remove fugitive dust.
‘Popcorn’ sulphur
Union Oil Co of California developed the so-called ‘popcorn’ process, where molten sulphur and water are sprayed together into the open air from a specially designed jet. The product lands on a stockpile as small solid particles. Although the company installed it at their own sites in the US, however, it was not sold on the open market.
Pastillation
Pastillation took the belt driven slate process and refined it by dropping liquid sulphur from a distributor onto a moving metal belt to form small hemispherical pastilles. As with slating, the belt is cooled from below by jets of water. The temperature of the cooling belt is controlled by regulating the flow and temperature of the cooling water sprayed onto the underside of the belt. The cooling water is collected and re-circulated through a cooling system. Control of the heat transfer rate from the molten sulphur droplets to the metal belt and from the metal belt to the cooling water not only optimises production capacity, but also ensures the production of a high quality product. The process was developed by Sandvik Process Systems (now IPCO) in the 1980s and is marketed as Rotoform. A claimed advantage for the system is that the formed sulphur is low in moisture content, although debate continues to rage over the optimum water content for dry bulk sulphur.
Granulation
The final development of sulphur forming processes was as dedicated granulation technologies. These use a size enlargement process to gradually build seeds layer by layer into dense spherical solid granules. Small particles of sulphur (seed) are introduced at the feed end of the drum and are sprayed and coated with molten sulphur as the product moves toward the drum discharge. Each applied layer is cooled to solidification before another coat of molten sulphur is applied. With repeated application, bonding and then cooling of successive coats, the seeds increase in volume and weight until they reach the desired granule size.
An early example of this was the Procor (now Enersul) GX process, which was first commercialised in 1979. Over the years, the GX process has become a family of granulators, from the GXM1 to the large scale GXM1 Nexgen and the smaller scale modular GXM3. Other granulation processes include the Devco wet granulation process, developed by Devco USA in 1980 and eventually updated as the Devco II process, which was bought by Matrix PDM Engineering in 2016. There is also the Brimrock process, developed by Brimrock and Martin Sulphur Systems in 2010, and acquired by IPCO in 2014. Kaltenbach-Thuring, acquired by Yara in 2003, also modified its own fluidised drum granulation (FDG) system in the 1990s for sulphur granulation.
Blocking
Finally, of course, where long term storage is required rather than sale and transport of sulphur product, sulphur can be poured to block. Generally this is done by spraying a thin layer of molten sulphur onto a block pad or existing sulphur block, then allowing it to cool and solidify before adding another layer.